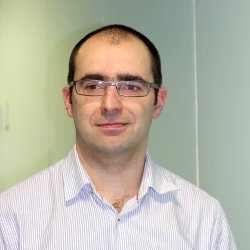
Dr Simão Marques
ResearchResearch interests
My research focuses on computational methods for aerodynamic and aeroelastic analysis and design.
My primary research objective is to develop advanced high-fidelity methods for the analysis and design of aerospace vehicles. To reach this objective, I am currently developing algorithms and numerical methods on the following topics:
- CFD development.
- High-Fidelity Aeroelastic Analysis.
- Multidisciplinary Optimization algorithms
- Uncertainty Quantification
Research projects
ONEheartThe ONEheart project has received funding from the UK Aerospace Technology Institute (ATI) (https://www.ati.org.uk/) in collaboration with AIRBUS Operations Ltd (Innovate UK proposal number 10003388)
Dynamically parameterising CAD models using sensitivities for optimisationTo design complex products, engineers need to consider and optimise many different attributes. In aerospace, optimisation mainly considers both structural (e.g. displacements, accelerations) and fluid (e.g. pressures acting on a body) attributes. One of the main factors which can impact performance is product shape, which affects a number of disciplines. When changing the shape of the design the options are to change the analysis model (i.e. a mesh) or the geometry model which represents the design. The preferred option is to optimise the geometry model as the result is integrated with the wider design enterprise (e.g. it can also be used for manufacturing considerations). This is particularly true if the geometry model is a feature based CAD model (e.g. Catia V5 or Siemens NX). In a feature based CAD system, the object shape is modified using the parameters which define the features that make up the model itself.
One challenge is that the variables which define the shape of the design and control how it can change, may not actually be well suited for the disciplines driving the optimisation. This means that regardless of how much effort the optimiser puts in, it will not be possible to reach a truly optimum design. This three year project will ensure the parameterisation is suited to optimisation by investigating robust methodologies to automatically insert new features into the CAD model, for which the associated parameters will be new optimisation variables. This will rely on robust and efficient new methods for computing multi-disciplinary sensitivities. The project benefits from collaboration with a major UK industrial partner (Airbus) and developers of key analysis software (DLR). They will assist in researching a new capability with the overall aim of "delivering a step change in the configuration, time to market and performance of new designs." The following objectives have been set:
1. Implement strategies for improving CAD parameterisations for multi-disciplinary optimisation by automatically inserting features into the model based on sensitivity.
2. Investigate efficient and robust methodologies for computing aero-structural sensitivities. This will see a novel approach to the calculation of the sensitivities.
3. Develop strategies for coupling and coherently meshing solid and fluid models. This is a key piece of research required in any aero-structural analysis.
4. Combine aero-structural sensitivities with CAD parameterisation strategies, in an automated optimisation framework, for a range of test cases. This is where the benefits of the work will be demonstrated to industry.
5. Quantify the decrease in time to market and increase in performance due to this research.
Application areas for this research include the design of products which require the optimisation of complex shapes. It will be particularly relevant in industries where feature based CAD systems underpin the design process, and where the physics of the problem may identify the need for shape features which may not be apparent when the CAD models are being setup. An example may be where the surface sensitivities suggest the need for a winglet, but where the parameterisation of a basic wing does not include the parameters to allow such a feature to form. Benefits include:
1. the ability to discover new, optimum, configurations. This is a route to innovative design solutions which will help to keep the UK as a world leader in the design and manufacture of complex products;
2. improved product performance due to the improved optimisation variables (CAD parameters) created based on the requirements of the physics of the problem. For air travel this will result in more environmentally friendly aircraft and lower travel prices;
3. reduced development times due to an automated and efficient optimisation processes, leading to new, better performing, products being available sooner;
Funding Agency: EPSRC EP/P025692/1
Research collaborations
- Queen's University Belfast
- DLR
- Airbus
Research interests
My research focuses on computational methods for aerodynamic and aeroelastic analysis and design.
My primary research objective is to develop advanced high-fidelity methods for the analysis and design of aerospace vehicles. To reach this objective, I am currently developing algorithms and numerical methods on the following topics:
- CFD development.
