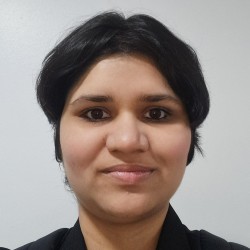
Sheeba Pathak
About
My research project
e-waste Management using Operations Research to strike a balance between sustainability, profitability and leanThe UN SDG Goal No.12 of responsible consumption and production lays the responsibility of ethical production on businesses and thus sustainability is taking centre-stage of boardroom discussions. However, it is common knowledge that sustainable measures are not considered to be cost effective and to bust this myth my research would like to showcase a balance between optimality, profitability and sustainability across the supply chain and operations in industrial applications demonstrating that it is indeed possible.
I aim to use Operations Research techniques to show its applicability and affirmation and even look forward to develop a case study using industry data.
Supervisors
The UN SDG Goal No.12 of responsible consumption and production lays the responsibility of ethical production on businesses and thus sustainability is taking centre-stage of boardroom discussions. However, it is common knowledge that sustainable measures are not considered to be cost effective and to bust this myth my research would like to showcase a balance between optimality, profitability and sustainability across the supply chain and operations in industrial applications demonstrating that it is indeed possible.
I aim to use Operations Research techniques to show its applicability and affirmation and even look forward to develop a case study using industry data.
Affiliations and memberships
ResearchResearch interests
Operations Research | Lean Six Sigma | Optimisation | Sustainable Supply Chains and Operations | Economics in Operations and Supply Chains
Research projects
Mathematical Construct to Assess if your Product is SustainableA working paper:-
Abstract
Humans are consuming resources faster than they are being replenished, thus there is a lot of emphasis on ensuring resources are available for future generations. A major consumer of these resources are industries and in specific the Energy sector with the automobile sector being one of the leading consumers’. Thus tracking of greenhouse emissions by firms and ensuring a mitigation plan has become centre stage to discussions in the corporate world. This paper thus provides a comprehensive list of formulae and calculation methodologies to carry out these assessments of the ecological and Carbon footprints of automobile firms at a product and process level. It uses the Life-cycle Inventory Assessment (LCA) methodology to arrive at these calculations to understand the present emissions and prepare an action plan to reduce it thereafter. The authors hope this will be a first step in addressing climate change impact and be a stepping stone for further actions to achieve the United Nations Sustainable Development Goal No. 12 of responsible production and consumption.
Keywords: Life-cycle Inventory Analysis, Greenhouse emissions
How to Optimise the Reverse Logistics for e-waste Management?A working paper:-
Abstract
This is a major business opportunity and hence traction is being witnessed in this industry towards the effective management of e-waste. To ensure optimal collection of such products and parts as well as appropriate disposal or recycling of these parts and products it is important to have a unified framework. While the United Nations Sustainable Development Goals mention the need for responsible production and consumption firms are still exploring methods to ensure e-waste collection, recycling or disposal is not a costly affair. This means that many aspects of the supply chain and its allied operations would come into play for not just collection and disposal or recycling but also for the purpose of ensuring a reverse logistics mechanism is in place for e-waste management.
The present paper provides a holistic take on each of the supply chain’s sub functions of sourcing, procurement, inbound logistics, manufacturing, outbound logistics, last mile distribution and reverse logistics.
Each stage of the supply chain will be observed to understand the forward and reverse flow of the electrical or electronic components. On studying different models of optimising e-waste reverse logistics, a novel model is proposed that ensures the e-waste is managed optimally with respect to cost as well as sustainable measures. The network planning of e-waste management centres for refurbishment and recycling are also discussed by means of designing sub-hubs, centres and include the relatively new concept of makerspaces for the purpose of repair/maintenance and re-manufacture of electrical items-. The findings of this review suggest for CReW set-up caters to not just segregation of e-waste but also ensures the materials’ applications for upcycling or recycling and extending the product lifecycle.
Research interests
Operations Research | Lean Six Sigma | Optimisation | Sustainable Supply Chains and Operations | Economics in Operations and Supply Chains
Research projects
A working paper:-
Abstract
Humans are consuming resources faster than they are being replenished, thus there is a lot of emphasis on ensuring resources are available for future generations. A major consumer of these resources are industries and in specific the Energy sector with the automobile sector being one of the leading consumers’. Thus tracking of greenhouse emissions by firms and ensuring a mitigation plan has become centre stage to discussions in the corporate world. This paper thus provides a comprehensive list of formulae and calculation methodologies to carry out these assessments of the ecological and Carbon footprints of automobile firms at a product and process level. It uses the Life-cycle Inventory Assessment (LCA) methodology to arrive at these calculations to understand the present emissions and prepare an action plan to reduce it thereafter. The authors hope this will be a first step in addressing climate change impact and be a stepping stone for further actions to achieve the United Nations Sustainable Development Goal No. 12 of responsible production and consumption.
