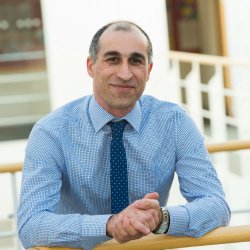
Dr Bahman Amini Horri
Academic and research departments
School of Chemistry and Chemical Engineering, Faculty of Engineering and Physical Sciences, Institute for Sustainability.About
Biography
Dr Bahman Horri is an Associate Professor of Energy Materials and the MSc programme leader in the School of Chemistry and Chemical Engineering at the University of Surrey. He is also a Sustainability Fellow at Surrey's Institute for Sustainability and an adjunct research fellow at Monash University. He coordinates the research studies in nanocomposite materials for Clean Energy applications (green hydrogen, solid oxide fuel cells & electrolysers (SOFCs/SOECs), and thermo-electrochemical water splitting), holding 7 US/European patents, 60+ papers in top-tiered journals, 5 book chapters, and 30+ presentations as the keynote, invited, or plenary speaker at national/international conferences. He received his PhD in Chemical Engineering from Monash University in 2012 (Australia). The national and international communities have recognised his research in hydrogen and fuel cells with multiple awards, including the IAAM Lecture Award (2023, Sweden), Research Supervision Award (2022, Surrey), Innovation Award in Emerging Technologies (2021, UK), Leverhulme Trust Research Fellowship Award (2021, UK), Postgraduate Publication Award (2012, Australia), etc. He is currently the PI of several research and commercialisation projects in Energy Materials and Sustainability sponsored by the EPSRC, the Royal Academy of Engineering, Innovate UK, the Royal Society, and the industrial sector. So far, he has secured, as PI, over £2m in different competitive research grants. He has recently patented a hybrid water-splitting process (WO2020016580A2) combining water electrolysis hydrolysis processes for efficient green hydrogen production. With a multidisciplinary research and engineering background dedicated to ceramic fuel cells and material science, he is a member of IChemE with CEng and CSci qualifications. He is also a member of the scientific board of H2FC-Supergen (the hydrogen and fuel cell hub, UK), a member of the International Society of Electrochemistry (ISE), an associate Editor of Frontiers (in Materials Process Engineering) and a Guest Editor of Energies, and Fellow of Higher Education Academy (UK FHEA).
Areas of specialism
University roles and responsibilities
- MSc Programmes Coordinator
- IChemE Liaison of the CPE Department
- The CPE Health and Safety Committee representative in the Department of Physics
- Former AIO of the CPE Department
- Green Hydrogen and Fuel Cell Research Cooridinator (Energy and Material Research Group)
My qualifications
Previous roles
Affiliations and memberships
Business, industry and community links
- Guest Editor, Special Issue Energies: Emerging Materials and Fabrication Methods for Solid Oxide Fuel Cells (SOFCs)
- Editorial board of “American Journal of Materials Science and Engineering”
- Reviewing board of International Conferences on Chemical Engineering and Applications: CCEA 2014, CCEA 2015, ICSEE 2015, ICCSE 2015, ICBBE 2015, and ICCSE 2017
- Technical Committee Member for ICPEME-2018, ICPEME-2019, ICCMME2020, and ICCMME 2021 conferences
- Member of the UK’s Advanced Materials Community for roadmapping of the ‘Strategic Low Carbon Hydrogen Production Technologies’
- Research Proposal Reviewer for EPSRC and Finland’s Higher Education Academy
- Journal paper reviewer for the ‘Journal of Materials Chemistry’, ‘Advanced Powder Technology’, ‘Ceramics International’, ‘Chemosphere’, ‘Journal of Alloys and Compounds’, ‘International Journal of Hydrogen Energy’, and ‘Thermochimica Acta’
European Fuel Cell Forum -2019 (Invited Speaker, EFCF 2019 Conference )
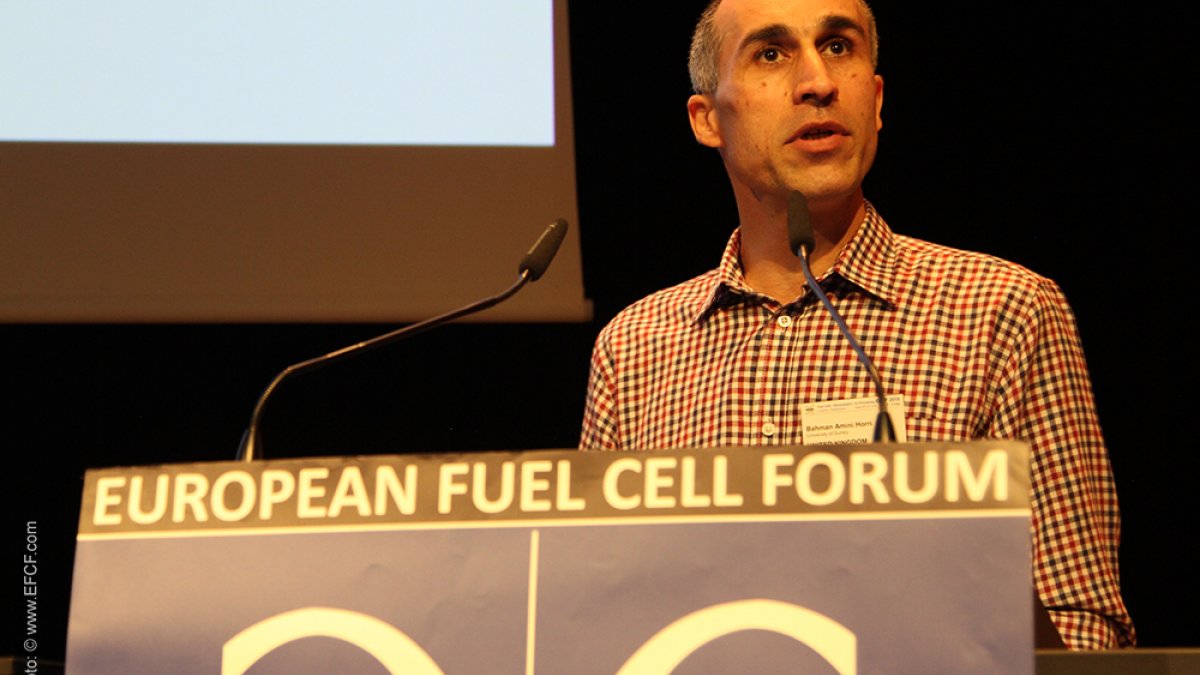
Winner of Guildford’s Innovation Award - 2018: Emerging Technologies “Tomorrow's World” for hydrogen generation patent
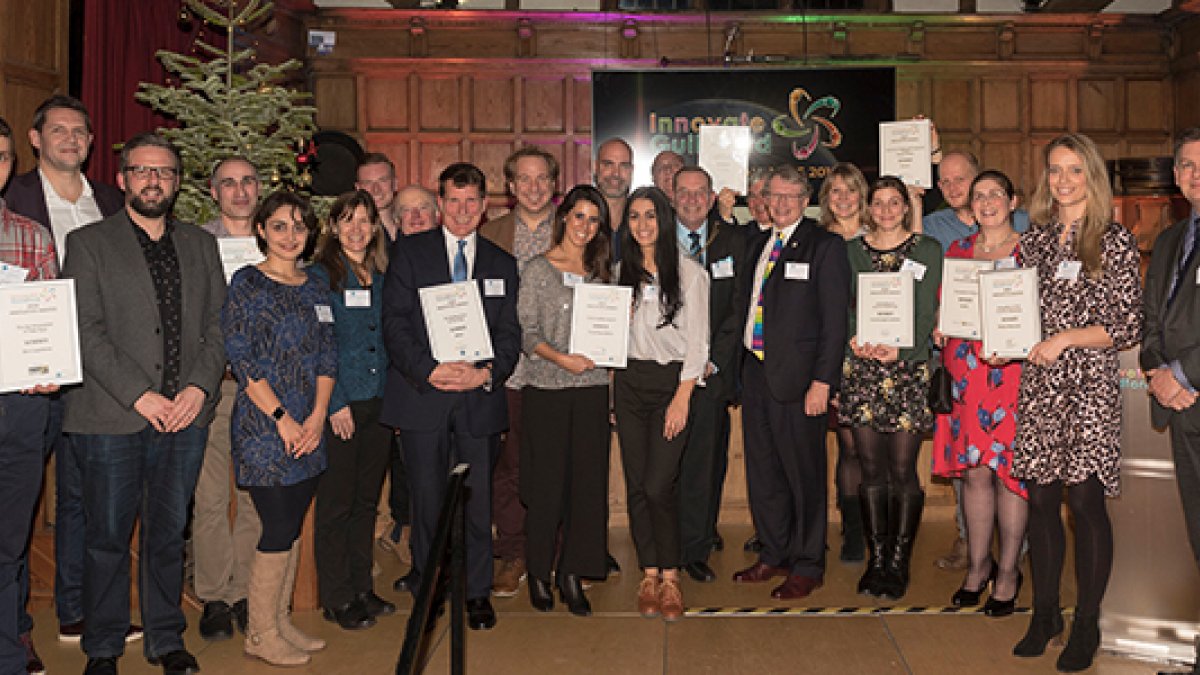
Newton Fund Researcher Links Workshops (Nanging, China, 2017)
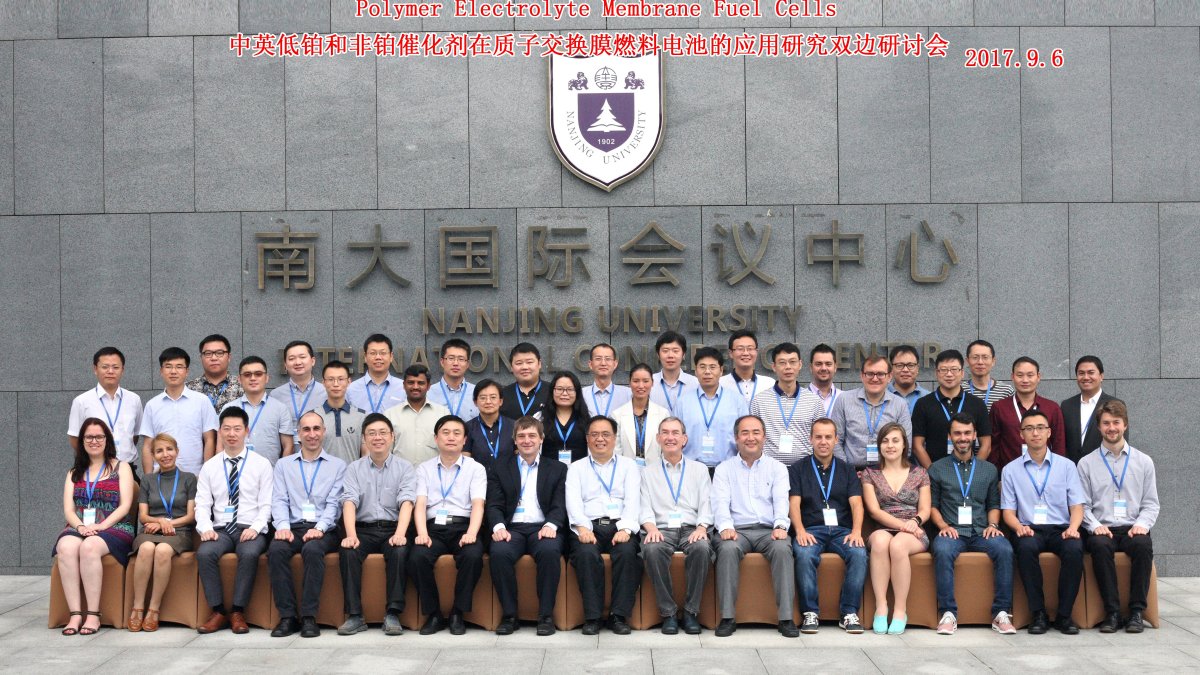
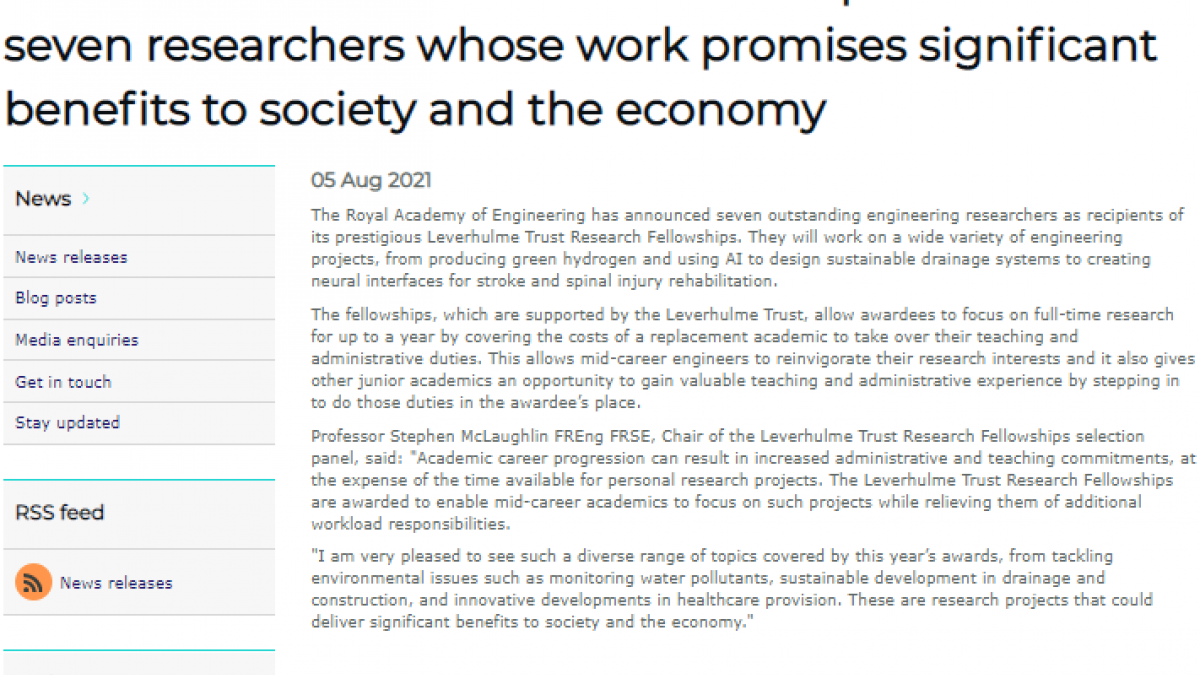
News
In the media
Innovate Guildford - 2018 (Guildford, Surrey)
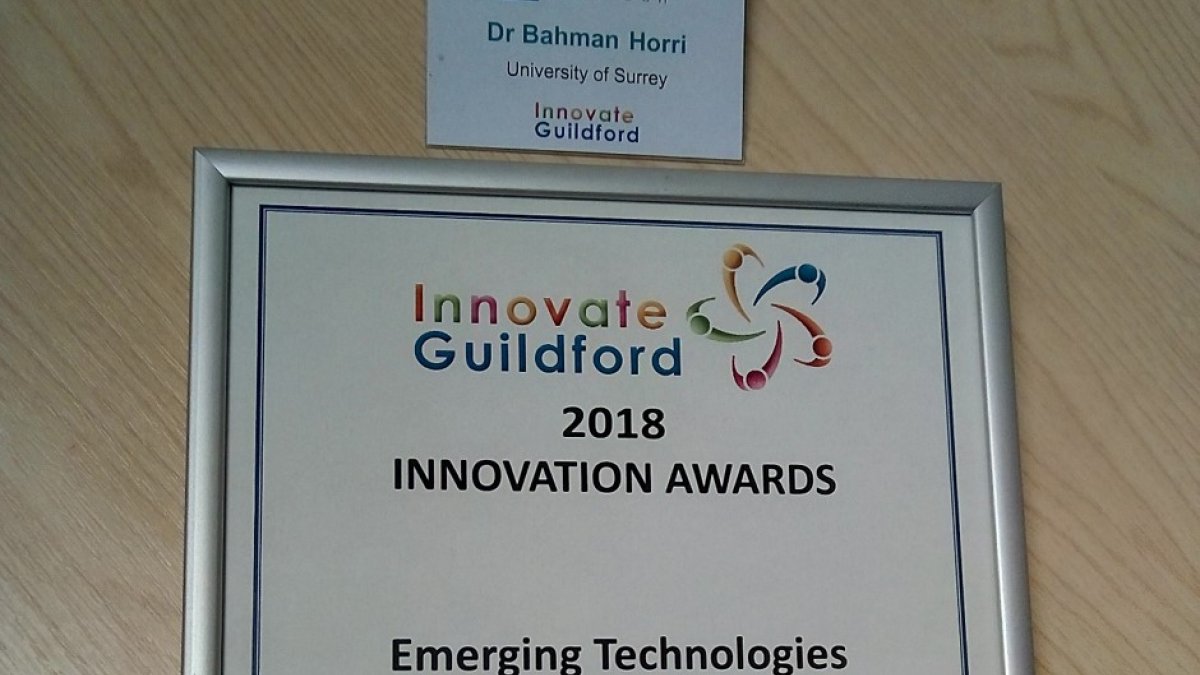
Leverhulme Trust Research Fellowships
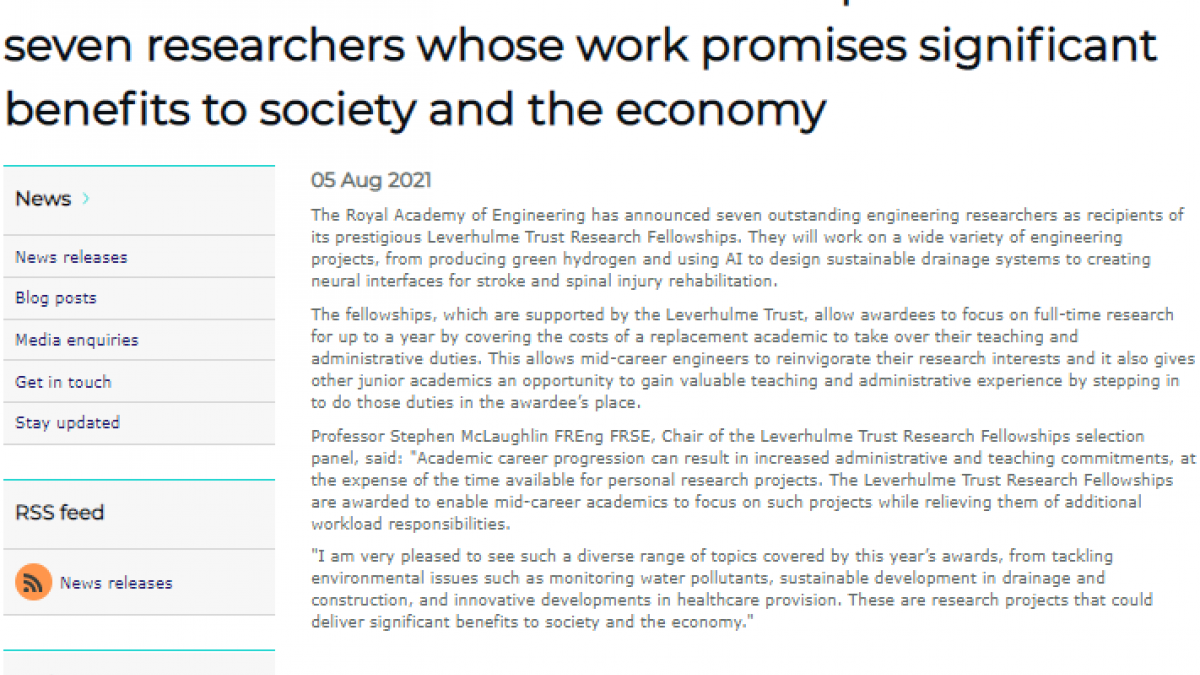
ResearchResearch interests
My current research interest mainly lies in the fields of green hydrogen production, solid oxide fuel cells / electrolysers (SOFCs/SOECs), and green synthesis of energy materials.
