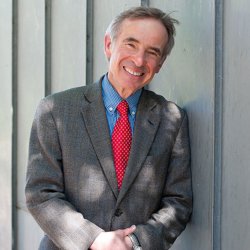
Professor Stephen Ogin
Publications
Military personnel use protective armour systems that are frequently exposed to low-level damage, such as non-ballistic impact, wear-and-tear from everyday use, and damage during storage of equipment. The extent to which such low-level pre-damage could affect the performance of an armour system is unknown. In this work, low-level pre-damage has been introduced into a Kevlar/phenolic resin-starved composite panel using tensile loading. The tensile stress-strain behaviour of this eight-layer material has been investigated and has been found to have two distinct regions; these have been understood in terms of the microstructure and damage within the composite panels investigated using micro-computed tomography and digital image correlation. Ballistic testing carried out on pristine (control) and pre-damaged panels did not indicate any difference in the V50 ballistic performance. However, an indication of a difference in response to ballistic impact was observed; the area of maximal local out-ofplane deformation for the pre-damaged panels was found to be twice that of the control panels, and the global out-of-plane deformation across the panel was also larger.
Matrix as well as interlayer regions of laminated polymer composites have been reinforced with carbon nanotubes, additionally to shape memory alloy wires, in order to further enhance the overall material toughness and introduce the improved impact resistance mechanisms through micro- and nano-engineering. In this work, we examine carbon fiber reinforced polymer composites with constant carbon fiber volume fraction, further reinforced with carbon nanotube and shape memory alloy wires, under controlled impact. Single-type as well as multiple-type impact tests have been carried out, demonstrating that the energy absorption and damage development are similar in both impact tests for the same material. When the carbon nanotube and shape memory alloy wires reinforcements are compared separately, shape memory alloy-reinforced carbon fiber reinforced polymers present higher energy absorption than the carbon nanotube-reinforced carbon fiber reinforced polymers. When they are combined, although the carbon nanotube + shape memory alloy-reinforced carbon fiber reinforced polymers present similar energy absorption improvement to shape memory alloy-only carbon fiber reinforced polymers, the carbon nanotube addition increases toughness, resulting in damage initiation at higher depths of impact penetration.
In this paper, chirped fibre Bragg grating (CFBG) sensors used to monitor the structural health of a composite patch used to repair an aluminium panel is presented. To introduce damage, a notch was produced at the centre of an aluminium panel. The repair consisted of bonding a pre-cured composite patch to the host panel using an aerospace-grade film adhesive; the sensor was embedded in the bond-line during fabrication of the repair. The repaired panels were subjected to tension-tension loading in fatigue. Cracks initiated and grew from both ends of the notch in the aluminium panels and the fatigue loading was stopped periodically for short periods of time to record the reflected spectra from the sensor. It was found that perturbations in the reflected spectra began to occur when the crack was within about 2 to 3 mm of the sensor location; after the crack passed the sensor location, the perturbations essentially stabilised. Predicted reflected spectra have been found to be in good agreement with the experiment, confirming that CFBG sensors can detect crack growth in patch-repaired panels.
Armour which is manufactured and distributed for personnel, vehicle and structural protection, primarily for military or policing applications, undergoes stringent testing to ensure that it can meet the demands of a range of impact scenarios. However, the effects of repetitive low-level damage are not fully understood and, in order to maintain a given level of protection, armour is recalled and replaced periodically, which is costly, and may be unnecessary. This paper reports preliminary studies on the relationship between minor damage and the resulting impact resistance of a woven fabric reinforced composite laminate (E-glass with epoxy resin). Specimens were subjected to displacement-controlled fatigue tests to introduce dispersed damage before being subjected to quasi-static indentation testing. The results showed that during penetration of the specimens, the peak load was reduced by approximately 10% for the pre-fatigued specimens, compared to the non-fatigued specimens, and there was some indication the energy absorption also reduced. It is proposed that the development of fibre fractures during the pre-fatigue of the specimens is the origin of these changes.
In this work the tensile properties and failure mechanisms for a knitted fabric reinforced composite has been investigated. Two commercial composites manufactured with Milano 2×68 tex knitted fabric as a reinforcement and Derakane vinyl ester resin as matrix were analysed. The quasi-static behaviour of the materials has been analysed as a function of tested direction, including an investigation of the damage accumulation. Characterization of these materials under tensile loading has been carried out for monotonic and cyclic loading and the results have been compared with those found earlier for a single layer and the sandwich model material with epoxy resin as matrix1. Various failure mechanisms such as cracking at loop cross-over points, resin matrix cracking, fibre bundle debonding and tensile fracture of fibre bundles in failed specimens were observed.
