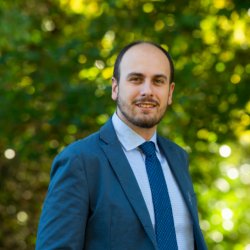
Dr Francesco Ciampa
About
Biography
Dr Francesco Ciampa is an Associate Professor (Reader) in Structural Integrity and Composites at the Department of Mechanical Engineering Sciences of the University of Surrey. Dr Ciampa has multi-disciplinary experience in numerical and experimental testing of materials and structures for the aerospace and energy sectors, in which non-destructive inspection, structural health monitoring, and multifunctional composites have been his major focus areas. Dr Ciampa specialises in ultrasonic and thermographic techniques for both metallic and composite materials and he has created new damage detection solutions that are currently used by leading aerospace companies. He has received funding from various sources as both PI and Co-I including DSTL, Royal Society, EPSRC, Leverhulme Trust and the EU.
Teaching
- EEEM049 - Spacecraft Structures and Mechanisms
- ENG2096 - Aircraft Structures & Aeroelasticity
- ENG2087 - Design Project
Publications
The through-the-thickness reinforcement of carbon-epoxy composite joints with shape memory alloy (SMA) tufts has shown significant improvement of the mechanical strength, fracture toughness, and delamination resistance. This study explores the thermal-electric properties of SMA filaments tufted in composite T-joints to exhibit multiple functionalities including material-enabled thermographic inspection and structural health monitoring via in-situ strain sensing. Infrared thermography image analysis was performed on both pristine and damaged T-joint specimens subject to pull-off testing. Experimental results showed that the heat generated by SMA tuftsmeasured by an infrared camera provided accurate indication of delamination perpendicular to the tuft direction. SMA tufts were also used as strain sensors embedded within the T-joint. Local changes of the electrical resistance in SMA filaments, both separately and within the joint, were observed during pulling loads. Digital Image Correlation measurements exhibited good correlation between electrical resistance variations and the opening of delamination. These results pave the way for the development of multifunctional composite joining systems combining enhanced through-the-thickness damage tolerance and self-sensing capabilities.
In this article, we demonstrated the physical application of a portable infrared (IR) security scanning system for the non-contact and stand-off detection of target objects concealed underneath clothing. Such a system combines IR imaging and transfer learning with convolutional neural network (CNN) to enhance the detection of weak thermal signals and automate the classification of IR images. A mid-wavelength IR detector was used to record the real-time heat emitted from the clothing surface by human subjects. Concealed objects reduce transmissivity of IR radiation from the body to the clothing surface, generally showing lower IR intensity compared to regions without objects. Due to limited resource for training data, the transfer learning approach was applied by fine tuning a pre-trained CNN ResNet-50 model using the ImageNet database. Two image types were here investigated, i.e., raw thermal and Fuzzy-c clustered images. Receiver operating characteristic curves were built using a holdout set, showing an area-under-the-curve of 0.8934 and 0.9681 for the raw and Fuzzy-c clustered image models, respectively. The Gradient-weighted Class Activation Mapping (Grad-CAM) visualisation method was used to improve the target identification, showing accurate prediction of the object area. It was also found that complex clothing, such as those composed of materials of different transmissivity, could mislead the model in classification. The proposed IR-based detector has shown potentials as a non-contact, stand-off security scanning system that can be deployed in diverse locations and ensure higher safety of civilians.
This paper describes a novel deployment method for rollable spacecraft booms that is suitable for high-force and precision deployment applications where reliability and low mass are critical. The piezoelectric linear shear motor controls and constrains the boom at the deployer exit with longitudinal and shear actuators through a 'pinch and push' process. This design eliminates the 'blossoming' failure mode and produces a less massive device that does not generate a magnetic field. Simulation and testing are used to evaluate the major limitation of rollable boom slippage through the device. The force at which this scenario occurs is dependent upon the friction force exerted between the tape-spring and linear motor, and hence can be characterised by the coefficient of static friction and the normal force acting between the linear motor and the rollable boom. The piezoelectric linear shear motor provides a high-force, high-precision, easily scalable deployment method.
A thermal management system for lithium-ion batteries is an essential requirement for electric vehicle operation due to the large amount of heat generated by these cylindrical batteries during fast charging/discharging. Previously, researchers have focused mostly on pouch and prismatic cells with heat pipes arranged in the horizontal direction. The current study introduces a novel vertically-oriented heat-pipe-based hybrid cooling battery thermal management system (BTMS) that numerically evaluates the thermal performance of the cylindrical batteries and the flow pattern within the cooling channel at C rates as high as 8C. The model was experimentally validated using five round heat pipes in a vertical orientation utilizing the effect of gravity to assist condensate flow through the heat pipe. The heat pipes were arranged in a staggered pattern to improve the overall heat transfer performance by means of forced convective cooling. This design allowed for maximizing the heat transfer process despite the lack of contact between the cylindrical-shaped batteries and round-shaped heat pipes. During this study, the temperatures of the evaporator end and the condenser end of the heat pipes and battery surfaces were monitored, and the thermal performances of the system were determined at varying inlet cooling liquid temperatures (15, 20, 25 °C) and high rates of 4C and 8C. Representatively, the proposed hybrid BTMS could maintain a maximum battery surface temperature of around 64 °C and a temperature difference between cells under 2.5 °C when the inlet velocity was 0.33 L/min and the cooling liquid temperature was 25 °C. The high temperatures reached the fourth and fifth heat pipes because they are part of the backflow design and are affected by backflow temperature. Nevertheless, the current design shows that the proposed system can maintain battery surface temperatures well within 5 °C.
Multifunctional fibre reinforced polymer (FRP) composites combine multiple properties that can include mass efficiency, damage resistance, damage tolerance, self-repair, in-service health monitoring and ease of inspection. This paper describes a new type of multifunctional FRP composite material that enables large improvements to the interlaminar fracture toughness and damage tolerance whilst also allowing rapid self-sensing and material-enabled thermography capabilities. The composite material is reinforced in the through-thickness direction using shape memory alloy (SMA) wires inserted by tufting.Tufting is a cost-effective manufacturing process that uses commercially available automated systems to insert yarns in the through-the-thickness direction of dry fabric preforms [1]. Tufting uses a single needle to penetrate the fabric stack, and requires access only from a single side of the preform. As shown in Fig. 1, thin and flexible SMA filaments made of nitrol (Ni-Ti alloy) were tufted into six layers of 0˚/90˚ non-crimp carbon fabric using a KSL RS 522 tufting machine mounted on a KUKA KR240–2 robotic arm. The tufted fabric was infused with epoxy resin using the resin transfer moulding (RTM) process. The final cured composite panel was cut into double cantilever beam (DCB) coupons to perform mode I interlaminar fracture toughness tests according to the ASTM D5528-01 specification.
Abstract We hereby report for the first time on the design, manufacturing and testing of a three-dimensional (3D) nearly-periodic, locally resonant phononic crystal (PnC). Most of the research effort on PnCs and metamaterials has been focused on the enhanced dynamic properties arising from their periodic design. Lately, additive manufacturing techniques have made a number of designs with intrinsically complex geometries feasible to produce. These recent developments have led to innovative solutions for broadband vibration attenuation, with a multitude of potential engineering applications. The recently introduced concept of rainbow metamaterials and PnCs has shown a significant potential for further expanding the spectrum of vibration attenuation in such structures by introducing a gradient profile for the considered unit cells. Given the above, it is expected that designing non-periodic PnCs will attract significant attention from scientists and engineers in the years to come. The proposed nearly-periodic design is based on cuboid blocks connected by curved beams, with internal voids in the blocks being implemented to adjust the local masses and generate a 3D rainbow PnC. Results show that the proposed approach can produce lightweight PnCs of a simple, manufacturable design exhibiting attenuation bandwidths more than two times larger than the equivalent periodic designs of equal mass.
A new type of fibre reinforced polymer composite is presented that uniquely combines high delamination resistance with crack closure properties via the use of tufted shape memory alloy (SMA) filaments. A carbon-epoxy laminate was tufted in the through-thickness direction using thin SMA filaments of Ni-Ti alloy (nitinol). The SMA tufts increase the mode I interlaminar fracture toughness of the laminate by forming a large-scale bridging process zone along the delamination crack. Following crack growth, electrical heating of the SMA tufts activates a shape memory effect that partially closes the delamination. Finite element (FE) analysis reveals that complete crack closure occurs when the SMA tufts are not deformed above the shape memory strain limit. The use of SMA tufts offers the important opportunity to produce a new class of damage tolerant composite material that both resist the opening and aid the closing of delamination cracks formed by overloading, impact or other damaging events.
An optimal steering law for sails that exploit both solar and infrared planetary radiation pressure is presented in this paper. The optimal steering law maximises the orbit raise over one revolution of the sail around the planet. An indirect analytical approach, that uses Pontryagin Minimum Principle, is used to develop specialised steering laws for the sunlit and eclipse cases in a planar motion scenario. The law for the sunlit case uses both the solar and infrared radiation emitted from the planet, while the law for the eclipse case finds the optimal sail attitude that maximises the raise of the orbit using only the planetary radiation. Numerical results show that these laws lead to better performance in terms of orbit raising against other sub-optimal and optimal strategies exploiting the solar radiation pressure only. A numerical study is also carried out to show the effects of the reflectivity coefficient in the infrared band on the orbital motion of the sail.
Infrared imaging-based machine vision (IRMV) is the technology used to automatically inspect, detect, and analyse infrared images (or videos) obtained by recording the intensity of infrared light emitted or reflected by observed objects. Depending on whether controllable excitation is used during the imaging of infrared rays, thermal IRMV can be categorised into passive thermography and active thermography. Passive thermography is an important supplement to conventional machine vision based on visible light and is a valid imaging tool for self-heating objects such as the human body and electrical power devices. Active thermography is a non-destructive testing method for the quality evaluation and safety assurance of non-self-heating objects. In active thermography, the trend is to inspect rapidly, reliably, and intelligently by introducing multiple-mode excitation sources and artificial intelligence. The rapid development of deep learning makes IRMV more and more intelligent and highly automated, thus considerably increasing its range of applications. This paper reviews the principle, cameras, and thermal data of IRMV and discusses the applications of deep learning applied to IRMV. Case studies of IRMV and deep learning on various platforms such as unmanned vehicles, mobile phones and embedded systems are also reported.
One of fundamental steps in the infrared thermographic process is the accurate segmentation of defects displayed on thermal images. State-of-the art segmentation algorithms are still inefficient to background noise, which may cause poor damage detection. In this study, an infrared image segmentation algorithm combined with artificial intelligence-based technology such as the variational level set and fuzzy clustering algorithm is proposed to enhance the quality of thermal images for damage assessment. Local Shannon entropy and fuzzy membership functions are introduced into the external clustering energy in order to make the algorithm robust to the clustering segmentation of noisy images. A higher-order derivative edge detection operator is used in the regularization energy to solve the singularity in the evolution of the level set function. An internal penalty energy is also introduced into the energy functional to avoid the re-initialization of the level set function and reduce the computational time. Experimental results on thermographic data are shown to demonstrate the efficiency and robustness of the proposed methodology.
Nonlinear ultrasonic methods typically measure second harmonic waves for a rapid and sensitive detection of material micro-cracks. However, fictitious second harmonics generated by the ultrasonic equipment can interfere with signal measurements, causing poor damage detection. This paper aims at enhancing the damage sensitivity of nonlinear ultrasound by developing acrylic phononic crystal waveguide transducers using Polyjet additive manufacturing, which can filter out undesired nonlinear harmonic waves. These sensing devices consist of traditional piezoelectric sensors surface bonded on periodically corrugated structures. Such periodicity can induce stop band frequencies in which the propagation of ultrasonic waves is inhibited. Nonlinear ultrasonic tests confirmed the filtering capabilities of phononic crystal transducers to suppress harmonics created by the ultrasonic instrumentation, thus enabling second harmonic detection on a damage aluminium plate. These results pave the way for simpler, automatable and more accurate nonlinear ultrasonic inspection systems.
Noise harms the effectiveness of imaging algorithms for damage localisation. Traditional impedance-based algorithms are not effective under noisy inspections. A New impedance-based imaging algorithm for damage localisation was proposed. New imaging algorithm is effective for the measurement taken under noise. The electro-mechanical impedance (EMI) measurements have been extensively studied in recent years to provide a reliable diagnosis of aerospace infrastructures. Existing imaging algorithms for EMI-based damage localisation have been proposed for controlled inspection environments or under the sole influence of temperature variations. However, the presence of signal noise may alter impedance signals and limit the use of the EMI method in real operating scenarios. Based on this issue, this short communication proposes a novel EMI probabilistic imaging algorithm for damage localisation under noisy inspections. Furthermore, as another advantage compared to traditional techniques, which do not perform a noise compensation, the proposed application does not require high computational cost since it does not require licensed software or the calculation of acoustic parameters. Experimental results on an aluminium plate-like structure revealed that the new algorithm proved to be adequate to image the location of damage under noise influence as opposed to traditional approaches.
