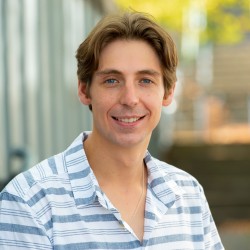
Dr Henry Ayres MEng
Academic and research departments
School of Mechanical Engineering Sciences, EPSRC Centre for Doctoral Training in Micro- and NanoMaterials and Technologies.About
My research project
Advanced Deployable Structures for Space FlightHenry is currently undertaking a PhD at the University of Surrey, which is sponsored by the Atomic Weapons Establishment (AWE), within the field of advanced deployable structures for space flight.
The small satellite market is a rapidly growing and developing sector, in which deployable structures allow for small satellites to perform missions that previously would have required much more expensive, large satellites. This project evaluates the feasibility of a new deployment method for spacecraft rollable booms. The use of a piezoelectric linear shear motor enables a more compact, reliable, and low power rollable boom deployment mechanism which increasse the capabilities of small satellites.
Supervisors
Henry is currently undertaking a PhD at the University of Surrey, which is sponsored by the Atomic Weapons Establishment (AWE), within the field of advanced deployable structures for space flight.
The small satellite market is a rapidly growing and developing sector, in which deployable structures allow for small satellites to perform missions that previously would have required much more expensive, large satellites. This project evaluates the feasibility of a new deployment method for spacecraft rollable booms. The use of a piezoelectric linear shear motor enables a more compact, reliable, and low power rollable boom deployment mechanism which increasse the capabilities of small satellites.
My qualifications
Publications
This paper describes a novel deployment method for rollable spacecraft booms that is suitable for high-force and precision deployment applications where reliability and low mass are critical. The piezoelectric linear shear motor controls and constrains the boom at the deployer exit with longitudinal and shear actuators through a 'pinch and push' process. This design eliminates the 'blossoming' failure mode and produces a less massive device that does not generate a magnetic field. Simulation and testing are used to evaluate the major limitation of rollable boom slippage through the device. The force at which this scenario occurs is dependent upon the friction force exerted between the tape-spring and linear motor, and hence can be characterised by the coefficient of static friction and the normal force acting between the linear motor and the rollable boom. The piezoelectric linear shear motor provides a high-force, high-precision, easily scalable deployment method.