In terms of green hydrogen, my research mainly focuses on designing and developing novel systems and hybrid chemical looping processes for water-splitting. Hydrogen has been determined to play a significant role in deploying prospective low-carbon technologies with great versatility to provide sustainable heat, transport, and power system services.
My research in this field focuses on developing hybrid chemical looping systems by combining the electrochemical and thermolysis processes for splitting water at low – intermediate temperature ranges. I have recently patented a highly efficient electrolyser for hydrogen production (WO2019/002841 A1) and a hybrid process for sustainable production of hydrogen using metal/metal-oxide looping (WO 2020/016580 A2).
The development of new ceramic nanocomposites for lowering the operating temperature of SOFCs/SOECs is another aspect of my research. In this field, I mainly focus on improving the thermochemical and electrochemical performance of the L-T SOFCs/SOECs by developing superionic heterogenous solid composite electrolytes and optimising the microstructural properties of electrodes (porosity, surface area, and electrical conductivity).
The other aspect of my research is the development of novel, cost-effective, and environmentally friendly synthesis methods for energy materials (anode, electrolyte, and cathode nanocomposites). The objective of my current research in this field is to develop low-cost, efficient, and highly active ceramic nanocomposites for improving the electrochemical properties, thermo-mechanical properties, and durability of the fabricated SOFCs/SOECs, which are all the major challenges currently associated with the development of ceramic fuel-cells in both the research and manufacturing communities.
Here is a summary of my research interests:
- Hydrogen production, water splitting, and thermochemical looping
- Solid oxide fuel cells and electrolysers (especially low temperature SOFCs and SOECs)
- Ceramic nanocomposites and nanomaterial synthesis
- Green synthesis of metal oxides, nanocomposite ceramics, and catalysts
- Ammonia synthesis with solid oxide electrolysers, microstructural improvement of SOFC/EC electrodes
- Alkaline electrolysers and flow cells
Main equipment/facilities in my research lab (the Energy Lab)
- High temperature fuel cell (SOFC/SOEC) testing rig, potentiostat/galvanostat, DC loads, high resolution desktop multimeters
- An innovative water splitting setup for hydrogen production
- BET, TGA, Pycnometer, mercury porosimeter
- Spin coater, lab press, screen printing unit, tube and muffle furnaces, etc.
Research projects
Research Grants:- Jul 2022 – Jun 2023: UKRI: Innovate UK - Smart Grants: Clean Hydrogen Manufacture, CHROME (£ 364,527); PI
- Jul 2022 – Jun 2023: EPSRC: EP/W033178/1: Production and Integration of zero emission hydrogen, METASTASIS (£ 238,947); Co-I
- Nov 2022 – Mar 2023: UKRI: Innovate UK - Fast Start: Innovation: Power-to-gas via microbial electrosynthesis, (£ 49,998); Co-I
- Jul 2021 – Jun 2022 Royal Academy of Engineering (LTRF2021\17131): Leverhulme Trust Research Fellowship: Development of a Redox Hydrothermal Reactor for Hydrogen Production (£ 33,727); PI (link)
- Jul 2021 – Mar 2022 EPSRC IAA Grant 2021/22: A Techno-economic Analysis for Large-Scale Hydrogen Production (£ 32,000); PI
- Aug 2021 – Jul 2022 UGPN Research Grant: Synergistic Hybrid Marine Renewable Energy Harvest Systems; Co-I
- Oct 2020 – Sep 2021 Royal Society Research Grants 2020 (RGS\R2\202137): Improving Ionic Conductivity of Co-Doped Ceria Based Nanocomposite Electrolytes (£ 20,000); PI
- Feb 2019 – Jan 2020 Equipment Capital Funding (FEPS): Surface area analysis matching fund (£ 89,000); PI
- Oct 2017 – Mar 2018 Innovation Voucher: Development of an innovative washable ceramic filter with a high surface area (£ 7,000); PI
- Jan 2017 – Jan 2018 Equipment Capital Funding (FEPS): Microporous ceramic nanocomposite (£ 82,000); PI
- Jul 2016 – Mar 2017 Starting Grant: Energy materials for solid oxide fuel cells (£ 10,000); PI
- Dec 2015– Dec 2018 eScience Grant (Ministry of Science, Technology, and Innovations, Malaysia), Hierarchically-Structured Nanocomposites for Improving Microstructural and Electrochemical Properties of Metal-Supported Solid Oxide Fuel Cells, Project no: 03-02-10-SF0259, RM 112,000; PI
- Jul 2014 – Jun 2017 FRGS Grant (Fundamental Research Grant Scheme, Ministry of Higher Education, Malaysia), Redox Stable Anode-Supported Solid Oxide Fuel Cell by Nanostructured Electrode Composites Using Nickel Oxide Nanowires, FRGS/2/2014/TK05/MUSM/03/2, RM 82,100; PI
- Nov 2013– Oct 2014 Multidisciplinary Platform of Advanced Engineering Grant, School of Engineering, Monash Malaysia, Improving Anode Microstructure for Ceramic Fuel Cells, 2014, RM27,000; PI
Indicators of esteem
Awards:
2021: Innovation Award in Caring for the Environment, Innovative Guildford, Surrey, UK
2020: IAAM: Award Lecture of the International Association of Advanced Materials, Sweden.
2020: InnoEnergy Award: Top 10% finalist in the 9th Call of Repsol Foundation’s Entrepreneurs Fund accelerator program, Germany.
2018: Innovation Award in Emerging Technologies: Tomorrow's World, Innovative Guildford, Surrey, UK.
2012: Postgraduate Publication Award, Monash University.
2009: Monash Graduate Scholarship (MGS), Monash University.
2009: Faculty of Engineering International Post Graduate Scholarship (FEIPRS), Monash University.
1997: The Best Industrial Trainee Award, Iran University of Science and Technology.
Patents:
- UK Patent GB1811785.3, PCT/GB2019/052002 (2019): A Continuous Process for Sustainable Production of Hydrogen. filed on 19/07/2018. B.A. Horri, S. Gu.
- UK Patent GB1710224.5, PCT/GB2018/051778 (2018): Hydrogen Generator. filed on 27/06/2017). B.A. Horri, S. Gu, M. Choolaei.
- US Patent 9,206,050 B2 (2015): Continuous Process for Producing Carbon Nanotubes. A.M. Rashidi, B.A. Horri, A. Mohajeri, S. Sadraei Noori, K. Jafari Jozani, A. Nakhaeipor.
- European Patent EP2196260 (2010), US Patent 20100167915 (2010): Hydrodesulphurization Nanocatalyst, Its Use and a Process for Its Production. A. Mohajeri, A.M. Rashidi, K. Jafari Jozani, P. Khorami, B. Amini Horri, D. Parviz, M. Kalbasi.
- US Patent 7,491,750 (2009), also European Patent EP1754769 (2007): Continuous Catalyst/Wax Separation Method. H.R. Khakdaman, B.A. Horri, H. Manafi Varklani, S. Sadraei Noori.
Recent Presentations as the Keynote / Invited Speaker:
- B.A. Horri “Green Hydrogen Production: Major Developments and Future Prospects” Keynote Speaker and Panel Member: G3 Energy Summit - 2022, Rudolf Steiner House, London, UK, 19 March 2022
- B.A. Horri and S. Gu, “Development of a red‐ox process for sustainable production of hydrogen” H2FC Supergene Hub Conference - 2020, University of Nottingham, Nottingham, UK, 17 – 18, Feb 2020.
- B.A. Horri, M.M. Choolaei, S. Gu, “Sustainable Production of Hydrogen Through a Metal/Metal-Oxide Loop”, EFCF 2019, The 23rd Conference in Series with Exhibition on Low-Temperature Fuel Cells, Electrolysers and H2 Processing, Fundamentals and Engineering Design, Lucerne, Switzerland, 2– 5 July 2019
- B.A. Horri, “Lowering the temperature of solid oxide fuel cells”. The 13th of European SOFC & SOE Forum, Lucerne, Switzerland. 3 – 6 Jul 2018
- B.A. Horri, “Synthesis and application of nanocomposite materials for ceramic fuel cells”, ICNN-2018, Tehran, IRAN, 26-28 Sep 2018.
- B.A. Horri, “A highly efficient hydrogen generation electrolysis system using alkaline zinc hydroxide solution”. The 2nd International Conference on Advanced Energy Materials, AEM-2017, University of Surrey, England, 11 – 13 Sep 2017
- B.A. Horri, “Gelling synthesis of NiO/YSZ nanocomposite powder for solid oxide fuel cells, The European Advanced Materials Congress, EAMC-2017, Stockholm, 22 – 24 Aug 2017.
I am currently accepting self-funded PhD and volunteer research applicants in the field of hydrogen, fuel cell, and energy materials. You may contact me (b.aminihorri@surrey.ac.uk) to discuss the available topics/projects.
Research interests
My current research interest mainly lies in the fields of green hydrogen production, solid oxide fuel cells / electrolysers (SOFCs/SOECs), and green synthesis of energy materials.
In terms of green hydrogen, my research mainly focuses on designing and developing novel systems and hybrid chemical looping processes for water-splitting. Hydrogen has been determined to play a significant role in deploying prospective low-carbon technologies with great versatility to provide sustainable heat, transport, and power system services.
My research in this field focuses on developing hybrid chemical looping systems by combining the electrochemical and thermolysis processes for splitting water at low – intermediate temperature ranges. I have recently patented a highly efficient electrolyser for hydrogen production (WO2019/002841 A1) and a hybrid process for sustainable production of hydrogen using metal/metal-oxide looping (WO 2020/016580 A2).
The development of new ceramic nanocomposites for lowering the operating temperature of SOFCs/SOECs is another aspect of my research. In this field, I mainly focus on improving the thermochemical and electrochemical performance of the L-T SOFCs/SOECs by developing superionic heterogenous solid composite electrolytes and optimising the microstructural properties of electrodes (porosity, surface area, and electrical conductivity).
The other aspect of my research is the development of novel, cost-effective, and environmentally friendly synthesis methods for energy materials (anode, electrolyte, and cathode nanocomposites). The objective of my current research in this field is to develop low-cost, efficient, and highly active ceramic nanocomposites for improving the electrochemical properties, thermo-mechanical properties, and durability of the fabricated SOFCs/SOECs, which are all the major challenges currently associated with the development of ceramic fuel-cells in both the research and manufacturing communities.
Here is a summary of my research interests:
- Hydrogen production, water splitting, and thermochemical looping
- Solid oxide fuel cells and electrolysers (especially low temperature SOFCs and SOECs)
- Ceramic nanocomposites and nanomaterial synthesis
- Green synthesis of metal oxides, nanocomposite ceramics, and catalysts
- Ammonia synthesis with solid oxide electrolysers, microstructural improvement of SOFC/EC electrodes
- Alkaline electrolysers and flow cells
Main equipment/facilities in my research lab (the Energy Lab)
- High temperature fuel cell (SOFC/SOEC) testing rig, potentiostat/galvanostat, DC loads, high resolution desktop multimeters
- An innovative water splitting setup for hydrogen production
- BET, TGA, Pycnometer, mercury porosimeter
- Spin coater, lab press, screen printing unit, tube and muffle furnaces, etc.