This paper considers the effects of an atmospheric plasma treatment (APT) on the surface properties of an amine cured carbon fibre/epoxy resin composite, and how those effects manifest over time. In particular, the ability of the APT to remove a thin layer of silicone-containing, proprietary, release agent (Chemlease® 41 EZ), typically used in the production of composite components, has been investigated. It was concluded that the reduction in water contact angle (WCA) after APT for both the solvent wiped and contaminated surfaces was as a result of an increase in oxygen containing species at the surface, as determined through X-ray photoelectron spectroscopy (XPS). Further, it was found that the APT slightly reduced the failure strength of lap shear specimens for solvent wiped surfaces, whereas an increase in failure strength was observed for silicone contaminated samples. WCA and XPS results suggest that the contaminant layer was not removed, but instead transformed to a more stable inorganic form.
The thickness of a laminated composite structure can be varied by reducing the number of plies through the thickness of the composite material (i.e. using ply drop-offs), where one or more plies are terminated prematurely at some position within the composite, or at the surface. One of the disadvantages of using ply drop-offs is the likelihood of stress concentrations at the terminations of the dropped plies, as these stress concentrations frequently lead to the premature development of damage. In this work, composite coupons with a double ply drop-off have been fabricated using out-of-autoclave CFRP. Coupons cut from the panels have been subjected to quasi-static and fatigue loading and the development of damage has been monitored using microscopy, and in some coupons, by using a chirped fibre Bragg grating (CFBG) sensor. The first damage appeared as resin cracks within the resin pocket associated with the ply drop-off and this damage developed subsequently into delaminations. Under quasi-static loading, the delaminations grew stably within the ply drop-off region with increasing load; under fatigue loading, the delaminations grew with a constant growth rate. The paper will present observations on the initiation and growth of the damage.
The characterization by DMA and compressive stress-strain behavior of an epoxy resin cured with a number of liquid amines is studied in this work along with predictions of the associated properties using Group Interaction Modeling (GIM). A number of different methods are used to assign two of the input parameters for GIM, and the effect on the predictions is investigated. Excellent predictions are made for the glass transition temperature, along with good predictions for the beta transition temperature and modulus for the majority of resins tested. Predictions for the compressive yield stress and strain are less accurate, due to a number of factors, but still show reasonable correlation with the experimental data. © 2013 Wiley Periodicals, Inc. J. Appl. Polym. Sci. 130: 3130-3141, 2013 Copyright © 2013 Wiley Periodicals, Inc.
A chirped fibre Bragg grating (CFBG) optical sensor has been used to detect delamination growth in an ENF specimen. CFBG sensors, with a sensor length of 60 mm, have been embedded within ENF specimens fabricated from out-of-autoclave CFRP. Delaminations have been propagated within the specimen from an insert embedded at the specimen midplane during manufacture. The sensor has been interrogated with the specimen subjected to four-point loading, and the perturbations detected within the reflected spectra of the sensor are in reasonable agreement with the physical position of the delaminations measured at the coupon edges. The prediction of the reflected spectrum for one delamination length, using a combination of 3-D finite-element analysis and commercial software for predicting FBG spectra, is in qualitative agreement with the experimental results. Better quantitative agreement is expected to require a more refined finite-element model of the ENF specimen.
The growth of transverse ply cracks in composite laminates has been investigated both theoretically and experimentally. Some of the closed-form strain energy release rate based analyses of this problem in the literature have been compared and extensions to these approaches are presented. These models have been shown to be consistent with an alternative approach based on an approximate expression for the stress intensity factor at the tip of a growing transverse ply crack. An experimental study of transverse ply crack growth has been carried out using a simple model array of transverse ply cracks in a glass/epoxy laminate. By making the transverse ply sufficiently thick, the specimen compliance was found to change measurably as individual cracks grow. Hence, the strain energy release rate could be determined experimentally (via the compliance relationship) and compared with analytical predictions. Agreement was found to be satisfactory.
A thermally-assisted piercing (TAP) process has been investigated as an alternative to current methods of machining holes in thermoplastic composites. The spike force/displacement responses during piercing were affected by both the processing temperature and the size of the heated area, as were the resultant microstructure and subsequent mechanical performance. Overall, the results suggest that for advanced manufacturing of thermoplastic composites, good tensile and compressive open-hole properties are produced in the TAP process when using small heated areas and higher temperatures.
