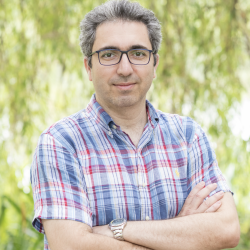
Dr Abdolreza Roshani FHEA
Academic and research departments
Business Analytics and Operations, Centre of Digital Economy, Centre for Business Analytics in Practice.About
Biography
Abdolreza Roshani is a Lecturer (Assistant Professor) in Business Analytics at Surrey Business School. Prior to this role, he was a Post-doctoral Researcher at the Centre for Digital Economy (CoDE) within Surrey Business School and furthered his expertise as a visiting scholar at Kettering University in Michigan.
Abdolreza has contributed to academia through publications in top-tier journals, including the International Journal of Production Research, Journal of Cleaner Production, Annals of Operations Research, Journal of Manufacturing Systems, International Journal of Advanced Manufacturing Technology, and International Journal of Computer Integrated Manufacturing. Abdolreza is also committed to education, teaching a range of management and engineering modules to undergraduate and postgraduate students.
Dr. Abdolreza Roshani was an active researcher in the RAMONA Project, which focused on developing effective techniques for detecting disruptions in manufacturing, analyzing them, and creating responsive strategies for reconfigured manufacturing processes. This collaborative initiative involved three universities: the University of Warwick, the University of Reading, and the University of Surrey, supported by over £1 million in funding from the EPSRC. The project's primary aim was to develop innovative tools and techniques that enhance the resilience of additive manufacturing.
The RAMONA Project was led by Professor Greg Gibbons from Warwick University, with contributions from researchers at Surrey University, including co-investigator Professor Glenn Parry and Dr. Abdolreza Roshani as a researcher.
I am currently accepting applications from prospective PhD students in the fields of Business Analytics and resilient supply chain design. Please feel free to email me your CV.
ResearchResearch interests
Operations Research, Optimisation, Supply Chain Management, Business Analytics
Research interests
Operations Research, Optimisation, Supply Chain Management, Business Analytics
Publications
Additive Manufacturing (AM), an innovative technology, plays a pivotal role in localising supply chains, with the integration of digital technologies further enhancing production flexibility and system resilience. However, AM increases digitalisation in the supply chain, which brings a range of cybersecurity vulnerabilities. Consequently, a comprehensive risk assessment framework is necessary to assist decision-makers considering AM systems. Prior research has employed Composite Indicators (CIs) for risk evaluation, aggregating sub-indicators to assess risks. However, the approach to determining suitable weights for these sub-indicators presents notable limitations such as limited discriminant power, non-unique outcome, subjective assumption on weight preference. To solve the limitation in determining the weight, this paper introduces a multi-level (three-stage) risk assessment model based on the Multiplicative Non-Parametric Approach. This model provides a thorough evaluation of threats within AM systems, considers both individual and industrial perspectives, and determines the global weights of each sub-indicator. The empirical analysis demonstrates that the proposed multi-level model effectively identifies appropriate weights for the sub-indicators, resulting in outcomes that closely align with the original assessment results. The model's performance improves as the number of analysis stages increases, reaching its peak in the final stage of analysis. ARTICLE HISTORY
With increased globalisation supply chain (SC) disruption significantly affects people, organisations and society. Supply chain network design (SCND) reduces the effects of disruption, employing mitigation strategies such as extra capacity and flexibility to make SCs resilient. Currently, no systematic literature review classifies mitigation strategies for SCND. This paper systematically reviews the literature on SCND, analysing proposed mitigation strategies and the methods used for their integration into quantitative models. First to understand the key failure drivers SCND literature is categorised using geography, with local, regional or global disruptions linked to vulnerable sections of a SC. Second, the strategies used in mathematical models to increase SC resilience are categorized as proactive, reactive, or SC design quality capabilities. Third, the relative performance of mitigation strategies is analysed to provide a comparison, identifying the most effective strategies in given contexts. Forth, mathematical modelling techniques used in resilient SCND are reviewed, identifying how strategies are integrated into quantitative models. Finally, gaps in knowledge, key research questions and future directions for researchers are described.
Multi-Manned assembly line balancing problems are usually occurred in plants producing large-sized high-volume products such as automobiles and trucks. In this paper, a cost oriented objective function is presented for a multi-manned assembly line balancing problem. This kind of objective function may be used to balance final assembly lines of products in which manufacturing process is very labor intensive. A mixed-integer mathematical programming model is proposed to solve the problem optimally. The proposed formulation has been used to solve some small size problems by considering; both time-oriented and cost-oriented objective functions. The experiments show that, given the same precedence graph of multi manned assembly line with a Same cycle time, two different optimal solutions can be actually found when switching from time-oriented to cost-oriented objective functions, and vice versa. This difficulty increases the complexity of the cost-oriented multi manned assembly line balancing problems with respect to the multi-manned assembly line balancing problems addressed in the literature. (C) 2015, IFAC (International Federation or Automatic Control) Hosting by Elsevier Ltd. All rights reserved.
