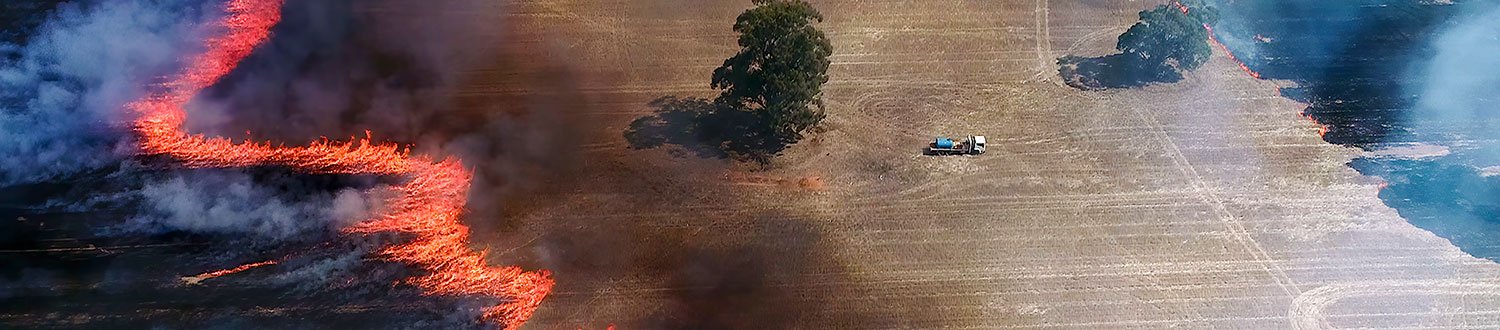
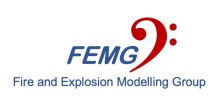
Gaseous hydrogen safety
Detailed analysis about safety issues related to hydrogen gas applications in transport systems and the built environment, working closely with international energy companies.
Small leaks
Using in-house modified HyFOAM code has been used to simulate leaks of hydrogen gas into an enclosure. Below examples show the comparison of predictions with measurements in the HYSEA project for the following conditions:
- Hydrogen release rate 0.00036 kg/s
- Average H2 release temperature 291 K
- Release time 7.5 min
- 20 - 2 inch holes for pressure relief on lower section of the container wall
- Release nozzle diameter 18 mm
- Release location at centre of the container floor and 0.3 m elevation.
Spontaneous ignition in pressurised hydrogen release
Spontaneous ignition of pressurised hydrogen release is an important safety concern. An in-house solver has been modified from KIVA 3V to facilitate its study. The code uses the implicit large eddy simulation (ILES) approach coupled with the 5th-order weighted essentially non-oscillatory (WENO) scheme. A mixture-averaged multi-component approach was used for accurate calculation of molecular transport. The thin flame was resolved with fine grid resolution and the auto-ignition and combustion chemistry were accounted for using a 21-step kinetic scheme.
Numerical simulations have been conducted for releases via a length of tube. The predictions revealed that the finite rupture process of the initial pressure boundary plays an important role in the spontaneous ignition. The rupture process induces significant turbulent mixing at the contact region via shock reflections and interactions. The predicted leading shock velocity inside the tube increases during the early stages of the release and then stabilizes at a nearly constant value. The air behind the leading shock is shock-heated and mixes with the released hydrogen in the contact region. Ignition is firstly initiated inside the tube and then a partially premixed flame is developed.
Publications
Xu, B. P. and Wen, Jennifer X. (2014) The effect of tube internal geometry on the propensity to spontaneous ignition in pressurized hydrogen release. Int. J of Hydrogen Energy, 39 (35). pp. 20503-20508. doi:10.1016/j.ijhydene.2014.04.141
Ruddick, W. O., Teodorczyk, A. and Wen, J. X. (Jennifer X.) (2017) Self-ignition of hydrogen–nitrogen mixtures during high-pressure release into air. Int. J of Hydrogen Energy, 42 (11). pp. 7340-7352. doi:10.1016/j.ijhydene.2016.06.051
Xu, B. P. and Wen, Jennifer X. (2012) Numerical study of spontaneous ignition in pressurized hydrogen release through a length of tube with local contraction. Int. J of Hydrogen Energy, Volume 37 (Number 22). pp. 17571-17579. doi:10.1016/j.ijhydene.2012.04.150
Xu, B. P., Wen, Jennifer X. and Tam, V. H. Y. (2011) The effect of an obstacle plate on the spontaneous ignition in pressurized hydrogen release: a numerical study. Int. J of Hydrogen Energy, Volulme 36 (Number 3). pp. 2637-2644. doi:10.1016/j.ijhydene.2010.03.143
Xu, B. P., EL Hima, L., Wen, Jennifer X. and Tam, V. H. Y. (2009) Numerical study of spontaneous ignition of pressurized hydrogen release into air. Int. J of Hydrogen Energy, Volume 34 (Number 14). pp. 5954-5960. doi:10.1016/j.ijhydene.2009.01.045
Wen, J.X., Xu, B.P., Tam, V.H.Y. (2009) Numerical study on spontaneous ignition of pressurized hydrogen release through a length of tube. Combustion and Flame, Volume 156 (Number 11). pp. 2173-2189. doi:10.1016/j.combustflame.2009.06.012
Xu, B. P., Wen, Jennifer X., Dembele, S., Tam, V. H. Y. and Hawksworth, S. J. (2009) The effect of pressure boundary rupture rate on spontaneous ignition of pressurized hydrogen release. J of Loss Prevention in the Process Industries, Volume 22 (Number 3). pp. 279-287. doi:10.1016/j.jlp.2008.07.007.
