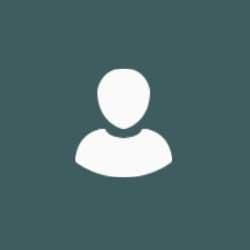
Dr Salvatore De Lellis
About
My research project
Uncertainty Investigation in Microvibration PredictionsThe aim of this project is the investigation of the effects of structural uncertainties in microvibration predictions. In particular, source-related and transfer function-related variability on the satellite are studied in order to account for both contributions in the analysis.
Supervisors
The aim of this project is the investigation of the effects of structural uncertainties in microvibration predictions. In particular, source-related and transfer function-related variability on the satellite are studied in order to account for both contributions in the analysis.
University roles and responsibilities
- Responsible for Environmental Testing (Shock and Vibration)
My qualifications
Salvatore obtained his Bachelor Degree in Aerospace Engineering (2014) and Master Degree in Space Engineering (2016) from Politecnico di Milano. He then started his PhD at Surrey Space Centre (University of Surrey) in October 2016.. His research is mainly interested in microvibration characterisation and analysis. His research involves the study of microvibration source mechanisms, such as Reaction Wheel, and the evaluation of their effects on the performance of the satellite. In addition, he is also interested in the quantification of structural uncertainties and the development of a reliable and cost-effective tool for their predictions.
His doctorate project is sponsored by Surrey Satellite Technology Limited (SSTL) and Airbus DS
ResearchResearch projects
Uncertainty Investigation in Microvibration PredictionsThe aim of this project is the evaluation of the effects of structural uncertainties on microvibration predictions. The main source devices generating microvibrations are analysed and their effects are studied. Variability of the satellite structure is also taken into account and the main uncertain parameters are modelled and investigated.
Research collaborations
The PhD project is in collaboration with Surrey Satellite Technology Limited (SSTL) and Airbus DS.
Research projects
The aim of this project is the evaluation of the effects of structural uncertainties on microvibration predictions. The main source devices generating microvibrations are analysed and their effects are studied. Variability of the satellite structure is also taken into account and the main uncertain parameters are modelled and investigated.
Research collaborations
The PhD project is in collaboration with Surrey Satellite Technology Limited (SSTL) and Airbus DS.
Teaching
Teaching Assistant in the following modules:
- Structural Mechanics and Analysis (ENG 2103) - October 2016 to January 2017
- Solid Mechanics 2 (ENG 2088) - October 2016 to January 2017
- Aircraft Structures & Materials (ENG 2096) - April 2017 to June 2017
- Solid Mechanics 2 (ENG 2088) - October 2017 to January 2018
- Solid Mechanics 1 (ENG 1066) - April 2018 to June 2018
- Advanced Stress Analysis (ENG 3171) - February 2019 to -
Publications
Due to constantly increasing requirements for more precise and high-resolution instrumentations, microvibration prediction represents an issue of growing importance. Hence the need of reliable analysis tools which can evaluate microvibrations effects efficiently. This paper describes how to tackle the issue of structural uncertainties in microvibration predictions. In particular, uncertainties related to the microvibration sources are analysed as well as those linked to the modelling of the structure. A methodology to define the worst case of vibration produced by on board sources is presented and compared to experimental data. Additionally, an approach to quantify the uncertainties in the Finite Element model is also described.
Disturbances generated by reaction wheels on board the spacecraft are among the most substantial. Hence they play a crucial role when microvibration budget has to be assessed. This paper aims at characterising the effects of RW on the structure by focusing on the format of the disturbance input matrix of these components. In particular the case of single and multiple wheel accounted for. In the first one the responses are evaluated at some specific locations of the reaction wheel where their disturbance is amplified, i.e. harmonics. In the second case a more realistic scenario is considered with several wheels to be characterised and the effects of neglecting some terms of the disturbance input matrix are discussed. Finally a sensitivity analysis is carried out to quantify in which extent changes in the input matrix can alter the response. A preliminary methodology is then suggested to characterise a large number of wheels.
It is well documented that reaction wheels are among the most significant microvibration sources in space applications. These components, despite being nominally identical, can show differences in the generated signals due to manufacturing imperfections in their internal elements, such as ball bearing, internal and external race. In this article a methodology to account for those variations in microvibration predictions is proposed, aiming at generating a disturbance input matrix that encompasses the effects of a family of reaction wheels. With such a tool, it is possible to provide a more accurate microvibration budget at an early stage of the mission, reducing the uncertainty margin usually applied to quantify reaction wheel effects on the structure. As a consequence better designs are produced faster and cheaper. This allows for more flexibility in the mission design and reduces the degree of uncertainties in the predictions. Furthermore, it is shown that the proposed approach is able to characterise the effects of the entire family of wheels by considering only a limited number. The methodology is validated by assessing the microvibration excitation on different structures, including a real space structure with various reaction wheel mounting configurations.