Mixed-model synchronous assembly line (MMSAL) is a type of assembly line that can be found in the production of large household appliances (e.g., washing machines, dryers, etc.). In this assembly line, products that are simultaneously processed on the line are transferred to the next station at the same time. In this paper, the sequencing problem of MMSAL with three objectives: (1) total idle cost, (2) total production rate variation cost, and (3) total setup cost is simultaneously studied. These three objectives are first weighted by their relative importance weights and a mathematical model is proposed for the problem. Since this problem is well known as non-deterministic polynomial-time hard class, a meta-heuristic algorithm based on simulated annealing is proposed to solve it. Performance of the proposed algorithm is compared against the Lingo 9 software. The computational results validate the efficiency and effectiveness of the proposed algorithm.
► We addressed multi-manned assembly line balancing problems. ► The performance criteria are the line efficiency, line length and the smoothness index. ► We proposed a simulated annealing approach to solve the problem. ► The performance of proposed algorithm is tested on a set of test problems. ► The computational results show that the proposed algorithm performs well. Assembly line balancing problems with multi-manned workstations usually occur in plants producing high volume products (e.g. automotive industry) in which the size of the product is reasonably large to utilize the multi-manned assembly line configuration. In these kinds of assembly lines, usually there are multi-manned workstations where a group of workers simultaneously performs different operations on the same individual product. However, owing to the high computational complexity, it is quite difficult to achieve an optimal solution to the balancing problem of multi-manned assembly lines with traditional optimization approaches. In this study, a simulated annealing heuristic is proposed for solving assembly line balancing problems with multi-manned workstations. The line efficiency, line length and the smoothness index are considered as the performance criteria. The proposed algorithm is illustrated with a numerical example problem, and its performance is tested on a set of test problems taken from literature. The performance of the proposed algorithm is compared to the existing approaches. Results show that the proposed algorithm performs well.
Purpose - This paper aims to study a generalized type of mixed-model assembly line with multi-manned workstations where multiple workers simultaneously perform different tasks on the same product. This special kind of assembly line is usually utilized to assemble different models of large products, such as buses and trucks, on the same production line. Design/methodology/approach - To solve the mixed-model multi-manned assembly line balancing problem optimally, a new mixed-integer-programming (MIP) model is presented. The proposed MIP model is nondeterministic polynomial-time (NP)-hard, and as a result, a simulated annealing (SA) algorithm is developed to find the optimal or near-optimal solution in a small amount of computation time. Findings - The performance of the proposed algorithm is examined for several test problems in terms of solution quality and running time. The experimental results show that the proposed algorithm has a satisfactory performance from computational time efficiency and solution accuracy. Originality/value - This research is the very first study that minimizes the number of workers and workstations simultaneously, with a higher priority set for the number of workers, in a mixed-model multi-manned assembly line setting using a novel MIP model and an SA algorithm.
In real-world assembly lines, that the size of the product is large (e.g., automotive industry), usually there are multi-manned workstations where a group of workers simultaneously perform different operations on the same individual product. This paper presents a mixed integer programming model to solve the balancing problem of the multi-manned assembly lines optimally. This model minimizes the total number of workers on the line as the first objective and the number of opened multi-manned workstations as the second one. Since this problem is well known as NP (nondeterministic polynomial-time)-hard, a heuristic approach based on the ant colony optimization approach is developed to solve the medium- and large-size scales of this problem. In the proposed algorithm, each ant tries to allocate given tasks to multi-manned workstations in order to build a balancing solution for the assembly line balancing problems by considering the precedence relations, multi-manned assembly line configuration, task times, and cycle time constraints. Through computational experiments, the performance of the proposed ACO is compared with some existing heuristic on various problem instances. The experimental results validate the effectiveness and efficiency of the proposed algorithm.