Chirped fibre Bragg grating (CFBG) sensors have been embedded within the adhesive bondline of single-lap bonded composite joints, fabricated using a transparent glass fibre reinforced plastic (GFRP) adherend bonded to a carbon fibre reinforced plastic (CFRP) adherend. During fatigue cycling, disbonds initiated adjacent to the cut ends of one, or both, of the adherends and the disbonds propagated with continued fatigue cycling. The results show that the CFBG sensor within the bondline can detect the initiation of the disbond and can also monitor the position of the disbond front as it propagates during fatigue cycling. As the disbond front propagated, there was reasonable agreement between the measurements of the position of the disbond front using the CFBG sensor spectra and photographic measurements of the location of the disbond front taken through the transparent GFRP adherend. This method of monitoring disbonding (with the sensor embedded in the adhesive bondline) could be used to monitor bonded composite structures when it is difficult to embed the sensors within the adherends themselves.
Fibre-reinforced polymer matrix composite materials for engineering structures are now commonplace. Their low densities, combined with high strength and high stiffness, provide many benefits in performance and durability; when combined with the expertise of the current generation of engineers and materials scientists prepared to accept the complexity of designing and fabricating structures using anisotropic materials, the range of applications (from human prosthetics to airplane fuselages) becomes less surprising. Whereas thirty years ago, the majority of high-performance composite materials were manufactured from individual layers of unidirectionally reinforced material, textile-reinforced polymer matrix composites are increasingly used today. This chapter begins with a brief introduction to continuous fibre-reinforced composite materials before describing the various major types of textile-reinforced polymer matrix composite materials based on the following fabric types: two-dimensional woven, braided, knitted, stitched, three-dimensional woven. In each case, an introduction to the mechanical and damage accumulation behaviour, as well as approaches to modelling the composite, are provided.
The ballistic performance of "smart-sized" S2-glass fibre reinforced epoxy was evaluated in comparison with matrix compatible, matrix semi-compatible and matrix incompatible sized materials. The smart size is a formulation designed to give rate-dependent behaviour. The smart-sized material was shown to exhibit rate dependent changes in interlaminar shear strength and mode I interlaminar fracture toughness testing; the ballistic performance of the material was improved only slightly over compatible sized materials. This is attributed to reduced fibre tensile strength in the smart-sized fibres, which was a competing effect, limiting energy absorption during ballistic impact. Overcoming the fibre strength degradations, which appears to be caused by frictional handling effects, is likely to result in significant improvement in ballistic limit. A hybrid laminate consisting of interleaved plies of the compatible and incompatible sizings described above showed synergistic improvements to ballistic performance above what might be expected through rule of mixtures when incompatible sized plies were located towards the rear of the laminate.
An experimental and theoretical study of the effects of 90° ply cracking on the thermal expansion coefficients of crossply laminates has been carried out. It has been found experimentally that reductions in the coefficient of thermal expansion of up to 50% are caused by 90° ply cracks induced mechanically, although considerable care is needed in the experimentation. This behavior was modeled using a simple shear-lag analysis, and the resulting analytical expressions are compared with other approaches available in the literature. The growth of matrix cracks in a model GFRP system under severe thermal cycling (77 to 373 K) is investigated. The changes in expansion coefficient are affected by the growth of 0° ply cracks in addition to the 90° ply cracks. The crack growth rate/cyclic strain energy release rate range data are compared with those reported previously for mechanical fatigue cycling of similar material. The two data sets are consistent if plotted in terms of a fracture mechanics parameter which aims to account for the temperature dependence of material properties.
Composite sandwich structures are well-suited for applications requiring high bending strength, flexural rigidity, crashworthiness, and light weight. However, skin-core debonding and core failure remain a barrier to optimal structural performance when polymeric foams are used as core materials. Suppressing or compartmentalising these failure modes can enhance the structural integrity of sandwich structures. In this paper, the flexural response of a sandwich structure was improved by adding carbon fibre-reinforced plastic in the form of through-thickness ribs during the manufacturing process. The effect of the position of the ribs was investigated using a quasi-static three-point bend test. A camera was used to capture failure events, while the digital image correlation technique provided the full-strain field at different stages of loading. Improved flexural performance was obtained when a reinforcement was placed on either side of the loading roller. With this configuration, skin-core debonding was restricted to a confined portion of the panel, resulting in a more localised and stable fracture process, which involved enhanced foam crushing and hardening. A simple FEA approach has been adopted in this paper and has proven to be an effective approach for capturing the details of the failure process, including the debonding in the composite foam structures, without the need for complex and computationally expensive interface modelling.