Adhesively bonded joints are susceptible to contamination of surfaces during manufacture and environmental deterioration in real operating conditions. These may cause the generation of so-called “kissing bonds” that can dramatically alter the strength of the joint leading to premature failure. Nonlinear acousto-ultrasonic (AU) techniques have shown great potential for monitoring kissing bonds with piezoelectric sensors permanently installed on the structural joint, thus enabling online and in-situ inspection. This paper investigated the combined contact acoustic nonlinearity (CAN) and local damage resonance (LDR) effects in the presence of kissing bonds in adhesive joints. Experimental nonlinear AU tests showed the formation of LDR frequency down-shifts and “jumps” of the fundamental damage resonance in adhesively bonded aluminium joints, with the kissing bond located internally to the overlapping region between the two adherends. These results were supported by a theoretical model based on the solution of the nonlinear Duffing's equation, under the assumption that the debonded region is a damped nonlinear harmonic oscillator subject to harmonic forcing. The Harmonic Balance Method was used to solve the nonlinear differential problem, showing the generation of frequency down-shifts via the dependence of the ratio between the excitation and LDR frequencies with the amplitude of the fundamental damage resonance. Additionally, two-dimensional finite element simulations using a reduced order model based on the Craig-Bampton technique were carried out to support experimental AU tests for the the identification of the LDR frequency and the generation of nonlinear resonance effects. Good agreement between analytical, numerical, and experimental results revealed that a monitoring approach combining CAN and LDR is an extremely efficient and sensitive tool for ensuring integrity and safety of structural adhesive joints.
Literature offers a quantitative number of diagnostic methods that can continuously provide detailed information of the material defects and damages in aerospace and civil engineering applications. Indeed, low velocity impact damages can considerably degrade the integrity of structural components and, if not detected, they can result in catastrophic failure conditions. This paper presents a nonlinear Structural Health Monitoring (SHM) method, based on ultrasonic guided waves (GW), for the detection of the nonlinear signature in a damaged composite structure. The proposed technique, based on a bispectral analysis of ultrasonic input waveforms, allows for the evaluation of the nonlinear response due to the presence of cracks and delaminations. Indeed, such a methodology was used to characterize the nonlinear behaviour of the structure, by exploiting the frequency mixing of the original waveform acquired from a sparse array of sensors. The robustness of bispectral analysis was experimentally demonstrated on a damaged carbon fibre reinforce plastic (CFRP) composite panel, and the nonlinear source was retrieved with a high level of accuracy. Unlike other linear and nonlinear ultrasonic methods for damage detection, this methodology does not require any baseline with the undamaged structure for the evaluation of the nonlinear source, nor a priori knowledge of the mechanical properties of the specimen. Moreover, bispectral analysis can be considered as a nonlinear elastic wave spectroscopy (NEWS) technique for materials showing either classical or non-classical nonlinear behaviour.
Impact damage is a major concern for new generation aircraft composite components due to their low impact resistance capabilities. The development of an impact location and force reconstruction algorithm would provide rapid and efficient prediction of damage occurrence, thus making structures safer and creating maintenance inspection procedures more efficient, thus saving time and costs. However, state-of-the-art impact force reconstruction algorithms use reference data from numerical simulations and require a detailed knowledge of mechanical properties, which are difficult to obtain under real operational conditions. This paper presents a hierarchical impact force reconstruction algorithm that relies on experimental structural responses measured by a sparse array of surface bonded receiving ultrasonic transducers. This algorithm uses time reversal method to retrieve the location of an impact source and interpolation techniques based on hierarchical radial basis functions to calculate the transfer function at the impact point and reconstruct the impact force history. A number of impact testing were performed on a composite plate-like structure and a wing stringer-skin panel, and compared with impact force algorithms available in literature. Experimental results revealed that the proposed impact force reconstruction method was able to extrapolate the information associated with points far from the impact location and determine the impact force history with high level of accuracy in a real aircraft structure. Since the proposed algorithm requires the calibration of transfer functions from a very sparse training set of data and it does not need numerical models of the component under investigation, it demonstrates its potential as a useful monitoring tool for impact force reconstruction in composite components for full-scale aircraft structural applications leading to timely and cost-efficient inspections. © 2019 IOP Publishing Ltd.
Non-invasive scanning techniques are vital for threat detection in areas of heavy human traffic to ensure civilian safety. Longer waves in the electromagnetic spectrum, such as millimetre waves and terahertz, have been successfully deployed in commercial personnel scanning systems. However, these waves suffer from lower image resolution due to their longer wavelengths.Infrared has a shorter wavelength compared to millimetre waves and terahertz. Infrared has a lower penetration potential compared to its counterparts but boosts higher image resolution due to its shorter wavelength. Machine learning techniques, i.e., principal component analysis, active contour, and Fuzzy-c, were applied to the infrared images to improve the visualization of concealed objects.Convolutional neural networks, i.e., ResNet-50, were explored as an automatic classifier for the presence of concealed objects. A transfer learning approach was applied to an ImageNet pre-trained ResNet-50 model. After preprocessing the IR images using Fuzzy-c, two models were trained, using 900 and 3082 images, respectively. Evaluating the models using a confusion matrix and receiver operating characteristic curve, an area-under-curve of 0.869 and 0.922 was obtained. An optimization procedure was used to determine the model threshold, resulting in a prediction error of 19.9% and 14.9%, respectively.
The most commonly encountered type of damage in aircraft composite structures is caused by low-velocity impacts due to foreign objects such as hail stones, tool drops and bird strikes. Often these events can cause severe internal material damage that is difficult to detect and may lead to a significant reduction of the structure’s strength and fatigue life. For this reason there is an urgent need to develop structural health monitoring systems able to localise low-velocity impacts in both metallic and composite components as they occur. This article proposes a novel monitoring system for impact localisation in aluminium and composite structures, which is able to determine the impact location in real-time without a-priori knowledge of the mechanical properties of the material. This method relies on an optimal configuration of receiving sensors, which allows linearization of well-known nonlinear systems of equations for the estimation of the impact location. The proposed algorithm is based on the time of arrival identification of the elastic waves generated by the impact source using the Akaike Information Criterion. The proposed approach was demonstrated successfully on both isotropic and orthotropic materials by using a network of closely spaced surface-bonded piezoelectric transducers. The results obtained show the validity of the proposed algorithm, since the impact sources were detected with a high level of accuracy. The proposed impact detection system overcomes current limitations of other methods and can be retrofitted easily on existing aerospace structures allowing timely detection of an impact event.
Ultrasonic systems based on 'smart' composite structures with embedded sensor networks can reduce both inspection time and costs of aircraft components during maintenance or in-service. This paper assessed the tensile strength and fatigue endurance of carbon fibre reinforced plastic (CFRP) laminates with embedded piezoelectric (PZT) transducers, which were covered with glass fibre patches for electrical insulation. This sensor layout was proposed and tested by the authors in recent studies, proving its suitability for nonlinear ultrasonic detection of material damage without compromising the compressive, flexural or interlaminar shear strength of the 'smart' CFRP composite. In this work, CFRP samples including PZTs (G-specimens) were tested against plain samples (P-specimens), and their mean values of tensile strength and fatigue cycles to failure were found to be statistically the same (910 MPa and 713 000 cycles) using the one-way analysis of variance method. The same tests on P- and G-specimens with barely visible impact damage (BVID) showed that the corresponding group means were also the same (865 MPa and 675 000 cycles). Nonlinear ultrasonic experiments on impacted G-samples demonstrated that embedded PZTs could monitor the growth of BVID during fatigue testing, for a minimum of 480 000 cycles. This was achieved by calculating an increase of nearly two orders of magnitude in the ratio of second-to-fundamental harmonic amplitude. Finally, PZT transducers were confirmed functional under cyclic loading up to ∼70% of sample's life, since their capacitance remained constant during ultrasonic testing.
Summary Structural health monitoring systems for the localisation of acoustic emission (AE) events have been developed in the past few years for aircraft components. However, these systems still require complex and heavy electrical wiring for each sensing device and sophisticated algorithms for the localisation of AE signals, which inevitably increases both weight and costs. This paper reports the creation of a low‐power (few hundred mW) and low‐weight (~30 g) global navigation satellite system‐based wireless sensor network for the identification of AE events in aircraft structures. Each wireless node is instrumented with a low‐power micro‐controller, a radio frequency wireless transceiver, an analogue‐to‐digital converter, and a global navigation satellite system receiver for accurate time synchronisation. The AE coordinates and the speed of propagating waves are determined by using a localisation algorithm relying on time of arrival measurements. A peak amplitude detection system is implemented to process the AE data recorded by the wireless sensor network. The AE time features are locally extracted by the individual wireless modules and transferred to a remote processing unit for the execution of the localisation algorithm. Experimental results revealed that AE sources generated by low‐velocity impacts are identified with a high level of accuracy. The successful implementation of the proposed wireless sensor network demonstrates its suitability for continuous and autonomous structural health monitoring aerospace applications.
In order to overcome the current limitations of the impact localisation process in composite materials, such as the a-priori knowledge of the mechanical properties and the direction dependency of the wave speed, a novel method is here proposed based on the machine learning approach. The algorithm is formed by two steps: the first is the training process, in which a baseline consisting of the structural responses due to impact tests is acquired; the second one evaluates the impact location exploiting the highest cross-correlation coefficient, obtained after the interpolation of the impact response baseline using the Radial Basis Function (RBF) method. Numerous experimental tests are performed on a simple carbon fibre reinforced polymer (CFRP) plate fitted with three piezo-sensors at three different drop heights to validate the training process. The results showed high accuracy in both the reconstruction and the impact localisation, with an error less than 10 mm.
Summary Nonlinear ultrasonic experiments typically require digital pass‐band filters and advanced signal processing tools to highlight low‐amplitude nonlinear elastic effects such as harmonics, subharmonics, and sidebands, which are used as signatures for the presence of damage. However, current signal processing techniques cannot be used with dual periodic excitation without reducing signal frequency resolution and severely altering measured waveforms. This paper reports the theoretical development of phase symmetry analysis for nonlinear ultrasound with dual periodic transmission. The proposed signal postprocessing technique consists of determining the phase angles of transmitted waveforms that allow filtering modulated nonlinear ultrasonic waves from the measured signal spectrum. Experimental results validated theoretical predictions and revealed that phase symmetry analysis method provides an easy‐to‐implement and reliable procedure to extract sidebands from the measured signal noise. Phase symmetry analysis with dual excitation has, therefore, the potential to enable sensitive and efficient nonlinear ultrasound testing for various materials, damage scenarios, and applications.
Adhesive bonded lap joints are widely used in the aerospace field and non-destructive testing (NDT) techniques are critical in evaluating the quality of adhesion before and during use. Two types of bonded samples have been experimentally investigated in order to verify the reliability of non-linear elastic wave spectroscopy (NEWS) based on the use of ultrasound. Piezoelectric sensors have been attached to the samples and used as generators and receivers. Both the samples have shown non-linearities in their dynamic behaviour. Non-linear metrics have been applied to their structural responses over an assigned range of excitation frequencies based on higher order harmonic analysis in order to evaluate the degree of non-linearity of the samples. Possible interpretations of the experimental behaviour are provided in the paper based also on tomographic testing of the adhesive layer that showed the presence of microbubbles in the bond due to manufacturing process.
This paper presents a novel approach to improve the structural properties and damage tolerance of fibre-reinforced polymer composite joints via tufting using shape memory alloy (SMA) filaments. T-shaped joints made of carbon-epoxy composite material were reinforced with thin SMA (Ni-Ti nitinol) tufts. Experimental testing and finite element (FE) modelling reveal that the ultimate load, ultimate displacement and absorbed energy capacity of the T-joint increase with the areal density of SMA tufts. Improvements of over 110% in strength and 450% in absorbed energy capacity were achieved by SMA tufting. Under certain conditions, the shape memory effect of the tufts can be activated via electrical resistance heating to partially or completely close cracks in the T-joint caused by over-loading. The novel use of SMA tufts both to improve the resistance against cracking and to close cracks when they occur is a unique approach to improving the damage tolerance of composite structural joints.
Structural health monitoring (SHM) systems have been extensively studied in recent decades to determine the health statuses of mechanical, naval and aerospace engineering components. Currently, one of the most promising non-destructive tests for the detection of structural damage is the electromechanical impedance (EMI) technique, which uses low-cost, surface-bonded piezoelectric transducers operating both as sensors and actuators. Although many studies have reported the effectiveness of the EMI method, numerous practical issues, such as signal noise effects caused by environmental conditions, may severely affect the detection and quantification of damage. Therefore, this paper presents a comparative analysis of three signal processing techniques used in the context of the EMI method, which have the potential to enhance the detection of structural damage under environmental signal noise effects. These signal analysis methods include (i) damage indices, such as the correlation coefficient deviation metric, computed directly on impedance signatures; (ii) the wavelet transform computed on transducer response signals in the time domain; and (iii) a novel approach of damage feature extraction in the EMI method based on the Hinkley criterion. Experimental tests were carried out to analyse the three signal processing techniques on a damaged aerospace composite carbon fibre structure subjected to various signal noise levels. The experimental results revealed that conventional damage indices and wavelet transform were significantly affected by noise, whereas the proposed approach based on the Hinkley criterion was more effective for detecting damage in noisy environments.
This research work presents an in-situ imaging method for the localization of the impact point in complex anisotropic structures with diffuse field conditions, using only one passive transducer. The proposed technique is based on the time reversal approach applied to a number of waveforms stored into a database containing the experimental Green's function of the medium. The present method exploits the benefits of multiple scattering, mode conversion and boundaries reflections to achieve the focusing of the source with high resolution. The optimal re-focusing of the back propagated wave field at the impact point is accomplished through a "virtual" imaging process, which does not require any iterative algorithms and a priori knowledge of the mechanical properties of the structure. The robustness of the time reversal method is experimentally demonstrated on a stiffened composite panel and the source position can be retrieved with a high level of accuracy (error less than 3%). The simple configuration, minimal processing requirements and computational time (less than 1 sec) make this method a valid alternative to the conventional imaging structural health monitoring systems for the acoustic emission source localization.