Jet fires
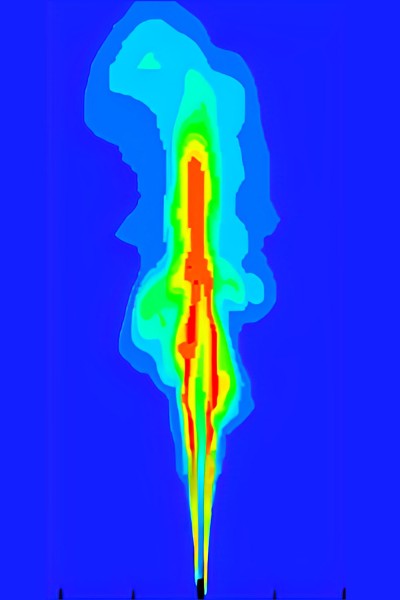
A possible consequence of pressurised hydrogen release is an under-expanded jet fire, which can be extensive in length and pose significant radiation and impingement hazards. Knowledge of the flame length, radiative heat flux as well as the effects of variations in ground reflectance is important for safety assessment.
The in-house HyFOAM code has been modified to study the radiation characteristics of hydrogen jet fires. For combustion, the eddy dissipation concept for multicomponent fuels recently developed by the authors in the large eddy simulation (LES) framework is used. The radiative heat is computed with the finite volume discrete ordinates model, in conjunction with the weighted sum of grey gas model for the absorption/emission coefficient. The pseudo-diameter approach is used in which the corresponding parameters are calculated using the established formulations with the thermodynamic properties corrected by the Able-Noble equation of state.
Publications
Wang, C. J., Wen, Jennifer X., Chen, Z. B. and Dembele, S. (2014) Predicting radiative characteristics of hydrogen and hydrogen/methane jet fires using FireFOAM. Int. J of Hydrogen Energy, 39 (35). pp. 20560-20569. doi:10.1016/j.ijhydene.2014.04.062
Zhang, J., Dembele, S. and Wen J. X., Exploratory Study of Under-expanded Sonic Hydrogen Jets and the Resulting Jet Flames, 5th Int. Seminar on Fire and Explosion Hazards, April 2007, Edinburgh, UK
Shelke, Ashish V. and Wen, Jennifer X. (2021) The burning characteristics and flame evolution of hydrocarbon and hydrogen flash fires. Proc. of the Combustion Institute, 38 (3). pp. 4699-4708. doi:10.1016/j.proci.2020.05.013.
Hydrogen explosions in the presence of obstacles
Safety studies for hydrogen involve identification of possible accidental scenarios, modelling of consequences and measures to mitigate associated hazards with it. Accidental release of hydrogen during its handling and storage can lead to the formation of an ignitable mixture in a very short time. Ignition of such a mixture can lead to the generation of over-pressure affecting structure and people. Understanding the possible overpressures generated is critical in designing the system safe from explosion hazards.
The in-house modified HyFOAM code has been used to model the worst-case scenario where high-pressure hydrogen storage cylinders are enveloped by a premixed hydrogen-air cloud is numerically simulated. The computational domain mimics the setup for a premixed hydrogen cloud in a mock hydrogen cylinder storage congestion environment which were previously studied experimentally. The flame Surface Wrinkling Model in large eddy simulation (LES) context is used for modelling deflagrations. Numerical simulation results are compared against experiments.
Simulations are able to predict experimental flame arrival and overpressure reasonably well. The effects of ignition location, congestion and confining walls on the turbulent deflagrations in particular on explosion overpressure are discussed. It was concluded that explosion overpressure increases in confinement.