Research projects
- Jul 2022 – Jun 2023: UKRI: Innovate UK - Smart Grants: Clean Hydrogen Manufacture, CHROME (£ 364,527); PI
- Jul 2022 – Jun 2023: EPSRC: EP/W033178/1: Production and Integration of zero emission hydrogen, METASTASIS (£ 238,947); Co-I
- Nov 2022 – Mar 2023: UKRI: Innovate UK - Fast Start: Innovation: Power-to-gas via microbial electrosynthesis, (£ 49,998); Co-I
- Jul 2021 – Jun 2022 Royal Academy of Engineering (LTRF2021\17131): Leverhulme Trust Research Fellowship: Development of a Redox Hydrothermal Reactor for Hydrogen Production (£ 33,727); PI (link)
- Jul 2021 – Mar 2022 EPSRC IAA Grant 2021/22: A Techno-economic Analysis for Large-Scale Hydrogen Production (£ 32,000); PI
- Aug 2021 – Jul 2022 UGPN Research Grant: Synergistic Hybrid Marine Renewable Energy Harvest Systems; Co-I
- Oct 2020 – Sep 2021 Royal Society Research Grants 2020 (RGS\R2\202137): Improving Ionic Conductivity of Co-Doped Ceria Based Nanocomposite Electrolytes (£ 20,000); PI
- Feb 2019 – Jan 2020 Equipment Capital Funding (FEPS): Surface area analysis matching fund (£ 89,000); PI
- Oct 2017 – Mar 2018 Innovation Voucher: Development of an innovative washable ceramic filter with a high surface area (£ 7,000); PI
- Jan 2017 – Jan 2018 Equipment Capital Funding (FEPS): Microporous ceramic nanocomposite (£ 82,000); PI
- Jul 2016 – Mar 2017 Starting Grant: Energy materials for solid oxide fuel cells (£ 10,000); PI
- Dec 2015– Dec 2018 eScience Grant (Ministry of Science, Technology, and Innovations, Malaysia), Hierarchically-Structured Nanocomposites for Improving Microstructural and Electrochemical Properties of Metal-Supported Solid Oxide Fuel Cells, Project no: 03-02-10-SF0259, RM 112,000; PI
- Jul 2014 – Jun 2017 FRGS Grant (Fundamental Research Grant Scheme, Ministry of Higher Education, Malaysia), Redox Stable Anode-Supported Solid Oxide Fuel Cell by Nanostructured Electrode Composites Using Nickel Oxide Nanowires, FRGS/2/2014/TK05/MUSM/03/2, RM 82,100; PI
- Nov 2013– Oct 2014 Multidisciplinary Platform of Advanced Engineering Grant, School of Engineering, Monash Malaysia, Improving Anode Microstructure for Ceramic Fuel Cells, 2014, RM27,000; PI
Indicators of esteem
Awards:
2021: Innovation Award in Caring for the Environment, Innovative Guildford, Surrey, UK
2020: IAAM: Award Lecture of the International Association of Advanced Materials, Sweden.
2020: InnoEnergy Award: Top 10% finalist in the 9th Call of Repsol Foundation’s Entrepreneurs Fund accelerator program, Germany.
2018: Innovation Award in Emerging Technologies: Tomorrow's World, Innovative Guildford, Surrey, UK.
2012: Postgraduate Publication Award, Monash University.
2009: Monash Graduate Scholarship (MGS), Monash University.
2009: Faculty of Engineering International Post Graduate Scholarship (FEIPRS), Monash University.
1997: The Best Industrial Trainee Award, Iran University of Science and Technology.
Patents:
- UK Patent GB1811785.3, PCT/GB2019/052002 (2019): A Continuous Process for Sustainable Production of Hydrogen. filed on 19/07/2018. B.A. Horri, S. Gu.
- UK Patent GB1710224.5, PCT/GB2018/051778 (2018): Hydrogen Generator. filed on 27/06/2017). B.A. Horri, S. Gu, M. Choolaei.
- US Patent 9,206,050 B2 (2015): Continuous Process for Producing Carbon Nanotubes. A.M. Rashidi, B.A. Horri, A. Mohajeri, S. Sadraei Noori, K. Jafari Jozani, A. Nakhaeipor.
- European Patent EP2196260 (2010), US Patent 20100167915 (2010): Hydrodesulphurization Nanocatalyst, Its Use and a Process for Its Production. A. Mohajeri, A.M. Rashidi, K. Jafari Jozani, P. Khorami, B. Amini Horri, D. Parviz, M. Kalbasi.
- US Patent 7,491,750 (2009), also European Patent EP1754769 (2007): Continuous Catalyst/Wax Separation Method. H.R. Khakdaman, B.A. Horri, H. Manafi Varklani, S. Sadraei Noori.
Recent Presentations as the Keynote / Invited Speaker:
- B.A. Horri “Green Hydrogen Production: Major Developments and Future Prospects” Keynote Speaker and Panel Member: G3 Energy Summit - 2022, Rudolf Steiner House, London, UK, 19 March 2022
- B.A. Horri and S. Gu, “Development of a red‐ox process for sustainable production of hydrogen” H2FC Supergene Hub Conference - 2020, University of Nottingham, Nottingham, UK, 17 – 18, Feb 2020.
- B.A. Horri, M.M. Choolaei, S. Gu, “Sustainable Production of Hydrogen Through a Metal/Metal-Oxide Loop”, EFCF 2019, The 23rd Conference in Series with Exhibition on Low-Temperature Fuel Cells, Electrolysers and H2 Processing, Fundamentals and Engineering Design, Lucerne, Switzerland, 2– 5 July 2019
- B.A. Horri, “Lowering the temperature of solid oxide fuel cells”. The 13th of European SOFC & SOE Forum, Lucerne, Switzerland. 3 – 6 Jul 2018
- B.A. Horri, “Synthesis and application of nanocomposite materials for ceramic fuel cells”, ICNN-2018, Tehran, IRAN, 26-28 Sep 2018.
- B.A. Horri, “A highly efficient hydrogen generation electrolysis system using alkaline zinc hydroxide solution”. The 2nd International Conference on Advanced Energy Materials, AEM-2017, University of Surrey, England, 11 – 13 Sep 2017
- B.A. Horri, “Gelling synthesis of NiO/YSZ nanocomposite powder for solid oxide fuel cells, The European Advanced Materials Congress, EAMC-2017, Stockholm, 22 – 24 Aug 2017.
I am currently accepting self-funded PhD and volunteer research applicants in the field of hydrogen, fuel cell, and energy materials. You may contact me (b.aminihorri@surrey.ac.uk) to discuss the available topics/projects.
Supervision
Postgraduate research supervision
PhD Graduates (as the principal supervisor)
- 2018 – 2022: Nasrin Ghaemi: Solid oxide electrolyser for ammonia synthesis using water and nitrogen
- 2016 – 2020: Mohammadmehdi Choolaei: Lowering the operational temperature of solid oxide fuel cells
- 2016 – 2020: Andrew Dunne: Development of a stable and highly efficient sodium-ion battery
Current PhD Students
- 2021 – 2024: Yuheng Liu: Development of a metal-supported solid oxide electrolyser for efficient water splitting
- 2020 – 2023: Jing Li: Hydrogen production using solid oxide electrolysis cells
- 2019 – 2022: Junbin Huang: CO2 reduction through microbial electrolysis system and chemicals upgrading
MEng and MSc Graduates
- 2021 – 2022: Panagiotis Sarikas
- 2019 – 2020: Aaron Seabrook, Brad Apps, Jack McDermott, Berfin Aksoy, Pasang Sherpa, Mustafa Yasar Afacan, Albert Masso Basora
- 2018 – 2019: Tim Bull, Christian Harding, Isaiah Chase, Abdulrahman Mohamed, Usman Muhammad Alkali, Hussein Kaawar
- 2017 – 2018: Tomas Trendler, Peter Klim, Talia Brooks, Laura Quinlan, Rhiannon King, Umar Galadima, Mudiwa Maenzanise, Pranav Prakasan Sreekaladas
- 2016 – 2017: Ismail Unal, Sonal Meisuria, Aneeb Chaudhry, Hassan Qaalib, Ronnie Katungi, Ibongeninkosi Njani Mohamed Taher, Kwadwo Amponsah
PDRA and postdoctoral visiting researchers
- 2021 – 2022 Dr Hasan Ozcan: Modeling and simulation of thermochemical water-splitting processes
- 2019 – 2020 Dr Mohanad Oleiwi: The Investigation of Aqueous Ions Separation Using a Drift Cell
- 2019 – 2020 Dr Serdar Yilmaz: Investigation of electrical properties of a new type of proton-conducting electrolyte in energy materials.
- 2016 – 2017 Dr Maggie Svensson: Development of a ceramic filter with controlled surface area (with Smart Separation Ltd.)
Monash University (Sunway Campus):
PhD Graduates
- 2015 – 2020: Yuan Teng Foo: A Novel Approach to In-Situ Synthesis of Ceramic Nanocomposite Particles: Case for Gadolinia-doped YSZ
MSc Graduates
- 2015 – 2017: Hui Hui Lim: Carbon Microspheres synthesised from Crystalline Nano-Cellulose as pore former for NiO/YSZ composite using NiO sub-micro rods via co-precipitation route
- 2015 – 2017: Lee Jay Yang: Synthesis of Nickel Oxide Nanoparticles Using Gelatine as a Green Template for Photocatalytic Degradation of Dyes
- 2014 – 2017: Choo Cheng Keong: Synthesis of NiO-Nanoparticles Templated on Chitosan Biopolymer for Photocatalytic Degradation of Methylene Blue Dye
Teaching
Current Module / Courses:
- ENGM288: Batteries, Fuel Cells, and Supercapacitor technologies (MSc module, FHEQ Level 7, 15 Credits): Module Leader
- ENG3187: Advanced mass transfer (year 3, semester 2, FHEQ Level 6, 15 credits): Module Leader
- ENG3192/ENG3193 MEng/BEng Design Project (year 3, Semester 2, FHEQ Level 6, 45 credits).
- ENGM290: Chemical Engineering Research Project: (postgraduate, Semester 1 and 2, FHEQ Level 7, 30 credits)
- ENGM083: MSc Research Dissertation: (postgraduate, Semester 2 + summer, FHEQ Level 7, 60 credits)
Teaching Creativity:
New Programme Development:
- 2018 – 2019 MSc Programme: BFCESS: Batteries, Fuel Cells and Energy Storage Systems (Launched in 2019, Department of Chemical and Process Engineering, University of Surrey)
New Module Development:
- 2019 – 2020 MSc Module: ENGM288: Batteries, Fuel Cells and Supercapacitor Technologies (Department of Chemical and Process Engineering, University of Surrey)
MSc programme Leadership:
- PESE: Petroleum Refining Systems Engineering
- PSE: Process Systems Engineering
- BFCESS: Batteries, Fuel Cells and Energy Storage Systems
Sustainable development goals
My research interests are related to the following:
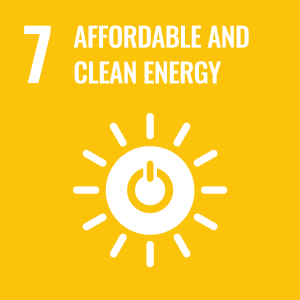
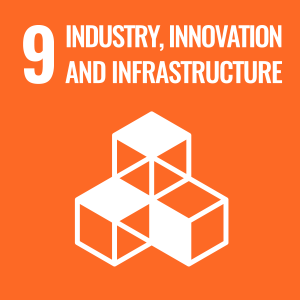
Publications
Highlights
Patents
- A Continuous Process for Sustainable Production of Hydrogen. WO 2020/016580 A2, (2020). B.A. Horri, S. Gu.
- Hydrogen Generator. US 2020/0115806 A1 (2020). B.A. Horri, S. Gu,
- Continuous Process for Producing Carbon Nanotubes. US Patent 9,206,050 B2 (2015), A.M. Rashidi, B.A. Horri, A. Mohajeri, S. Sadraei Noori, K. Jafari Jozani, A. Nakhaeipor.
- Hydrodesulphurization Nanocatalyst, Its Use and a Process for Its Production. US Patent 20100167915 (2010), also European Patent EP2196260 (2010). A. Mohajeri, A.M. Rashidi, K. Jafari Jozani, P. Khorami, B.A. Horri, D. Parviz, M. Kalbasi.
- Continuous Catalyst/Wax Separation Method. US Patent 7,491,750 (2009), also European Patent EP1754769 (2007). H.R. Khakdaman, B.A. Horri, H. Manafi Varklani, S. Sadraei Noori.
Book Chapters:
- M.M. Choolaei and B.A. Horri. "Catalytic aspects of fuel cells and electrolysers", In Heterogeneous catalysis for Energy applications, edited by T.R. Reina and J.A. Odriozola, In press (2020)
- M.Y. Wong, B.A. Horri, B. Salamatinia, Chapter 8 – "Grafted Copolymerized Chitosan and Its Applications as a Green Biopolymer", In Biopolymer Grafting, edited by Vijay Kumar Thakur, Elsevier, Pages 285-333, (2018)
- H.H. Lim, E. Sulistya, B. Salamatinia, and B.A. Horri "Ceramic Nanocomposites for Solid Oxide Fuel Cells". In "Sol-Gel Based Nanoceramic Material", Edited by Ajay Kumar Mishra, Springer (2017).
- P. Amouzgar, M.Y. Wong, B.A. Horri, B. Salamatinia "Advanced material for pharmaceutical removal from wastewater". In "Smart Materials for Wastewater Application", Edited by Ajay Kumar Mishra, Wiley-Scrivener Publisher (2016).
This study investigates the optimisation of the electrochemical performance of a novel Mn/MnSO₄ redox cycle using monovalent cations, including Li + , Na + , and K + , to enhance hydrogen generation. The reaction mechanism of cations in the simultaneous hydrogen evolution reaction (HER) and manganese electrodeposition reaction (MEDR) was confirmed through a systematic analysis of the co-evolution stages to maximise the cell electro-chemical performance. The results indicated that the effects of cations primarily depend on the differences between the activation of ion pairing/bridging and the inactivation of surface blocking for the HER and MEDR, along with the influence of mass-to-charge ratio, ion size, conductivity, ion distribution, and concentration polar-isation. A high concentration of cations can efficiently boost the cell performance and current density due to the enhancement of HER, even though it simultaneously leads to the inhibition of MEDR, presenting high energy efficiency and productivity, but low manganese CE. Optimal performance was achieved by adding K + cations using 0.8 mol/L potassium sulphate (K 2 SO 4) solution to MnSO 4 , with a pH of 2.86, which resulted in 7.16 % improved current efficiency. In addition, it was found that potassium cations can make the electrodeposited manganese metal more easily detached from the electrode and cause a lower corrosion current density, which is in favour of production. The proposed system and approach offer the advantages of reducing specific energy consumption by 7.23 % compared to the conventional cells, providing new insights into the electrochemical behaviour of redox pairs mediated water splitting systems for the next generation of scalable, low-cost PEM electrolysis systems for sustainable hydrogen production.
An effective power input is essential for achieving high-performance electrolysis in water splitting, characterised by a high hydrogen production rate and low energy consumption. This study investigates the optimisation of electrochemical performance in a novel hybrid manganese cycle by employing a superimposed pulsation technique to enhance hydrogen generation and realise " Power-to-Manganese-toGas ". The electrolysis system was comprised of a proton exchange membrane (PEM) incorporated with the Mn/MnSO 4 redox pair to facilitate efficient water splitting. The electrochemical performance measurements of the cell revealed that elevated cell voltages enhance the charge acquisition of Mn 2+ ions more than protons, thereby improving manganese recovery efficiency. However, this also introduces higher non-Faradaic losses, resulting in an increase in the specific energy consumption and a decrease in the overall energy conversion efficiency. The application of a superimposed pulse—featuring a peak voltage of 5.6 V and a base voltage of 3.5 V—proved beneficial in maintaining cathodic protection, supporting ion replenishment, reducing current oscillations, and sustaining the hydrogen evolution reaction. Moreover, pulse frequency was found to significantly influence productivity, while the duty cycle had a marked impact on improving current efficiency (99.43 %), overall energy conversion efficiency (37.11 %), manganese content (28.50 %), and other performance metrics. A duty cycle of 50 % at 50 Hz was identified as optimal , reducing specific energy consumption by 4.33 % compared to the conventional direct current operation.