Nonlinear ultrasonic techniques rely on the measurement of nonlinear elastic effects caused by the interaction of ultrasonic waves with the material damage, and have shown high sensitivity to detect microcracks and defects in the early stages. This paper presents a nonlinear ultrasonic technique, here named nonlinear elastic multi-path reciprocal method, for the identification and localisation of micro-damage in composite laminates. In the proposed methodology, a sparse array of surface bonded ultrasonic transducers is used to measure the second harmonic elastic response associated with the material flaw. A reciprocal relationship of nonlinear elastic parameters evaluated from multiple transmitter-receiver pairs is then applied to locate the micro-damage. Experimental results on a damaged composite panel revealed that an accurate damage localisation was obtained using the normalised second order nonlinear parameter with a high signal-to-noise-ratio (~11.2 dB), whilst the use of bicoherence coefficient provided high localisation accuracy with a lower signal-to-noise-ratio (~1.8 dB). The maximum error between the calculated and the real damage location was nearly 13 mm. Unlike traditional linear ultrasonic techniques, the proposed nonlinear elastic multi-path reciprocal method allows detecting material damage on composite materials without a priori knowledge of the ultrasonic wave velocity nor a baseline with the undamaged component.
This paper presents a study on the effectiveness of a convolutional neural network (CNN) in classifying infrared images for security scanning. Infrared thermography was explored as a non-invasive security scanner for stand-off and walk-through concealed object detection. Heat generated by human subjects radiates off the clothing surface, allowing detection by an infrared camera. However, infrared lacks in penetration capability compared to longer electromagnetic waves, leading to less obvious visuals on the clothing surface. ResNet-50 was used as the CNN model to automate the classification process of thermal images. The ImageNet database was used to pre-train the model, which was further fine-tuned using infrared images obtained from experiments. Four image pre-processing approaches were explored, i.e., raw infrared image, subject cropped region-of-interest (ROI) image, K-means, and Fuzzy-c clustered images. All these approaches were evaluated using the receiver operating characteristic curve on an internal holdout set, with an area-under-the-curve of 0.8923, 0.9256, 0.9485, and 0.9669 for the raw image, ROI cropped, K-means, and Fuzzy-c models, respectively. The CNN models trained using various image pre-processing approaches suggest that the prediction performance can be improved by the removal of non-decision relevant information and the visual highlighting of features.
This work proposes a novel technique for the localization of low-velocity impacts in composites without a-priori knowledge of the mechanical properties nor the speed of propagating waves, thus overcoming current limitations of existing impact localization methods. The proposed algorithm is based on the estimation of the power of acoustic emissions generated by impacts on a composite plate instrumented with embedded piezo-transducers. The signal power values calculated at sparse sensor locations are interpolated over the sample by using radial basis function networks. The impact coordinates on the specimen surface are estimated by a center-of-gravity method based on the interpolated power values. Experimental tests were performed by using both an instrumented impact hammer and a drop tower. The results obtained showed the validity of the presented approach, which was able to identify the impact locations with high level of accuracy.
This paper reports the development of a contactless non-destructive evaluation technique using an air-coupled haptic ultrasonic phased array to induce thermosonic frictional heating in damaged carbon fibre reinforced polymer composites. Haptic ultrasonic systems consist of controllable, narrowband, and high-power piezoelectric transducer arrays that are capable of electronically steering and shaping the ultrasonic beam on the surface of test samples. Localised thermal images of the damaged area were observed using an infrared camera. It was found that the intensity of the thermosonic heating reduced with increased distances between the ultrasonic excitation location and the damage. This approach allowed the ultrasonic focal point to be moved across the sample to identify the areas of damage, without moving either the array or the infrared camera, thus significantly decreasing the time needed for inspection.
This paper is aimed at developing a theoretical model able to predict the generation of nonlinear elastic effects associated to the interaction of ultrasonic waves with the steady-state nonlinear response of local defect resonance (LDR). The LDR effect is used in nonlinear elastic wave spectroscopy to enhance the excitation of the material damage at its local resonance, thus to dramatically increase the vibrational amplitude of material nonlinear phenomena. The main result of this work is to prove both analytically and experimentally the generation of novel nonlinear elastic wave effects, here named as nonlinear damage resonance intermodulation, which correspond to a nonlinear intermodulation between the driving frequency and the LDR one. Beside this intermodulation effect, other nonlinear elastic wave phenomena such as higher harmonics of the input frequency and superharmonics of LDR frequency were found. The analytical model relies on solving the nonlinear equation of motion governing bending displacement under the assumption of both quadratic and cubic nonlinear defect approximation. Experimental tests on a damaged composite laminate confirmed and validated these predictions and showed that using continuous periodic excitation, the nonlinear structural phenomena associated to LDR could also be featured at locations different from the damage resonance. These findings will provide new opportunities for material damage detection using nonlinear ultrasounds.
Embedded piezoelectric lead zirconate titanate (PZT) transducers in carbon fibre reinforced plastic (CFRP) composites are typically electrically insulated by interlaying materials such as polyimide Kapton films between the PZT and the laminate ply. However, the presence of polymeric films may cause debonding at the layer interface, thus reducing the structural performance. This paper proposes an alternative insulation technique in which PZTs are covered by a thin patch of woven E-glass fibre fabric for enhanced adhesion with the surrounding epoxy matrix. An analysis of variance on experimental test results showed that the compressive, flexural and interlaminar shear strengths of plain CFRP specimens were equal to the means of the smart CFRP composite (0.41
Pulsed thermography is a contactless and rapid non-destructive evaluation (NDE) technique that is widely used for the inspection of fibre reinforced plastic composites. However, pulsed thermography uses expensive and specialist equipment such high-energy flash lamps to generate heat into the sample, so that alternative thermal stimulation sources are needed. Long pulse thermography was recently developed as a cost-effective solution to enhance the defect detectability in composites by generating step-pulse heat into the test sample with inexpensive quartz halogen lamps and measuring the thermal response during the material cooling down. This paper provides a quantitative comparison of long pulse thermography with traditional pulsed thermography and step heating thermography in carbon fibre and glass fibre composites with flat-bottomed holes located at various depths. The three thermographic methods are processed with advanced thermal image algorithms such as absolute thermal contrast, thermographic signal reconstruction, phase Fourier analysis and principal component analysis in order to reduce thermal image artefacts. Experimental tests have shown that principal component analysis applied to long pulse thermography provides accurate imaging results over traditional pulsed thermography and step heating thermography. Hence, this inspection technique can be considered as an efficient and cost-effective thermographic method for low thermal conductivity and low thermal response rate materials.
In recent years, the growing interest of aerospace companies in wireless structural health monitoring systems has led to the research of new energy efficient sources and power harvesting solutions. Among available environmental power sources, temperature gradients originated at different locations of the aircraft can be used by thermo-electric generators (TEGs) to create electrical voltage. TEGs are lightweight, provide high-energy conversion and do not contain movable parts. Thermal diffusion systems, commonly known as heatsinks, can be combined with TEGs to enhance their performance by increasing heat dissipation from a high temperature surface to the ambient air. This paper focused on the enhancement of TEG performance by developing an air-cooled heatsink for low-power wireless structural health monitoring applications. The design, manufacturing and testing of the proposed thermal diffusion system was investigated by evaluating the increase of the temperature gradient between the opposite surfaces of a commercial TEG element. The thermal performance of the heatsink was assessed with numerical finite element thermal simulations and validated with experimental tests. Experimental results revealed that the proposed thermal diffusion system provided higher temperature differences and, therefore, higher output power in comparison with traditional cylindrical pin-fin heatsinks. A hybrid heat diffusion system composed by copper heatsinks and highly oriented pyrolytic graphite layers was also here proposed in order to allow TEG reaching wireless SHM operative power requirements of tens of mW and, at the same time, adapt the assembly to the complexity of aerospace SHM arrangements. Experimental results revealed that the proposed heatsink-TEG arrangement was able to generate an output power over 25 mW.
Custom made electrostatic transducers were used for ultrasonic investigations of damaged CFRP. These investigations resulted in identification of non-linear ultrasonic responses due to the presence of damage. The broadband nature of electrostatic transducers is essential for this work to scan a wide range of frequencies to identify non-linear responses. These non-linear response frequencies were used with an electrostatic transducer to induce thermosonic heating at the damage which was measured with an IR camera. The use of non-linear response frequencies reduces the power required to produce thermosonic heating. Travelling guided waves (Lamb waves) allow excitation of the damage at a distance from the excitation source allowing large samples to be studied. This provides a completely non-contact measurement for NDE which shows promise for future composite inspection systems.
Active infrared thermography is a fast and accurate non-destructive evaluation technique that is of particular relevance to the aerospace industry for the inspection of aircraft and helicopters' primary and secondary structures, aero-engine parts, spacecraft components and its subsystems. This review provides an exhaustive summary of most recent active thermographic methods used for aerospace applications according to their physical principle and thermal excitation sources. Besides traditional optically stimulated thermography, which uses external optical radiation such as flashes, heaters and laser systems, novel hybrid thermographic techniques are also investigated. These include ultrasonic stimulated thermography, which uses ultrasonic waves and the local damage resonance effect to enhance the reliability and sensitivity to micro-cracks, eddy current stimulated thermography, which uses cost-effective eddy current excitation to generate induction heating, and microwave thermography, which uses electromagnetic radiation at the microwave frequency bands to provide rapid detection of cracks and delamination. All these techniques are here analysed and numerous examples are provided for different damage scenarios and aerospace components in order to identify the strength and limitations of each thermographic technique. Moreover, alternative strategies to current external thermal excitation sources, here named as material-based thermography methods, are examined in this paper. These novel thermographic techniques rely on thermoresistive internal heating and offer a fast, low power, accurate and reliable assessment of damage in aerospace composites.
SMArt Thermography exploits the electrothermal properties of multifunctional smart structures, which are created by embedding shape memory alloy (SMA) wires in traditional carbon fibre reinforced composite laminates (known as SMArt composites), in order to detect the structural flaws using an embedded source. Such a system enables a built-in, fast, cost-effective and in-depth assessment of the structural damage as it overcomes the limitations of standard thermography techniques. However, a theoretical background of the thermal wave propagation behaviour, especially in the presence of internal structural defects, is needed to better interpret the observations/data acquired during the experiments and to optimise those critical parameters such as the mechanical and thermal properties of the composite laminate, the depth of the SMA wires and the intensity of the excitation energy. This information is essential to enhance the sensitivity of the system, thus to evaluate the integrity of the medium with different types of damage. For this purpose, this paper aims at developing an analytical model for SMArt composites, which is able to predict the temperature contrast on the surface of the laminate in the presence of in-plane internal damage (delamination-like) using pulsed thermography. Such a model, based on the Green's function formalism for one-dimensional heat equation, takes into account the thermal lateral diffusion around the defect and it can be used to compute the defect depth within the laminate. The results showed good agreement between the analytical model and the measured thermal waves using an infrared (IR) camera. Particularly, the contrast temperature curves were found to change significantly depending on the defect opening.
The purpose of this paper is to analyse the possibility to manufacture and verify the self-sensing capability of composite materials plates with an embedded network of NiTi shape memory alloys (SMA) used as transducers for structural integrity. Firstly, the thermo-electrical material properties of SMAs were investigated to assess their capability to sense strain within. The results showed that the electrical resistance variation provided by the shape memory alloys network enables a built in and fast assessment of the stress distribution over the entire structure. Then, by transmitting a low amperage current, results in an electric and thermal flow through the entire SMA network. Using an IR Camera it is possible to capture the emitted thermal waves from the sample and create an image of the thermal field within the material. Consequently, analysing the behaviour of the heating curves on different points of the sample, it is possible to identify potential variation in the apparent temperature of the composite, leading to the identification of damages within the composite structure.
In this research work, an imaging method of the nonlinear signature in a reverberant complex anisotropic structure with hysteretic behaviour is reported. The proposed technique relies on a combination of phase symmetry analysis with frequency modulation excitation and nonlinear time reversal, and it is applied to a number of waveforms containing the nonlinear impulse responses of the medium. Phase symmetry analysis was used to characterize the third order nonlinearity of the structure due to delamination and cracks, by exploiting its invariant properties with the phase angle of the input waveforms. Then, a "virtual" reciprocal time reversal imaging process, using only two sensors in pitch-catch mode, was used to "illuminate" the damage. Taking advantage of multiple linear scattering, this methodology allows achieving the optimal focalization at the nonlinear source by a compensation of the distortion effects in a dissipative medium. The robustness of this technique was experimentally demonstrated on a damaged sandwich panel undergone to low-velocity impact loading. The nonlinear source was retrieved with a high level of accuracy with little computational time (less than 1 sec). Its minimal processing requirements make this method a valid alternative to the traditional nonlinear elastic wave spectroscopy techniques for materials showing either classical or non-classical nonlinear behaviour.
Second harmonic generation is one of the most sensitive and reliable nonlinear elastic signatures for micro-damage assessment. However, its detection requires powerful amplification systems generating fictitious harmonics that are difficult to discern from pure nonlinear elastic effects. Current state-of-the-art nonlinear ultrasonic methods still involve impractical solutions such as cumbersome signal calibration processes and substantial modifications of the test component in order to create material-based tunable harmonic filters. Here we propose and demonstrate a valid and sensible alternative strategy involving the development of an ultrasonic phononic crystal waveguide transducer that exhibits both single and multiple frequency stop-bands filtering out fictitious second harmonic frequencies. Remarkably, such a sensing device can be easily fabricated and integrated on the surface of the test structure without altering its mechanical and geometrical properties. The design of the phononic crystal structure is supported by a perturbative theoretical model predicting the frequency band-gaps of periodic plates with sinusoidal corrugation. We find our theoretical findings in excellent agreement with experimental testing revealing that the proposed phononic crystal waveguide transducer successfully attenuates second harmonics caused by the ultrasonic equipment, thus demonstrating its wide range of potential applications for acousto/ultrasonic material damage inspection. © 2017 The Author(s).