Digital Image Correlation (DIC) can be used to obtain full-field strain information of specimens under load. Through analysis of the resultant strain-contours, defects such as delaminations in composite materials can be detected based on their effect on the deformation behaviour. This paper focuses on the use of DIC to detect the presence of fully embedded artificial delaminations, introduced during the manufacturing process, inside a flat panel specimen under three-point bending. Two types of delamination insert have been considered: an insert containing two sealed pieces of PTFE, and an insert consisting of a single sheet of PTFE in combination with a stress-raiser. When tested in three-point bending, the position and approximate size of the delaminations were clearly visible due to the presence of a plateaux in the longitudinal surface strain profile. Finite element modelling predictions were in good agreement with the DIC measurements for both types of artificial delamination.
The growth of individual transverse ply cracks during tension-tension fatigue of (0/90//2)s GFRP and (0/90//3)s CFRP has been observed using transmitted light and penetrant enhanced X-radiography, respectively. The growth rate of cracks in both laminates is independent of crack length but depends on the spacing between the cracks. Very low growth rates occur for small crack spacings or if crack branching occurs. The results are interpreted using a stress intensity factor approach.
The results presented in this paper explore the extent to which indentation in the interfacial region of polymer composites can be used to identify, unambiguously, an interphase of distinct elastic properties. Supporting evidence is presented in the form of atomic force microscopy indentation in the interfacial region of two polymer composites, a glass fibre reinforced vinylester and a glass flake reinforced polypropylene, where a transition region of measurement artefact is revealed as opposed to a physically distinct interphase. The conclusions from these tests are augmented by further work on a glass fibre reinforced phenolic using a new in situ method of identifying measurement artefacts.
Recent work has shown that a simple rule-of-mixtures approach may be used to predict the stress-strain behaviour of a cross-ply metal matrix composite laminate. However, the low-strain behaviour was not predicted accurately, probably because thermal residual stresses are obviously not included in such an approach. To increase the understanding of the limitations of the rule-of-mixtures approach for predicting the stress-strain response, the residual strain-state of the fibre reinforcement has been determined using an etching technique (henceforth referred to as the 'total etch removal method'), and results have been compared both with finite element modelling and with thermal residual strain measurements derived from stress-strain curves. The results show that the residual strain distribution in a cross-ply composite may be more complex than previously thought, with the fibres in internal 0 degrees plies having considerably higher thermal residual strains than fibres in external plies. The results confirm that the rule-of-mixtures approximation can be used, with some reservations with regard to the low-strain behaviour.
This chapter provides an introduction to the generic types of constituents, manufacturing defects and in-service defects to be found in composite materials based on continuous fibres. First, the basic composite constituents are outlined. Next, fibre/matrix debonding, matrix cracking damage, fibre fractures and delaminations are discussed for simple fibre architectures in order to introduce some basic ideas relating to damage accumulation. Subsequent chapters of the book deal with more complex fibre architectures and/or types of loading, and elaborate on the strategies used for modelling damage accumulation.
Debonding between the skins and the core in a sandwich structure is a critical failure mode in automotive applications; once debonding occurs, the load carrying capacity of a sandwich structure drastically decreases. In the present paper, the effect of using three core materials, with different cell characteristics, on the interfacial strength between the foam cores and a CFRP skin is investigated through mechanical testing and numerical modelling. A key finding is that foams with a coarse cellular structure favour a high resin uptake at the interface during the manufacturing process, which results in a stronger interfacial bonding between the foam and the CFRP. During Mode I loading, the thick resin layer at the interface postpones crack initiation and kinking in the core, whilst under Mode II, this resin layer delays the collapse in compression of foam cells under the crack tip. Thus, the importance of including this thick resin layer in the FE modelling was demonstrated. Finally, as the CZM was shown to be unable to predict the unstable crack propagation within the core, an alternative approach was suggested which has the significant benefit of not requiring experimental testing of the interface between the skin and the core.
This paper outlines preliminary work developing graphene modified thermoplastic inserts to be used for the toughening of CFRP. The paper outlines laminate manufacture, mechanical testing and fracture analysis of graphene modified CFRP.