Developing solid-state ionic conductors with desirable charge-transport efficiency and reasonable durability is a fundamental and long-lasting challenge for solid-oxide fuel cells (SOFCs). Ceria-based electrolytes, as one of the most common types of electrolytes for intermediate-temperature solid-oxide fuel cells (IT-SOFCs), offer a high surface-exchange coefficient and faster kinetics in the triple phase boundaries (TPBs); however, they suffer to some extent of electronic conductivity in the reducing atmosphere and gradual phase transitions. Here in this work, we have reported a novel co-doped IT-SOFC electrolyte composite combining the apatite structure of Lanthanum Silicate (LSO) with the fluorite structure of Gadolinium-doped Ceria (GDC), which showed a high ionic conductivity and a minimal electronic leak. The resulting GDC-LSO composite electrolyte also achieved an OCV (open-circuit voltage) of 1 V at 800 °C, implying a significant improvement in the OCV values reported for the typical ceria-based electrolytes (∼0.75 V). The sample was prepared using 40 wt% GDC and 60 wt% LSO (40GDC-60LSO) showed a maximum electrical conductivity of 25 mS cm−1 at 800 °C with good densification properties (>95 % relative density). The cell electrochemical performance measurement was conducted using a 3.0 vol% humified H2 stream at the anode side while the cathode side was exposed to the air at 800 °C. The interdiffusion of cations between La3+ in the LSO phase and Ce4+ and Gd3+ in the GDC phase was detected by XRD and EDX results after sintering samples at 1500 °C for 4 h using 0.5 wt% PVA or 0.5 wt% Ethyl cellulose (EC) as the binder. The proposed GDC-LSO composite could help better understand the influence of compositional constituents and processing variables on the densification and electrical properties of the electrolyte materials for the IT-SOFCs.
This study reports the reaction mechanism and electrolyte optimisation aspects of a novel low-temperature water-splitting system developed for the efficient production of hydrogen based on the Mn–MnSO4 redox pair. The system incorporates an electrolysis step and an Mn2+ ion recovery step for splitting water in a cyclic operation. Two steps operate within similar temperature ranges, enabling tight integration and efficient heat exchange. The optimisation of electrolytes for the electrolysis step was first carried out in a proton-exchange membrane (PEM) H-cell. The experiments were figured out using a three-factor case study based on the factorial design approach, incorporating temperature, concentration, and pH value as the main variables. Subsequently, machine learning models were employed to analyse the data and predict the best pairing of electrolytes by systematically exploring the critical ratio of conductivity to potential. The results showed that at a cell voltage of 5.0 V and 40 °C, the ratio of importance between the conductivity and MEDR potential is 1:9 for the catholyte, while the anolyte ratio of importance between the conductivity and OER potential is 6:4. Accordingly, the optimal electrolyte composition was found to be a combination of MnSO4 solution (1.64 mol/L; pH 2.86) with H2SO4 (25.25 wt%). Also, a remarkable corresponding current efficiency of 99.25 % was achieved with an overall energy conservation efficiency of 40.15 %. The proposed cycle is the first of its kind developed based on the chemical looping principle and can be potentially applied for large-scale continuous green hydrogen production at a low-levelized cost.. [Display omitted]. •A novel hybrid water-splitting cycle was proposed and validated for H2 production.•A factorial design approach was applied to optimise the electrolyte properties.•The two-stage current and cell-voltage mechanism were identified.•An unprecedented current efficiency showed great potential for scale up.
The disclosure provides a method of producing hydrogen. The method comprises conducting a thermochemical reaction by contacting an active reagent and a basic aqueous solution, to thereby cause water from the basic aqueous solution to react with the active reagent and to produce hydrogen and a basic aqueous solution comprising an oxidised product. The method further comprises disposing the basic aqueous solution comprising the oxidised product in an electrochemical cell comprising an anode and a cathode, such that at least a portion of the cathode contacts the solution; and conducting an electrochemical reaction by applying a voltage across the anode and the cathode to produce hydrogen, oxygen and the active reagent. The active reagent comprises a metal or metal ion in a first oxidation state and the oxidised product comprises the metal or metal ion in a second oxidation state which is higher than the first oxidation state.
Solid oxide electrolysers (SOE) are a promising type of technology of hydrogen production with the potential to be a part of the sustainable future of the energy sector. Advantageous efficiency of these devices is coming from the combined use of the heat and electrical energy. The current research proposes to improve the electrical efficiency of solid oxide electrolysers by fabricating a metasurface upon the standard porous anode layer of the electrolysis cell. The study considers the tubular cell design with the thick metallic support and several types of meta-elements, including squared shapes, lines parallel to the air flow and a net-structured surface. Computational fluid dynamics (CFD) analysis is performed for the 1/16 sector model of the tubular cell in parallel flow conditions to evaluate current density characteristics of the considered metasurfaces. As a result of this study, the net-structured metasurface is found to increase the current density by 8.5 %. [Display omitted] •Tubular solid oxide electrolysis (SOE) cell investigated with the metallic support.•Introduced a metasurface-patterned anode structure for enhanced performance.•Simulations are performed for the 1/16th sector model of the short tubular cell.•Current density evaluated for four types of the porous anode metasurface.•Net-structure metasurface of the porous anode found to be the most efficient by 8.5 %.
High-temperature processes for hydrogen production unlock the potential for high energy efficiency combined with a relatively low environmental impact. However, structural integrity should be carefully considered. Solid oxide electrolysis cells (SOEC) employ a range of ceramic and metallic materials capable of withstanding high temperatures, ranging from 500 degrees C to 1000 degrees C, while facilitating active electrochemical reactions. The present structural analysis focuses on the challenge of anticipating the formation of debonding cracks at the interfaces of layers (assumed non-porous) within a single SOEC cell with a tubular design and a metal support. This study includes implementation of material properties for ceramic mixtures, model verification, analysis of deformation, stresses, crack formation using the cohesive zone model (CZM) - a method commonly used to simulate the process of crack initiation and propagation. In this pioneering research, several potential areas of debonding have been identified, with the primary concentration occurring around the fixed-end boundaries. Findings reveal a temperaturedependent curvature for the maximum expected total deformations, where a linear growth pattern turns into a random pattern, peaking at 750 degrees C. Up to eight deformation zones, which could potentially serve as crack initiation locations, are identified near the fixed boundaries, and up to four zones are indicated by deformation contours for the main body of the tubular cell model. The study establishes and reports the evolution of these debonding zones through the high-temperature operating range.
The disclosure describes an apparatus for hydrogen production. The apparatus comprises (a) an electrochemical cell comprising an anode and a cathode, (b) a battery comprising a positive current collector and an electrolyte compartment configured to hold an electrolyte therein and (c) a thermochemical reactor. The electrochemical cell is configured to receive a basic aqueous solution comprising zinc hydroxide and/or zincate, such that at least a portion of the cathode contacts the solution comprising the zinc hydroxide and/or zincate when it is disposed in the electrochemical cell. The apparatus further comprises a battery comprising a positive current collector and an electrolyte compartment configured to hold an electrolyte therein. The battery is configured to receive a gas comprising oxygen on the positive current collector and to receive at least a portion of the zinc produced in the electrochemical cell, such that the zinc forms an anode of the battery. The apparatus further comprises a thermochemical reactor. The thermochemical cell comprises a reaction chamber configured to receive at least a portion of the zinc metal produced in the electrochemical cell. The thermochemical cell is configured to enable the zinc metal to contact water in the reaction chamber and thereby cause a thermochemical reaction to proceed and thereby produce zinc oxide and a gas stream comprising hydrogen.
In this study, a comprehensive process for production of an environmentally friendly octane booster (acetophenone) from lignin is presented, along with a detailed techno-economic analysis. Recognizing that much of the prior research on octane boosters has been confined to experimental lab-level investigations, this study develops comprehensive process design to unravel the intricacies of large-scale acetophenone production. The acetophenone production process involves catalytic hydrogenolysis, which also yields phenol as a valuable side product. Based on the process flow diagram, mass and energy balances were developed, revealing significantly improved yields and purity of acetophenone compared to industry standards, reaching 0.74 kg acetophenone per kg of lignin and 99 wt%. In the techno-economic analysis, calculations involving fixed capital investment (FCI), operating costs, and working capital were conducted based on a feed of 100 kg/h of dry lignin. The results indicate FCI at 2.72 million USD, operating costs at 1.09 million USD per year, and working capital at 0.57 million USD. Assuming a 20-year operational lifespan, the payback period is estimated at 6.09 years, as depicted by the cumulative cash flow diagram. Moreover, techno-economic analysis demonstrates a net present value (NPV) of 3.24 million USD at a 10% discount rate, an internal rate of return (IRR) of 22.73%, and a return on investment (ROI) of 34.39%. These positive outcomes underscore the robust profitability of the proposed acetophenone production plant derived from lignin. Additionally, a sensitivity analysis on the IRR indicates that increasing the production capacity could further enhance profitability, reaffirming the feasibility of the plant's operation. Crucially, this study highlights the potential for sustainable and economically viable production of acetophenone, offering an environmentally friendly alternative to toxic octane boosters and advancing the development of sustainable fuel additives.
Electrolytic manganese metal (EMM) produced from recyclable resources has recently gained increasing attention due to the scarcity of high-quality manganese natural resources and its broad range of applications. This review has summarised recent progress in manganese recovery techniques, including pyrometallurgy and hydrometallurgy. It has also critically assessed the processes and mechanisms involved in manganese electrodeposition for the Mn chloride- and Mn sulphate-based systems, with a major focus on electrode reactions and Mn nucleation growth. The key optimisation factors influencing manganese electrodeposition, such as electrolytes, power consumption, additives, cell structures, and electrode materials, were analysed, with particular attention to their impact on current efficiency, specific energy consumption, and product quality. The recent research directions were also highlighted to address practical challenges and enhance the sustainability of the EMM process, which mainly includes improving the ecological outcomes and reducing both the operating and investment costs. Promising strategies for the simultaneous production of EMM and electrolytic manganese dioxide (EMD) were also identified, which mainly comprised applying membrane technology, electrodeposition from ionic liquids, recycling and reusing waste materials, and exploring hybrid techniques. The results of this study showed that the prospective optimisation approaches for EMM are mainly driven by the need to enhance efficiency, reduce costs, and improve product quality through sustainable technological advancements. This review can be used as a comprehensive guide for manganese electrodeposition approaches for both practical and scientific research communities.
Hydrogen fuel cells and hydrogen production stand at the forefront of efforts to achieve net-zero emissions. Among these technologies, solid oxide fuel cells (SOFCs) and electrolysers (SOEs) are distinguished as particularly promising for broad practical application, offering superior efficiency, robust stability, cost-effectiveness, and inherent safety. Lowering the operating temperature can significantly facilitate their commercialization by improving the stability and reducing the costs associated with electrodes and the fabrication process. Furthermore, reducing the operating temperature to 600 degrees C enables the utilization of heat sources from industrial processes, such as steel production or various combustion systems, effectively enhancing energy recycling efficiency. At low and intermediate temperatures, SOFCs and SOECs' performance heavily relies on electrolyte conductivity. Therefore, rationally improving electrolyte conductivity under a relatively low temperature plays an important role in facilitating the widespread application of SOFCs and SOECs on a large scale. Aimed at practical application, this work delivers an extensive review of cutting-edge modification strategies intended to enhance the conductivity of several promising electrolytes and outlines the characterisation methods utilised to assess their properties. It further investigates novel synthesis techniques aimed at reducing the sintering temperature. Moreover, this paper provides a comprehensive analysis and evaluation of electrolytes tailored for large-scale implementation in SOFCs and SOECs.
The necessity for high operational temperatures presents a considerable obstacle to the commercial viability of solid oxide fuel cells (SOFCs). The introduction of active co-dopant ions to polycrystalline solid structures can directly impact the physiochemical and electrical properties of the resulting composites including crystallite size, lattice parameters, ionic and electronic conductivity, sinterability, and mechanical strength. This study proposes cobalt-iron-substituted gadolinium-doped ceria (Co(x)Fe(1-x)GDC) as an innovative, nickel-free anode composite for developing ceramic fuel cells. A new co-precipitation technique using ammonium tartrate as the precipitant in a multi-cationic solution with Co2+, Gd3+, Fe3+, and Ce3+ ions was utilized. The physicochemical and morphological characteristics of the synthesized samples were systematically analysed using a comprehensive set of techniques, including DSC/TGA for a thermal analysis, XRD for a crystallographic analysis, SEM/EDX for a morphological and elemental analysis, FT-IR for a chemical bonding analysis, and Raman spectroscopy for a vibrational analysis. The morphological analysis, SEM, showed the formation of nanoparticles (
Thermochemical water splitting stands out as the most efficient techniques to produce hydrogen through electrolysis at a high temperature, relying on a series of chemical reactions within a loop. However, achieving a durable thermochemical cycle system poses a significant challenge, particularly in manufacturing suitable coating materials for reaction vessels and pipes capable of enduring highly corrosive conditions created by high-temperature molten salts. The review summarizes thermally sprayed coatings (deposited on structural materials) that can withstand thermochemical cycle corrosive environments, geared towards nuclear thermochemical copper-chlorine (Cu-Cl) cycles. An assessment was conducted to explore material composition and selection (structure-property relations), single and multi-layer coating manufacturing, as well as corrosion environment and testing methods. The aim was to identify the critical areas for research and development in utilizing the feedstock materials and thermal spray coating techniques for applications in molten salt thermochemical applications, as well as use lessons learnt from other application areas (e.g., nuclear reaction vessels, boilers, waste incinerators, and aero engine gas-turbine) where other types of molten salt and temperature are expected. Assessment indicated that very limited sets of coating-substrate system with metallic interlayer is likely to survive high temperature corrosive environment for extended period of testing. However, within the known means and methods, as well as application of advanced thermal spray manufacturing processes could be a way forward to have sustainable coating-substrate assembly with extended lifetime. Spraying multi-layered coating (nano-structured or micro-structured powder materials) along with the application of modern suspension or solution based thermal spray techniques are considered to result in dense microstructures with improved resistance to high temperature thermochemical environment.
The scientific and industrial communities worldwide have recently achieved impressive technical advances in developing innovative electrocatalysts and electrolysers for water and seawater splitting. The viability of water electrolysis for commercial applications, however, remains elusive, and the key barriers are durability, cost, performance, materials, manufacturing, and system simplicity, especially with regard to running on practical water sources like seawater. This article, therefore, primarily aims to provide a concise overview of the most recent disruptive water-splitting technologies and materials that could reshape the future of green hydrogen production. Starting from water electrolysis fundamentals, the recent advances in developing durable and efficient electrocatalysts for modern types of electrolysers, such as decoupled electrolysers, seawater electrolysers, and unconventional hybrid electrolysers, have been represented and precisely annotated in this report. Outlining the most recent advances in water and seawater splitting, the article can help as a quick guide in identifying the gap in knowledge for modern water electrolysers while pointing out recent solutions for cost-effective and efficient hydrogen production to meet zero-carbon targets in the short to near term.
