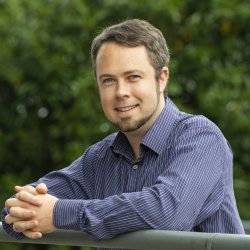
Dr Simon King
About
Biography
Biography
Dr Simon G King currently works as a Research Fellow at the Advanced Technology Institute (ATI) as part of the Nano-Electronics Centre (NEC). He is also an active member of the Institute of Physics.
Dr King is an alumnus of the University of Surrey (BSc Physics - 2010), and continued at Surrey to complete his doctorate (2014 - "Novel Electrospinning Techniques with Nano-materials").
After a brief period working is the financial sector, Dr King returned to Surrey as a Research Fellow within the University of Surrey's Electrical and Electronic Engineering department, in Prof Ravi Silva's Nano-Electronics Centre.
Dr King specialises electrospinning (included nanofibre production and analysis), and nano-materials (including carbon nanotubes and graphene). His current primary research project is titled 'Manufacturing Lightweight Carbon Nanotube Electrical Cables', funding by the EPSRC.
Research Interests
- Large-area Electrospinning
- Electrospinning of nano-materials (inc. CNT and Graphene)
- Composite Materials and nano-material enhanced composites
- Thermoelectrics
- Energy Harvesting
- Printed flexible sensors/switches/transistors
- Nano-material manipulation and processing
- Carbon Motors
Collaborators
- Revolution Fibres Ltd. (New Zealand)
- Thomas Swan & Co. Ltd. (UK)
- KYMIRA Ltd. (UK)
- University of Bristol (UK)
Areas of specialism
Affiliations and memberships
ResearchResearch projects
Manufacturing Lightweight Carbon Nanotube Electrical CablesCNTs have already demonstrated to exhibit electrical properties that exceed that of copper, yet remaining up to 10x lighter. However, with the current inability to grow CNTs to any required length they must be manipulated and processed before they can be utilised. This project uses electrospinning to develop a manufacturing solution to produce and process the CNT wires. this includes managing and healing any structural defects within a CNT network, effectively 'welding' them together. This welding will effectively eliminate the tube-to-tube resistances currently faced in CNT electrical devices and allow for large-scale application.
Research projects
CNTs have already demonstrated to exhibit electrical properties that exceed that of copper, yet remaining up to 10x lighter. However, with the current inability to grow CNTs to any required length they must be manipulated and processed before they can be utilised. This project uses electrospinning to develop a manufacturing solution to produce and process the CNT wires. this includes managing and healing any structural defects within a CNT network, effectively 'welding' them together. This welding will effectively eliminate the tube-to-tube resistances currently faced in CNT electrical devices and allow for large-scale application.
Publications
Carbon nanotubes (CNTs) have unique properties with promise to outperform the electrical characteristics of bulk copper, giving rise to its primary driver for use in electronic devices. The challenge still hindering their full exploitation stems from an inability to manufacture them to long lengths, resulting in a requirement to align and entwine them into a yarn or wire. There have been several methods presented in achieving this, however, the common disadvantage has been that they are only applicable to specific types and morphologies of CNTs. In the work reported here, using electrospinning as a universally applicable route for any CNT type, we re-engineer and optimise the various formulation, fabrication and processing steps required to manufacture CNT wires. Through a series of investigations using a materials agnostic approach, we experimentally probe the choice of solvent, surfactant and thermal treatment temperature of the CNT inks, demonstrating the CNT-type optimum using a range of commercially available single- double- and multiwalled CNTs. Finally, this allowed us to develop and probe an electrical conditioning process to further enhance the electrical performance, achieving the highest reported un-doped electrical conductivity of 36,000 S⋅m− 1 for electrospun CNT wires, or a specific conductivity of 0.2×106S·m−1/g·cm−3. [Display omitted]
Large-scale incorporation of nanomaterials into manufactured materials can only take place if they are suitably dispersed and mobile within the constituent components, typically within a solution/ink formulation so that the additive process can commence. Natural hydrophobicity of many nanomaterials must be overcome for their successful incorporation into any solution-based manufacturing process. To date, this has been typically achieved using polymers or surfactants, rather than chemical functionalization, to preserve the remarkable properties of the nanomaterials. Quantifying surfactant or dispersion technique efficacy has been challenging. Here we introduce a new methodology to quantify dispersions applicable to high-weight fraction suspensions of most nanomaterials. It’s based on centrifuging and weighing residue of undispersed material. This enables the determination of the efficacy of surfactants to disperse nanomaterials (e.g. ultrasonication power and duration) and leads to increased nanomaterial solution loading. To demonstrate this technique, we assessed carbon nanotube dispersions using popular surfactants: Benzalkonium chloride (ADBAC), Brij®52, Brij®58, Pluronic®F127, sodium dodecyl sulfate (SDS), sodium dodecylbenzenesulfonate (SDBS), Triton™ X-100, Triton™X-405 and Tween®80, evaluating the dispersion outcome when varying sonicator power and horn depth, as well as imaging sono-intensity within the solution with luminol. The methodology is shown to be applicable for high-weight fraction nanomaterial suspensions, enabling greater deployment.