Premature failure of a first stage gas turbine nozzle has been the subject of a precise study and the present investigation comprehensively describes it. It was determined that failure occurred by thermal fatigue mechanism during start-up/shutdown of gas turbine. The cracks initiated from the surface of trailing edge section in which intergranular oxidation caused by high temperature hot corrosion (HTHC) was significant. In addition, the presence of continuous film of carbides at the grain boundaries was a direct result of transformation of primary carbides M(6)C type to secondary carbides M(23)C(6) type as a result of high temperature operation of the nozzle. Therefore, the nozzle crack initiation and propagation was facilitated by grain boundaries brittleness caused by formation of continuous film of carbides M(23)C(6) at the grain boundaries. Furthermore, to experimentally confirm the degradation of the nozzle, mechanical test data was taken into consideration. It was found that the tensile properties of the alloy have decreased. In the similar test conditions, the hardness of the exposed alloy increased considerably compared to the as-cast sample, which could be attributed to the microstructural degradation, especially formation of M(23)C(6) carbides in the large quantity in the matrix alloy. (C) 2011 Elsevier Ltd. All rights reserved.
Scheduling for job shop is very important in both fields of production management and combinatorial optimization. Since the problem is well known as NP-Hard class, many metaheuristic approaches are developed to solve the medium and large scale problems. One of the main elements of these metaheuristics is the solution seed structure. Solution seed represent the coding structure of real solution. In this paper, a new solution seed for job shop scheduling is presented. This solution seed is compared with a famous solution seed presented for the job shop scheduling. Since the problem is well known as NP-Hard class, a Tabu search algorithm is developed to solve large scale problems. The proposed solution seed are examined using an example and tabu search algorithm.
Multi-manned assembly lines are often designed to produce big-sized products, such as automobiles and trucks. In this type of production lines, there are multi-manned workstations where a group of workers simultaneously performs different operations on the same individual product. One of the problems, that managers of such production lines usually encounter, is to produce the optimal number of items using a fixed number of workstations, without adding new ones. In this paper, such a class of problems, namely, the multi-manned assembly line balancing problem is addressed, with the objective of minimising the cycle time. A mixed-integer mathematical programming formulation is proposed for the considered problem. This model has the primary objective of minimising the cycle time for a given number of workstations and the secondary objective of minimising the total number of workers. Since the addressed problem is NP-hard, two meta-heuristic approaches based on the simulated annealing algorithm have been developed: ISA and DSA. ISA solves the problem indirectly while DSA solves it directly. The performance of the two algorithms are tested and compared on a set of test problems taken from the literature. The results show that DSA outperforms ISA in term of solution quality and computational time.
In this paper, a system designed to produce multi-class single-level products through both manufacturing of raw materials and remanufacturing of return products is taken into consideration, with the aim of defining and solving an integrated lot sizing and energy-efficient job shop scheduling problem. A mixed-integer programming formulation is proposed for the problem. This model minimizes not only the manufacturing and remanufacturing costs, the setup cost and the inventory holding and backlogging costs over the planning horizon, but also the energy costs paid for the utilization of machines and the compression of processing times. Since the model is NP-hard, a relax-and-fix heuristic is proposed to solve the problem. The proposed algorithm is illustrated with a numerical example, and its performance is tested on a set of randomly generated experimental problems. The results show the efficiency of the algorithm. Besides, the performance of the proposed energy-efficient model has been compared with classical models (that consider only the minimization of manufacturing/remanufacturing, holding and setup costs); the results indicate that the proposed model not only diminishes the energy consumption and the machines idle times, but it actually reduces the overall cost of the system.
The capacitated dynamic lot sizing problem with product returns in a closed remanufacturing system is addressed in this paper. The system is designed to satisfy the demands of different classes of single level products by remanufacturing end-life returned products. A single machine with a limited capacity in each time period is used to perform the remanufacturing operations. A mathematical programming formulation is proposed for the considered problem: the proposed model minimizes the sum of remanufacturing costs over a finite planning horizon. The problem is a generalized version of the classical capacitated dynamic lot, sizing problem, and thus it is NP-hard itself. Therefore, a simulated annealing algorithm, with an efficient neighborhood generation which takes into account the constraints of the problem, is proposed as a solution approach. To evaluate the efficiency of the proposed algorithm, a set of experimental instances are generated and solved. The comparison between the results obtained with the proposed simulated annealing approach and the ones generated by the CPLEX solver shows the effectiveness of the proposed algorithm. (C) 2016, IFAC (International Federation of Automatic Control) Hosting by Elsevier Ltd. All rights reserved.
