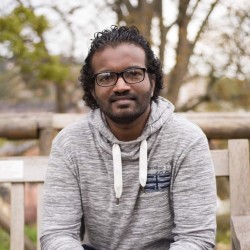
Dr Delika M. Weragoda
Academic and research departments
Centre for Automotive Engineering, School of Mechanical Engineering Sciences.About
My research project
A novel battery thermal management systems based on capillary driven evaporative coolingThe project is focused on developing a novel battery thermal management system based on capillary driven evaporative cooling (CDEC), that could potentially minimize the power consumption, thermal resistance and the overall weight of the battery pack benefiting different EV applications such as eVTOLs.
Supervisors
The project is focused on developing a novel battery thermal management system based on capillary driven evaporative cooling (CDEC), that could potentially minimize the power consumption, thermal resistance and the overall weight of the battery pack benefiting different EV applications such as eVTOLs.
Affiliations and memberships
ResearchResearch interests
Battery thermal management (active & passive)
Heat transfer and heat transfer enhancement
Heat pipes and heat exchangers
Interfacial sciences (liquid-solid)
Research interests
Battery thermal management (active & passive)
Heat transfer and heat transfer enhancement
Heat pipes and heat exchangers
Interfacial sciences (liquid-solid)
Publications
Thermal runaway (TR) of Li-ion batteries (LIBs) presents a disastrous safety hazard and a significant barrier to the wider adoption of electric vehicles (EVs). Internal short circuit (ISC) induced by mechanical abuse is one of the causes of battery TR. This paper uses hemispherical indentation tests to trigger ISC in the battery at different temperatures and studies the battery deformation and fracture mode. Results show as the initial temperature increases, the battery hardness and strength decrease, and the fracture mode of the laminar structure changes from shear fracture to localized rupture. In the shear fracture mode, the ISC homogeneously heats the battery, and it does not directly trigger TR. In the localized rupture mode, the ISC is only induced at the layers close to the indenter and generates a hot spot exceeding 200 °C, leading to the initiation of TR. Therefore, the mechanical properties of batteries under different conditions need to be studied in more detail to develop batteries that are safer under mechanical abuse. •Three deformation phases: Compaction and plasticity, destabilization, and collapse.•The hardness and strength of the battery decrease as the temperature increases.•The deformation is concentrated locally at higher temperatures.•Shear fracture at low temperatures and localized rupture at high temperatures.•Shear fracture causes gradual heating, and localized rupture directly triggers TR.
•Heat generation of Lithium ion batteries and consequences of thermal instability.•Capability of heat pipes in maintaining thermal stability of Li-ion cells.•Gaps in heat pipe based battery thermal management.•Current status, challenges and future direction of heat pipe based battery thermal management. Heat pipes are currently attracting increasing interest in thermal management of Electric vehicle (EV) and Hybrid electric vehicle (HEV) battery packs due to its superconductive capability, robustness, low maintenance and longevity. With the focus of battery thermal management directed towards both convective and conductive cooling, a significant number of research, both experimental and numerical investigations have been performed during the past decade. However, heat pipe based battery thermal management systems (HP-BTMS) are yet to be commercialized due to lack of understanding their limitations during rapid heat fluctuations and adverse environmental conditions, performance under multiple heat loads, failure criteria in the context of battery thermal management and lack of simple and versatile thermal models to accurately predict the battery thermal performance at module and pack level. This comprehensive review highlights the different heat generation mechanisms of Li-ion batteries and their resulting consequences, followed by the operating principles of heat pipes along with background and shortcomings related to heat pipe based battery thermal management, for the mere purpose of further development of this promising thermal management system. Different heat pipe based thermal management systems developed during the last decade along with their modelling approaches, including the methods adopted for enhancing heat transfer are critically analysed. Heat pipes have demonstrated to be an effective approach in maintaining optimum cell surface temperature, however, several areas require attention if this system is to be commercialized. Niche types of heat pipes such as pulsating heat pipes, loop heat pipe, mini/micro heat pipe have also been reviewed and their advantages, disadvantages, and challenges in the context of BTMS are discussed. Finally, the current status, challenges and prospects of the future direction in HP-BTMS are highlighted.