The presence of space debris and micrometeoroids particles in the space environment are a serious threat for Earth orbiting spacecraft. Hypervelocity impacts (HVIs) at the typical velocities of ∼7 to 10 km/s can severely damage or destroy satellites, so that debris detection systems are necessary. In the present research work, a “smart” composite detector of orbital debris and micrometeoroids particles is proposed and developed as proof-of-concept for future space missions. The presented detector consists of two thin parallel carbon fibre reinforced plastic (CFRP) composite plates, each instrumented with three piezoelectric transducers embedded into the laminate. The developed algorithm can estimate both directions and velocities of orbital debris and micrometeoroids particles by the knowledge of: (i) impact locations on the two plates, (ii) the time differences of arrival of acoustic emissions generated by impacts and (iii) the wave velocity profile in the composite plates. The localisation of the impact events is achieved by time reversal method, while the time of arrivals are calculated using Akaike Information Criterion method. A set of experimental tests were performed to validate the proof-of-concept using a small drop tower. Impact results showed the high accuracy of the proposed algorithm in the estimation of impact locations, directions and velocities of impact objects.
Literature on solar sailing has thus far mostly considered solar radiation pressure (SRP) as the only contribution to sail force. However, considering a sail in a planetary mission scenario, a new contribution can be added. Since the planet itself emits radiation, this generates a radial planetary radiation pressure (PRP) that is also exerted on the sail. Hence, this work studies the combined effects of both SRP and PRP on a sail for two case studies, i.e. Earth and Venus. In proximity of the Earth, the effect of PRP can be significant under specific conditions. Around Venus, instead, PRP is by far the dominating contribution. These combined effects have been studied for single- and double-sided reflective coating and including eclipse. Results show potential increase in the net acceleration and a change in the optimal attitude to maximise the acceleration in a given direction. Moreover, an increasing semi-major axis manoeuvre is shown with and without PRP, to quantify the difference on a real-case scenario.
Space debris particles with dimensions smaller than tens of millimetres are not trackable with existing monitoring systems and have sufficient energy to harm orbiting Earth satellites during impact events. This paper presents a proof-of-concept for an in-situ smart carbon fibre reinforced plastic (CFRP) composite orbital debris detector that is capable of localising space debris impacts on Earth satellites and measuring the direction and velocity of debris particles. This spacecraft detection system can be used to warn satellites about the impact occurrence and to enhance current Space Surveillance Networks by providing a catalogue of debris objects. The proposed orbital debris detector consists of two thin parallel CFRP composite plates, each instrumented with three piezoelectric transducers embedded into the laminate. The localisation method is based on the measurement of acoustic emissions generated by debris impacts on the CFRP plates, which are processed with the time reversal algorithm. The calculation of the direction of debris particles and their speed are accomplished by determining the arrival time of acquired signals and the speed of waves propagating within each CFRP plate. Experimental results showed accurate estimation of the impact location, direction and velocity, thus demonstrating the potential use of the proposed orbital debris detector in future Earth satellite systems.
Guided waves have immense potential for structural health monitoring applications in numerous industries including aerospace. It is necessary to evaluate guided wave dispersion characteristics, i.e., group velocity and phase velocity profiles, for using them effectively. For complex structures, the profiles can have highly irregular shapes. In this work, a direct method for calculating the group velocity profiles for complex, composite, and periodic structures using a wave and finite element scheme is presented. The group velocity calculation technique is easy to implement, highly computationally efficient, and works with the standard finite element formulation. The major contribution is summarised in the form of a comprehensive algorithm for calculating the group velocity profiles. The method is compared with the existing analytical and numerical methods for calculation of dispersion curves. Finally, an experimental study in a multilayered composite plate is conducted and the results are found to be in good agreement. The technique is suitable to be used in all guided wave application areas such as material characterisation, non-destructive testing, and structural health monitoring.
Long pulse thermography (LPT) is an emerging non-destructive technique that has been used for rapid, cost-effective and accurate damage assessment of composite materials. This paper proposes three analytical models for the in-depth evaluation of defects in a carbon fibre-reinforced plastic (CFRP) specimen by long pulse thermography. The first two models rely on the estimate of the peak temperature-contrast and the peak temperature-contrast slope from the thermal data recorded by an infrared (IR) camera. Both the analytical and experimental results showed that the arriving time of the peak temperature-contrast depends on both the depth and the diameter of defects, whilst the contrast time slope is mainly proportional to the square of the damage depth. The third model here proposed consists of a two-dimensional (2D) axisymmetric heat conduction model based on virtual heat sources. Compared to previously reported analytical models, the proposed 2D one showed higher accuracy on the depth estimation.
Ultrasonic methods for damage imaging typically use baseline signals from the undamaged part, which are often affected by real operational conditions and may not always be available. This paper proposes a baseline-free damage imaging algorithm based on a combination of virtual time reversal (VTR) and the Reconstruction Algorithm for Probabilistic Inspection of Damage (RAPID) tomographic technique. VTR is an alternative to traditional time reversal as it reduces the burden of physically back-propagating re-mitted signals by applying signal operations between the transmitted and received waveforms. Spatial VTR-based damage indices were here proposed to enhance defect detection as they do not require the time domain reconstruction of reemitted signals. Experimental results on damaged aluminium and composite specimens showed that the proposed VTR-based damage indices coupled to the RAPID imaging algorithm were able to localise material flaws with a maximum localisation error of similar to 6 mm and similar to 2 mm for aluminium and composite samples, respectively.
This paper proposes a novel nonlinear ultrasonically stimulated thermography technique for a quick and reliable assessment of material damage in carbon fibre reinforced plastic (CFRP) composite materials. The proposed non-destructive evaluation (NDE) method requires narrow sweep ultrasonic excitation using contact piezoelectric transducers in order to identify dual excitation frequencies associated with the damage resonance. High-amplitude signals and higher harmonic generation are necessary conditions for an accurate identification of these two input frequencies. Dual periodic excitation using high-and low-frequency input signals was then performed in order to generate frictional heating at the crack location that was measured by an infrared (IR) camera. To validate this concept, an impact damaged CFRP composite panel was tested and the experimental results were compared with traditional flash thermography. A laser vibrometer was used to investigate the response of the material with dual frequency excitation. The proposed nonlinear ultrasonically modulated thermography successfully detected barely visible impact damage in CFRP composites. Hence, it can be considered as an alternative to traditional flash thermography and thermosonics by allowing repeatable detection of damage in composites.
Recent nonlinear elastic wave spectroscopy experiments have shown that the nonlinear ultrasonic response of damaged composite materials can be enhanced by higher vibrations at the local damage resonance. In this paper, the mathematical formulation for the generation of nonlinear wave effects associated with continuous periodic excitation and the concept of local defect resonance is provided. Under the assumption of both quadratic and cubic approximation, the existence of higher harmonics of the excitation frequency, superharmonics of the damage resonance frequency and nonlinear wave effects, here named as nonlinear damage resonance intermodulation, which correspond to the nonlinear intermodulation between the driving and the damage resonance frequencies, is proved. All these nonlinear elastic effects are caused by the interaction of propagating ultrasonic waves with the local damage resonance and can be measured at locations different from the material defect one. The proposed analytical model is confirmed and validated through experimental transducer-based measurements of the steady-state nonlinear resonance response on a damaged composite sample. These results will provide opportunities for early detection and imaging of material flaws.
This paper presents a nonlinear elastic material model able to simulate the nonlinear effects generated by the interaction of acoustic/ultrasonic waves with damage precursors and micro-cracks in a variety of materials. Such a constitutive model is implemented in an in-house finite element code and exhibits a multiscale nature where the macroscopic behavior of damaged structures can be represented through a contribution of a number of mesoscopic elements, which are composed by a statistical collection of microscopic units. By means of the semi-analytical Landau formulation and Preisach-Mayergoyz space representation, this multiscale model allows the description of the structural response under continuous harmonic excitation of micro-damaged materials showing both anharmonic and dissipative hysteretic effects. In this manner, nonlinear effects observed experimentally, such as the generation of both even and odd harmonics, can be reproduced. In addition, by using Kelvin eigentensors and eigenelastic constants, the wave propagation problem in both isotropic and orthotropic solids was extended to the three-dimensional Cartesian space. The developed model has been verified for a number of different geometrical and material configurations. Particularly, the influence of a small region with classical and non-classical elasticity and the variations of the input amplitudes on the harmonics generation were analyzed.
Bistable energy harvesting has become a major field of research due to some unique features for converting mechanical energy into electrical power. When properly loaded, bistable structures snap-through from one stable configuration to another, causing large strains and consequently power generation. Moreover, bistable structures can harvest energy across a broad-frequency bandwidth due to their nonlinear characteristics. Despite the fact that snap-through may be triggered regardless of the form or frequency of exciting vibration, the external force must reach a specific snap-through activation threshold value to trigger the transition from one stable state to another. This aspect is a limiting factor for realistic vibration energy harvesting application with bistable devices. This paper presents a novel power harvesting concept for bistable composites based on a 'lever effect' aimed at minimising the activation force to cause the snap through by choosing properly the bistable structures' constraints. The concept was demonstrated with the help of numerical simulation and experimental testing. The results showed that the actuation force is one order of magnitude smaller (3%-6%) than the activation force of conventionally constrained bistable devices. In addition, it was shown that the output voltage was higher than the conventional configuration, leading to a significant increase in power generation. This novel concept could lead to a new generation of more efficient bistable energy harvesters for realistic vibration environments. © 2016 IOP Publishing Ltd.
Shape memory alloy (SMA) tufted composites have shown a significant improvement of the mechanical strength, fracture toughness, and delamination resistance of structural joints. This paper investigated the self-sensing functionality of SMA tufted carbon/epoxy composite T-joints to enable in-situ strain monitoring for the detection of low-velocity impacts. Indeed, large deformations in the tufted composite due to impacts caused abrupt changes in electrical resistance of SMA filaments, which were used to trigger the detection system. An Arduino Mega controller was programmed to simultaneously extract and process real-time electrical resistance recordings from SMA tufts during impact tests conducted at 5 J and 10 J. Experimental results showed that the proposed SMA-enabled detection system can capture accurately the time of the impact and localise the delamination onset, thus demonstrating the truly multifunctional capabilities of proposed SMA tufted composites.
Structural health monitoring techniques are widely used in industry applications to guarantee the integrity of several types of components. This article proposes a baseline-free damage imaging algorithm based on Spatial Frequency Domain Virtual Time Reversal (SFD-VTR). Virtual time reversal (VTR) is an alternative to traditional time reversal as it reduces the burden of physically back-propagating re-emitted signals by applying signal operations between the transmitted and received waveforms. However, VTR rely on the reconstruction of the emitted signal in the time domain, which involves significant data manipulation causing sampling errors of reconstructed signals. Novel SFD-VTR damage indices were here proposed to enhance defect detection as they do not require the time domain reconstruction of re-emitted signals. Experimental results showed that the proposed algorithm was able to localise material flaws and can be use as Human Machine Interface (HMI).
A commercially-available air coupled piezoelectric array was used to induce thermosonic heating in damaged CFRP. Themosonic heating of the damage has been observed with an IR camera. The intensity of the thermosonic heating decreased with the increased distance of the ultrasonic excitation from the damage, as would be expected with energy dissipation into the CFRP. The use of an array allowed scanning of the focal point across a sample to locate and image areas of damage, without moving either the array or the camera. This scanning capability could increase the speed at which composites can be inspected, reducing the current laborious contact transducer methods.
This research work presents a hierarchical method able to reconstruct the time history of the impact force on a composite wing stringer-skin panel by using the structural responses measured by a set of surface bonded ultrasonic transducers. Time reversal method was used to identify the impact location by the knowledge of structural responses recorded from a set of excitation points arbitrarily chosen on the plane of the structure. Radial basis function interpolation approach was then used to calculate the transfer function at the impact point and reconstruct the impact force history. Experimental results showed the high level of accuracy of the proposed impact force reconstruction method for a number of low-velocity impact sources and energies.
Thermosonics, also known as ultrasonic stimulated thermography, is a rapid non-destructive evaluation technique that uses an infrared camera to visualise material defects by detecting the frictional heating at crack surfaces when a part under inspection is vibrated. These vibrations are usually produced by an ultrasonic horn being pressed against the surface of the test sample, which result in uncontrolled generations of frequency components and excitation amplitude. This makes thermosonics highly non-reproducible and unreliable. This paper presents a novel thermographic method, here named as nonlinear ultrasound stimulated thermography, for the detection and imaging of real material defects such as impact damage on a complex composite stiffener panel. This technique combines nonlinear ultrasonic techniques with thermography. A nonlinear ultrasonic approach was used as signature for a reliable frequency-selective excitation of material defects, while an infrared camera was employed to reveal the damage location and severity. A nonlinear narrow sweep excitation method was employed to efficiently excite the local resonance frequencies of the damaged region in order to give rise to the highest nonlinear harmonic response in the material leading to a high heat generation at the crack surface. The experimental tests were carried out with a laser vibrometer in order to better understand the interaction of elastic waves with nonlinear scattering. An ad-hoc nonlinear thermal-structural finite element and crack model was developed to study the heat generation caused by the movement of the crack surfaces when elastic waves with a particular frequency impinges on the crack interphase with good agreement with the experimental results. The proposed new method allows to detect single and multiple barely visible impact damage in a quick, reliable and reproducible manner and overcomes the main limitations of classical thermosonics.
