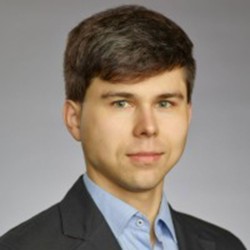
Dr Michal Delkowski
Publications
Future space travel needs ultra-lightweight and robust structural materials that can 10 withstand extreme conditions with multiple entry points to orbit to ensure mission reliability. This is unattainable with current inorganic materials, while ultra-highly stable carbon fibre reinforced polymers (CFRP´s) have shown susceptibility to environmental instabilities and electrostatic discharge, thereby limiting the full lightweight potential of CFRP. To improve space travel and structural engineering further, a robust CFRP is required. Here, we address these 15 challenges and present a superlattice nano-barrier enhanced CFRP (SNBE-CFRP) with a density of ~3.18 [g/cm 3 ] that blends within the mechanical properties of the CFRP, thus becoming part of the composite itself. We demonstrate composites with enhanced radiation resistance coupled with electrical conductivity (3.2x10-8 Ωm), while ensuring ultra-dimensionally stable physical properties even after temperature cycles from 77 to 573 K. 20
Thermal control is essential to guarantee the optimal performance of most advanced electronic devices or systems. In space, orbital satellites face the issues of high thermal gradients, heating, and different thermal loads mediated by differential illumination from the Sun. Todaýs state-of-the-art thermal control systems provide protection; however, they are bulky and restrict the mass and power budgets for payloads. Here, we develop a lightweight optical superlattice nanobarrier structure to provide a smart thermal control solution. The structure consists of a moisture and outgassing physical barrier (MOB) coupled with atomic oxygen (AO)-UV protection functionality. The nanobarrier exhibits transmission and reflection of light by controlling the optical gap of individual layers to enable high infrared emissivity and variable solar absorptivity (minimum Δα = 0.30) across other wavelengths. The multifunctional coating can be applied to heat-sensitive substrates by means of a bespoke room-temperature process. We demonstrate enhanced stability, energy-harvesting capability, and power savings by facilitating the radiation cooling and facility for active self-reconfiguration in orbit. In this way, the reduction of the operating temperature from ∼120 to ∼60 °C on space-qualified and nonmechanically controlled composite structures is also demonstrated.
The endeavors to develop manufacturing methods that can enhance polymer and composite structures in spacecraft have led to much research and innovation over many decades. However, the thermal stability, intrinsic material stress, and anisotropic substrate properties pose significant challenges and inhibit the use of previously proposed solutions under extreme space environment. Here, we overcome these issues by developing a custom-designed, plasma-enhanced cross-linked poly(p-xylylene):diamond-like carbon superlattice material that enables enhanced mechanical coupling with the soft polymeric and composite materials, which in turn can be applied to large 3D engineering structures. The superlattice structure developed forms an integral part with the substrate and results in a space qualifiable carbon-fiber-reinforced polymer featuring 10–20 times greater resistance to cracking without affecting the stiffness of dimensionally stable structures. This innovation paves the way for the next generation of advanced ultra-stable composites for upcoming optical and radar instrument space programs and advanced engineering applications. • Plasma-enhanced cross-linked poly(p-xylylene) (PECLP):DLC superlattice is deposited • PECLP exhibits ∼10 times higher elastic modulus compared to classic poly(p-xylylene) • PECLP:DLC barrier provides near-zero stress conditions for use on composites • Enhanced composites exhibit mechanical integrity and improved crack resistivity Aerospace Engineering; Engineering materials; Materials physics
The quest to develop materials that enables the manufacture of dimensionally ultra-stable structures for critical-dimension components in spacecraft, has led to much research and evolution of carbon-fibre reinforced polymer materials (CFRP) over many decades. This has resulted in structural designs that feature a near-zero coefficient of thermal expansion. However, the dimensional instabilities that result from moisture ingression and release remains the fundamental vulnerability of the matrix, which restricts many such applications. Here, we address this challenge by developing a space-qualifiable physical surface barrier that blends within the mechanical properties of the composite, thus becoming part of the composite itself. The resulting enhanced composite features mechanical integrity and strength that is superior to the underlying composite, whilst remaining impervious to moisture and outgassing. We demonstrate production capability on a model-sized component for Sentinel-5 mission and demonstrate such capability for future European Space Agency (ESA) and National Aeronautics and Space Administration (NASA) programs such as Copernicus Extension, Earth Explorer and Science Cosmic Visions.