The Polymer Electrolyte Membrane Water Electrolyser (PEMWE) has gained significant interest among various electrolysis methods due to its ability to produce highly purified, compressed hydrogen. The spatial configuration of bipolar plates and their flow channel patterns play a critical role in the efficiency and longevity of the PEM water electrolyser. Optimally designed flow channels ensure uniform pressure and velocity distribution across the stack, enabling high-pressure operation and facilitating high current densities. This study uses flow channel geometry inspired by authentic vine leaf patterns found in biomass, based on various plant leaves, including Soybean, Victoria Amazonica, Water Lily, Nelumbo Nucifera, Kiwi, and Acalypha Hispida leaves, as a novel channel pattern to design a PEM bipolar plate with a circular cross-section area of 13.85 cm2. The proposed bipolar design is further analysed with COMSOL Multiphysics to integrate the conservation of mass and momentum, molecular diffusion (Maxwell-Stefan), charge transfer equations, and other fabrication factors into a cohesive single-domain model. The simulation results showed that the novel designs have the most uniform velocity profile, lower pressure drop, superior pressure distribution, and heightened mixture homogeneity compared to the traditional serpentine models.
Gadolinium-doped ceria (GDC) is a promising electrolyte material for developing solid oxide fuel cells (SOFCs) because it offers a higher ionic conductivity at the intermediate operating temperature. In this work, nanocrystalline GDC (Ce1-xGdxO2-x/2, where x = 0.1 and 0.2) powders were synthesised through a novel co-precipitation synthesis method (benzoate route) using ammonium benzoate as a low-cost precipitant. The effect of the synthesis route and processing variables (calcination temperatures and time) on the microstructural and electrical properties of the resulting GDC powder was studied systematically. Multiple GDC electrolyte pellets were fabricated by pressing the GDC powders, followed by sintering the samples at 1100 °C for 6 h. The ionic and electronic conductivity of the GDC pellets were measured in air using EIS at different temperatures (450–750 °C). Huggins' model was used to determine the ionic and electronic conductivity of the GDC pellets. The fabricated electrolyte pellets showed a high relative density of 98.31and 99.02 % for the pre-calcined non-washed and pre-calcined washed powders, respectively, with a crystal size lower than 12 nm. Among all samples, the GDC electrolyte pellet fabricated using the pre-calcined washed powder exhibited the highest ionic conductivity of 3.63E-01 S cm−1 at 750 °C and activation energy of 0.52 eV with an average crystal size of 7–8 nm. The results of this study help to understand and design more efficient ceramic fuel cells with controlled microstructure and compositions at a lower cost.
Biogas is a renewable, as well as abundant, fuel source which can be utilised in the production of heat and electricity as an alternative to fossil fuels. Biogas can additionally be upgraded via the dry reforming reactions into high value syngas. Nickel-based catalysts are well studied for this purpose but have shown little resilience to deactivation caused by carbon deposition. The use of bi-metallic formulations, as well as the introduction of promoters, are hence required to improve catalytic performance. In this study, the effect of varying compositions of model biogas (CH4/CO2 mixtures) on a promising multicomponent Ni-Sn/CeO2-Al2O3 catalyst was investigated. For intermediate temperatures (650 °C), the catalyst displayed good levels of conversions in a surrogate sewage biogas (CH4/CO2 molar ratio of 1.5). Little deactivation was observed over a 20 h stability run, and greater coke resistance was achieved, related to a reference catalyst. Hence, this research confirms that biogas can suitably be used to generate H2-rich syngas at intermediate temperatures provided a suitable catalyst is employed in the reaction.
We have demonstrated a new strategy for enhancing solar evaporation by using floating light-absorbing materials. Floating Fe3O4/C magnetic particles with an average size of 500 nm were synthesized by carbonization of poly(furfuryl alcohol) (PFA) incorporated with Fe3O4 nanoparticles. The Fe3O4/C particles had a BET surface area of 429 m2 g−1, and a density of 1.44 g cm−3. Because of their hydrophobicity and a bulk packing density of 0.53 g cm−3, Fe3O4/C particles were floatable on water. Our results indicated that these Fe3O4/C particles enhanced the water evaporation rate by as much as a factor of 2.3 in the solar evaporation of 3.5% salt water. In addition, Fe3O4/C particles were easily recycled using a magnet, and stable after being recycled three times. Our work provides a low-cost and highly effective way for accelerating solar evaporation for industrial applications such as solar desalination, salt production, brine management and wastewater treatment.
This study is focused on nanocrystalline cellulose (NCC) flakes for methylene blue (MB) removal via adsorption. NCC flakes exhibit a high adsorption capacity (188.7 mg/g fixed at 0.7 g/L adsorbent dosage, 25 °C and pH 6) compared to other nanomaterials, such as carbon nanotube and other cellulosic materials, such as coffee husks. Unlike NCC powder, it was observed that NCC flakes can be easily separated from wastewater containing MB. Further adsorption studies were conducted on NCC flakes, and it was found that 0.7 g/L was the optimum adsorbent dosage, which fitted well with the Langmuir Isotherm. The mean free energy value from Dubinin-Radushkevich isotherm was less than 8 kJ/mol. ΔGo values at different temperatures were within the -20 kJ/mol to 0 kJ/mol range. In conclusion, NCC flakes is a promising and practical ‘green’ nanomaterial that can be further developed for industrial applications.
Transition metal oxides have various interesting properties, especially nanostructures of the Copper (II) Oxides (CuO) have special magnetic properties and larger surface area which enhance the applications of the CuO in various fields. In this study, CuO nanoparticles supported on Halloysite Nanotubes (HNTs) via an in-situ glycine nitrate process was successfully synthesized by templating on chitosan. Effects of calcination time and temperature are fully elaborated by detail charactrizations including, FESEM, FTIR, TGA, EDX, BET and Raman Spectroscopy. The best calcination condition was found to be at 600 C for 5 h of calcination duration. Charactrizations confirmed the presence of both HNT and CuO within the particles confirming that the in-situ synthesis of metal-oxides by supporting them on HNTs is very much feasible.
Pure cubic phase yttrium oxide or yttria (Y2O3) nanoparticles were successfully synthesised via the co-precipitation method in a distillate pack, followed by calcination of the precursor, yttrium oxalate (Y2(C2O4)3) in a furnace. The co-precipitation reaction temperature was varied between room temperature and 100 °C for various reaction durations ranging between 0.5 and 3 h. The as-synthesised precursor was characterised using a thermogravimetric analyser (TGA) and Fourier transform infrared spectrometer (FTIR). The Y2O3 nanoparticles obtained from the calcination of the precursor at various calcination conditions (temperature ranged from 500 to 800 °C for 2–8 h) were characterised using a field emission scanning electron microscope (FESEM), a transmission electron microscope (TEM), X-ray diffraction (XRD), FTIR, a Raman spectrometer, and Brunauer–Emmett–Teller analyser (BET). It was concluded from these characterisations that the optimum processing parameters for pure Y2O3 nanoparticles are co-precipitation reaction at 40 °C for 1 h, followed by calcination at 650 °C for 4 h. This method yielded semispherical Y2O3 nanoparticles with crystallite size ranging between 7 and 21 nm and a large specific surface area of 7.40 m2/g.
A conveyor-belt dryer for picrite has been modeled mathematically in this work. The necessary parameters for the system of equations were obtained from regression analysis of thin-layer drying data. The convective drying experiments were carried out at temperatures of 40, 60, 80, and 100°C and air velocities of 0.5 and 1.5 m/sec. To analyze the drying behavior, the drying curves were fitted to different semi-theoretical drying kinetics models such as those of Lewis, Page, Henderson and Pabis, Wang and Singh, and the decay models. The decay function (for second order reactions) gives better results and describes the thin layer drying curves quite well. The effective diffusivity was also determined from the integrated Fick's second law equation and correlated with temperature using an Arrhenius-type model. External heat and mass transfer coefficients were refitted to the empirical correlation using dimensionless numbers (J h , J D = m · Re n ) and their new coefficients were optimized as a function of temperature. The internal mass transfer coefficient was also correlated as a function of moisture content, air temperature, and velocity.
This book summarizes recent research and development in the field of nanostructured ceramics and their composites.
Steam electrolysis is one of the most efficient approaches for producing green hydrogen. The method is based on the application of solid oxide electrolysis cells (SOECs) fabricated by functional ceramic composites for water splitting at high temperatures. Gadolinium doped ceria (GDC) is a promising electrolyte material for the fabrication of SOECs. However, the effective sintering temperature for GDC composite is usually above 1250 °C, which makes it impossible to use conventional supporting materials like ferritic steels for stack fabrication. In this work, for the first time, we have developed a lithium bismuth-copper co-doped GDC composite capable of sintering at ~750 °C. The physicochemical and electrochemical characteristics of the co-doped GDC electrolyte were systematically analysed using thermogravimetric analysis (TG/DTA), Raman spectroscopy, SEM/EDX, XRD, EIS, XPS and dilatometry analysis. The fabricated electrolyte pellets sintered at 750 °C for 6 hours in an inert atmosphere (argon) showed high densification, obtaining 96.70 % relative density. Also, the electrical conductivity obtained for the synthesised composite Ce0.712Gd0.178Li0.05Bi0.05Cu0.01O1.801 (sintered at 950 °C 6h) was 29.6 mS.cm-1 at 750 °C with activation energy as low as 0.13 eV. The result of this study helps to understand better the properties of co-doped electrolyte materials for the fabrication of more efficient steam electrolysers for environmentally-friendly hydrogen generation.
Hydrogen is known to be the carbon-neutral alternative energy carrier with the highest energy density. Currently, more than 95% of hydrogen production technologies rely on fossil fuels, resulting in greenhouse gas emissions. Water electrolysis is one of the most widely used technologies for hydrogen generation. Nuclear power, a renewable energy source, can provide the heat needed for the process of steam electrolysis for clean hydrogen production. This review paper analyses the recent progress in hydrogen generation via high-temperature steam electrolysis through solid oxide electrolysis cells using nuclear thermal energy. Protons and oxygen-ions conducting solid oxide electrolysis processes are discussed in this paper. The scope of this review report covers a broad range, including the recent advances in material development for each component (i.e., hydrogen electrode, oxygen electrode, electrolyte, interconnect, and sealant), degradation mechanisms, and countermeasures to mitigate them.
The 15 state-of-the-art review chapters contained in this book cover the recent advancements in the area of waste water, as well as the prospects about the future research and development of smart materials for the waste water applications ...
Nanocomposite powders of gadolinium-doped ceria (GDC, Ce0.8Gd0.2O1.9) were synthesized via thermal treatment of the gel formed by contacting ionic solutions of sodium alginate as the jelling template and metal (gadolinium/cerium) nitrates as the starting material. The influence of calcination temperature and sodium alginate loading fraction on the properties of the synthesized GDC nanocomposite powders was investigated. Characterization was performed by energy dispersive X-ray spectroscopy, powder X-ray diffraction, thermogravimetric analysis, Field Emission Scanning Electron Microscopy, Fourier transformed infrared spectroscopy and nitrogen adsorption/desorption analysis. It was observed that the particle size and the surface area of the produced GDC nanocomposite powders are dominantly controlled by the calcination temperature, while the effect of sodium alginate loading fraction is limited by the range of the calcination temperature. In this study, the smallest mesoporous GDC nanocomposite powder with cubic fluorite structure (8 nm crystallite size and 3.05 ± 0.005 m2/g surface area) was synthesized using 2 wt. % of sodium alginate at a calcination temperature of 550 °C (for 4 h).The results of this study could help to perceive the influence of the basic processing variables on the particle size and the other physiochemical properties of GDC nanocomposite powders produced by the ionic-gelation method.
The catalytic performance of a series of bimetallic Ni-Co/CeO2-Al2O3 catalysts were evaluated within the dry reforming of methane (DRM) reaction, commonly used for upgrading biogas. The study focused on the variation of CeO2 weight loadings between 0, 10, 20 and 30%. It was found that the addition of CeO2 promoted CH4 and CO2 conversion across the temperature range and increased H2/CO ratio for the “low temperature” DRM. X-Ray Diffraction (XRD), H2-Temperature Programmed Reduction (H2-TPR) and X-Ray Photoelectron Spectroscopy (XPS) analysis revealed the formation of Ce4+ during activation of the 30% sample, resulted in excessive carbon deposition during reaction. The lowest CeO2 weight loadings exhibited softer carbon formation and limited increased chemical stability during reaction at the expense of activity. Of the tested weight loadings, 20 wt% CeO2 exhibited the best balance of catalytic activity, chemical stability and deactivation resistance in the DRM reaction. Hence this catalyst can be considered a promising system for syngas production from biogas at relatively low temperatures evidencing the pivotal role of catalysts design to develop economically viable processes for bioresources valorisation.
In this study, nanosized nickel oxide (NiO) and nickel (Ni) powders were synthesised via glycine-nitrate (GN) combustion process, assisted by nanocrystalline cellulose (NCC) as a template. Despite the unique morphology of NCC, it has yet to be applied as a sacrificial bio-template for GN combustion process. In addition, NiO and Ni nanoparticles were obtained at relatively low temperatures in this study, whereby the calcination temperatures were varied from 400 °C to 600 °C, with calcination durations of 2, 4, and 6 h. The morphological analysis of the resulting products were conducted using FESEM, which showed uniformly dispersed NiO and Ni particles with average crystallite size of 25 nm and 27 nm, respectively. These results were confirmed using X-ray diffraction (XRD) technique. The Raman and Fourier transform infrared (FTIR) spectra revealed that the molecular fingerprints of the samples were in agreement with each other. Further analyses revealed that samples calcined at 600 °C for 4 h showed the lowest particle size for pure NiO, whereas the lowest particle size for pure Ni was obtained at 400 °C for 4 h. The TGA results were also consistent with the XRD analysis, whereby pure Ni was initially formed and upon heating, had gradually converted into NiO.
One important factor limiting the development of solid oxide fuel cell is its high operational temperature (700–750 °C), significantly hindering its commercialization. Here, for the first time, it is reported that nanocrystalline Co1-x-Znx-Gd0.1Ce0.9O1.95 (x = 0.50, and 0.65) anode powders can provide a practical solution toward Ni-free low temperature SOFCs (LT-SOFCs; 450–550 °C) by illustrating strikingly high redox capabilities at temperatures below 400 °C. An anode-electrolyte bilayer with tailored electrical conductivity is fabricated by co-sintering a Gd0.1Ce0.9O1.95 disc (as support) and the synthesized Co1-x-Znx-Gd0.1Ce0.9O1.95 anode powder. During co-sintering, the tunable internal Zn supply from the anode composite to the electrolyte support significantly decreases the densification temperature of the GDC electrolyte support (down to 1100–1200 °C), while promoting the cell efficiency (∼ 7%) by drastically reducing the electron conductivity through the GDC electrolyte layer (open circuit voltage ∼ 0.91 V at 650 °C). The electrolyte layer shows excellent compatibility with the anode electrode, leading to possible long term thermal cyclability to room temperature. Fuel cell characterizations over a broad range of operating conditions estimate activation energies of 0.49, 0.48, and 0.63 eV for the three identified anodic processes. Zinc can increase the cell power-density by about five times compared to Co-based anode composites.
