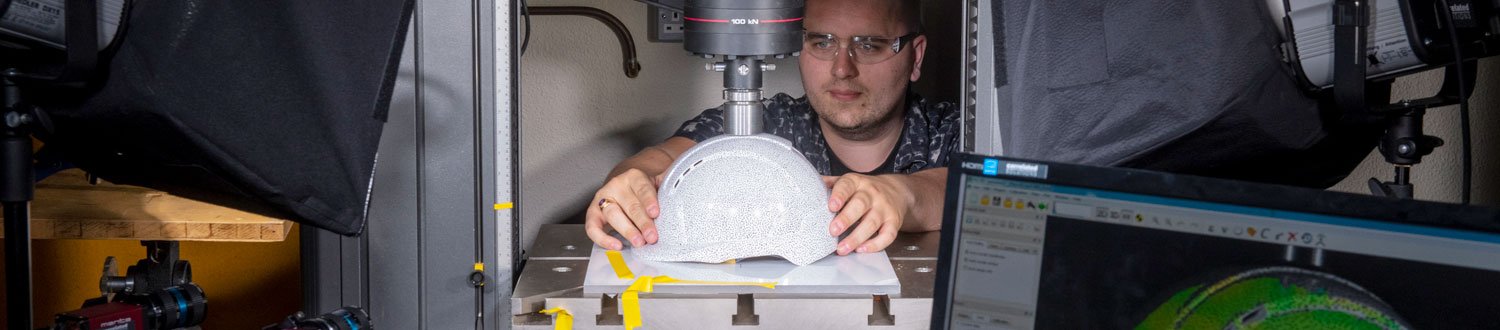
Additive manufacturing
Current research on printing and additive manufacturing includes fabrication at a range of length-scales, from the micrometre and millimetre scales for printed devices, to more than a metre for metallic aerospace components.
The range of materials being explored includes polymers, ceramics and metals, often used in conjunction with each other.
Overview
Printing and additive manufacture (AM) are disruptive technologies; they offer opportunities for producing components, structures and products with unique structures and properties. These products potentially offer tailored properties, novel design opportunities (via topological optimisation), shorter lead-time and reduced environmental impact.
Additive manufacture includes a broad range of methods that are currently undergoing rapid development. The term is arguably preferable to the popular term ‘3D printing’ in that many conventional manufacturing processes are ‘subtractive’ in nature.
The term is therefore a reminder that additive processes, as opposed to subtractive ones, can enable more complex and structurally efficient shapes to be manufactured.
Large-scale metallic additive manufacture
Our current focus of large-scale AM research is on the manufacture of metallic alloys by additive processes includes a variety of laser and arc-based processes. In the former case, a fine powder is the precursor, and in the latter, a wire is normally used. We are exploring the metallurgical issues encountered in both areas, with a view to improving structural integrity and establishing appropriate structural certification.
In one project, the School of Mechanical Engineering Sciences is working with the Surrey Space Centre and Frazer-Nash with the goal of space certifying additive manufactured satellite components. The process used in this project is Selective Laser Melting (SLM) as it offers good tolerance and reasonable surface finish. SLM is a relatively slow process as a component is created, or built, by adding layers of a few tens of micrometres at a time.
Other work is underway with other industrial partners, including Lockheed Martin UK, to produce very large components for aerospace applications. For large components (metres by tens of centimetres), a wire and arc process is used. This process is closely related to MIG welding but requires robotic automation. With this approach up to around 10 kg of material can be deposited per hour. Such a process brings a range of issues centred on stress build-up and metallurgical issues. These aspects form a major part of the current research work at Surrey.
Direct write of structural devices
Additive manufacture of functional materials at micrometre length scales is leading to the creation of novel functional devices for sensing and energy harvesting. This work forms a pivotal part of Surrey's research on functional materials and devices via the SPARKlab.
Meet the team
If you are interested in finding out more about our research, or have a query then please contact Professor Robert Dorey.

Professor Robert Dorey
Professor of Nanomaterials
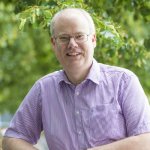
Dr Mark Whiting
Professor of Materials Ageing / William Penney Fellow in Materials Ageing