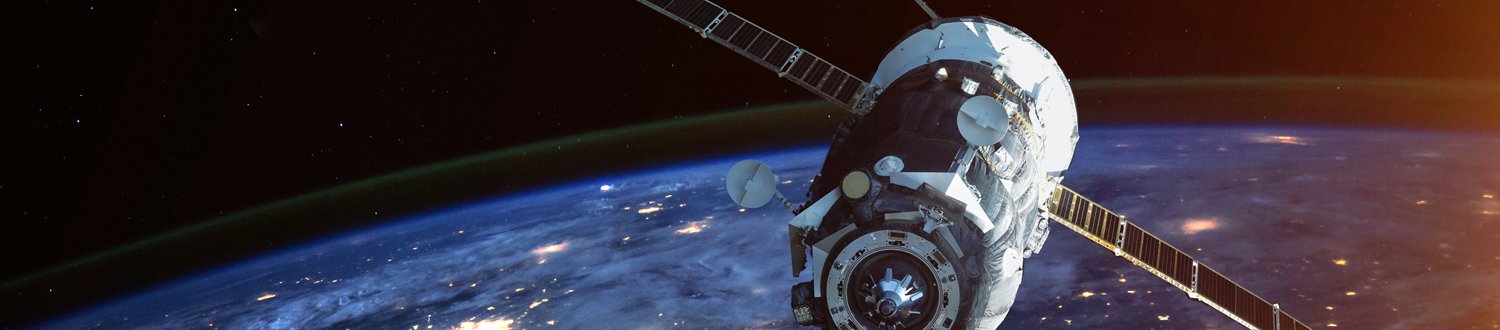
Docking facilities
Our Centre makes use of a number of air bearing test facilities, to model the micro-gravity space environment for testing of spacecraft navigation and control systems.
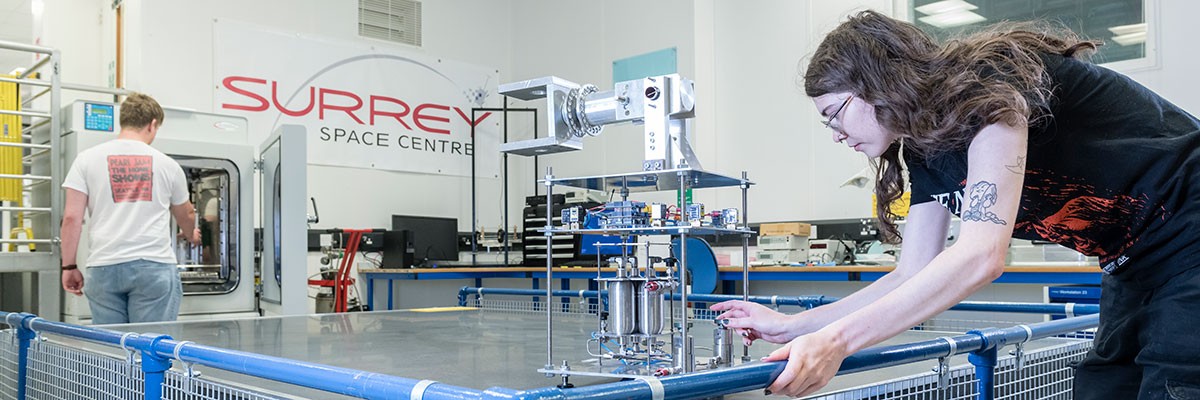
Falcon
Micro-porous carbon table
- 100x150cm 3DoF air table (X-Y translation, Yaw)
- Table consists of 15 Micro-Porous Carbon (MPC) strips supplied by New Way Air Bearings
- MPC provides uniform airflow across surface—Table not subject to turbulent currents as effects similar “Air Hockey” type tables
- Supplied by in house compressed air supply at range of pressures providing up to 70um fly height
- Facility established to model CubeSat manoeuvring and docking using representative spacecraft simulator seated on passive puck through EPSRC funding
- Mounting frame for docking targets and machine vision systems.
Eagle
Granite table
The frictionless motion testbed was developed to allow the real time demonstration and practical application of new attitude and orbital control algorithms developed within the group.
The facility is comprised of three elements: a precision levelled and smoothed granite surface table, miniature air cushion platforms and a motion capture system. Translation of the air cushion platforms across the table provides a frictionless motion that is analogous in two dimensions to the microgravity conditions of orbital free-fall.
The testbed is situated in the Space Centre laboratories and provides a 2 by 3 m surface area for experimental use. The entire volume is captured by Kinect video depth sensors, providing truth measurements of the air cushion platform position and pose. Two classes of air cushion platform provide the base for a diverse range of experiments.
The design of the first class was driven by the worldwide interest in the CubeSat platform and its application in space. This air cushion platform is similar in mass, dimensions and its inertial properties to a 3U flight CubeSat, providing motion behaviour that closely matches that seen on orbit.
A second platform class sacrifices some of the compactness of the CubeSat format to allow longer duration fly times. Furthermore, the larger platform is suitable for testing experimental hardware from subsystem level to full spacecraft engineering models.
CubeSat simulator
- Mass-/dimension-/inertia-analogous to 3U CubeSat
- Size - 0.3 x 0.1 x 0.1m
- Mass - 3.5kg
- Max load - 20kg
- Fly time - 5 minutes
- Thrust - 150mN/valve
Microsatellite simulator
- Actuated base to support full scale reference satellites
- Size - 0.3 x 0.2 x 0.2m
- Mass - 4.5kg
- Max load - 60kg
- Fly time - 20 minutes
- Thrust - 150 mN/valve
The development of the facility was motivated by the requirements of current research into a nanosatellite-class inspection mission, or “InspectorSat”.
The group research has output several conceptually proven but experimentally untested algorithms for position and pose estimation, trajectory prediction and relative motion and formation flying path planning. To continue the development of these capabilities toward flight readiness their practical performance must be characterised and integration into space-qualified hardware demonstrated.
The InspectorSat will fly these methods as part of a visual inspection payload implemented as an AODCS for close proximity spacecraft control. The frictionless air table testbed is an integral part in the development of such hardware, as it provides a laboratory-based system capable of validating performance under conditions analogous to orbital motion.
Get in contact
If you want to find out more about our facilities or are interested in using them then please contact us.
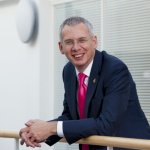
Professor Craig Underwood
Emeritus Professor of Spacecraft Engineering