Zirconia-based composites with high thermochemical stability and electrochemical activity are the most promising solid electrolytes for manufacturing solid oxide fuel cells (SOFCs). In the present work, nanocrystalline composite powders of gadolinium-doped zirconia (GDZ: Gd2xZr2(1−x)O4−x) with various doping fractions (0.01 ≤ x ≤ 0.16) were synthesized by the Pechini method and applied for the fabrication of several electrolyte pellets to evaluate their physicochemical properties, sinterability, and conductivity. The X-ray diffraction (XRD) patterns and the thermogravimetry/differential thermal analysis (TGA/DTA) of the synthesized powders confirmed the successful formation of nanocrystalline GDZ in the tetragonal phase with complete substitution of gadolinium phase into the zirconia (ZrO2) lattice. The synthesized gadolinium zirconate powders were then shaped into pellet forms using the tape casting method, followed by sintering at 1300 °C (for 2.5 h). The microstructural analysis of the electrolyte pellets showed suitable grain boundary welding at the surface with an acceptable grain growth at the bulk of the T-phase GDZ samples. The impedance measurements indicated that the T-phase GDZ-8 could provide a comparably higher ionic conductivity (with 7.23 × 10−2 S/cm in the air at 800 °C) than the other dopant fractions. The results of this work can help better understand the characteristics and electrochemical performance of the T-phase gadolinium zirconate as a potential electrolyte for the fabrication of SOFCs.
Recently, there have been considerable interests to immobilize photocatalyst in alginate beads for removing pollutants from water sources. However, the feasibility of using alginate beads in industry largely depends on its long-term stability during operation. This study investigated the physicochemical stability of alginate/titanium dioxide beads (Alg/TiO2) when exposed to UV irradiation in aqueous environment. The degradation of Alg/TiO2 beads was evident because the diameter and mass of the beads was reduced by 12% and 40%, respectively, after 120 h of irradiation. A substantial amount of TiO2 was leached into the external medium. Consequently, the removal efficiency of model cationic dye was found to reduce after every process cycle. Morphological analysis showed the formation of cavities on the surface of the Alg/TiO2 beads. Interestingly, the blank alginate beads degraded more rapidly than the Alg/TiO2 beads, confirming the UV shielding effect of TiO2. Nevertheless, this study reveals the need to improve the UV stability of alginate-based beads before they can be considered for practical application. © 2017 Wiley Periodicals, Inc. J. Appl. Polym. Sci. 2017, 133, 45002.
This paper deals with the development and potential application of a novel mixed ionic-electronic conductive anode composite comprised of copper and iron oxide based on gadolinium-doped ceria (CuO–Fe2O3/GDC) for solid-oxide fuel cell (SOFC). Synthesis of the nanocrystalline CuO–Fe2O3/GDC powders was carried out using a novel co-precipitation method based on ammonium tartrate as the precipitant in a mixed-cationic solution composed of Cu2+, Fe3+, Gd3+, and Ce3+. Thermal decomposition of the resultant precipitate after drying (at 55 °C) was investigated in a wide range of temperature (25–900 °C) using simultaneous DSC/TGA technique in air. The DSC/TGA results suggested the optimal calcination temperature of 500 °C for obtaining the nanocrystalline anode composite from the resultant precipitate. The synthesised CuO–Fe2O3/GDC samples were further characterised using XRD, dilatometry, FESEM, and EDX. Several single cells of SOFCs were fabricated in the anode-supported geometry using the synthesised CuO–Fe2O3/GDC composite as the anode, GDC/CuO composite as the electrolyte, and LSCF/GDC composite as the cathode layer. The fabricated cells were analysed using FESEM imaging and EIS analysis, where an equivalent circuit containing five R-CPE terms was used to interpret the EIS data. The module fitted well the impedance data and allowed for a detailed deconvolution of the total impedance spectra. The catalytic activity and uniformity of the synthesised nanocomposites was further evaluated using TPR analysis, demonstrating excellent activity at temperatures as low as 200 °C.
The impacts of co-precipitation reaction temperature and duration, as well as calcination temperature and duration, on the particle morphology and properties of gadolinia (Gd2O3) nanopowders were investigated. Thermogravimetric curve of thermally treated gadolinium oxalate (Gd2(C2O4)3) showed that pure stable cubic phase Gd2O3 nanopowders could be obtained by calcining at 640 °C and higher. This finding was also supported by results obtained from Fourier Transform Infrared Spectrometry (FTIR) and Raman spectrometry. This study also shows that uniform spherules of Gd2O3 nanopowders could be obtained under controlled synthesis conditions. However, with an increase in both the co-precipitation reaction temperature and duration, the extent of agglomeration of Gd2O3 nanopowders increased, as observed under a Field Emission Scanning Electron Microscope (FESEM). The FESEM images and X-ray Diffraction (XRD) patterns also revealed accelerated grain growth and increased average crystallite size at high calcination temperatures and holding times. It was determined that the most favourable Gd2O3 particle morphology was achieved when Gd2(C2O4)3 was co-precipitated at 40 °C, then thermally degraded at 650 °C, for 1 h and 4 h, respectively. Estimated Scherrer's average crystallite size of the resulting Gd2O3 nanopowders was 16.54 nm, which was further affirmed with the transmission electron microscope (TEM) image, where crystallite sizes of 3–27.5 nm were observed in the Gd2O3 sample. This specimen also demonstrated a considerably large specific surface area of 9.16 m2/g, as measured using a Brunauer–Emmett–Teller (BET) analyser.
In this study, nanocrystalline nickel oxide gadolinium-doped ceria (NiO-GDC) powder was synthesized using an ionic sol-gel method. The effects of calcination time and temperature on the particle size and the physiochemical properties of nanocrystalline NiO-GDC are presented in this paper. Using this method, gel beads were formed by contacting sodium alginate solution as the gelling template and metal (gadolinium/cerium/Ni) nitrates as the precursor. The obtained nanocrystallites were characterized using Field Emission Scanning Electron Microscopy, powder X-ray diffraction, energy dispersive X-ray spectroscopy, thermo gravimetric analysis, nitrogen adsorption/desorption analysis, and Fourier transform infrared spectroscopy. It was observed that the increasing calcination temperature had affected both the particle size and the surface area of the NiO-GDC, whereas the increasing calcination time had only impacted the size of the particles. The smallest mesoporous nanocrystalline NiO-GDC powder (12.1225 ± 0.005 m2/g surface area), composed of cubic GDC (5.18 nm crystallite size) and cubic NiO (7.99 nm crystallite size) were synthesized at a calcination temperature of 500 °C for 2 hours. This study hopes to inspire more researches on the ionic-gelation method for synthesizing other metal nanostructures as well as other reaction parameters.
Solid oxide fuel cells (SOFCs) are amongst the most widely used renewable alternative energy systems with near-zero carbon emission, high efficiency, and environment-friendly features. However, the high operating temperature of SOFCs is still considered a major challenge due to several issues regarding the materials’ corrosion, unwanted reactions between layers, etc. Thus, low-temperature SOFCs (LT-SOFCs) have gained significant interest during the past decades. Despite the numerous advantages of LT-SOFCs, material selection for each layer is of great importance as the common materials have not shown a desirable performance so far. In addition to the selection of the materials, fabrication techniques have a great influence on the properties of the SOFCs. As SOFCs with thinner layers showed lower polarisation resistance, especially in the electrolyte layer, different thin-film fabrication methods have been employed, and their effect on the overall performance of SOFCs has been evaluated. In this review, we aim to discuss the past and recent progress on the materials and thin-film fabrication techniques used in LT-SOFCs.
This work reports the preparation of nanocrystalline Ni-Gd0.1Ce0.9O1.95 (NiO-GDC) anode powders using a novel single-step co-precipitation synthesis method (carboxylate route) based on ammonium tartrate as a low-cost green precipitant. The thermogravimetric analysis (TGA) of the synthesised powder showed the complete calcination/crystallisation of the resultant precipitates to take place at 500 °C. The prepared NiO-GDC powder was coated on a GDC electrolyte disc and co-sintered at 1300 °C. A mixture of La0.6Sr0.4Co0.2Fe0.8O3−δ and GDC was used as the cathode material and subsequently coated onto the anode-electrolyte bilayer, resulting in the fabrication of a NiO-GDC|GDC|La0.6Sr0.4Co0.2Fe0.8O3−δ-GDC cell. The crystallite size of both NiO and CeO2 phases were estimated using the X-ray powder diffraction (XRD) profiles and were calculated to be ~14 nm. Applied H2 temperature-programmed reduction (H2-TPR) analysis indicated a synergetic effect among different anode composites' constituents, where an intense interaction between the dispersed NiO nanocrystalline particles and the GDC crystallite phase had weakened the metal-oxygen bonds in the synthesised anode composites, resulting in a strikingly high catalytic activity at temperatures as low as 300 °C. The electrochemical impedance spectroscopy (EIS) and the electrochemical performance of the fabricated cells were measured over a broad range of operating temperatures (500–750 °C) and H2/Ar-ratios of the anode fuel (e.g. 100%–15%). Quantitative analysis from the EIS data and the application of the distribution of relaxation times (DRT) method allowed for the estimation of the activation energies of the anodic high and intermediate frequency processes that were 0.45 eV and 0.76 eV, respectively. This is the first report of a NiO-GDC synthesis, where a considerable improvement in activation energy is observed at the low-temperature region. Such low activation energies were later associated with the adsorption/desorption process of water molecules at the surface of NiO-GDC composite, indicating a high activity towards hydrogen oxidation.
Electrolyte powders with low sintering temperature and high-ionic conductivity can considerably facilitate the fabrication and performance of solid oxide fuel cells (SOFCs). Gadolinia-doped ceria (GDC) is a promising electrolyte for developing intermediate- and low-temperature (IT and LT) SOFCs. However, the conventional sintering temperature for GDC is usually above 1200 °C unless additives are used. In this work, a nanocrystalline powder of GDC, (10 mol% Gd dopant, Gd0.1Ce0.9O1.95) with low-sintering temperature has been synthesized using ammonium benzoate as a novel, environmentally friendly and cost-effective precursor/precipitant. The synthesized benzoate powders (termed washed- and non-washed samples) were calcined at a relatively low temperature of 500 °C for 6 h. Physicochemical characteristics were determined using thermal analysis (TG/DTA), Raman spectroscopy, FT-IR, SEM/EDX, XRD, nitrogen absorptiometry, and dilatometry. Dilatometry showed that the newly synthesized GDC samples (washed and non-washed routes) start to shrink at temperatures of 500 and 600 °C (respectively), reaching their maximum sintering rate at 650 and 750 °C. Sintering of pelletized electrolyte substrates at the sintering onset temperature for commercial GDC powder (950 °C) for 6 h, showed densification of washed- and non-washed samples, obtaining 97.48 and 98.43% respectively, relative to theoretical density. The electrochemical impedance spectroscopy (EIS) analysis for the electrolyte pellets sintered at 950 °C showed a total electrical conductivity of 3.83 × 10−2 and 5.90 × 10−2 S cm−1 (under air atmosphere at 750 °C) for washed- and non-washed samples, respectively. This is the first report of a GDC synthesis, where a considerable improvement in sinterability and electrical conductivity of the product GDC is observed at 950 °C without additives addition.
Co-precipitation method has been used for the synthesis of single crystalline Nickel (II) Oxide sub-micro rods. A two-step method was used to synthesise NiO sub-micro rods, in which the first step was the co-precipitation process Nickel (II) Nitrate with Ammonium Oxalate to form Nickel (II) Oxalate (NiC2O4), which is the precursor for the precipitates. The precipitate precursor then underwent the calcination process to form NiO sub-micro rods. Synthesized materials undergo Field Emission Scanning Electron Microscope (FESEM), particle size measurement via Zetasizer, elemental analysis via Energy-Dispersive X-ray Spectroscopy (EDX), Fourier Transform Infrared Spectroscopy (FT-IR) and Thermogravimetric Analysis (TGA). The morphology of NiO is found to have uniform rod- like crystals with mean z-diameter between 1600 nm to 2600 nm using Zetasizer.
n this study, zinc oxide (ZnO) was prepared via extrusion-dripping method through an ion exchange mediated process using sodium alginate. The samples were synthesized at 500 °C and 600 °C to study the effect of calcination temperature. The morphology, microstructure and optical activity of the calcined ZnO nanoparticles were analyzed by TGA, FESEM and XRD. It was found that ZnO nanoparticles synthesized at 600 °C was of higher purity with high crystallinity. To enhance the photocatalytic efficiency of zinc oxide, ZnO/NCC films were synthesized at varying ZnO loading fractions of 10 wt%, 15 wt%, 20 wt% and 25 wt% and were evaluated by photodegradation of Methylene blue dye and the highest dye percentage removal is found to be 96% which is obtained at ZnO loadings of 25 wt%. The usage of ion-exchange process has shown promising results in producing ZnO of desirable characteristics.
This paper has described the application of nickel-doped catalytic constituents based on gadolinium-doped ceria (GDC) for fabrication of the solid-oxide fuel cell (SOFC) anode layer integrated with an in-situ methane-reforming layer (MRL). Nanocrystalline powders of Ni1-xCo3xO1+3x/GDC and Ni1-xCuxO/GDC with various compositions (x = 0.3, 0.5, 0.7) were synthesised using an ultrasound-assisted method followed by a thermal treatment to be applied for fabrication of the integrated MRL and the SOFC anode layer, respectively. Thermogravimetric analysis showed that the synthesized powders should be optimally calcined at 700 °C to exhibit improved crystallinity and catalytic activity. The morphological analysis showed the formation of nanocrystalline powders with particle size ranging from 4-86 nm that was confirmed by the crystal size analysis using XRD results. The elemental analysis by EDX indicated a successful distribution of the constituent ceramic and bimetallic phases after the addition of a sonication stage. The results of FT-IR and Raman spectroscopy confirmed lack of solvents residual after calcination that was in agreement with residual moisture content values obtained from TGA data. The fabricated anode-MRL bilayers had an adequate porosity (36.7%) and shrinkage (33.5%) after adding carbon particles as a pore former (at a loading fraction of 5.9 wt.%). The catalytic performance measurements of the MRL showed a methane conversion of 13% at maximum activity with a weight hour space velocity (WHSV) of 60 L/gh that was mainly due to carbon deposition in the reaction condition.
This is an extensive review on the application of thermally sprayed coatings with functional properties for electrolysers. Such coatings are critical and vital constituents (as catalysts (anode/cathode), solid electrolyte, and transport layer, including corrosion-prone parts such as bipolar plates) of the water splitting electrolysis process for hydrogen production. Thermal spray coatings have the advantage of providing thick and functional coatings from a range of engineering materials. The associated coating processes provide good control of coating thickness, morphology, microstructure, pore size and porosity, and residual strain in the coatings through selection of suitable process parameters for any coating material of interest. This review consolidates scarce literature on thermally sprayed components which are critical and vital constituents (e. g., catalysts (anode/cathode), solid electrolyte, and transport layer, including corrosion-prone parts such as bipolar plates) of the water splitting electrolysis process for hydrogen production. The research shows that there is a gap in thermally sprayed feedstock material selection strategy as well as in addressing modelling needs that can be crucial to advancing applications exploiting their catalytic and corrosion-resistant properties to split water for hydrogen production. Due to readily scalable production enabled by thermal spray techniques, this manufacturing route bears potential to dominate the sustainable electrolyser technologies in the future. While the well-established thermal spray coating variants may have certain limitations in the manner they are currently practiced, deployment of both conventional and novel thermal spray approaches (suspension, solution, hybrid) is clearly promising for targeted development of electrolysers.