A mixed-model assembly line is a type of production line where different models of a product are assembled on. Mixed-model assembly lines can respond to unanticipated changes in product demands quickly without keeping so many inventories. Designing mixed-model assembly line involves solving the traditional problems of the assembly line design (consists of balancing problem, determining cycle time, and the number and sequence of stations) in addition of determining the sequence of products in assembly line. The main goal of this paper is presenting a method in order to determine the sequence of products in mixed-model assembly line by considering Just-in-Time systems. Moreover, supplying some required components from feeding lines is considered. A mathematical model is presented which is capable of specifying the sequence of products in the mixed-model assembly line by considering main criteria and keeping feeding lines balanced. Mathematical model can be used for solving small-size problems. Because the combinatorial nature of sequencing problems typically provides an intractable search space for problems of “real world” size, the search heuristics of simulated annealing and ant colony algorithms are presented and used to find solutions for several problem sets. Experimentations show that the simulated annealing approach outperforms the ant colony approach in objective function performance.
In this study, an attempt to investigate the role of isothermal aging on the microstructure and tribological characteristics of Co-28Cr-5Mo-0.3C alloy was made. Regarding the results, isothermal aging at 850 degrees C and 950 degrees C for at least 16 h contributed to the formation of lamellar-type carbides at the grain boundary regions. Moreover, at higher aging times (over 16 h), the amount of lamellar-type carbides decreased. The wear properties of as-cast and heat treated samples were determined at 0.5 ms (1) speed several under normal applied loads such as 50, 80, and 110 N. At the lowest applied load (50 N), the samples were isothermally aged at 850 degrees C for 8 and 16 h and also the ones were aged at 950 degrees C for 16 h had higher wear resistance probably due to more volume fraction of lamellar-type carbides when compared to as-cast and the other aged samples, but, at higher applied loads (80 and 110 N) due to the formation of adhesive oxide layer on the as-cast sample surface, the wear rate of as-cast samples is lower compared with all heat treated ones. (C) 2012 Elsevier Ltd. All rights reserved.
Two-sided assembly line balancing problems usually occur in plants producing large-sized high-volume products such as automobiles, buses or trucks. The difference between these kinds of assembly lines and traditional assembly lines is that there is the possibility of installing two parallel single stations in each position of the line so that the workers can work simultaneously on different tasks of one same product. In this paper, the cost-oriented two-sided assembly line balancing problem is addressed. This kind of assembly line balancing problem usually occurs in final assembly of products in which the manufacturing process is very labour intensive. A mix integer programming is proposed to solve the problem optimally. Since the problem is well known as NP (nondeterministic polynomial-time)-hard, a heuristic algorithm based on simulated annealing approach is developed to solve the medium- and large-size scales of this problem. Through computational experiments, the performance of the proposed heuristic approach is examined. The experimental results validate the effectiveness and efficiency of the proposed algorithm.
Multi-manned assembly lines are often designed to produce large-sized products, such as automobiles, trucks and buses. In this type of production lines, usually there are multi To manned workstations where a group of workers simultaneously performs different, operations On the Same individual product. One of the problems, that managers of such production lines usually encounter, is to produce the optimal number of items using a fixed number of workstations, without adding new ones in order to meet the market, demand. In this paper, such a class of assembly line balancing problems, named multi-manned assembly line balancing problems type II, has been addressed. Since the problem is NP-hard, a meta-heuristic approach based On a simulated annealing algorithm has been developed to solve the problem. The performance of the proposed algorithm has been tested On a set of test problems taken from the literature; the results show that the algorithm performs well. (C) 2015, IFAC (International Federation of Automatic Control) Hosting by Elsevier Ltd. All rights reserved.
Electric vehicles can be perceived as a means to achieve carbon reduction, energy efficiency, and sustainable development of the transportation industry. Electric vehicle sales and deployment are increasing rapidly over time. However, electric vehicle deployment should be conducted in a planned manner, as electric vehicles have some limitations (e.g., limited driving range, refueling capacity, carrying capacity). The electric vehicle scheduling problem should be studied in detail to overcome such limitations, as it addresses them while optimizing the paths and timetables of electric vehicles. A number of studies have been dedicated towards electric vehicle scheduling. Yet, there is a lack of survey studies that cover a structural recapitulation of the electric vehicle scheduling efforts and provide a thorough overview of the existing tendencies, operations research aspects, problem-specific properties, and future research needs. For this reason, this study offers a structured survey of the existing research studies, which assessed electric vehicle scheduling. The collected studies are grouped into three categories for a detailed review, namely general electric vehicle scheduling, electric vehicle scheduling with power grid considerations, and electric vehicle scheduling with environmental considerations. A detailed description of the relevant studies along with a summary of findings and future research needs are provided for each of the study categories. In addition, a representative mathematical model is outlined for each study category in order to guide the future research. The outcomes of this research are expected to provide interesting and important insights to different groups of professionals in the field of electric vehicles.