Dielectrophoresis (DEP) is a physical effect that generates a force on polarisable particles experiencing a non-homogeneous electric field; studying the effect as a function of frequency allows the determination of the electrical properties of that particle, i.e. the electrical permittivity and conductivity. In the past, DEP-based techniques applied to the measurement of one or several cells at a time have been subject to many sources of noise, which result in an ambiguous or inaccurate result. However, improvements are possible by generating more information from the experiments. In this paper, we present a rapid automated system that measures the DEP spectrum from a large population of cells with a low level of noise using the microwell electrodes, based on a method of analysis that provides additional information about the electrical properties of the cells and a new theoretical approach was developed to obtain accurate, bias-free results in
The effect of braid angle and number of axial tow insertions on the behavior of flattened tubular braided composites (carbon fibre/epoxy resin) has been investigated. Two type of braids i.e. bi-axial and tri-axial (i.e. 6 and 12 inserted axial tows), for three braid angles (35°, 45° and 55°), have been studied. The stress–strain curve for the bi-axial braided composites is pseudo-ductile in nature, with a smooth transition into a plateau region at low strains, accompanied by necking of the composite. By contrast, the tri-axial braided composites show an initially high peak stress, related to the deformation and fracture of the axial tows, and subsequent plateau-like behaviour accompanied by neck formation, the extent of which appears to be determined by the strain-to-failure of the composite. For the bi-axial braids, an increase in braid angle produced decreased strength, axial modulus and specific energy absorption, but an increase in strain to failure. Inserted axial tows produced increased strengths and Young’s moduli, but a decrease in specific energy absorption (except for 55°) and strain to failure. In all cases, the braided composites outperformed the specific energy absorption of aluminium.
During the quasi-static indentation of thin composite panels, well-defined flaps (sometimes called ‘‘petals’’) can develop on the exit face as a consequence of through-thickness penetration of the panel; such flaps can also be seen in impact tests. The flaps develop as four triangles, with the apex of each triangle at the point of impact. In this work, thin panels of CFRP with a 0/90 configuration have been subjected to quasi-static indentation tests and the development of the flaps has been monitored. The results show that the dependence of the flap compliance is proportional to the square of the flap length, which is in agreement with theoretical predictions. The determination of the compliance/crack-length relationship enables a toughness value for fracture of the composite panel to be derived that is directly relevant to through-thickness penetration of the panel.
This study describes a novel and versatile method of incorporating graphene nano-platelets (GNP) into compos-ite laminates to investigate its effect on mode I and mode II interlaminar fracture toughness (ILFT). Non-woventhermoplastic veil interleaves have been modified by spray deposition with a GNP dispersion to give either a con-tinuous or strip-patterned distribution. The coated interleaves were used to modify the interlaminar region ofcarbonfibre reinforced polymer (CFRP) laminates. The fracture surfaces were characterised by scanning electronand optical microscopy.The continuous GNP distribution in mode I prevented the formation of carbonfibre bridging, resulting in similarinitiation and propagation values. In mode II, the increased thickness of the interlaminar region, coupled with theuneven fracture surface showed the highest increase in the mode II ILFT for the continuous GNP distribution. Thestrip-patterned GNP distribution showed reduced carbonfibre bridging compared to the baseline CFRP and ther-moplastic interleave laminates. This may be due to small scalefibre bridging between the deposited GNP-stripswhich also lead to peaks and troughs in the load-displacement response. In mode II, it is suggested that the de-posited GNP-strips were sufficiently tough to re-direct the propagating crack from the modified interlaminar re-gion to the adjacent ply.
The choice of the materials used for the core and skin of a sandwich structure plays an extremely important role in the skin-core interfacial behaviour. In this paper, three PMI foams are used as core material and the effect of foam type in the skin-core interfacial response is examined.
Three measurement techniques used to measure the glass transition temperature (Tg) have been subjected to a critical comparison; dynamic mechanical analysis (DMA), thermomechanical analysis (TMA) and differential scanning calorimetry (DSC). A new procedure, whereby different specimens are tested over a range of heating rates, has been used in order to eliminate the effects of thermal lag and determine a Tg independent of heating rate (Tg(0)). It has been shown that for measurements of Tg(0) for composites, the DMA thermal lag ‘corrected’ method gave the most reliable data. The work has provided additional guidance on these techniques that could usefully be incorporated in future standards, to improve precision, comparisons and consistency of Tg measurement.
Delamination growth within transparent, unidirectionally reinforced glass fibre/epoxy doublecantilever beam (DCB) specimens has been monitored using a surface-mounted chirped fibre Bragg grating (CFBG) sensor. The specimens were tested using a constant displacement rate, with the delamination length being measured using (i) surface-mounted CFBG sensors, (ii) in situ photography, and (iii) surface-mounted strain gauges. The DCB specimens showed characteristics typical of such material, with the development of extensive fibre bridging and pronounced R-curve behaviour. A distinct perturbation in the reflected spectra, when monitoring the delamination growth using the CFBG sensors, was indicative of the location of the delamination front during the test. The in situ photographs and the surface strain measurements provided by the strain gauges were used to predict the experimentally determined CFBG reflected spectra, with good agreement between prediction and experiment. These results enabled the delamination length to be measured using the CFBG sensor technique to within 4 mm over the 60 mm sensor length.