Vented hydrogen explosions – CFD models
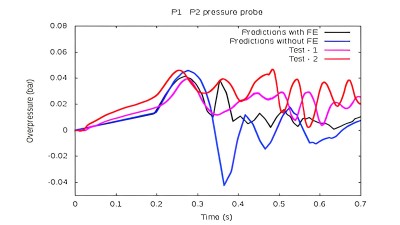
Containers are being considered for hydrogen fuel installations at refuelling stations housing the compressor and pumps, or for portable standalone power generation units housing the fuel cell and its accessories. Identifying the hazards associated with these kind of container applications is essential for its design, safe operations and in mitigating any accidental risks.
The in-house HYFOAM solver has been modified to aid consequences analysis of potential explosions. The code models turbulent flame deflagration using the flame wrinkling combustion model. Additional sub-models have been added to account for the dominant flame instabilities present in the vented lean hydrogen-air mixtures deflagrations.
The 20-foot ISO containers of dimensions 20’ x 8’ x 8’.6” filled with homogenous mixture of hydrogen-air at different concentration, with and without model obstacles have been simulated using LES based HyFOAM code. The predictions have been validated against the experiments carried out in the HYSEA project. To account for the container wall deflections which were found to be of considerable influence on the overpressure, the fluid structure interactions (FSI) have also been considered. The CFD and FSI are coupled in pseudo two-way approach.
Vented hydrogen explosions – engineering models
A simple mathematical model for estimating peak overpressure attained in vented explosions of hydrogen has been developed. It consists of a single equation with four parameters. Two of these parameters only depend on the fuel properties and hence can be pre-tabulated. The other two parameters are simple functions of enclosure and obstacle geometry, which are relatively easy to compute. The new model is much simpler than other models in literature and existing standards. Moreover, predictions from this model are found to be either more accurate than or comparable with other existing models.
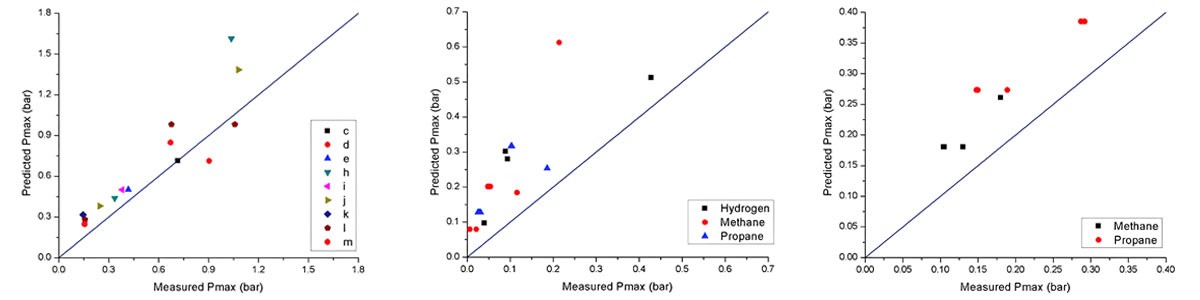
A large set of experimental results have been used to assess the applicability of the new model. These include realistic conditions which involve obstacles, initial turbulence and mixture stratification. The model predictions were found to match well with the available measurements. Although the tests data considered in this study comprise of results for hydrogen, methane and propane, the model can also be used for other gases by re-evaluating the two fuel parameters F1 and F2 from their physical properties. The model is included in the new release of EN14998.
Publications
Vendra, C. Madhav Rao, Sathiah, Pratap and Wen, Jennifer X. (2018) Effects of congestion and confining walls on turbulent deflagrations in a hydrogen storage facility-part 2 : numerical study. International Journal of Hydrogen Energy, 43 (32). pp. 15593-15621. doi:10.1016/j.ijhydene.2018.06.100
Vendra, C. Madhav Rao and Wen, Jennifer X. (2019) Numerical modelling of vented lean hydrogen deflagations in an ISO container. International Journal of Hydrogen Energy, 44 (17). pp. 8767-8779. doi:10.1016/j.ijhydene.2018.11.093
C. Madhav Rao Vendra, Jennifer X. Wen, Fluid structure interactions modelling in vented lean deflagrations, Journal of Loss Prevention in the Process Industries, 2019, 61: 183-194, https://doi.org/10.1016/j.jlp.2019.06.004
Sinha, Anubhav and Wen, J. (2019) A simple model for calculating peak pressure in vented explosions of hydrogen and hydrocarbons. International Journal of Hydrogen Energy, 44 (40)
Skjold, Trygve, Hisken, Helene, Bernard, Laurence, Mauri, Lorenzo, Atanga, Gordon, Lakshmipathy, Sunil, Lucas, Melodia, Carcassi, Marco, Schiavetti, Martino, Vendra, Chandra Madhav Rao et al. (2019) Blind-prediction : estimating the consequences of vented hydrogen deflagrations for inhomogeneous mixtures in 20-foot ISO containers. Journal of Loss Prevention in the Process Industries, 61. pp. 220-236. doi:10.1016/j.jlp.2019.06.013
Sinha, Anubhav, Vendra, C. Madhav Rao and Wen, Jennifer X. (2019) Modular phenomenological model for vented explosions and its validation with experimental and computational results. Journal of Loss Prevention in the Process Industries. 61, pp. 8-23. doi:10.1016/j.jlp.2019.05.01.