The target of this paper is to present a novel mathematical model to design a resilient and energy efficiency additive manufacturing supply chain. This model minimizes the total cost of designing SC by selecting the optimal location and type of 3D printers to meet customer demand through active facilities and penalizing lost demand if necessary. To evaluate the efficiency of the proposed algorithm, several experimental instances are solved and the results for a selected case is reported. The results obtained for the selected case demonstrate that the proposed model can effectively reduce energy costs, with only a slight increase in expected shipment costs while the fixed location costs and expected penalty costs remains unchanged.
Highway-rail grade crossing (HRGC) accidents pose a serious risk of safety to highway users, including pedestrians trying to cross HRGCs. A significant increase in the number of HRGC accidents globally calls for greater research efforts, which are not limited to the analysis of accidents at HRGCs but also understanding user perception, driver behavior, potential conflicting areas at crossings, effectiveness of countermeasures and user perception towards them. HRGC safety is one of the priority areas in the State of Florida, since the state HRGCs experienced a total of 429 injuries and 146 fatalities between 2010 and 2019 with a significant increase in HRGC accidents over the last years. The present study aims to conduct a comprehensive analysis of the HRGCs that experienced accidents in Florida over the last years. The databases maintained by the Federal Rail Administration (FRA) are used to gather the relevant information for a total of 578 crossings that experienced at least one accident from 2010 to 2019. In contrast with many of the previous efforts, this study investigates a wide range of various factors, including physical and operational characteristics of crossings, vehicle and train characteristics, spatial characteristics, temporal and environmental characteristics, driver actions and related characteristics, and other relevant information. The outcomes of this research will help better understanding the major causes behind accidents at the HRGCs in the State of Florida in a holistic way by considering a variety of relevant factors, which will assist the appropriate stakeholders with implementation of safety improvement projects across the state.
Multi-manned assembly line balancing problems (MALBPs) can be usually found in plants producing large-sized high-volume products such as automobiles and trucks. In this paper, a cost-oriented version of MALBPs, namely, CMALBP, is addressed. This class of problems may arise in final assembly lines of products in which the manufacturing process is very labor-intensive. Since CMALBP is NP-Hard, a heuristic approach based on a tabu search algorithm is developed to solve the problem. The proposed algorithm uses two neighborhood generation mechanisms, namely swap and mutation, that effectively collaborate with each other to build new feasible solutions; moreover, two separate tabu lists (associated with the two generation mechanisms) are used to check if moving to a new generated neighbor solution is forbidden or allowed. To examine the efficiency of the proposed algorithm, some experimental instances are collected from the literature and solved. The obtained results show the effectiveness of the proposed tabu search approach.
Multi-sided assembly line balancing problems usually occur in plants producing big-sized products such as buses, trucks, and helicopters. In this type of assembly line, in each workstation, it is possible to install several workplaces, in which a single operator performs his/her own set of tasks at an individual mounting position. In this way, the operators can work simultaneously on the same product without hindering each other. This paper considers for the first time the multi-sided assembly line balancing problem with the objective of minimising the cycle time, proposing a new mathematical formulation to solve small-sized instances of this problem. Besides, a metaheuristic algorithm based on variable neighbourhood search hybridised with simulated annealing is developed to solve large-sized instances. The algorithm is called adaptive because of the adopted neighbourhood selection mechanism. A novel three-string representation is introduced to encode the problem solutions and six different neighbourhood generation structures are presented. The developed approach is compared to other meta-heuristics, considering some well-known in literature test instance and a real world assembly line balancing problem arising in a car body assembly line. The experimental results validate the effectiveness of the proposed algorithm.
In this paper, the capacitated lot-sizing and scheduling problem with sequence dependent setup times and costs in a closed loop supply chain is addressed. The system utilizes the closed-loop supply chain strategy so that the multi-class single-level products are produced through both manufacturing of raw materials and remanufacturing of returned recovered products. In this system, a single machine with a limited capacity in each time period is used to perform both the manufacturing and remanufacturing operations. The sequence-dependent setup times and costs (both between two lots of products of different classes and between two lots belonging to the same class of products produced through different methods) are considered. A large-bucket mixed integer programming formulation is proposed for the problem. This model minimizes not only the manufacturing and remanufacturing costs, the setup costs and the inventory holding and backlogging costs over the planning horizon, but also the energy costs paid for the utilization of machine and the compression of processing times. Since the problem is NP-hard, a matheuristic and a grey wolf optimization algorithm are proposed to solve it. To evaluate the efficiency of the proposed algorithm, some experimental instances are generated and solved. The obtained results show the effectiveness of the proposed algorithms.