By electrospinning poly(ethylene oxide) (PEO)-blended sodium dodecyl sulfate (SDS) functionalized carbon nanotube (CNT) solutions, we engineered single- and double-walled nanotubes into highly aligned arrays. CNT alignment was measured using electron microscopy and polarised Raman spectroscopy. Mechanical tensile testing demonstrates that a CNT loading of 3.9wt% increases the ultimate tensile strength and ductility of our composites by over a factor of 3, and the Young's modulus by over a factor of 4, to ∼260MPa. Transmission electron microscopy (TEM) reveals how the aligned nanotubes provide a solid structure, preventing polymer chains from slipping, as well as polymer crystallisation structures such as ‘shish-kebabs’ forming, which are responsible for the improved mechanical properties of the composite. Differential scanning calorimetry (DSC) and small angle X-ray scattering (SAXS) reveals micellar and hexagonal columnar structures along the axis of the fibers, some of which are associated with the presence of the CNT, where these hexagonal structures are associated with the SDS functionalization on the CNT surfaces. This work demonstrates the benefits of CNT alignment within composites, revealing the effectiveness of the electrospinning technique, which enables significantly improved functionality, increasing the utility of the composites for use in many different technological areas.
A simple, low-cost, linearly polarized reconfigurable reflectarray surface (RAS) is presented that can provide beam steering over a wide range of angles in one plane. The results for a prototype design demonstrated beam steering from 35° to 60° at 5.5 GHz. Simple equations describing the beam steering angle and overall size for a minimum radar cross-sectional area (RCS) are presented that aid the system designer. The concertina RAS can be manufactured using screen-printing techniques making this potentially a low-cost product that can meet the needs of widespread deployment needed by wireless systems. A sample design using an A2-sized sheet of paper increased a 5.5 GHz signal by 20 dB, eliminating a "dead spot" in the laboratory.
Thermoelectrics are a promising solution to the recovery of some of the 60% of the worldwide energy wasted as heat. However, their conversion efficiency is low and the best performing materials are brittle, toxic, and made of expensive ceramics. The challenge in developing better performing materials is in disrupting the electrical vs thermal conductivity correlation, to achieve low thermal conductivity simultaneously with a high electrical conductivity. Carbon nanotubes allow for the decoupling of the electronic density of states from the phonon density of states and this paper shows that flexible, thin films of double-walled carbon nanotube (DWCNT) can form effective n- and p-doped semiconductors that can achieve a combined Seebeck coefficient of 157.6 mu V K-1, the highest reported for a single DWCNT device to date. This is achieved through selected surfactant doping, whose role is correlated with the length of the hydrocarbon chain of the hydrophobic tail group of the surfactant's molecules. CNTs functionalized with Triton X-405 show the highest output power consisting of a single junction of p- and n-type thermoelectric elements, reaching as high as 67 nW for a 45 K temperature gradient. Thus enabling flexible, cheaper, and more efficient thermoelectric generators through the use of functionalized CNTs.
As a technique, electrospinning has been increasingly utilised for polymer nanofibre production, which has a growing list of advanced applications to which they are being applied. However, commercially scaling the process is challenging, especially when the uniformity of the nanofibres across the bulk of the material is important for the required application. At present, most commercially-scalable systems tend to rely on a drum or cylindrical-style electrode, where a multitude of electrospinning jets are formed with no specific controlled distribution or uniformity over its surface. These electrospinning systems also have the drawback of possessing a varying electrostatic field across the length of the electrode, resulting in a range of spinning conditions which result in an inconsistency in the produced nanofibres. Due to the high centrifugal stresses exerted on the polymer during electrospinning, controlling the electrostatic field is crucial for consistent nanofibre production, which forms the basis for applications such as cellular scaffolds and smart materials. In the work reported here, we utilise computational simulation to explore a range of electrode designs to achieve a large area electrospinning system with a balanced electrostatic field across its entire active surface. We demonstrate the output by producing a high-throughput of nanofibres with comparable properties to that of a traditional single spinneret system, but at a processing rate two orders of magnitude faster.
A method to simultaneously synthesize carbon-encapsulated magnetic iron nanoparticles (Fe-NPs) and attach these particles to multi-walled carbon nanotubes (MWCNT) is presented. Thermal decomposition of cyclopentadienyliron dicarbonyl dimer [(C5H5)(2)Fe-2(CO)(4)], over a range of temperatures from 250 degrees C to 1200 degrees C, results in the formation of Fe-NPs attached to MWCNT. At the same time, a protective carbon shell is produced and surrounds the Fe-NPs, covalently attaching the particles to the MWCNT and leading to resistance to acid dissolution. The carbon coating varies in degree of graphitisation, with higher synthesis temperatures leading to a higher degree of graphitisation. The growth model of the nanoparticles and subsequent mechanism of MWCNT attachment is discussed. Adsorption potential of the hybrid material towards organic dyes (Rhodamine B) has been displayed, an indication of potential uses as a material for water treatment. The material has also been electrospun into aligned nanocomposite fibres to produce a soft magnetic composite (SMC) with future applications in sensors and fast switching solenoids.