This review paper presents state-of-the-art electrolytic-based hydrogen production technologies capable of helping to achieve the “net-zero” targets. It covers the recent advances in electrochemical water-splitting technologies, considering their maturity, durability, and operational aspects related to their near-term deployment. This paper aims to critically assess electrochemical technologies compatible with renewables, nuclear, or other clean energy sources with a high potential to be applied for green hydrogen production at scale. It also discusses the techno-economic aspects as well as the technological readiness of the potential carbon-free hydrogen production routes based on electrochemical approaches. With a comprehensive survey of the recent literature and extensive insight into current developments, the issues associated with deploying the electrolytic water splitting technologies are discussed, along with a review of their market readiness level to play a potential role in the transition journey from fossil fuel-based-economy into hydrogen-driven energy infrastructure. In addition, the paper provides insight into the legal strategies and the governmental incentives required to reach the so-called “net-zero” emission plans globally to enable green hydrogen for deep decarbonization of the industrial, transportation, and residential sectors. Near-term projects to deploy large-scale clean hydrogen production announced globally are also listed with their expected contribution toward the zero-emission targets. The result of this review shows that wind and solar photovoltaic energies, as the two most preferred renewable sources, can be used to drive Proton Exchange Membrane (PEM) and Alkaline Electrolysers (AE) at a cost range of USD 2 - 3 /kg of H2. This figure is expected to decrease by more than 40% until 2030 if these electrolyzers can be deployed at a large scale.
In this study, Ni-GDC Nano-powder was synthesized via ion-exchange technique using sodium alginate as the templating material. Nanoparticles were obtained by controlling the calcination temperature. FE-SEM showed that the particle size of the grain decreased with the increase in the calcination temperature. Furthermore, pure NiO-GDC structure was obtained at the calcination temperature of 500 C with no secondary phase present which is evident through the compositional characterization performed including XRD, FTIR and TGA analysis. The usage of ion-exchange sol gel technique has shown promising results to overcome high polarization observed at low operating temperature.
We have recently developed a new drying-free casting method for shape forming of ceramics, in which a polymerizable solvent such as furfuryl alcohol (FA) is used to disperse the ceramic powders, and then polymerized into a poly (furfuryl alcohol) (PFA) binder during the casting process. Compared with conventional casting processes, this method offers more flexibility in controlling the microstructure of ceramics and eliminates defects that are likely to arise from the drying step. Controlling the rheological behaviour of ceramic slurries is an important step in the casting process to achieve improved microstructural properties. In this study, the viscosity of slurries comprising NiO/YSZ (yttria stabilized zirconia) powders and FA as solvent was investigated over a wide range of shear rates (1 s− 1–1000 s− 1) and at different volumetric solid concentrations (from 20% to 70%), while the effects of dispersant were quantified by adding different amounts of PVP (polyvinyl pyrrolidone) between 1 wt.% and 4 wt.%. The minimum viscosity of NiO/YSZ/FA slurries could be achieved with 2 wt.% dispersant. The experimental data relating the changes in viscosity to the volumetric solid concentration were modeled using different viscosity models, with Liu's equation showing the best fit for NiO/YSZ/FA slurries with and without dispersant. The slurries showed a highly pseudoplastic behaviour without dispersant, while adding PVP as dispersant effectively modified the rheological behaviour toward Newtonian fluids.
The geometrical diversion of combustible gas molecules notably affects their self-ignition in high-pressure tubes. This study investigates the propagation of shock waves and flame induced by a sudden pressure release of hydrogen in various Y-shaped tubes. The impact of the initial burst pressure, downstream tube length, and bifurcation angle (60°, 120°) were analyzed by recording the pressure signals, photoelectric curves, and jet fire evolution. The results showed that the gas diversion caused by the Y-shaped structure significantly reduces the maximum overpressure of the hydrogen jet, the intensity, and the velocity of the leading shock wave. Also, it was indicated that increasing the Y-shaped tube's length downstream of the bifurcation point could enhance the strength of leading and reflected shock waves after the Y-bifurcation, making self-ignition more likely to happen. Applying a 60°-bifurcation angle could create stronger leading and reflected shock waves during the propagation downstream of the bifurcation point, while a 120°-bifurcation angle could make a more substantial reflected shock wave propagating upstream. It leads to the re-ignition downstream of the bifurcation in the 60°-bifurcation tube after the flame quenching and stronger far-field jet fire outside the tube. •The impact of geometrical diversion of pressurized hydrogen was investigated.•The influence of tube length and bifurcation angle were analyzed.•The flame quenching and re-ignition were explored.•The evolution of double far-field jet fire was recorded.
This review summarizes the current status, operating principles, and recent advances in high-temperature polymer electrolyte membranes (HT-PEMs), with a particular focus on the recent developments, technical challenges, and commercial prospects of the HT-PEM fuel cells. A detailed review of the most recent research activities has been covered by this work, with a major focus on the state-of-the-art concepts describing the proton conductivity and degradation mechanisms of HT-PEMs. In addition, the fuel cell performance and the lifetime of HT-PEM fuel cells as a function of operating conditions have been discussed. In addition, the review highlights the important outcomes found in the recent literature about the HT-PEM fuel cell. The main objectives of this review paper are as follows: (1) the latest development of the HT-PEMs, primarily based on polybenzimidazole membranes and (2) the latest development of the fuel cell performance and the lifetime of the HT-PEMs.
The disclosure relates to an electrolysis cell for producing hydrogen . The cell comprises an electrolyte compartment and an electrolyte disposed therein . The electrolyte com prises an aqueous alkaline solution comprising a transition metal ion or p block metal ion . The cell further comprises first and second spaced apart electrodes at least partially disposed in the electrolyte .
The influence of fabrication pressure and other ceramic processing variables, including volumetric loading fraction and the particle size ratio of pore-forming agents, on the porosity of fabricated ceramic anodes, was investigated using an integrated experimental approach with mathematical modeling to differentiate the impacts of each parameter. Despite historic observation of the properties of ceramic bodies, to date, there is a lack of available models to accurately interpret the ceramic properties as a function of the processing variables. Herein, we focus on the open porosity of the solid oxide fuel cell anode prepared from NiO/YSZ (nickel oxide/yttria stabilized zirconia) as the ceramic powder and using CMS (carbon microspheres) as a pore-forming agent. A range of pore-former volumetric blend ratios (4.4%–44.6%) and different particle size ratios between NiO/YSZ and CMS (11.27, 4.29, and 0.26) were used, whereas the influence of the applied uni-axial fabrication pressure on the open porosity of sintered anode was studied in a range of atmospheric pressure up to 40 MPa. A good agreement was observed between the proposed model and the experimental data, implying that the approach could be used to determine the significant processing parameters to fabricate ceramics with desired porosity. The model could also be used to interpret the physical basis of pore formation when using a pore-forming agent in a fabricated porous ceramic body.
Solid oxide fuel cells (SOFCs) have been considered as promising candidates to tackle the need for sustainable and efficient energy conversion devices. However, the current operating temperature of SOFCs poses critical challenges relating to the costs of fabrication and materials selection. To overcome these issues, many attempts have been made by the SOFC research and manufacturing communities for lowering the operating temperature to intermediate ranges (600–800 °C) and even lower temperatures (below 600 °C). Despite the interesting success and technical advantages obtained with the low-temperature SOFC, on the other hand, the cell operation at low temperature could noticeably increase the electrolyte ohmic loss and the polarization losses of the electrode that cause a decrease in the overall cell performance and energy conversion efficiency. In addition, the electrolyte ionic conductivity exponentially decreases with a decrease in operating temperature based on the Arrhenius conduction equation for semiconductors. To address these challenges, a variety of materials and fabrication methods have been developed in the past few years which are the subject of this critical review. Therefore, this paper focuses on the recent advances in the development of new low-temperature SOFCs materials, especially low-temperature electrolytes and electrodes with improved electrochemical properties, as well as summarizing the matching current collectors and sealants for the low-temperature region. Different strategies for improving the cell efficiency, the impact of operating variables on the performance of SOFCs, and the available choice of stack designs, as well as the costing factors, operational limits, and performance prospects, have been briefly summarized in this work.
The disclosure provides a method of producing hydrogen. The method comprises conducting a thermochemical reaction by contacting a metal, or an alloy thereof, with steam to produce a metal oxide and/or a metal hydroxide and hydrogen. The method then comprises contacting the metal oxide and/or the metal hydroxide produced in the thermochemical reaction with water or a basic aqueous solution to produce a solution comprising a metal ion. Finally, the method comprises conducting an electrochemical reaction by applying a voltage across an anode and a cathode, whereby at least a portion of the cathode contacts the solution comprising the metal ion, to produce hydrogen, oxygen and the metal, or the alloy thereof.
Air pollution, climate changes, and global warming are strongly correlated with burning huge amounts of petroleum fuels. Biodiesel has emerged as a promising alternative to alleviate these problems. Nonetheless, high density and viscosity, low energy content, and poor atomization of biodiesel restrict its widespread usage in diesel engines. The addition of nanoparti-cles (NPs) in biodiesel-based fuels has recently received considerable attention to modify the physicochemical properties of fuel as well as to improve the performance and emission characteristics of diesel engines. Among the various NP additives, alumina (Al 2 O 3) NPs are of high interest owing to their excellent chemical and thermal stability, nontoxicity, high catalytic activity, etc. Hence, the present paper attempts to review the available literature concerning biodiesel fuels containing Al 2 O 3 NPs. In this regard, the preparation techniques and physiochemical properties of these fuels including density, kinematic viscosity , cetane number, flash point, and calorific value are first discussed. Furthermore, the impact of Al 2 O 3 NPs on the spray atomization and evaporation features of as-used fuels is investigated. Finally, the performance, combustion, and emission characteristics of diesel-fueled engines with Al 2 O 3 NP-added biodiesel fuels are assessed. In conclusion, it was found that the use of Al 2 O 3 NPs in biodiesel fuels can lead to enhanced engine performance by increasing the brake thermal efficiency, decreasing brake-specific fuel consumption, and lowering the emission of various harmful pollutants. Graphical abstract The performance of Al 2 O 3 nanoadditives for biodiesel-fueled diesel engines
This paper proposes a novel hybrid marine renewable energy-harvesting system to increase energy production, reduce levelized costs of energy and promote renewable marine energy. Firstly, various marine renewable energy resources and state-of-art technologies for energy exploitation and storage were reviewed. The site selection criteria for each energy-harvesting approach were identified, and a scoring matrix for site selection was proposed to screen suitable locations for the hybrid system. The Triton Knoll wind farm was used to demonstrate the effectiveness of the scoring matrix. An integrated energy system was designed, and FE modeling was performed to assess the effects of additional energy devices on the structural stability of the main wind turbine structure. It has been proven that the additional energy structures have a negligible influence on foundation/structure deflection (
The production of size-tunable Carbon microspheres (CMSs) from cheaply available materials using an environmentally friendly technique is highly appreciated. In this study, size-tunable CMSs were hydrothermally synthesized at 190°C using sucrose as carbon source, and citric acid as a catalyst. The effect of varying citric acid concentration on the size of the microspheres was investigated. Results indicated that under similar hydrothermal conditions, variation in the concentration of citric acid between 0 and 5 wt.% increased the size of CMSs ranging from 3.12 to 11.2 μm, as evidenced by SEM and particle size analyzer. TGA confirmed the purity of the carbonaceous particles in a single-step degradation with the presence of D-band and G-band in Raman spectra. FTIR and elemental analyzer confirmed the presence of hydrophilic oxygen functionalities such as –OH, –C=O, and COOH on the surface of CMSs. This study opens a novel and straightforward approach to produce size-tunable CMSs with functional groups.
Heterogeneous catalysis plays a central role in the global energy paradigm, with practically all energy-related process relying on a catalyst at a certain point. The application of heterogeneous catalysts will be of paramount importance to achieve the transition towards low carbon and sustainable societies. This book provides an overview of the design, limitations and challenges of heterogeneous catalysts for energy applications. In an attempt to cover a broad spectrum of scenarios, the book considers traditional processes linked to fossil fuels such as reforming and hydrocracking, as well as catalysis for sustainable energy applications such as hydrogen production, photocatalysis, biomass upgrading and conversion of CO2 to clean fuels. Novel approaches in catalysts design are covered, including microchannel reactors and structured catalysts, catalytic membranes and ionic liquids. With contributions from leaders in the field, Heterogeneous Catalysis for Energy Applications will be an essential toolkit for chemists, physicists, chemical engineers and industrials working on energy.
A nano-supported hydrodesulphurization (HDS) catalyst is prepared for hydrodesulphurization of hydrocarbonaceous feed stock. The catalyst can be prepared through different methods and also used under milder conditions than those required for conventionally used HDS catalysts, but can also function under other hydrodesulphurization operating conditions
In this study, high quality monodispersed nanocrystalline cupric oxide (CuO) nanopowder was prepared through novel sol-gel green synthesis method, assisted by sodium alginate (Na-ALG) as the green ionic exchange material. The morphology and structural properties of CuO nanopowders synthesized with and without the incorporation of extrusion dripping, at different Na-ALG solution concentrations and calcination temperatures, were studied using thermalgravimetric analysis (TGA), field emission scanning electron microscopy (FE-SEM), energy dispersive X-ray spectroscopy (EDX) and Raman spectroscopy. Optimum synthesis conditions were identified, resulting in high-purity, monodispersed nanocrystalline CuO powder in the range of 9.92 – 12.4 nm, which could have a promising future in various applications.
Alkaline water electrolysis is a well-established conventional technique for hydrogen production. However, due to its relatively high energy consumption, the cost of hydrogen produced by this technique is still high. Here in this work, we report for the first time the application of alkaline zinc hydroxide solution (composed of sodium zincate and potassium zincate in NaOH and KOH solutions, respectively) as an efficient, simple and recursive electrolyte for producing clean hydrogen through a continuous dual-step electrolysis process. The ionic conductivity, electrodes current density, and hydrogen evolution rate were measured in a wide range of the electrolyte concentrations (0.1-0.59 M). Also, the cell efficiency was studied at different ranges of current density (0.09-0.25 A/cm2) and applied potential (1.8-2.2 V). Results indicated that the application of alkaline zinc hydroxide solution at the optimum electrolyte concentration can enhance the hydrogen evolution rate minimally by a factor of 2.74 (using sodium zincate) and 1.47 (using potassium zincate) compared to the conventional alkaline water electrolysers. The results of this study could be helpful to better understand the electrochemical behaviour of the alkaline water electrolysers when sodium zincate and potassium zincate are used as ionic activators for enhancing hydrogen evolution.
The rare-earth-doped zirconia-based solid electrolytes have gained significant interest in protonic ceramic fuel cell (PCFC) applications due to their high ionic conductivity. However, these solid electrolytes are susceptible to low conductivity and chemical stability at low operating temperatures, which are of interest in commercializing ceramic fuel cells. Thus, tailoring the structural properties of these electrolytes towards gaining high ionic conductivity at low/intermediate temperatures is crucial. In this study, Ce (cerium) and Nd (neodymium) co-doped barium zirconate perovskites, BaZr (0.80-x-y) Ce x Nd y Y 0.10 Yb 0.10 O 3-δ (BZCNYYO) of various doping fractions (x, y: 0, 0.5, 0.10, 0.15), were synthesized (by the Pechini method) to systematically analyze their structural and conductivity properties. The X-ray diffraction patterns showed a significant lattice strain, and the stress inferences for each co-doped BZCNYYO sample were compared with Nd-cation-free reference samples, BaZrO 3 and BaZr (0.80-x-y-z) Ce x Y y Yb z O 3-δ (x: 0, 0.70; y: 0.20, 0.10; z: 0, 0.10). The comparative impedance investigation at low-to-intermediate temperatures (300–700 • C) showed that BaZr 0.50 Ce 0.15 Nd 0.15 Y 0.10 Yb 0.10 O 3-δ offers the highest lattice strain and stress characteristics with an ionic conductivity (σ) of 0.381 mScm −1 at 500 • C and activation energy (E a) of 0.47 eV. In addition, this σ value was comparable to the best reference sample BaZr 0.10 Ce 0.70 Y 0.10 Yb 0.10 O 3-δ (0.404 mScm −1) at 500 • C, and it outperformed all the reference samples when the set temperature condition was ≥600 • C. The result of this study suggests that Ce-and Nd-doped BZCNYYO solid electrolytes will be a specific choice of interest for developing intermediate-temperature PCFC applications with high ionic conductivity.