- High-Fidelity Aeroelastic Analysis.
- Multidisciplinary Optimization algorithms
- Uncertainty Quantification
Research projects
The ONEheart project has received funding from the UK Aerospace Technology Institute (ATI) (https://www.ati.org.uk/) in collaboration with AIRBUS Operations Ltd (Innovate UK proposal number 10003388)
To design complex products, engineers need to consider and optimise many different attributes. In aerospace, optimisation mainly considers both structural (e.g. displacements, accelerations) and fluid (e.g. pressures acting on a body) attributes. One of the main factors which can impact performance is product shape, which affects a number of disciplines. When changing the shape of the design the options are to change the analysis model (i.e. a mesh) or the geometry model which represents the design. The preferred option is to optimise the geometry model as the result is integrated with the wider design enterprise (e.g. it can also be used for manufacturing considerations). This is particularly true if the geometry model is a feature based CAD model (e.g. Catia V5 or Siemens NX). In a feature based CAD system, the object shape is modified using the parameters which define the features that make up the model itself.
One challenge is that the variables which define the shape of the design and control how it can change, may not actually be well suited for the disciplines driving the optimisation. This means that regardless of how much effort the optimiser puts in, it will not be possible to reach a truly optimum design. This three year project will ensure the parameterisation is suited to optimisation by investigating robust methodologies to automatically insert new features into the CAD model, for which the associated parameters will be new optimisation variables. This will rely on robust and efficient new methods for computing multi-disciplinary sensitivities. The project benefits from collaboration with a major UK industrial partner (Airbus) and developers of key analysis software (DLR). They will assist in researching a new capability with the overall aim of "delivering a step change in the configuration, time to market and performance of new designs." The following objectives have been set:
1. Implement strategies for improving CAD parameterisations for multi-disciplinary optimisation by automatically inserting features into the model based on sensitivity.
2. Investigate efficient and robust methodologies for computing aero-structural sensitivities. This will see a novel approach to the calculation of the sensitivities.
3. Develop strategies for coupling and coherently meshing solid and fluid models. This is a key piece of research required in any aero-structural analysis.
4. Combine aero-structural sensitivities with CAD parameterisation strategies, in an automated optimisation framework, for a range of test cases. This is where the benefits of the work will be demonstrated to industry.
5. Quantify the decrease in time to market and increase in performance due to this research.
Application areas for this research include the design of products which require the optimisation of complex shapes. It will be particularly relevant in industries where feature based CAD systems underpin the design process, and where the physics of the problem may identify the need for shape features which may not be apparent when the CAD models are being setup. An example may be where the surface sensitivities suggest the need for a winglet, but where the parameterisation of a basic wing does not include the parameters to allow such a feature to form. Benefits include:
1. the ability to discover new, optimum, configurations. This is a route to innovative design solutions which will help to keep the UK as a world leader in the design and manufacture of complex products;
2. improved product performance due to the improved optimisation variables (CAD parameters) created based on the requirements of the physics of the problem. For air travel this will result in more environmentally friendly aircraft and lower travel prices;
3. reduced development times due to an automated and efficient optimisation processes, leading to new, better performing, products being available sooner;
Funding Agency: EPSRC EP/P025692/1
Research collaborations
- Queen's University Belfast
- DLR
- Airbus
Publications
A novel surrogate model is proposed in lieu of computational-fluid-dynamics solvers, for fast nonlinear aerodynamic and aeroelastic modeling. A nonlinear function is identified on selected interpolation points by a discrete empirical interpolation method. The flowfield is then reconstructed using a least-square approximation of the flow modes extracted by proper orthogonal decomposition. The aeroelastic reduced-order model is completed by introducing a nonlinear mapping function between displacements and the discrete empirical interpolation method points. The proposed model is investigated to predict the aerodynamic forces due to forced motions using a NACA 0012 airfoil undergoing a prescribed pitching oscillation. To investigate aeroelastic problems at transonic conditions, a pitch/plunge airfoil and a cropped delta wing aeroelastic models are built using linear structural models. The presence of shock waves triggers the appearance of limit-cycle oscillations, which the model is able to predict. For all cases tested, the new reduced-order model shows the ability to replicate the nonlinear aerodynamic forces and structural displacements and reconstruct the complete flowfield with sufficient accuracy at a fraction of the cost of full-order computational-fluid-dynamics model.A novel surrogate model is proposed in lieu of computational-fluid-dynamics solvers, for fast nonlinear aerodynamic and aeroelastic modeling. A nonlinear function is identified on selected interpolation points by a discrete empirical interpolation method. The flowfield is then reconstructed using a least-square approximation of the flow modes extracted by proper orthogonal decomposition. The aeroelastic reduced-order model is completed by introducing a nonlinear mapping function between displacements and the discrete empirical interpolation method points. The proposed model is investigated to predict the aerodynamic forces due to forced motions using a NACA 0012 airfoil undergoing a prescribed pitching oscillation. To investigate aeroelastic problems at transonic conditions, a pitch/plunge airfoil and a cropped delta wing aeroelastic models are built using linear structural models. The presence of shock waves triggers the appearance of limit-cycle oscillations, which the model is able to predict. For all cases tested, the new reduced-order model shows the ability to replicate the nonlinear aerodynamic forces and structural displacements and reconstruct the complete flowfield with sufficient accuracy at a fraction of the cost of full-order computational-fluid-dynamics model.