Keywords: Life-cycle Inventory Analysis, Greenhouse emissions
A working paper:-
Abstract
This is a major business opportunity and hence traction is being witnessed in this industry towards the effective management of e-waste. To ensure optimal collection of such products and parts as well as appropriate disposal or recycling of these parts and products it is important to have a unified framework. While the United Nations Sustainable Development Goals mention the need for responsible production and consumption firms are still exploring methods to ensure e-waste collection, recycling or disposal is not a costly affair. This means that many aspects of the supply chain and its allied operations would come into play for not just collection and disposal or recycling but also for the purpose of ensuring a reverse logistics mechanism is in place for e-waste management.
The present paper provides a holistic take on each of the supply chain’s sub functions of sourcing, procurement, inbound logistics, manufacturing, outbound logistics, last mile distribution and reverse logistics.
Each stage of the supply chain will be observed to understand the forward and reverse flow of the electrical or electronic components. On studying different models of optimising e-waste reverse logistics, a novel model is proposed that ensures the e-waste is managed optimally with respect to cost as well as sustainable measures. The network planning of e-waste management centres for refurbishment and recycling are also discussed by means of designing sub-hubs, centres and include the relatively new concept of makerspaces for the purpose of repair/maintenance and re-manufacture of electrical items-. The findings of this review suggest for CReW set-up caters to not just segregation of e-waste but also ensures the materials’ applications for upcycling or recycling and extending the product lifecycle.
Publications
Impact: A Framework and Model Proposition
This paper is an attempt to study the best practices in the supply chain and operations arena of firms across sectors, and propose a framework and a model to arrive at profitable options and alternatives towards achieving sustainability. A test of a small-scale manufacturing apparel unit is taken to check the model; it is found that sub-functions of each supply chain component by itself can be used to reduce costs and achieve sustainability. Vendor sourcing, logistics, and manufacturer’s make-or-buy decision (buy) is used to emphasise the model’s sub-functions utility. Some sub-functions are not applicable for the case in question; however, the same is aimed towards manufacturing automobile firms to deploy in future researches
The main aim of this study is to study the e-tailing industry in India and understand the nuances of the problem of stock-out. Thus, the leading e-tailing firm-Flipkart is selected for the same. With the advent of the internet and the increase in its usage; India is expected to observe a high surge of e-commerce. Thus, its inventory regulations are a cause of concern. The study explores the causes for the occurrence of stock-outs. This paper also sheds light on probable solutions to combat these constraints of inventory stock-outs. Apart from fundamental process changes and improvements, suggestions of a strong business intelligence system and integration via ERP systems is also recommended.
The supply chain requires the collaboration and synchronisation of each entity for the success of need fulfilment. Hence, entities cannot work in isolation. Thus, the need for collaborations with reference to not just customers and the manufacturer but also with the supplier is pivotal. ABC’s two suppliers are selected for the scope of the study. Their manufacturing processes are understood and the lead times are analysed. The researcher arrived at the conclusion that immense number of shortages amount due to lack of information sharing and transparency. Hence, with the help of IT support an effective supplier network is introduced and implemented for the supplier PQR Incorporation. This is then used as a benchmark for another supplier: XYZ Motors.
Spare Parts Division
Automobile manufacturing firms rely heavily on their suppliers for timely production of vehicles. Hence, the ownership and responsibility of the suppliers’ delivery to the firm increases. However, following the 80-20 rule, suppliers too tend to cater to the firms that give them a fair share of business, along with a continuous flow. Some suppliers are able to adhere to these norms of providing the parts the purchasing firm demands; however, several are unable to do so. The issues of line stoppage, delays, and non-conformance of production arise because of delays, deficits, and no-show of critical parts. Thus, many firms not only resort to the ABC (Activity-Based Classification) of parts to test their inventories, but also classify their suppliers on a similar categorisation, depending on several parameters of deliverability, quality, and costs. This paper aims to highlight the poor performing suppliers’ reasons for poor performance, and suggests several solutions for improvement, after performing a historical analysis and performing gemba. The short-term solutions of alterations in plans and vendors allow room to achieve 100% delivery from the vendors, while long-term solutions of system ERP requirements allow management intervention to seek system software that eliminate non-value added (NVA) activities that are manual and are moved to an ERP system instead.