A thermal management system for lithium-ion batteries is an essential requirement for electric vehicle operation due to the large amount of heat generated by these cylindrical batteries during fast charging/discharging. Previously, researchers have focused mostly on pouch and prismatic cells with heat pipes arranged in the horizontal direction. The current study introduces a novel vertically-oriented heat-pipe-based hybrid cooling battery thermal management system (BTMS) that numerically evaluates the thermal performance of the cylindrical batteries and the flow pattern within the cooling channel at C rates as high as 8C. The model was experimentally validated using five round heat pipes in a vertical orientation utilizing the effect of gravity to assist condensate flow through the heat pipe. The heat pipes were arranged in a staggered pattern to improve the overall heat transfer performance by means of forced convective cooling. This design allowed for maximizing the heat transfer process despite the lack of contact between the cylindrical-shaped batteries and round-shaped heat pipes. During this study, the temperatures of the evaporator end and the condenser end of the heat pipes and battery surfaces were monitored, and the thermal performances of the system were determined at varying inlet cooling liquid temperatures (15, 20, 25 °C) and high rates of 4C and 8C. Representatively, the proposed hybrid BTMS could maintain a maximum battery surface temperature of around 64 °C and a temperature difference between cells under 2.5 °C when the inlet velocity was 0.33 L/min and the cooling liquid temperature was 25 °C. The high temperatures reached the fourth and fifth heat pipes because they are part of the backflow design and are affected by backflow temperature. Nevertheless, the current design shows that the proposed system can maintain battery surface temperatures well within 5 °C.
Hydrogen energy is considered to be the most potential “ultimate energy source” due to its high combustion calorific value, cleanliness, and pollution-free characteristics. Furthermore, the production of hydrogen via the electrolysis of water has the advantages of simplicity, high efficiency, environmentally safe, and high-purity hydrogen. However, it is also associated with issues such as high-power consumption for the reaction and limited large-scale application of noble metal catalysts. Metal–organic frameworks (MOFs) are porous composite materials composed of metal ions and organic functional groups through orderly coordination with large specific surface areas and large porosity. Herein, we focus on the research status of MOFs and their transition metal derivatives for electrocatalytic water splitting to produce hydrogen and briefly describe the reaction mechanism and evaluation parameters of the electrocatalytic hydrogen evolution and oxygen evolution reactions. Furthermore, the relationship between the catalytic behavior and catalytic activity of different MOF-based catalysts and their morphology, elemental composition, and synthetic strategy is analyzed and discussed. The reasons for the excellent activity and poor stability of the original MOF materials for the electrolysis of water reaction are shown through analysis, and using various means to improve the catalytic activity by changing the electronic structure, active sites, and charge transfer rate, MOF-based catalysts were obtained. Finally, we present perspectives on the future development of MOFs for the electrocatalytic decomposition of water.
In conventional heat pipe based battery thermal management systems the thermal contact between the battery and the heat pipe is enhanced by means of heat conductive elements. These additional elements introduce multiple layers of thermal resistance and contribute to increased weight. This paper aims to address this issue by minimizing the contact thermal resistance and potentially reduce this additional weight. The proposed solution relies on capillary-driven evaporative cooling (CDEC), wherein a wick structure is directly integrated onto the battery's surface to enable direct cooling. To demonstrate this concept, an experimental study was conducted by affixing a Copper foam to an emulated battery block, and using ethanol and Novec 7000 as cooling media. The CDEC system's thermal performance was assessed under three heating conditions, and different operating conditions. The results indicated that the copper foam with higher pore density outperformed the other due to its greater wetting height. The maximum cell surface temperature was maintained around 40 °C for a continuous 50 W heat input. Furthermore, the thermal resistance of the system was lowered by a factor of 6 compared to an air-cooled system. The thermal resistance ranged from a minimum of 0.32 to a maximum of 1.5 K/W, which were comparatively low compared to some existing battery thermal management system designs. This paper introduces an innovative battery cooling concept, presents experimental evidence of its feasibility, and demonstrates its ability to effectively regulate battery temperature within acceptable limits even under high heat loads, while minimizing overall thermal resistance.