This work proposes a novel approach to compute transonic Lim
it Cycle Oscillations
(LCOs)
using high fidelity analysis. CFD based Harmonic Balance
(HB)
methods have
proven to be efficient tools to predict periodic phenomena. Th
is paper’s contribution
is to present a new methodology to determine the unknown freq
uency of oscillations,
enabling HB methods to accurately capture
LCOs
; this is achieved by defining a fre-
quency updating procedure based on a coupled CFD/CSD (Compu
tational Structural
Dynamics) HB formulation to find the LCO condition. A pitch/p
lunge aerofoil and
delta wing aerodynamic and respective linear structural mo
dels are used to validate
the new method against conventional time-domain simulation
s. Results show con-
sistent agreement between the proposed and time-marching me
thods for both LCO
amplitude and frequency, while producing at least one order
of magnitude reduction
in computational time.
The Harmonic Balance method is an attractive solution for computing periodic responses and can be an alternative to time domain methods, at a reduced computational cost. The current paper investigates using a Harmonic Balance method for simulating limit cycle oscillations under uncertainty. The Harmonic Balance method is used in conjunction with a non-intrusive polynomial-chaos approach to propagate variability and is validated against Monte Carlo analysis. Results show the potential of the approach for a range of nonlinear dynamical systems, including a full wing configuration exhibiting supercritical and subcritical bifurcations, at a fraction of the cost of performing time domain simulations.
Over the past decade the Harmonic-Balance technique has been established as a viable alternative
to direct time integration methods to predict periodic aeroelastic instabilities. This article reports the
progress made in using a frequency updating procedure, based on a coupled fluid-structural solver using the Harmonic-Balance
formulation. In particular, this paper presents an efficient implicit time-integrator that accelerates the convergence of the structural equations of motion to
the final solution. To demonstrate the proposed approached, the paper includes a detailed investigation of the impact of input parameters and exercises the
method for two types of fluid-structural nonlinear instabilities: transonic limit-cycle oscillations and vortex-induced vibrations.
An Aeroelastic-Harmonic Balance (A-HB) formulation of the Euler flow equations using a high-order spatial discretization scheme coupled with structural dynamic equations is proposed. The main objective of this new approach is to dramatically reduce the computational cost required to predict unsteady, periodic problems such as limit cycle oscillations (LCO). To this end, a new solver based on the Monotonicity Preserving limiter together with the AUSM+-up flux function is developed for the harmonic balance equations. The use of high-order CFD schemes allows the reduction of the number of degrees of freedom required to achieve a given desired accuracy, with respect to lower order schemes. In this paper, the reduction in degrees of freedom of the fluid system is exploited in the context of a CFD based Harmonic-Balance framework using a frequency updating procedure to determine the limit cycle conditions. The standard A-HB methodology has shown over one order of magnitude speed-up over time-marching methods; by employing the proposed high-order scheme in conjunction with coarser grids, the LCO computational time is halved without compromising accuracy.