During the impact of thin composite panels, well-defined flaps can develop on the exit face as a consequence of through-thickness penetration of the panel. For certain materials (for example, CFRP panels based on plies of plain-woven fabric) the flaps develop as four triangles, with the apex of each triangle at the point of impact. As the impactor is driven through the panel, the flap (i.e. crack) lengths increase, until complete penetration of the panel by the impactor occurs. In the experiments described within this paper, CFRP panels fabricated from epoxy resin reinforced with plain-woven carbon fibre fabrics have been impacted using controlled multiple impact tests. During these tests, the impactor is driven at a controlled velocity to a particular depth of penetration through the composite panel, withdrawn, and then driven further through the panel subsequently. The experimental results show that the dependence of the flap compliance is proportional to the square of the flap length, which is in agreement with theoretical predictions. This compliance/crack-length also enables a toughness value for the composite panel to be derived that is directly relevant to through-thickness impact. The relationship of this toughness value to measurements of the mode I toughness of the composite panel using single edge notch specimens is also discussed.
There has been extensive development in the offshore and marine industries of the use of polymer composite materials and understanding the durability of these materials is a significant challenge. Numerous test methods exist for the accelerated ageing of polymeric materials at the laboratory scale, but tests employing a combination of exposure conditions (e.g. at elevated temperature, under pressure, under a mechanical load) are lacking. In this work elevated temperatures are used to accelerate the ageing of polymer composite specimens when exposed to different combinations of immersion in water, pressure and mechanical loading. The results show that the behaviour of the material exposed to different combinations of exposure conditions, produces changes in residual properties (i.e. flexural modulus flexural strength and Tg) which are complex. Of immediate significance to understanding the behaviour of composites in a marine environment is the observation of a very significant decrease in the rate of moisture absorption for specimens tested under a pressure of 300 bar.
Model sandwich laminates were manufactured by orienting the knitted cloth at a range of angles to the loading direction using a single Milano weft knitted layer sandwiched between outer plies of unidirectional glass reinforced epoxy resin in order to be able to observe progressive damage accumulation along the sample. By this way, the relationship between fibre architecture and damage accumulation under tensile loading, as well as the sequence of damage accumulation has been investigated. Damage has been found to initiate at the loop cross-over points of the knitted fabric structure for all orientations, although the further development of the damage depends on the orientation of the fabric to the applied load. The resultant transparent laminates provide a novel method of monitoring the damage development in a knitted-fabric composite as a function of increasing strain by allowing direct observation of the sequence of damage.
PeakForceTM quantitative nanomechanical mapping (QNMTM) is a new atomic force microscopy technique for measuring Young's modulus of materials with high spatial resolution and surface sensitivity by probing at the nanoscale. In this work, modulus results from PeakForce™ QNM™ using three different probes are presented for a number of different polymers with a range of Young's moduli that were measured independently by instrumented (nano) indentation testing (IIT). The results from the diamond and silicon AFM probes were consistent and in reasonable agreement with IIT values for the majority of samples. It is concluded that the technique is complementary to IIT; calibration requirements and potential improvements to the technique are discussed.
Shape-memory alloy composites are relatively new materials and their behaviour is not yet completely understood. The purpose of this work is to minimise the effect of impact damage on their structural performance. To do that, GFRP woven fabric reinforced epoxy composite panels, with and without additional superelastic shape-memory alloy wires, have been impacted at constant velocities using a servo-hydraulic testing machine, and a digital video camera has been used to monitor the impact event. Single, multiple and partial penetration impact tests have been carried out, and the energy absorption and damage development are similar in all cases for the same material. The benefit of using the superelastic shape-memory alloy wires was seen only at high displacements and when the volume fraction of the wires was high
Matrix cracking in composite laminates is the first macroscopic damage mode to be readily detected. Polarimetric sensors embedded in composite laminates can detect the development of this damage and they have an advantage over other sensors in being able to sense damage over long gauge lengths (potentially, many metres). In this paper, the sensitivity of a polarimetric sensor manufactured from Hi-Bi PANDA fibre has been measured experimentally and a phase-strain model available in the literature has been used to determine the characteristic parameters of the sensor. The sensitivity of such sensors embedded in unidirectional composites is shown to be in good agreement with theoretical predictions, allowing for material non-uniformity. In the case of cross-ply laminates, which are transversely anisotropic, it is shown that sensor sensitivity is dependent on the relationship of the sensor axes to the composite axes, as well as on the degree of sensor twist. Maximum sensitivity is obtained for a combination of low twist angle and congruence between the sensor optical axes and the composite axes. Twist angles of greater than 90° give rise to sensitivities, which, although lower, are reasonably constant and approximately the same as the sensitivity of the sensor in a unidirectional composite.