Impact damage is a major concern for the new generation of aircraft composites structures due to the low impact resistance of these materials. Development of an impact force location and force identification system would make maintenance procedures more efficient by allowing inspections to be scheduled only when necessary, and knowing the impact location would allow for a localized search, saving time and cost. Moreover, measuring the impact force would allow to predict damage initiation since delamination area is a function of the impact force and energy. State-of-the-art impact force reconstruction algorithms use reference data from numerical simulations and require a detailed knowledge of mechanical properties, which are difficult to obtain under real operational conditions. This paper presents an impact force reconstruction algorithm that relies on experimental structural responses measured by a sparse array of surface bonded receiving ultrasonic transducers. This algorithm uses time reversal method to retrieve the location of impact source and interpolation techniques based on hierarchical radial basis functions to calculate the transfer function at the impact point and reconstruct the impact force history. A number of impact testing were performed on a composite plate-like structure and a wing stringer-skin panel, and compared with impact force algorithms available in literature. Experimental results revealed that the proposed hierarchical impact force reconstruction method was able to extrapolate the information associated with points far from the impact location and determine the impact force history with high level of accuracy in a real aircraft structure. Since the proposed algorithm requires the calibration of transfer functions from a very sparse training set of data and it does not need numerical models of the component under investigation, it demonstrates its potential as a useful monitoring tool for impact force reconstruction in composite components for full-scale aircraft structural applications leading to timely and cost-efficient inspections.
Long pulse thermography (LPT) has recently been proposed as a new promising and cost-effective active thermographic technique over traditional flash thermography. However, LPT can be affected by uneven heating noise when two or multiple optical heat excitation sources are used. Signal pre-progressing algorithms such as the background subtraction method are typically used to remove uneven heating noise. In this study, a novel signal pre-progressing approach to remove uneven heating noise for LPT is presented, which relies on the Levenberg-Marquardt (LM) algorithm. Unlike the Ordinary Least Squares (OLS) method, LM operates an iterative optimization process to fitting the raw thermal data that allows selecting thermal signals contained only in the sound area. Results showed that the LM algorithm provided higher efficiency than the OLS algorithm to denoise thermal data. Moreover, the LM method combined with principal component analysis further enhanced the capability of LPT to visualize material damage. © 2019 Elsevier B.V.
The increased usage of adhesive bonding as a joining method in modern aerospace components has led to developing reliable ultrasonic health monitoring systems for detection of regions of poor adhesion. Nonlinear acousto-ultrasonic techniques based on higher harmonics and subharmonic frequencies have shown to be sensitive to the detection of micro-voids and disbonds. Nonlinear resonance properties of disbonds generate various nonlinear phenomena such as self-modulation, subharmonics, hysteresis and so on. By exploiting the local natures of these phenomena, this paper demonstrates the use of subharmonics for detection and imaging of flaws in bonded structures. To optimise the experimental testing a two-dimensional analytical model and a three-dimensional finite element analysis simulation were developed for understanding the generation of nonlinear elastic effects with emphasis on subharmonic frequency components. The proposed analytical model qualitatively described the generation of subharmonics but also higher harmonics due to the nonlinear intermodulation of the driving and resonance frequencies associated with the disbonded region. The numerical model was developed by modifying the user defined cohesive element formulation with a bi-linear traction-displacement relationship in order to simulate the interaction of elastic waves with the structural disbond. Whilst the analytical model supported the selection of the driving frequency, the numerical one successfully predicted the generation of subharmonic frequencies originating in the disbonded area. Experimental tests were conducted on a disbonded single lap joint structure using surface-bonded piezoelectric transducers and a laser-Doppler vibrometer, and allowed to validate the analytical and numerical results. It was clearly demonstrated that the nonlinear resonance effects in the form of subharmonics could be used to discriminate reliably regions of poor adhesion in bonded structures. This work can lead to new in situ nonlinear acoustic based health monitoring system for locating and imaging defects in critical aerospace components. © 2017 IOP Publishing Ltd.
Traditional non-destructive evaluation (NDE) and structural health monitoring (SHM) systems are used to analyse that a structure is free of any harmful damage. However, these techniques still lack sensitivity to detect the presence of material micro-flaws in the form of fatigue damage and often require time-consuming procedures and expensive equipment. This research work presents a novel "nonlinear ultrasonic stimulated thermography" (NUST) method able to overcome some of the limitations of traditional linear ultrasonic/thermography NDE-SHM systems and to provide a reliable, rapid and cost effective estimation of fatigue damage in isotropic materials. Such a hybrid imaging approach combines the high sensitivity of nonlinear acoustic/ultrasonic techniques to detect micro-damage, with local defect frequency selection and infrared imaging. When exciting structures with an optimised frequency, nonlinear elastic waves are observed and higher frictional work at the fatigue damaged area is generated due to clapping and rubbing of the crack faces. This results in heat at cracked location that can be measured using an infrared camera. A Laser Vibrometer (LV) was used to evaluate the extent that individual frequency components contribute to the heating of the damage region by quantifying the out-of-plane velocity associated with the fundamental and second order harmonic responses. It was experimentally demonstrated the relationship between a nonlinear ultrasound parameter ( βratio) of the material nonlinear response to the actual temperature rises near the crack. These results demonstrated that heat generation at damaged regions could be amplified by exciting at frequencies that provide nonlinear responses, thus improving the imaging of material damage and the reliability of NUST in a quick and reproducible manner.
Two methods have been evaluated in order to locate barely visible impact damage (BVID) in a composite stiffener panel. A nonlinear thermosonics technique and a nonlinear laser vibrometer technique were evaluated. Damaged regions were excited using a piezo shaker in both methods. Evaluation of the damaged regions was done by first determining the second and third order nonlinear harmonic response of the damaged regions. This was then used to determine the excitation frequency. By evaluating the presence of nonlinear responses in the output signal it is possible to excite the damaged structure at frequencies that give high heat generation and high displacements at the damaged regions. The results showed that both methods can be used to locate damaged regions, although it was shown that the stiffener impedes the propagation of the exciting wave and that these tests should be carried out in-between stiffeners in order to maximise the excitation
Over the years, traditional active infrared thermography has played a pivotal role in ensuring that a component is free of any damage. However, whilst optical thermography is still not sufficiently sensitive to the presence of material micro-flaws, current vibro-thermography requires inspection solutions that are not always feasible, such as the use of coupling materials between the sensing probe and the monitored structure. This paper presents a valid alternative to current thermographic systems by developing and experimentally validating nonlinear air-coupled thermosonics for a contactless, rapid and accurate detection of fatigue micro-cracks in an aero-engine turbine blade. The proposed thermographic method combines the high sensitivity to micro-damage of nonlinear ultrasonic techniques with non-contact air-coupled ultrasonic transducers and thermographic equipment. Narrowband frequency sweeps were performed to identify local damage resonance frequencies in order to generate large vibrational amplitudes at the damage location and compensate for signal losses caused by the high acoustic impedance mismatch between the air and the sample. An infrared camera was then used to acquire the thermal response generated by frictional heat at the crack interfaces. Moreover, an image processing method based on a combination of morphological opening and a Savitzky-Golay smoothing filter was employed to enhance the quality of thermal images affected by anisotropic heating and thermal noise effects. Nonlinear air-coupled thermosonics experiments were validated with laser Doppler vibrometry scan measurements and compared with both flash and pulsed phase thermography. Thermal imaging results showed that the proposed nonlinear air-coupled thermosonics was the only thermographic technique able to detect fatigue micro-cracks, thus demonstrating its potential as an efficient and sensitive inspection tool for micro-damage detection in geometrically complex components.
Morphing structures for lightweight and energy-efficient aircraft mobile surfaces have been investigated for several years. This paper presents a novel lightweight, passive and low-energy morphing surface concept based on the "lever effect" of a bistable composite plate that can be integrated in aircraft moving surfaces. By using appropriate boundary conditions, it is demonstrated that the magnitude of the activation force on the bistable composite can be tailored to match the differential pressure on the aircraft's airfoil. As a consequence, the bistable laminate can be used as a passive morphing surface. Both numerical simulations and experimental testing are used to prove this concept on a NACA 2412 airfoil structure. The results show that, by choosing proper configuration of constraints, lay-up and aspect ratio of the bistable composite, it is possible to tailor and activate the snap-through mechanism in a passive manner. The proposed concept would save significant weight when compared to an active morphing concept.
Accessing to glass fibre reinforcement plastic (GFRP) pipes in the on-line process is often limited to one side. To detect an internal defect of coated GFRP pipe, common non-destructive testing (NDT) methods such as eddy current testing and thermography are not effective because GFRP pipes are not conductive and their coating prevents heat transfer to the inner section of the material. Moreover, the curvature of GFRP pipes introduces lift-off variation, which is the primary challenge for NDT methods using C-scan technique; e.g., ultrasonic. This work proposes a novel microwave NDT application to detect and characterise internal defect; i.e., flat-bottom hole (FBH) in coated GFRP pipes. Initially, responses of four FBH areas obtained by microwave open-ended waveguide probe are analysed using principal component analysis (PCA) to reveal FBH defect and eliminate the pipe curvature influence. Following that, synthetic aperture radar (SAR) tomography images are produced to select the corresponding principal component and verify the location of FBHs. Finally, FBHs are evaluated using PC feature and SAR tomography including time-of-flight feature. The results show that the proposed method can clearly reveal the area of FBHs. Moreover, depths of FBHs are characterised by analysing the time-of-flight feature of background-subtracted responses. © 2019
Thermosonics is a well-established non-destructive evaluation (NDE) technique that uses an infrared camera to visualise material damage by capturing the frictional heating at crack surfaces when the sample under inspection is vibrated. A high power ultrasonic horn is typically used to generate vibrations, which is pressed against the surface of the test component. However, the direct contact between the horn and the surface generates acoustic chaos and high-amplitude vibrations, which can lead to non-reproducible and unreliable measurements and, ultimately, they can harm the structural integrity of components. This paper proposes an alternative to thermosonics, here named as nonlinear wave modulation thermography, for the detection and imaging of material flaws on a damaged carbon fibre composite panel. This material inspection technology combines the concept of nonlinear wave modulation spectroscopy using dual excitation with contact piezoelectric transducers and thermographic equipment. Whilst nonlinear ultrasonic modulation was used to enhance the sensitivity to micro-cracks, an infrared camera was used for defect visualisation. A nonlinear narrow sweep excitation method was employed to experimentally identify the dual excitation frequencies that resulted in high-amplitude damage resonance effects causing frictional heat at crack surfaces. A laser vibrometry system was also used to create a spatial mapping of the amplitude of sidebands. Nonlinear wave modulation thermography has proved to successfully detect barely visible impact damage in composites in a quick and reliable manner, thus overcoming the limitations of traditional optical thermography and thermosonics. © 2018 Elsevier Ltd
The electro-mechanical impedance (EMI) technique is one of the most promising structural health monitoring (SHM) approaches for material damage detection, which is based on impedance measurements of low-cost piezoelectric transducers. However, numerous practical issues such as signal noise effects caused by environmental conditions can alter signal measurements and limit the capabilities of the EMI technique when the characterization of damage is performed using conventional basic indices. Therefore, this paper proposes a new index for structure feature extraction based on the cross-correlation signal processing technique that can be applied in real noisy environment. The proposed index was evaluated in the frequency domain, where the damage detection is performed directly on the electrical impedance measurements of the transducer, as well as on the time domain, which is based on the wavelet transform applied to the transducer response signal. Experimental tests were carried out on a damaged aluminium structure subject to various signal noise levels. Experimental results revealed that the proposed approach for material feature extraction under noisy environments proved to be effective for detecting damage, thus enhancing the reliability and expanding the applicability of the EMI technique.
This research work presents an in-situ imaging method for the localization of the impact point in complex anisotropic structures with diffuse field conditions, using only one passive transducer. The proposed technique is based on the time reversal approach applied to a number of waveforms stored into a database containing the experimental Green's function of the medium. The present method exploits the benefits of multiple scattering, mode conversion and boundaries reflections to achieve the focusing of the source with high resolution. The optimal re-focusing of the back propagated wave field at the impact point is accomplished through a "virtual" imaging process, which does not require any iterative algorithms and a priori knowledge of the mechanical properties of the structure. The robustness of the time reversal method is experimentally demonstrated on a stiffened composite panel and the source position can be retrieved with a high level of accuracy (error less than 3%). The simple configuration, minimal processing requirements and computational time (less than 1 sec) make this method a valid alternative to the conventional imaging structural health monitoring systems for the acoustic emission source localization.
Among several structural health monitoring (SHM) systems, the electro-mechanical impedance (EMI) method is an effective failure detection approach in composite components. In the EMI method, damage detection is achieved by comparing the behaviour of piezoelectric impedance signatures, which are related mathematically to the mechanical impedance of the host structure. Although many studies have proved the effectiveness of the EMI method on composites, many practical issues such signal changes caused by noise and vibrations have limited its use in real-life applications. This work presents an experimental analysis of white noise effects on the impedance monitoring of a carbon fibre reinforced plastic composite plate, by applying the correlation coefficient deviation metric (CCDM) and cross-correlation square deviation (CCSD) index on the response signal of a pitch-catch mode piezoelectric transducer. Experimental results revealed that the CCSD was more sensitive to damage detection under noisy inspections.
Time reversal is a powerful imaging processing technique that focuses waves at their original source using a single receiver transducer when diffusive wave field conditions are met. This has been successfully proved on various engineering components and materials using elastic waves with surface bonded transducers. This paper investigates the performance of time reversal for the localization of impact sources on fiber reinforced plastic composite structures with embedded piezoelectric sensors. A topologic approach, here named as minimum average method, is proposed to enhance the accuracy of time reversal in retrieving the impact location. Experimental tests were carried out to validate the robustness and reliability of time reversal against traditional topological approaches by altering impulsive responses contained in the baseline signals. Impact localization results revealed that time reversal and the new topological approach provided high accuracy in identifying the impact location, particularly in the presence of double impacts and material damage, which were not accounted during the initial training process. Results indicate that time reversal with embedded transducers has potential to be effective in real operating conditions, where alterations of acoustic emission responses in the baseline signals are less predictable.