Steam treatment has been applied to our prefabricated highly aligned areas of electrospun carbon nanotube composite nano-fibres, leading to controlled and targeted removal of polymeric and amorphous carbon materials, resulting in areas of highly aligned, highly crystalline, pure nanotubes. Raman analysis shows how the ID to IG intensity ratio was reduced to 0.03, and the radial breathing mode peak intensity, used for nanotube diameter calculation, changes. Therefore, suggesting that some carbon nanotubes are more resistant to steam assisted oxidation, meaning that specific carbon nanotube diameters are preferentially oxidised. The remaining carbon nanotubes have displayed a significant improvement in both quality, with respect to defect density, and in crystallinity, resulting in an increased resistance to oxidation. These steam treated super resilient carbon nanotubes are shown to withstand temperatures of above 900 °C under ambient conditions. Applying this purification method to electrospun nano-fibres leads the way for the next generation of composite materials which can be used in high temperature extreme environments.
The need for the fabrication of a new generation of devices has developed with the next generation of ‘home’ engineers, which is resulting in an ever-increasing population interested in “do-it-yourself” electronics and the Internet of Things. However, this new trend should not be done at the expense of the environment. Almost all previous studies, related to the low-temperature processing of devices, fail to highlight the extent of the impact that the synthesis of these technologies have on both the environment and human health. In addition, the substrates typically used, are also often associated with major drawbacks such as a lack of biodegradability. In this paper, we fabricate a simple RC filter using various domestically available printing techniques, utilising readily available materials such as: carbon soots (carbon black) as an electric conductor, and egg white (albumen) as a dielectric. These devices have been fabricated on both polyethylene terephthalate (PET) and paper, which demonstrated the same performances on both substrates and revealed that recyclable substrates can be used without compromise to the devices’ performance. The filter was found to exhibit a cut-off frequency of 170 kHz, which made it suitable for high-frequency reception applications.
The feasibility of using self‐assembled InAs nanowire bottom‐gated field‐effect transistors as radio‐frequency and microwave switches by direct integration into a transmission line is demonstrated. This proof of concept is demonstrated as a coplanar waveguide (CPW) microwave transmission line, where the nanowires function as a tunable impedance in the CPW through gate biasing. The key to this switching capability is the high‐performance, low impedance InAs nanowire transistor behavior with field‐effect mobility of ≈300 cm2 V−1 s−1, on/off ratio of 103, and resistance modulation from only 50 Ω in the full accumulation mode, to ≈50 kΩ when the nanowires are depleted of charge carriers. The gate biasing of the nanowires within the CPW results in a switching behavior, exhibited by a ≈10 dB change in the transmission coefficient, S21, between the on/off switching states, over 5–33 GHz. This frequency range covers both the microwave and millimeter‐wave bands dedicated to Internet of things and 5G applications. Demonstration of these switches creates opportunities for a new class of devices for microwave applications based on solution‐processed semiconducting nanowires.
One of the major problems limiting the applications of electric double-layer (EDLC) supercapacitor devices is their inability to maintain their cell voltage over a significant period. Self-discharge is a spontaneous decay in charged energy, often resulting in fully depleted devices in a matter of hours. Here, a new method for suppressing this self-discharge phenomenon is proposed by using directionally polarized piezoelectric electrospun nanofiber films as separator materials. Tailored engineering of polyvinylidene fluoride (PVDF) nanofiber films containing a small concentration of sodium dodecyl sulfate (SDS) results in a high proportion of polar beta phases, reaching 38 +/- 0.5% of the total material. Inducing polarity into the separator material provides a reverse-diode mechanism in the device, such that it drops from an initial voltage of 1.6 down to 1 V after 10 h, as opposed to 0.3 V with a nonpolarized, commercial separator material. Thus, the energy retained for the polarized separator is 37% and 4% for the nonpolarized separator, making supercapacitors a more attractive solution for long-term energy storage.
Research into carbon nanotubes (CNTs) has been a hot topic for almost 3 decades, and it is now that we are beginning to observe the impact of advanced applictions of this nanomaterial in areas such as electronics. Currently, in order to mass produce CNT devices, either large-scale synthesis, followed by numerous energy-intensive processing steps or photolithography processes, including several sputter-deposition steps, are required to pattern this material to fabricate functional devices. In the work reported here, through the utilization of a universal catalyst precursor (cyclopentadienyl iron dicarbonyl dimer) and the optimization of solution parameters, patterned high-quality vertically aligned arrays of single- and few-walled CNTs have been synthesized via various inexpensive, commercially scalable methods such as inkjet printing, stamp printing, spray painting, and even handwriting. The two-step process of precursor printing, followed immediately by CNT growth, results in CNTs with a Raman I-D/I-G ratio of 0.073, demonstrating very high-quality nanotubes. This process eliminates time-consuming and costly CNT post processing techniques or the deposition of numerous substrate barrier and catalyst layers to achieve device manufacturing. As a result, this method has the potential to provide a route for the large-scale synthesis of high-quality single- and few-walled CNTs that can be applied in industrial settings.