Recent work has shown that a simple rule-of-mixtures approach may be used to predict the stress strain behaviour of a cross-ply metal matrix composite (MMC) laminate. However, the low-strain behaviour was not predicted accurately, probably because thermal residual stresses are obviously not included in such an approach. To increase the understanding of the limitations of the rule-of-mixtures approach for predicting the stress-strain response, the residual strain-state of the fibre reinforcement has been determined using an etching technique (henceforth referred to as the ‘total etch removal method’), and results have been compared both with finite element modelling and with thermal residual strain measurements derived from stress-strain curves. The results show that the residual strain distribution in a cross-ply composite may be more complex than previously thought, with the fibres in internal 00 plies having considerably higher thermal residual strains than fibres in external plies. The results confirm that the rule-of-mixtures approximation can be used, with some reservations with regard to the low strain behaviour.
Simple analytical models are applied in order to explore the relationship between notched and unnotched strength of CFRP laminates under a range of test conditions – cold dry, room temperature, and hot/wet. The methodology adopted makes use of a stress-based approach for predicting damage growth, in conjunction with a fracture mechanics model for ultimate failure/fracture. Applying the resulting model to the experimental data enables the fracture toughness of the test material to be determined as a function of test condition. The model is also able to demonstrate that at any particular test condition, a given variability in unnotched strength data translates into a smaller variability in the associated notched strength data.
Late-stage fatigue damage of an E-glass/epoxy 3D orthogonal non-crimp textile composite loaded in the warp direction has been investigated using a combination of mechanical testing, X-ray micro computed tomography (μCT), optical microscopy and finite element modelling. Stiffness reduction and energy dissipated per cycle were found to be complementary measurements of damage accumulation, occurring in three stages: a first stage characterised by rapid changes, a more quiescent second stage, followed by a third stage where the (decreasing) stiffness and (increasing) energy dissipation change irregularly and then rapidly, to failure. Microscopy of specimens cycled into the transition between the second and third stages showed macroscopic accumulations of fibre fractures in sections of warp tows which lying adjacent to the surface weft tows which are crowned-over by the Z-tows. At these locations, the warp tow fibres are subjected to stress concentrations both from transverse weft tow matrix cracks and resin pocket cracks.
Digital Image Correlation (DIC) can be used to obtain full-field strain information on specimens under load. Through analysis of the resultant strain-contours, defects such as delaminations in composite materials can be detected, based on their effect on the deformation behaviour. This work focusses on the use of the DIC technique and two variations of active thermography (lock-in thermography and pulse thermography) for determining the lengths of delaminations in “milled-slot” specimens; for each technique, the measured delamination lengths have been compared with visually observed (i.e. photographed) delaminations grown under fatigue loading in transparent woven fabric GFRP specimens. In addition, the DIC results have been interpreted with the aid of a finite element model of the strain distribution in the milled-slot specimens. It has been found that the DIC technique provides a reasonably good method for measuring the length of the fatigue-grown delaminations after an empirical fit is applied, with the aid of the FE analysis, to overcome complications caused by fibre-bridging. On the other hand, the results using both lock-in and pulse thermography showed reasonable correlations with the visually observed (i.e. photographed) delamination lengths without the need for an empirical fit, although some post-processing of the data was required. For both thermography techniques, there were difficulties in determining the delamination lengths close to the edge of the milled slot.
The choice of the materials used for the core and skin of a sandwich structure plays an extremely important role in the skin-core interfacial behaviour. In this paper, three PMI foams are used as core material and the effect of foam type in the skin-core interfacial response is examined.
A surface-mounted chirped fibre Bragg grating (CFBG) sensor has been used for the first time to monitor delamination growth within a composite material (a transparent, unidirectionally reinforced glass fibre/epoxy resin double-cantilever beam (DCB) specimen). The specimens were tested using a constant displacement rate, with the delamination length being measured using complementary techniques: (i) in situ photography, (ii) surface-mounted strain gauges, and (iii) the surface-mounted CFBG sensors. The unidirectionally reinforced DCB specimens showed characteristics typical of such material which complicate the curvature of the beams, i.e. the development of extensive fibre bridging and pronounced R-curve behaviour. To validate the interpretation of the CFBG reflected spectrum, the experimentally determined strains from the surface-mounted strain gauges have been used, together with in situ photographs of the position of the delamination front. Using the CFBG sensor technique, the delamination length was measured to within about 4 mm over the 60 mm sensor length.