In aerospace applications, carbon fibre reinforced plastic (CFRP) composite parts are prone to fibre-breakage, matrix cracking and delamination as a result of manufacturing and assembly errors, or in-service impacts. The idea of developing “smart” composites with built-in sensing networks for real-time ultrasonic inspection of aircraft parts has become very popular, to minimise equipment purchase costs and service delays associated with conventional non-destructive testing techniques. Recently, the authors proposed a novel design of “smart” CFRP plates including internal piezoelectric (PZT) transducers without any compromise on the compressive, flexural or interlaminar shear strength of the material. The sensors were embedded between the composite layers and covered with glass fibre patches for electrical insulation from the carbon fibres. A series of nonlinear ultrasonic experiments proved the suitability of this internal sensor configuration for detecting material damage, based on the second harmonic generation method. In this paper impacted CFRP samples with the same glass fibre insulated PZTs (G-specimens) were subject to fatigue testing and the number of cycles to failure (∼675,000) was found to be equal to that of impacted samples without sensors (P-specimens). Ultrasonic experiments on G-specimens showed that the acoustic nonlinearity was increased by almost two orders of magnitude up to 480,000 cycles based on the ratio of second-to-fundamental harmonic amplitude. This confirmed that the unique layout of embedded transducers could not only be used for material damage detection, but it was also capable of monitoring the damage evolution under repeated loading. The capacitance of the PZTs remained constant (∼1.54 nF) during ultrasonic experimentation, verifying their functionality for at least 70% of the fatigue life.
Eddy current pulsed thermography (ECPT) and long pulse thermography (LPT) are two emerging non-destructive evaluation techniques that have been recently used for sub-surface defect detection in both metallic and composite components. This paper provides a comparative analysis of these two methods by focussing on the detection of flat bottom holes (FBHs) in both aluminium and carbon fibre reinforced plastic samples. Principal component analysis was used for the post-processing of thermal data in order to enhance the detection of FBHs with various diameters and depths. Results showed that LPT had a better performance for detecting FBHs in low-thermally conductive materials such as carbon fibre-reinforced thermoplastic composites, whilst ECPT revealed a superior performance for detecting FBHs in materials with higher thermal and electrical conductivity such as aluminium.
Carbon fibre reinforced plastic composites used in spacecraft structures are susceptible to delamination, debonds and fibre cracking that may arise during manufacturing, assembly or in-service operations (e.g. caused by debris impacts in near-Earth orbital spaceflights). Therefore, in situ and real-time health monitoring is necessary to avoid time-consuming and unsafe visual inspections performed either on-ground or during extra vehicular activities. In this article, a recently created ‘smart’ carbon fibre reinforced plastic composite structure with embedded piezoelectric lead zirconate titanate transducers was used to detect multiple areas of artificial delamination and real impact damage of different size using nonlinear ultrasound. The electrical insulation of embedded piezoelectric lead zirconate titanate transducers was achieved by interlacing a dry layer of woven glass fibre fabric between the sensor and the carbon fibre reinforced plastic plies before curing. Damage detection was successfully demonstrated using both second harmonic generation and nonlinear modulation (sidebands) of the measured ultrasonic spectrum. The material nonlinear response at the second harmonic and sidebands frequencies was also measured with a laser Doppler vibrometer to validate the nonlinear ultrasonic tests and provide damage localisation. Experimental results revealed that the proposed configuration of embedded piezoelectric lead zirconate titanate transducers can be utilised for on-board ultrasonic inspection of spacecraft composite parts.
This paper presents a damage detection and localization technique based on nonlinear elastic waves propagation in a damage composite laminate. The proposed method relies on the time of arrival estimation of the second harmonic nonlinear response obtained with second order phase symmetry analysis filtering and burst excitation. The Akaike Information Criterion approach was used to estimate the arrival times measured by six receiver transducers. Then, a combination of Newton's method and unconstrained optimization was employed to solve a system of nonlinear equations in order to obtain the material damage coordinates. To validate this methodology, experimental tests were carried out on a damaged composite plate. The results showed that the technique allows calculating the damage position with high accuracy (maximum error similar to 5 mm).
Reciprocal time reversal (inverse filtering) of acousto-ultrasonic fields is a very efficient technique to focus elastic waves through reverberant isotropic and anisotropic media. Such a methodology relies on the correlation of the experimental Green's function that is acquired by a set of receiver sensors from a limited number of impact sources. However, although heterogeneities and discontinuities within the structural response can be compensated by the inverse filtering process, environmental effects such as temperature variations as well as incoherent noise measurements and the finite number of excitation sources may degrade the quality of time reversal focusing. The scope of this article was to study the factors affecting the impact location imaging using the reciprocal time reversal method in the presence of complex diffuse wave fields. Particularly, a signal-stretch strategy was developed to compensate the temperature changes before remitting the back-propagated wave field at the focus point. Then, in order to investigate the imaging performance and the sensitivity of the proposed methodology, different sets of libraries with reduced input signals were created and tested. Finally, different configurations of the receiver piezoelectric sensors were used to perform the reciprocal time reversal method. To validate this research work, two geometrically complex composite structures, that is, a composite tail rotor blade and a stiffened composite panel, were used. Results showed that both the temperature compensation and the signal processing with the reduced time traced signals and receiver sensors allowed obtaining an accurate identification of the impact events.
In different engineering fields, there is a strong demand for diagnostic methods able to provide detailed information on material defects. Low velocity impact damage can considerably degrade the integrity of structural components and, if not detected, can result in catastrophic failures. This paper presents a nonlinear structural health monitoring imaging method, based on nonlinear elastic wave spectroscopy, for the detection and localisation of nonlinear signatures on a damaged composite structure. The proposed technique relies on the bispectral analysis of ultrasonic waveforms originated by a harmonic excitation and it allows for the evaluation of second order material nonlinearities due to the presence of cracks and delaminations. This nonlinear imaging technique was combined with a radial basis function approach in order to achieve an effective visualisation of the damage over the panel using only a limited number of acquisition points. The robustness of bispectral analysis was experimentally demonstrated on a damaged carbon fibre reinforced plastic (CFRP) composite panel, and the nonlinear source's location was obtained with a high level of accuracy. Unlike other ultrasonic imaging methods for damage detection, this methodology does not require any baseline with the undamaged structure for the evaluation of the defect, nor a priori knowledge of the mechanical properties of the specimen.
This paper presents a nonlinear imaging method based on nonlinear elastic guided waves, for the damage detection and localisation in a composite laminate. The proposed technique relies on the study of the structural nonlinear responses by means of a combination of second order phase symmetry analysis (PSA) with chirp excitation and inverse filtering (IF) method. PSA was used to exploit the invariant properties of the propagating elastic waves with the phase angle of the pulse compressed chirp signals, in order to characterise the second order nonlinear behaviour of the medium. Then, the IF approach was applied to a library of second order nonlinear responses to obtain a two-dimensional image of the damage. The experimental tests carried out on an impact damage composite sample were compared to standard C-scan. The results showed that the present technique allowed achieving the optimal focalisation of the nonlinear source in the spatial and time domain, by taking advantage of multiple scattering and a small number of receiver sensors.
The use of pulsed thermography as a non-destructive evaluation tool for damage monitoring of composite materials has dramatically increased in the past decade. Typically, optical flashes are used as external heating sources, which may cause poor defect definition especially for thicker materials or multiple delaminations. SMArt thermography is a new alternative to standard pulsed thermography as it overcomes the limitations on the use of external thermal sources. Such a novel technology enables a built-in, fast and in-depth assessment of both surface and internal material defects by embedding shape memory alloy wires in traditional carbon fibre reinforced composite laminates. However, a theoretical model of thermal wave propagation for SMArt thermography, especially in the presence of internal structural defects, is needed to better interpret the observations/data measured during the experiments. The objective of this paper was to develop an analytical model for SMArt thermography to predict the depth of flaws/damage within composite materials based on experimental data. This model can also be used to predict the temperature contrast on the surface of the laminate, accounting for defect depth, size and opening, thermal properties of material and defect filler, thickness of the component, and intensity of the excitation energy. The results showed that the analytical model gives good predictions compared to experimental data. This paper is one of the first pioneering work showing the use thermography as a quantitative non-destructive tool where defect size and depth could be assessed with good accuracy.
A new smart polymer nanocomposite layer, based on semiconductor Cu2S nanoparticles embedded into an amorphous polystyrene matrix, was developed for the detection of low-velocity impact damage on composite structures. This material exhibits a combination of optical and electro-magnetic properties, in way that it can be employed to visualize in quick and effective manner barely visible impact damage (BVID). In particular, based on the phenomenon of the photoluminescence, this layer showed specific light emission in the visible range of the electromagnetic spectrum under UV-light excitation at different wavelength. The results of a series of low-velocity impact tests illustrated a visible contrast colour on the damaged area, representing the flaw. In fact, the study of the optical characteristics of this smart material is of particular benefit for fast, cost-effective and in situ damage identification. Hence, once the impact location has been determined, the detailed information of the damage can be further investigated by others non-destructive techniques.
•We present a nonlinear ultrasonic wave tomography method for the image of nonlinear elastic signatures in a damaged aluminium panel undergone to corrosion.•We use a combination of high order statistics and radial basis function interpolation to achieve an effective damage visualisation using only a limited number of receiver sensors.•We detect the nonlinear source location with a high level of accuracy compared to five standard ultrasonic imaging methods. This paper presents a nonlinear elastic wave tomography method, based on ultrasonic guided waves, for the image of nonlinear signatures in the dynamic response of a damaged isotropic structure. The proposed technique relies on a combination of high order statistics and a radial basis function approach. The bicoherence of ultrasonic waveforms originated by a harmonic excitation was used to characterise the second order nonlinear signature contained in the measured signals due to the presence of surface corrosion. Then, a radial basis function interpolation was employed to achieve an effective visualisation of the damage over the panel using only a limited number of receiver sensors. The robustness of the proposed nonlinear imaging method was experimentally demonstrated on a damaged 2024 aluminium panel, and the nonlinear source location was detected with a high level of accuracy, even with few receiving elements. Compared to five standard ultrasonic imaging methods, this nonlinear tomography technique does not require any baseline with the undamaged structure for the evaluation of the corrosion damage, nor a priori knowledge of the mechanical properties of the specimen.
In this paper the nonlinear material response of damaged composite structures under periodic excitation is experimentally and numerically investigated. In particular, the nonlinear wave propagation problem was numerically analysed through a finite element model able to predict the nonlinear interaction of acoustic/ultrasonic waves with damage precursors and micro-cracks. Such a constitutive model is based on the Landau’s semi-analytical approach to account for anharmonic effects of the medium, and is able to provide an understanding of nonlinear elastic phenomena such as the second harmonic generation. Moreover, Kelvin tensorial formulation was used to extend the wave propagation problem in orthotropic materials to the 3D Cartesian space. In this manner, the interaction of the stress waves with the 3D crack could be analysed. This numerical model was then experimentally validated on a composite plate undergone to impact loading. Good agreement between the experimental and numerical second harmonic response was found, showing that this material model can be used as a simple and useful tool for future structural diagnostic applications.
This article proposes an in situ structural health monitoring method able to locate the impact source and to determine the flexural Lamb mode A0 velocity in composite structures with unknown lay-up and cross section. The algorithm is based on the differences of the stress waves measured by six surface-attached acoustic emission piezoelectric (lead zirconate titanate) sensors and is branched off into two steps. In the first step, the magnitude of the squared modulus of continuous wavelet transform, which guarantees high accuracy in the time–frequency analysis of the acoustic waves, was used to identify the time of arrival of the flexural Lamb wave. Then, the coordinates of the impact location and the group speed values are obtained by solving a set of non-linear equations through a combination of local Newton’s iterative method associated with line search and polynomial backtracking techniques. The proposed method, in contrast to the current impact localization algorithms, does not require a priori knowledge of the anisotropy angular-group velocity pattern of the measured waveforms as well as the mechanical properties of the structure. To validate this method, experimental location testing was conducted on two different composite structures: a quasi-isotropic carbon fibre–reinforced plastic laminate and a sandwich panel. The results showed that source location was achieved with satisfactory accuracy (maximum error in estimation of the impact location was approximately 3 mm for quasi-isotropic carbon fibre–reinforced plastic panel and nearly 2 mm for sandwich plate), requiring little computational time (nearly 1 s). In addition, the values of the fundamental flexural Lamb mode A0 obtained from the optimization algorithm were compared with those determined by a numerical spectral finite element method.
This paper presents a new in situ Structural Health Monitoring (SHM) system able to identify the location of acoustic emission (AE) sources due to low-velocity impacts and to determine the group velocity in complex composite structures with unknown lay-up and thickness. The proposed algorithm is based on the differences of stress waves measured by six piezoelectric sensors surface bonded. The magnitude of the Continuous Wavelet Transform (CWT) squared modulus was employed for the identification of the time of arrivals (TOA) of the flexural Lamb mode (A0). Then, the coordinates of the impact location and the flexural wave velocity were obtained by solving a set of non-linear equations through a combination of global Line Search and backtracking techniques associated to a local Newton’s iterative method. To validate this algorithm, experimental tests were conducted on two different composite structures, a quasi-isotropic CFRP and a sandwich panel. The results showed that the impact source location and the group speed were predicted with reasonable accuracy (maximum error in estimation of the impact location was approximately 2% for quasi-isotropic CFRP panel and nearly 1% for sandwich plate), requiring little computational time (less than 2 s).