Flame acceleration and deflagration to detonation transition
DDT-FOAM has been developed within the in-house HyFOAM framework. It is a density based solver developed within the frame of OpenFOAM for predicting flame acceleration and transition from deflagration to detonation. The predictions have been validated with experimental measurements in a horizontal channel filled with both homogeneous and inhomogeneous hydrogen/air mixtures. Overall, the predicted flame tip velocities, overpressures, and locations of detonation onset are in reasonably good agreement with the measurements.
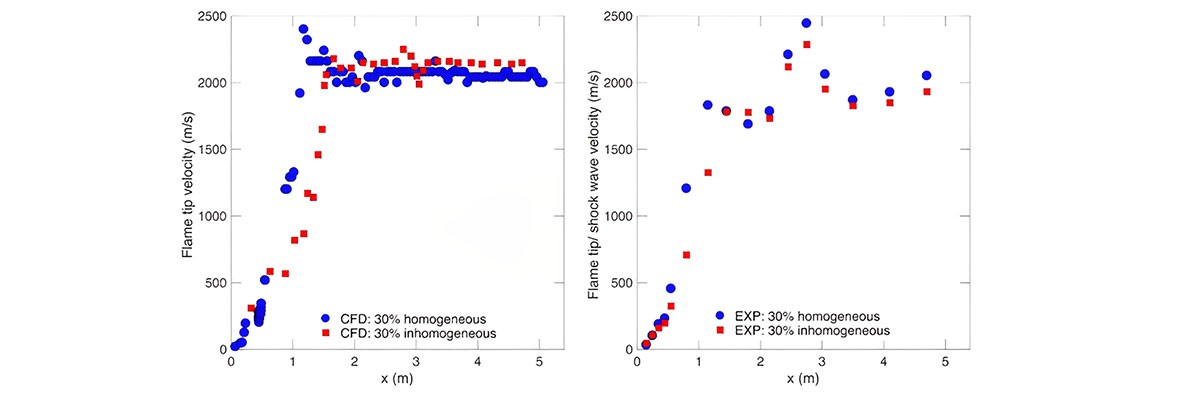
Publications
Khodadadi Azadboni, Reza, Heidari, Ali and Wen, Jennifer X. (2020) Numerical analysis of flame acceleration and onset of detonation in homogenous and inhomogeneous mixture. J of Loss Prevention in the Process Industries. 104063. doi:10.1016/j.jlp.2020.104063
Khodadadi Azadboni, Reza, Heidari, Ali and Wen, Jennifer X. (2018) A Computational Fluid Dynamic Investigation of Inhomogeneous Hydrogen Flame Acceleration and Transition to Detonation. Flow, Turbulence and Combustion, 101 (4). pp. 1009-1021. doi:10.1007/s10494-018-9977-4
Khodadadi Azadboni, Reza, Wen, Jennifer X., Heidari, Ali and Wang, ChangJian (2017) Numerical modeling of deflagration to detonation transition in inhomogeneous hydrogen/air mixtures. J of Loss Prevention in the Process Industries, 49 . pp. 722-730. doi:10.1016/j.jlp.2017.04.024
Heidari, A. and Wen, Jennifer X. (2017) Numerical simulation of detonation failure and re-initiation in bifurcated tubes. Int. J of Hydrogen Energy, 42 (11). pp. 7353-7359. doi:10.1016/j.ijhydene.2016.08.174
Heidari, A. and Wen, Jennifer X. (2014) Numerical simulation of flame acceleration and deflagration to detonation transition in hydrogen-air mixture. Int. J of Hydrogen Energy, 39 (36). pp. 21317-21327. doi:10.1016/j.ijhydene.2014.10.066
Heidari, A. and Wen, Jennifer X. (2014) Flame acceleration and transition from deflagration to detonation in hydrogen explosions. Int. J of Hydrogen Energy, 39 (11). pp. 6184-6200. doi:10.1016/j.ijhydene.2014.01.168
Heidari, A., Ferraris, S., Wen, Jennifer X. and Tam, V. H. Y. (2011) Numerical simulation of large scale hydrogen detonation. Int. J of Hydrogen Energy, Volume 36 (Number 3). pp. 2538-2544. doi:10.1016/j.ijhydene.2010.05.093.
Join us
If you are interested in undertaking a project with us then please contact us to discuss options.
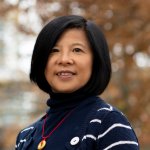
Professor Jennifer Wen
Head of Fire and Explosion Modelling Group