Polymer composite materials are widely used in marine applications where an understanding of the long-term performance is essential for economic, safety and durability requirements. Although moisture absorption in composites has been studied for many years, the relationship between the mechanisms of moisture absorption and consequent changes in material behaviour has received much less attention. Understanding degradation is necessary for developing lifetime assessments. In this work, long-term exposure of a unidirectional carbon fibre epoxy composite material in water has been investigated in relation to mechanical property changes and moisture uptake. Using diffusion modelling and microscopy of the fracture surfaces, it is possible to correlate water absorption to experimental data showing how the position of water in the material causes changes to flexural properties (modulus decreased by 14% and strength by 20%) and in the glass transition temperature, T g reduced by 18%. Flexural modulus has been shown to be most affected by water interaction with the fibre interface; T g by water interaction within the resin; and flexural strength equally by water interaction with both fibre interface and resin.
Matrix ply cracking is the most common damage to form when a laminate is loaded, and is of considerable significance for the integrity of a composite structure. The overall aim of the present work is to provide validated constitutive relations for crack accumulation in off-axis plies under mixed mode loading. The results presented in this paper include experimental investigations to describe the development of the cracking and the development of finite element-based models of cracked laminates. The effect of matrix cracking on the residual stiffness of various laminates is determined both experimentally and using finite element simulation. The ratio of modes in different angle ply laminates and the associated criteria for matrix crack initiation are explored.
This paper presents an experimental and numerical study on the structural health monitoring of composite patch repairs using chirped fibre Bragg grating (CFBG) sensors. The repair consisted of bonding a pre-cured patch of the same, but thinner, material to a parent GFRP panel containing a machined hole, with the sensors embedded in the bond-line. The repaired coupons were subjected to four-point flexural loading in fatigue. Bond-line delamination cracks (disbonds) initiated at both ends of the patch repair and grew towards the centre of the repair. Predictions of the strain distributions enabled the reflected spectra obtained during damage growth to be predicted with good agreement between theory and experiment. For practical applications when using CFBG sensors to monitor patch repairs, the results suggest that two sensors should be included within the bond-line so that both vulnerable edges of the repair can be monitored using the low-wavelength end of a sensor.
This paper details a quality control test for polymeric composite interfaces independent of reinforcement type and geometry. Experimentation has shown the capability of AFM indentation in characterising interfacial mechanical property variation with focus on measurement quantification to produce elastic modulus maps at the micro- and nano-scale
This thesis focuses on the subject of damage in composite materials and structures, in particular delaminations arising from an impact event and subsequent Mode I and Mode II loading and fatigue delamination growth. Interlaminar fracture toughness values have been calculated from an experimental study for DCB and ENF specimens. Specimens with artificial inserts at two different interfaces were used along with specimens with delaminations introduced from an impact event. The standard analysis method for both Mode I and Mode II has been adapted to account for the delamination away from the mid plane. For Mode I loading, the load to initiate delamination growth from experimental results is in good agreement with the predicted results from the adapted Mode I equation. For Mode II loading, crack migration did not appear obvious from the experimental study, and an adapted equation accounting for delaminations away from the mid plane has been successfully used. A fatigue study on a structural element loaded both in-plane and out of plane has highlighted the complex nature of damage growth in composite structures. The study has highlighted the issues of delamination investigation using the ultrasonic NDT technique, whereby non-critical delamination growth is sometimes masked by the more dominant delamination and as such the complex growth of delaminations within a structure is difficult to quantify using this technique.
In this paper it is shown that a chirped fibre Bragg grating sensor embedded within a composite adherend can be used to monitor disbond initiation and propagation in an adhesively bonded single lap-joint. Characteristic changes in the reflected spectra from the sensor indicate both disbond initiation and the current position of the disbond front to within about 2 mm (a distance which depends on adherend material and sensor position in relation to the adhesive bondline). When the sensor extends the full overlap length, disbond initiation from either end of the overlap can be monitored. The results have been modelled using a combination of finite-element analysis and commercial software for predicting FBG spectra; the predicted spectra are in very good agreement with experiment. The CFBG sensor technique could provide the basis for monitoring a wide range of bonded joints and structures where one adherend is a composite material.