This paper investigates the development of an in situ impact detection monitoring system able to identify in real-time the acoustic emission location. The proposed algorithm is based on the differences of stress waves measured by surface-bonded piezoelectric transducers. A joint time-frequency analysis based on the magnitude of the continuous wavelet transform was used to determine the time of arrival of the wavepackets. A combination of unconstrained optimization technique associated with a local Newton's iterative method was employed to solve a set of nonlinear equations in order to assess the impact location coordinates and the wave speed. With the proposed approach, the drawbacks of a triangulation method in terms of estimating a priori the group velocity and the need to find the best time-frequency technique for the time-of-arrival determination were overcome. Moreover, this algorithm proved to be very robust since it was able to converge from almost any guess point and required little computational time. A comparison between the theoretical and experimental results carried out with piezoelectric film (PVDF) and acoustic emission transducers showed that the impact source location and the wave velocity were predicted with reasonable accuracy. In particular, the maximum error in estimation of the impact location was less than 2% and about 1% for the flexural wave velocity.
Line scanning thermography (LST) is a fast non-destructive inspection (NDI) method for large-scale components. However, the current reconstruction algorithms for LST require the match between the frame rate and the scanning velocity. Moreover, these algorithms bring in spatial distortions. This paper proposes a non-orthogonal reconstructed space for LST. In such a space, the excitation motion in the line scanning process is described as a function of time delay, the moving velocity is estimated by the derived position map, and the reconstruction is achieved by image registration. The LST data are registered spatially by allowing the temporal misalignment among the pixels within the same reconstructed frame. The effectiveness of the proposed reconstruction algorithm is validated by both numerical simulations and experiments. The reconstruction results of experimental data indicate that the velocity is finely estimated so that the temporal alignment error is controlled within one pixel. Besides, no spatial distortions occur no matter how the frame rate and scanning velocity change. Furthermore, the Fourier phase image of the reconstructed LST reaches the diameter-to-depth ratio of 1.25 when inspecting a planar specimen with flat-bottom holes.
This article presents an in situ structural health monitoring imaging system for the localization of impacts on a composite complex structure such as a tail rotor blade. Unlike conventional plate-like panels, this composite structure presents a strong anisotropy and inhomogeneous elastic nature due to the presence of both glass fibre and carbon fibre, a geometrically complex shape due to the curvature of the blade’s airfoil section and variations in the mechanical behaviour due to local changes in the thickness. The proposed imaging technique is based on the inverse filtering or reciprocal time reversal approach applied to the waveforms originated from a point of the structure of unknown location (impact source) and a number of signals stored in a database containing the experimental Green’s function of the medium. Unlike other ultrasonic impact localization methods, the present technique allows achieving the optimal focalization of the impact point in the spatial and time domain, by taking advantage of multiple linear scattering and a small number of receiver sensors.
This paper presents a nonlinear imaging method for the detection of the nonlinear signature due to impact damage in complex anisotropic solids with diffuse field conditions. The proposed technique, based on a combination of an inverse filtering approach with phase symmetry analysis and frequency modulated excitation signals, is applied to a number of waveforms containing the nonlinear impulse responses of the medium. Phase symmetry analysis was used to characterize the third order nonlinearity of the structure by exploiting its invariant properties with the phase angle of the input waveforms. Then, a “virtual” reciprocal time reversal imaging process, using only one broadcasting transducer and one receiving transducer, was used to insonify the defect taking advantage of multiple linear scattering as mode conversion and boundary reflections. The robustness of this technique was experimentally demonstrated on a damaged sandwich panel, and the nonlinear source, induced by low-velocity impact loading, was retrieved with a high level of accuracy. Its minimal processing requirements make this method a valid alternative to the traditional nonlinear elastic wave spectroscopy techniques for materials showing either classical or non-classical nonlinear behavior.
This article presents an in situ imaging method able to detect in real-time the impact source location in reverberant complex composite structures using only one passive sensor. This technique is based on the time reversal acoustic method applied to a number of waveforms stored in a database containing the impulse response (Green's function) of the structure. The proposed method allows achieving the optimal focalization of the acoustic emission source in the time and spatial domain as it overcomes the drawbacks of other ultrasonic techniques. This is mainly due to the dispersive nature of guided Lamb waves as well as the presence of multiple scattering and mode conversion that can degrade the quality of the focusing, causing poor localization. Conversely, using the benefits of a diffuse wave field, the imaging of the source location can be obtained through a virtual time reversal procedure, which does not require any iterative algorithms and a priori knowledge of the mechanical properties and the anisotropic group speed. The efficiency of this method is experimentally demonstrated on a stiffened composite panel. The results showed that the impact source location can be retrieved with a high level of accuracy in any position of the structure (maximum error was less than 3%).
This paper presents an imaging method for the localization of the impact point in complex anisotropic structures with diffuse field conditions, using only one passive transducer. The proposed technique is based on the reciprocal time reversal approach (inverse filtering) applied to a number of waveforms stored into a database containing the experimental Green's function of the structure. Unlike most acoustic emission monitoring systems, the present method exploits the benefits of multiple scattering, mode conversion, and boundaries reflections to achieve the focusing of the source with high resolution. Compared to a standard time reversal approach, the optimal refocusing of the back propagated wave field at the impact point is accomplished through a "virtual" imaging process. The robustness of the inverse filtering technique is experimentally demonstrated on a dissipative stiffened composite panel and the source position can be retrieved with a high level of accuracy in any position of the structure. Its very simple configuration and minimal processing requirements make this method a valid alternative to the conventional imaging Structural Health Monitoring systems for the acoustic emission source localization.
Nonlinear ultrasound techniques have shown greater sensitivity to microcracks and they can be used to detect structural damages at their early stages. However, there is still a lack of numerical models available in commercial finite element analysis (FEA) tools that are able to simulate the interaction of elastic waves with the materials nonlinear behaviour. In this study, a nonlinear constitutive material model was developed to predict the structural response under continuous harmonic excitation of a fatigued isotropic sample that showed anharmonic effects. Particularly, by means of Landau׳s theory and Kelvin tensorial representation, this model provided an understanding of the elastic nonlinear phenomena such as the second harmonic generation in three-dimensional solid media. The numerical scheme was implemented and evaluated using a commercially available FEA software LS-DYNA, and it showed a good numerical characterisation of the second harmonic amplitude generated by the damaged region known as the nonlinear response area (NRA). Since this process requires only the experimental second-order nonlinear parameter and rough damage size estimation as an input, it does not need any baseline testing with the undamaged structure or any dynamic modelling of the fatigue crack growth. To validate this numerical model, the second-order nonlinear parameter was experimentally evaluated at various points over the fatigue life of an aluminium (AA6082-T6) coupon and the crack propagation was measured using an optical microscope. A good correlation was achieved between the experimental set-up and the nonlinear constitutive model.
The past few decades have seen significant growth in the development and application of multifunctional media for the enhancement of material properties, thermo-mechanical and sensing properties. This research work reports a novel approach in which a multifunctional material, herein referred to as SMArt composite, can be employed as a structural health monitoring system for strain sensing and damage detection (SMArt sensing and SMArt thermography), but also as an embedded ice protection tool for structural applications (referred as SMArt de-icing). Such a material, obtained by embedding shape memory alloy (SMA) wires within traditional carbon reinforced plastic composites, relies on the possibility of using the wires both to increase the mechanical properties of composites panels and to exploit their intrinsic electrothermal properties. The electrical resistance variation and the internal power resistive heating source provided by the SMA network, enable a built in and fast assessment of the strain distribution and in situ damage visualization via thermographic imaging. The efficiency of these techniques was experimentally validated on a number of SMArt composite laminates with single and multiple internal defects at various depths. The results showed that strain sensing and damage detection were achieved with high spatial resolution and accuracy, without the need to use large external heaters or complex signal processing techniques.
Thermoelectric generators (TEGs) have shown great potentials to supply low-power sensor nodes in aerospace applications due to their relatively small size, adequate output power and reliability. TEGs convert waste heat available at aircraft locations into a usable potential difference. However, TEGs’ performance greatly depends on the use of passive cooling systems such as heatsinks to enhance their energy supply. This paper reports the first proof-of-concept use of vapour chambers coupled to traditional circular pin-fin heatsinks to enhance the output power of TEGs. Vapour chambers are compact and small capillary-driven heat spreaders that incorporate a cavity in their volume containing a working fluid to provide a high effective thermal conductivity. Numerical simulations and experimental tests revealed that the use of vapour chambers provided significant increase of the output power, with a maximum produced power of 28.2 W and a relative difference of 6.27 W against conventional energy scavenging configurations. Results demonstrate the high thermal cooling performance of vapour chambers to efficiently support thermal energy harvesting solutions designed for condition and structural health monitoring.
Structural health monitoring (SHM) based on electromechanical impedance (EMI) measurements has been extensively studied in recent years and stands out as an effective damage detection approach. The EMI method commonly uses low-cost piezoelectric transducers and structural diagnosis can be accomplished by analyzing the changes in the impedance measurements from the transducers attached to the host structure. Although many studies have proved the effectiveness of the EMI method, one of the most reported problems is the variations in the impedance caused by external noise, which can alter the impedance measurements and limit the effectiveness of the detection and quantification of damage using conventional basic damage indices. Therefore, this paper proposes a new approach for structure feature extraction in noisy environments based on the chromatic signal processing technique associated with the Hinkley criterion, thus aiming to expand the applicability of the EMI method to real applications. Experimental tests were carried out on aluminum and carbon fiber composite plates subjected to various signal noise levels. The experimental results indicate that the proposed approach is more effective for damage detection compared to the basic indices commonly reported in the literature.
Additional publications
- Watson, R. L., Billson, D. R., Hutchins, D. A., Ciampa, F. Thermosonic inspection of carbon fibre reinforced polymer composites using an airborne haptic ultrasonic phased array. NDT & E International, 2022.
- Wang, Z., Wan, L., Zhu, J., Ciampa, F. Evaluation of defect depth in CFRP composites by long pulse thermography. NDT & E International 129, 102658, 2022.https://doi.org/10.1016/j.ndteint.2022.102658
- Sarris, A., Bhatti, B., Ciampa, F. Thermoelectric energy harvesting using vapour chamber coolers for aerospace applications. Journal of Intelligent Material Systems and Structures 33 (12), 1602-1612. 2022. https://doi.org/10.1177%2F1045389X211063944
- de Castro, B. A., Baptista, F. G., Ardila-Rey, A., Ciampa, F. Baseline-free Damage Imaging Algorithm using Spatial Frequency Domain Virtual Time Reversal. IEEE Transactions on Industrial Informatics, 2021. https://doi.org/10.1109/TII.2021.3124924
- Barles, A., Ceriotti, M., Ciampa, F., Felicetti, L. An Optimal Steering Law for Sailing with Solar and Planetary Radiation Pressure. Aerospace Science and Technology, 118, p.107051, 2021. https://doi.org/10.1016/j.ast.2021.107051
- Ciampa, F., Ladani, R., Knott, G., Buns, T., Foreman, A.D., Meeks, C., Steele, A., Cooper, T., Phillips, A. and Mouritz, A.P. Shape Memory Alloy Tufted Composites Combining High Delamination Resistant And Crack Closure Properties. Composites Part A: Applied Science and Manufacturing, p.106455, 2021. https://doi.org/10.1016/j.compositesa.2021.106455.
- He, Y., Deng, B., Wang, H., Cheng, L., Zhou, K., Cai, S., Ciampa, F. Infrared machine vision and infrared thermography with deep learning: a review. Infrared Physics & Technology, p.103754, 2021. https://doi.org/10.1016/j.infrared.2021.103754.
- Malik, M.K., Chronopoulos, D., Ciampa, F. Direct Calculation of the Group Velocity for Two-Dimensional Complex, Composite and Periodic Structures Using a Wave and Finite Element Scheme. Applied Sciences, 11(10), p.4319, 2021 https://doi.org/10.3390/app11104319.
- Sherwood, G.R., Chronopoulos, D., Marini, M., Ciampa, F. 3D-printed phononic crystal waveguide transducers for nonlinear ultrasonic damage detection. NDT & E International, p.102456., 2021. https://doi.org/10.1016/j.ndteint.2021.102456.
- Wang, Z., Wan, L., Xiong, N., Zhu, J., Ciampa, F. Variational level set and fuzzy clustering for enhanced thermal image segmentation and damage assessment. NDT & E International, 118, p.102396, 2021 https://doi.org/10.1016/j.ndteint.2020.102396.
- Andreades, C., Meo, M., Ciampa, F. Fatigue testing and damage evaluation using smart CFRP composites with embedded PZT transducers. Materials Today: Proceedings, 34, pp.260-265, 2021. https://doi.org/10.1016/j.matpr.2020.03.081.
- Cuomo, S., De Simone, M.E., Andreades, C., Ciampa, F. and Meo, M., Machine learning for impact detection on composite structures. Materials Today: Proceedings, 34, pp.93-98, 2021. https://doi.org/10.1016/j.matpr.2020.01.295.
- De Simone, M. E., Andreades, C., Meo, M., Ciampa, F. Smart composite detector of orbital debris and micrometeoroids particles. Materials Today: Proceedings, 34, pp.202-209, 2021. https://doi.org/10.1016/j.matpr.2020.02.796.
- de Castro, B. A., Baptista, F. G., Ciampa, F. A comparison of signal processing techniques for impedance-based damage characterization in carbon fibres under noisy inspections. Materials Today: Proceedings, 34, pp.275-279, 2021 https://doi.org/10.1016/j.matpr.2020.03.470.
- De Iuliis, A., Ciampa, F., Felicetti, L., Ceriotti, M. Sailing with solar and planetary radiation pressure. Advances in Space Research, 67(9), 2795-2811, 2021 https://doi.org/10.1016/j.asr.2019.11.036.
