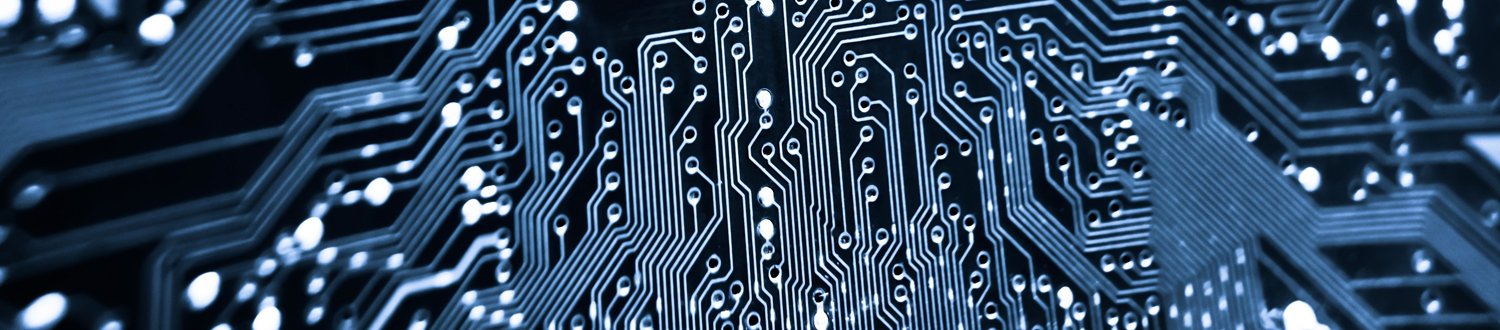
Microfabrication clean room
The Advanced Technology Institute (ATI) houses an extensive microfabrication clean room. This is used for processing of many different substrate types and sizes from individual die up to 150mm wafer.
About the room
Substrate materials include a range of compound semiconductors, silicon, glass, ceramic and some polymers. We can generally find a way to process whatever novel material is required.
Photolithography tools
The clean room has a range of photolithography tools working with UV400 resists. These are augmented by electron beam and ion beam lithography for deep sub-micron capability. We also have a nano-imprint lithography capability that can mechanically replicate structures originated using our photolithography tools.
Etch tools
Subsequent pattern transfer is achieved using both wet chemical etching and reactive ion etch (RIE) processes. The etch tools include RIE with fluorine chemistries dedicated to silicon compatible processing, chlorine chemistries for metal etch and compound semiconductor work, and ICP etch for a full range of process gases including the deep silicon etch (“Bosch process”).
Sputter tools
Metal deposition is carried out using both sputter processes and evaporation. We have an extensive range of targets for the sputter tools.
Dielectric deposition is performed using PECVD tools for silicon oxide and nitride and also by sputter coating, including reactive sputtering of oxides and nitrides. Polymer dielectrics are also used, and we are currently installing a parylene deposition system for low temperature processing and encapsulation. This is expected to be used especially in conjunction with organic materials. Organic material processing has been steadily enhanced. We have glove box processing and dedicated evaporators for use with these materials.
Nanowire device structures
In conjunction with other areas of the ATI the clean room processes nanowire device structures that are used in various applications, such as gas sensors.