Microstructural features and physical properties of the anodes crucially affect the electrochemical performance of anode-supported solid oxide fuel cells (SOFCs). This paper evaluated the microstructural characteristics and properties including porosity, pore size distribution, sintering shrinkage, mechanical strength, and electrical conductivity of the SOFC anode using carbon microspheres (CMSs) as the pore-former in the fabrication of Ni/YSZ ceramic anode. CMSs with different average particle sizes (CMS1: 11.54 μm, CMS2: 4.39 μm, and CMS3: 0.27 μm) were synthesized, and then incorporated into NiO/YSZ at various volumetric blend ratios ranging from 4.4 to 44.6 vol.%. SOFC anode cermets with a desirable range of porosity (30–40%), shrinkage (15.9–17.3%), flexural strength (75.4–157.8 N), and electrical conductivity (253.5–510.7 S/cm) were obtained using approximately 4–10 vol% of CMS1, 4–20 vol.% of CMS2, and 10–34 vol.% of CMS3. In addition, the use of CMS as the pore former reduced the amount of closed pores in the anode disks from 2.05% to
Chitosan is a linear polysaccharide that can be synthesized through the deacetylation of chitin, a naturally abundant biopolymer found in the exoskeleton of crustaceans. It has received a lot of attention because of important features such as biodegradability, biocompatibility and antibacterial and regenerative properties. These features render it useful as the basic building block in important applications such as adsorptive wastewater treatment, sustained drug delivery, gene therapy, and electrosensors. Grafting this polymer with different types of moieties enhances its properties in different ways, e.g., grafting polyethylene glycol (PEG) to chitosan increases its solubility, and subsequently tuning the percent content of PEG imparts thermoresponsivity to the hydrogel. In this chapter, different applications of grafted chitosan are outlined with respect to different types of moieties, cross-linking reagents, grafting techniques, and experimental parameters such as the pH and the percent concentration of polymers.
Zirconia (ZrO₂) nanoparticles were successfully synthesised from zirconyl chloride and ammonium oxalate via co-precipitation (CP), followed by calcination of the resulting co-precipitated precursor. CP and calcination processing parameters showed considerable effects on the surface morphology, average crystallite size, and phase purity of the resulting ZrO₂ particles. In this work, field emission scanning and transmission electron microscopy (FESEM and TEM) confirmed the existence of spherical and uniformly shaped ZrO₂ particles, with crystallite size ranging between 6 and 35 nm. Pure ZrO₂ nanoparticles synthesised through calcination at 650 °C had a strained monoclinic phase structure. On the other hand, ZrO₂ particles prepared through calcination at 600 °C revealed presence of a transitional phase from tetragonal to monoclinic phase in its X-ray diffraction (XRD) patterns. The FESEM images and XRD results also revealed that the degree of particle agglomeration and average crystallite size had increased with increasing processing temperatures and durations. Henceforth, precursor was co-precipitated at 40 °C for 1 h, then calcined at 650 °C for 4 h for optimum production of ZrO₂ nanoparticles with an average crystallite size of 12.85 nm and large Brunauer–Emmett–Teller (BET) surface area of 18.06 m²/g.
Multiwall carbon nanotubes are modified by urea (MWCNTs-U), as an amide group, through a simple amination method to be used as support for Pt nanoparticles in methanol electrooxidation reaction (MOR). The amination method involves a covalent grafting of urea molecules onto the surface of acid treated multiwall carbon nanotubes (MWCNTs-A) using O-(7-azabenzotriazol-1-yl)-N,N,N′,N′-tetramethyluronium hexafluorophosphate (HATU) as the coupling agent. Platinum nanoparticles are impregnated on the surface of MWCNTs-U using NaBH4. Pt/MWCNTs-U shows an enhanced electrocatalytic activity and durability with exposing larger accessible surface area and 27% higher active surface area compared to Pt/MWCNTs-A. In addition, urea incorporation can improve the electrocatalyst tolerance against CO-poisoning, due to the enhanced formation kinetics of the chemisorbed hydroxyl groups. The onset potential of COads oxidation indicates a decrease from 553 mV to 530 mV for Pt/MWCNTs-A and Pt/MWCNTs-U, respectively. It is observed that in the presence of amide group the forward peak current density and exchange current density, in CV and LSV experiments, respectively increase from 378 to 515 mA/mgPt and 1.59 × 10−8 A/cm2 to 2.12 × 10−8 A/cm2. These results are also in a good agreement with the theoretical activation energies obtained from Arrhenius plots, indicating a decrease from 41.7 to 38.8 kJ/mol methanol in the case of Pt/MWCNTs-A and Pt/MWCNTs-U, respectively.
Nanocrystalline gadolinium-doped ceria (GDC) was synthesized by a single step, low cost and environmentally friendly method using ammonium tartrate as an inexpensive, green and novel precipitant. The precipitate obtained during the process was calcined at 400 and 600 °C and the effect on the final microstructural properties of the powders of differing process variables were studied. The synthesized GDC samples were analysed using a range of different techniques, including XRD, TG/DSC, FESEM, STEM, and FT-IR and Raman spectroscopies. The thermal (TG/DSC), XRD and Raman spectroscopic analyses confirm the formation of a single crystalline phase with a cubic (fluorite) unit cell and formed at a low calcination temperature (400 °C). XRD profiles permitted estimation of crystallite sizes as
Apatite-type lanthanum silicate (LSO) electrolyte is one of the most promising candidates for developing intermediate-temperature solid oxide electrolysis cells and solid oxide full cells (IT-SOECs and SOFCs) due to its stability and low activation energy. However, the LSO electrolyte still suffers from unsatisfied ionic conductivity and low relative density. Here in this work, a novel co-doped method is reported to prepare highly purified polycrystalline powders of Mg-Mo co-doped LSO (Mg/Mo-LSO) electrolytes with high excellent densification properties and improved ionic conductivity. Introducing the Mo 6+ and Mg 2+ ions into the LSO structure can increase the number of interstitial oxide ions and improve the degree of densification at lower sintering temperatures, more importantly, expand the migration channel of oxide ions to enhance the ionic conductivity. As a result, the relative density of the fabricated Mo/Mg-LSO electrolytes pellets could achieve more than 98% of the theoretical density after sintering at 1500 ℃ for 4 h with a grain size of about 1-3 μm and the EIS results showed the ionic conductivity increased from 0.782 mS·cm-1 for the pristine LSO to 33.94 mS·cm-1 for the doped sample La 9.5 Si 5.45 Mg 0.3 Mo 0.25 O 26+δ at 800 ℃. In addition, the effect of different Mo 6+ doping contents was investigated systematically, in which La 9.5 Si 5.45 Mg 0.3 Mo 0.25 O 26+δ possessed the highest ionic conductivity and relative density. The proposed Mo/Mg co-doped method in this work is one step forward in developing apatite-structured electrolytes offering excellent potential to address the common issues associated with the fabrication of dense, highly conductive, and thermochemically stable electrolytes for solid oxide electrolysers and fuel cells.
Nowadays, the ever-growing energy demands, the associated greenhouse gas emissions, and the exhaustible nature of fossil fuels are the biggest challenges of our industrial world. The use of clean and renewable energy is key to tackling the global warming impact and the associated worldwide climate crisis. Among various state-of-the-art technologies, fuel cells have shown great promise for the addressal of the above-mentioned issues because of their higher efficiency compared to conventional methods and significant potential for integration with worldwide net-zero carbon emission activities. Fuel cells can be divided into several classifications, such as PEMFC, PAFC, SAFC, AFC, MCFC, SOFC, etc., and are comprised of three main components: the anode, cathode, and electrolyte. The electrolyte layer, which is sandwiched between the anode and cathode layers, is known to be the heart of the fuel cell. Generally, fuel cells should have a good ion conductivity, high electrochemical performance, and a stable physical, chemical, dimensional, and morphological state in redox or oxidising environments. Solid oxide fuel cells (SOFCs) are of great importance among all fuel cells, due to their higher efficiency (80–85%) through the capture and reuse of waste heat. The electrolyte layer, which is sandwiched between the electrodes, is a solid material and should have a high density, high ionic conductivity (more than 0.1 S·cm−1), high thermal, physical, and chemical stability in redox environments, matching thermal expansion coefficient, etc. [1]. On the other hand, both electrodes should have an adequate porosity, high conductivity, and matching TEC, as well as thermal, chemical, and physical stability in different atmospheres. SOFCs can catalytically convert energy from fuels to electricity, and can be used in different designations, namely, in electrode-, electrolyte-, or metal-supported configurations. Each of these designations has some advantages over the other ones. In another classification, SOFCs can be divided into three different types according to their operating temperature: (a) high-temperature SOFCs (>800 °C), (b) intermediate-temperature SOFCs (600–800 °C), and (c) low-temperature SOFCs (
The catalytic performance of a series of bimetallic Ni-Co/CeO2-Al2O3 catalysts were evaluated within the dry reforming of methane (DRM) reaction, commonly used for upgrading biogas. The study focused on the variation of CeO2 weight loadings between 0, 10, 20 and 30%. It was found that the addition of CeO2 promoted CH4 and CO2 conversion across the temperature range and increased H2/CO ratio for the “low temperature” DRM. X-Ray Diffraction (XRD), H2-Temperature Programmed Reduction (H2-TPR) and X-Ray Photoelectron Spectroscopy (XPS) analysis revealed the formation of Ce4+ during activation of the 30% sample, resulted in excessive carbon deposition during reaction. The lowest CeO2 weight loadings exhibited softer carbon formation and limited increased chemical stability during reaction at the expense of activity. Of the tested weight loadings, 20 wt% CeO2 exhibited the best balance of catalytic activity, chemical stability and deactivation resistance in the DRM reaction. Hence this catalyst can be considered a promising system for syngas production from biogas at relatively low temperatures evidencing the pivotal role of catalysts design to develop economically viable processes for bioresources valorisation.
In this study, nickel oxide was prepared through the calcination of extrusion dripped chitosan/nickel nitrate beads. The morphology and structural properties of the products were studied using various characterization techniques. Uniformly distributed nickel oxide was formed as observed from the studies of surface morphology where the processing parameters play a huge role on the resulting morphology. TEM results have shown that nickel oxide with crystallite sizes of 10–30 nm was obtained. The Fourier-transform infrared spectra studies show an intense peak at 525 cm−1, which is attributed to the vibration of Ni–O bond. Furthermore, the XRD results show NiO diffraction peaks correspond to (111), (200), (220), (311), and (222) which indicates that a bunsenite structure with a face-centered cubic phase was produced in this study. The usage of 500°C as the lower limit in this study is justified due to the complete removal of the templating material as seen in the thermalgravimetric analysis studies. Furthermore, it was obtained that the largest surface area of nickel oxide synthesized using this technique is 48.024 m2/g with pore sizes of 19.843 nm. The usage of chitosan as a green template for the synthesis of nanoparticles has shown promising results which allows a more economical and sustainable approach for the fabrication of nanomaterials.
This review critically analyses various aspects of the most promising thermochemical cycles for clean hydrogen production. While the current hydrogen market heavily relies on fossil-fuel-based platforms, the thermochemical water-splitting systems based on the reduction-oxidation (redox) looping reactions have a significant potential to significantly contribute to the sustainable production of green hydrogen at scale. However, compared to the water electrolysis techniques, the thermochemical cycles suffer from a low technology readiness level (TRL), which retards the commercial implementation of these technologies. This review mainly focuses on identifying the capability of the state-of-the-art thermochemical cycles to deploy large-scale hydrogen production plants and their techno-economic performance. This study also analyzed the potential integration of the hybrid looping systems with the solar and nuclear reactor designs, which are evidenced to be more cost-effective than the electrochemical water-splitting methods, but it excludes fossil-based thermochemical processes, such as gasification , steam methane reforming, and pyrolysis. Further investigation is still required to address the technical issues associated with implementing the hybrid thermochemical cycles in order to bring them to the market for sustainable hydrogen production.
The thermochemical water-splitting method is a promising technology for efficiently converting renewable thermal energy sources into green hydrogen. This technique is primarily based on recirculating an active material, capable of experiencing multiple reduction-oxidation (redox) steps through an integrated cycle to convert water into separate streams of hydrogen and oxygen. The thermochemical cycles are divided into two main categories according to their operating temperatures, namely low-temperature cycles (
The adsorption mechanism of pure cellulose is yet to be explored. Thus, in this study, the adsorption mechanism of Microcrystalline Cellulose (MCC), a polysaccharide which is renewable, low cost and non-toxic, was studied on the adsorption of model dye Methylene blue (MB). It was found that the main adsorption mechanism of MB on MCC was due to the electrostatic attraction between the positively charged MB dye and negatively charged MCC. Thus, physical adsorption was the dominant effect, since electrostatic attraction is categorized as physical adsorption. This was verified by Dubinin-Radushkevich isotherm, whereby mean free energy adsorption value was found to be less than 8 kJ/mol. The values of Gibbs free energy for thermodynamics studies were found to be within the range of -20 kJ/mol and 0 kJ/mol, which also indicated physical adsorption. It was due to the electrostatic attraction as adsorption mechanism of this adsorption process which resulted rapid adsorption of MB dye. It was found that equilibrium dye concentration was achieved between 1-3 minutes, depending on the adsorption temperature. The rapid adsorption, as compared to a lot of materials, showed the potential of MCC as the future of green adsorbent. The adsorption of Methylene Blue on MCC fitted well in Langmuir Isotherm, with R2 values of higher than 0.99, while fitted moderately in Freundlich Isotherm, with R2 values between 0.9224 and 0.9223. Comparatively, the adsorption of MB on MCC fitted best Langmuir Isotherm as compared to Freundlich Isotherm which monolayer adsorption occurred at the homogenous surface of MCC. This also indicated adsorbed MB molecules do not interact with each other at neighboring adsorption sites. The maximum adsorption capacity calculated from Langmuir Isotherm was found to be 4.95 mg/g. Despite the potential of MCC as green adsorbent, the challenge of low adsorption capacity has to be addressed in the future.
In this work methane was decomposed to hydrogen and carbon to determine its kinetic behavior during reaction over a Co–Mo–MgO supported catalyst using the CVD (Chemical Vapor Deposition) technique. Decomposition of methane molecules was performed in a continuous fixed bed reactor to obtain data to simulate methane decomposition in a gas phase heterogeneous media. The products and reactants of reaction were analyzed by molecular sieve column followed by GC-analysis of the fractions to determine the amount of product converted or reactant consumed. The synthesis of single-walled carbon nanotubes was performed at atmospheric pressure, different temperatures and reactant concentrations. The experimental data analyzed to suggest the formula for calculation of the initial specific reaction rate of the carbon nanotubes synthesis, were fitted by several mathematical models derived from different mechanisms based on Longmuir-hinshelwood expression. The suggested mechanism according to dissociation adsorption of methane seems to explain the catalytic performance in the range of operating conditions studied. The apparent activation energy for the growth of SWNTs was estimated according to Arrhenius equation. The as grown SWNTs products were characterized by SEM, TEM and Raman spectroscopy after purification. The catalyst deactivation was found to be dependent on the time, reaction temperature and partial pressure of methane and indicated that the reaction of deactivation can be modeled by a simple apparent second order of reaction.