- Meng, H., Bailey, N., Chen, Y., Wang, L., Ciampa, F., Fabro, A., Chronopoulos, D., Elmadih, W. 3D rainbow phononic crystals for extended vibration attenuation bands. Scientific Reports, 10(1), 1-9, 2020 https://doi.org/10.1038/s41598-020-75977-8.
- Deng, B., Li, X., Wang, H., He, Y., Ciampa, F., Li, Y., Zhou, K. Line Scanning Thermography Reconstruction Algorithm for Defects Inspection with Novel Velocity Estimation and Image Registration. IEEE Sensors Journal, 2020 https://doi.org/10.1109/JSEN.2020.3034460.
- de Castro, B. A., Baptista, F. G., Ciampa, F. New Imaging Algorithm for Material Damage Localisation Based on Impedance Measurements under Noise Influence. Measurement, 107953, 2020 https://doi.org/10.1016/j.measurement.2020.107953.
- Andreades, C., Meo, M., Ciampa, F. Tensile and fatigue testing of impacted smart CFRP composites with embedded PZT transducers for nonlinear ultrasonic monitoring of damage evolution. Smart Materials and Structures, 29(5), 055034, 2020 https://doi.org/10.1088/1361-665X/ab7f41.
- Coles, A., de Castro, B. A., Andreades, C., Baptista, F. G., Meo, M., Ciampa, F. Impact localisation in composites using time reversal, embedded PZT transducers and topological algorithms. Frontiers in Built Environment, 6 27, 2020 https://doi.org/10.3389/fbuil.2020.00027.
- Giannì, C., Balsi, M., Esposito, S., Ciampa, F. Low‐power global navigation satellite system‐enabled wireless sensor network for acoustic emission localisation in aerospace components. Structural Control and Health Monitoring, 27(6), e2525, 2020 https://doi.org/10.1002/stc.2525.
- Fierro, G. P. M., Ciampa, F., Meo, M. Phase symmetry analysis for nonlinear ultrasonic modulated signals. Structural Control and Health Monitoring, 27(5), e2516, 2020 https://doi.org/10.1002/stc.2516.
- Wang, Z., Zhu, J., Tian, G.-Y., Ciampa, F. Comparative analysis of eddy current pulsed thermography and long pulse thermography for damage detection in metals and composites. NDT & E International, 107, 102155, 2019 https://doi.org/10.1016/j.ndteint.2019.102155.
- Andreades, C., Fierro, G. P. M., Meo, M., Ciampa, F. Nonlinear Ultrasonic Inspection of Smart CFRP Composites with Embedded PZT Transducers for Space Applications. Journal of Intelligent Material Systems and Structures, 30(20), 2995-3007, 2019 https://doi.org/10.1177/1045389X19873419.
- Sutthaweekul, R., Tian, G.-Y., Wang, Z., Ciampa, F. Microwave open-ended waveguide for detection and characterisation of FBHs in coated GFRP pipes. Composite Structures, 225, 111080, 2019 https://doi.org/10.1016/j.compstruct.2019.111080.
- Wang, D., Wang, Z., Zhu, J., Ciampa, F. Enhanced pre-processing of thermal data in long pulse thermography using the Levenberg-Marquardt algorithm. Infrared Physics & Technology, 99, 158-166, 2019 https://doi.org/10.1016/j.infrared.2019.04.009.
- de Castro, B. A., Baptista, F. G., Ciampa, F. New Signal Processing Approach for Structural Health Monitoring in Noisy Environments Based on Impedance Measurements. Measurement, 137, 155-167, 2019 https://doi.org/10.1016/j.measurement.2019.01.054.
- De Simone, M. E., Andreades, C., Hilmi, A. M., Meo, M., Ciampa, F. Proof of concept for a smart composite orbital debris detector. Acta Astronautica, 160, 499-508, 2019 https://doi.org/10.1016/j.actaastro.2019.02.024.
- de Castro, B. A., Baptista, F. G., Ciampa, F. Comparative analysis of signal processing techniques for impedance-based SHM applications in noisy environments. Mechanical Systems and Signal Processing, 126, 326-340, 2019 https://doi.org/10.1016/j.ymssp.2019.02.034.
- De Simone, M., Ciampa, F., Meo, M. A Hierarchical Method for the Impact Force Reconstruction in Composites Structures. Smart Materials and Structures, 28(8), 085022, 2019 https://doi.org/10.1088/1361-665X/aae11c.
- Boccardi, Ciampa, F., Meo, M. Design and development of a heatsink for thermo-electric power harvesting in aerospace applications. Smart Materials and Structures, 28(10), 105057, 2019 https://doi.org/10.1088/1361-665X/aacbac.
- De Castro, B. A., Baptista, F. G., Rey, J. A. A., Ciampa, F. A chromatic technique for structural damage detection under noise effects based on impedance measurements. Measurement Science and Technology, 30(7), 075601, 2019 https://doi.org/10.1088/1361-6501/ab0fe2.
- Andreades, C., Mahmoodi, P., Ciampa, F. Characterisation of Smart CFRP Composites with Embedded PZT Transducers for Nonlinear Ultrasonic Applications. Composite Structures, 206, 456-466, 2018 https://doi.org/10.1016/j.compstruct.2018.08.083.
- Wang, Z., Tian, G., Meo, M., Ciampa, F. Image Processing based Quantitative Damage Evaluation in Composites with Long Pulse Thermography. NDT & E International, 99, 93-104, 2018 https://doi.org/10.1016/j.ndteint.2018.07.004.
- Dyrwal, A., Meo, M., Ciampa, F. Nonlinear Air-Coupled Thermosonics for Fatigue Micro-Damage Detection and Localisation. NDT & E International, 97, 59-67, 2018 https://doi.org/10.1016/j.ndteint.2018.03.012.
- Ciampa, F., Mahmoodi, P., Pinto, F., Meo, M. Recent Advances of Active Infrared Thermography for Non-destructive Testing of Aerospace Components. Sensors, 18(2), 609, 2018 https://doi.org/10.3390/s18020609.
- Nicassio, F., Scarselli, G., Pinto, F., Ciampa, F., Iervolino, O., Meo, M. Low energy actuation technique of bistable composites for aircraft morphing. Aerospace Science and Technology, 75, 35-46, 2018 https://doi.org/10.1016/j.ast.2017.12.040.
- Dionysopoulos, D., Fierro, G. P. M., Meo, M., Ciampa, F. Imaging of barely visible impact damage on a composite panel using nonlinear wave modulation thermography. NDT & E International, 95, 9-16, 2018 https://doi.org/10.1016/j.ndteint.2018.01.005.
- Boccardi, S., Calla’, D.-B., Ciampa, F., Meo, M. Nonlinear elastic multi-path reciprocal method for damage localisation in composite materials. Ultrasonics 82, 239-245, 2018 https://doi.org/10.1016/j.ultras.2017.09.001.
- Ciampa, F., Mankar, A., Marini, A. Phononic Crystal Waveguide Transducers for Nonlinear Elastic Wave Sensing. Scientific Reports 7(1), 14712, 2017 https://doi.org/10.1038/s41598-017-14594-4.
- De Simone, M., Ciampa, F., Boccardi, S., Meo, M. Impact Source Localisation in Aerospace Composite Structures. Smart Materials and Structures, 26(12), 125026, 2017 https://doi.org/10.1088/1361-665X/aa973e.
- Fierro, G. P. M., Ginzburg, D., Ciampa, F., Meo, M. Imaging of barely visible impact damage on a complex composite stiffened panel using a nonlinear ultrasound stimulated thermography approach. Journal of Nondestructive Evaluation, 36(4), 69, 2017 https://doi.org/10.1007/s10921-017-0449-x.
- Ginzburg, D., Ciampa, F., Scarselli, G., Meo, M. SHM of Single Lap Adhesive Joints using Subharmonic Frequencies. Smart Materials and Structures, 26(10), 105018, 2017 https://doi.org/10.1088/1361-665X/aa815c.
- Fierro, G. P. M., Ginzburg, D., Ciampa, F., Meo, M. Nonlinear ultrasonic stimulated thermography for damage assessment in isotropic fatigued structures. Journal of Sound and Vibration, 404, 102-115, 2017 https://doi.org/10.1016/j.jsv.2017.05.041.
- Scarselli, G., Nicassio, F., Ciampa, F., Meo, M. Non-linear methods based on ultrasonic waves to analyse disbonds in single lap joints. Proceedings of the Institution of Mechanical Engineers, Part C: Journal of Mechanical Engineering Science, 231(16), 3066-3076, 2017 https://doi.org/10.1177/0954406217704222.
- Ciampa, F., Scarselli, G., Pickering, S., Meo, M. Nonlinear imaging of damage in composite structures using sparse ultrasonic sensor arrays. Structural Control and Health Monitoring, 24(5), 2017 https://doi.org/10.1002/stc.1911.
- Ciampa, F., Scarselli, G., Meo, M. On the generation of nonlinear damage resonance intermodulation for elastic wave spectroscopy. The Journal of the Acoustical Society of America, 141(4), 2364-2374, 2017 https://doi.org/10.1121/1.4979256.
- Scarselli, G., Nicassio, F., Pinto, F., Ciampa, F., Iervolino, O., Meo, M. A novel bistable energy harvesting concept. Smart Materials and Structures, 25(5), 055001, 2016 https://doi.org/10.1088/0964-1726/25/5/055001.
- Angioni S.-L., Ciampa, F., Pinto, F., Scarselli, G., Almond, D.-P. Meo, M. An analytical model for defect depth estimation using pulsed thermography. Experimental Mechanics, 56(6), 1111-1122, 2016 https://doi.org/10.1007/s11340-016-0143-4.
- Ciampa, F., Boccardi, S., Meo, M. Factors affecting the imaging of impact location with inverse filtering and diffuse wave fields. Journal of Intelligent Material Systems and Structures, 27(11), 1523-1533, 2016 https://doi.org/10.1177%2F1045389X15596622.
- Ciampa, F., Meo, M. Nonlinear imaging method using second order phase symmetry analysis and inverse filtering. Journal of Nondestructive Evaluation, 34 (2), 1-6, 2015 https://doi.org/10.1007/s10921-015-0279-7.
- Ciampa, F., Scarselli, G., Pickering, S., Meo, M. Nonlinear elastic wave tomography for the imaging of corrosion damage. Ultrasonics, 62, 147-155, 2015 https://doi.org/10.1016/j.ultras.2015.05.011.
- Malfense Fierro, G.-P, Ciampa, F., Ginzburg, D., Onder, E., Meo, M. Nonlinear ultrasound modelling and validation of fatigue damage. Journal of Sound and Vibration, 343, 121-130, 2015 https://doi.org/10.1016/j.jsv.2014.10.008.
- Ciampa, F., Onder, E., Barbieri, E., Meo, M. Detection and Modelling of Nonlinear Elastic Response in Damaged Composite Structures. Journal of Nondestructive Evaluation, 33 (4), 515-521, 2014 https://doi.org/10.1007/s10443-008-9061-7.
- Ciampa, F., Barbieri, E., Meo, M. Modelling of Multiscale Nonlinear Interaction of Elastic Waves with Three Dimensional Cracks. The Journal of Acoustical Society of America, 135(6), 3209-3220, 2014 https://doi.org/10.1121/1.4868476.
- Ciampa, F., Meo, M. Impact location on a composite tail rotor blade using an inverse filtering approach. Journal of Intelligent Material Systems and Structures, 25 (15), 1950-1958, 2014 https://doi.org/10.1177%2F1045389X13512904.
- Pinto, F., Ciampa, F., Meo, M., Polimeno, U. Multifunctional SMArt composite material for in situ NDT/SHM and de-icing. Smart Materials and Structures, 21 105010, 2012 https://doi.org/10.1088/0964-1726/21/10/105010.
- Ciampa, F., Meo, M. Nonlinear elastic imaging using reciprocal time reversal and phase symmetry analysis. The Journal of Acoustical Society of America, 131(6), 4316-4323, 2012 https://doi.org/10.1121/1.4707522.
- Ciampa, F., Barbieri, E., Meo, M. Impact localization in composite structures of arbitrary cross section. Structural Health Monitoring, 11 (6), 643–655, 2012 https://doi.org/10.1177%2F1475921712451951.
- Ciampa, F., Meo, M. Impact detection in anisotropic materials using a time reversal approach. Structural Health Monitoring, 11 (1), 43-49, 2012 https://doi.org/10.1177%2F1475921710395815.
- Ciampa, F., Meo, M. Acoustic emission localization in complex dissipative anisotropic structures using a one-channel reciprocal time reversal method. The Journal of Acoustical Society of America, 130(1), pp. 168-175, 2011 https://doi.org/10.1121/1.3598458
- Ciampa, F., Meo, M. A new algorithm for acoustic emission localization and flexural group velocity determination in anisotropic structures. Composites: Part A: Applied Science and Manufacturing, 41(12), 1777-1786, 2010 https://doi.org/10.1016/j.compositesa.2010.08.013.
- Ciampa, F., Meo, M. Acoustic emission source localization and velocity determination of the fundamental mode A0 using wavelet analysis and a Newton-based optimization technique. Smart Materials and Structures, 22(3), 482-489, 2010 (https://doi.org/10.1088/0964-1726/19/4/045027.
- Capezzuto, F., Ciampa, F., Carotenuto G., Meo, M., Milella, E., Nicolais F. A smart multifunctional polymer nanocomposites layer for the estimation of low-velocity impact damage in composite structures. Composite Structures, 92(8), 1913-1919, 2010 https://doi.org/10.1016/j.compstruct.2010.01.003.