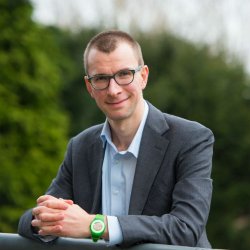
Dr Matthew Oldfield
Academic and research departments
Faculty of Engineering and Physical Sciences, School of Mechanical Engineering Sciences, Centre for Biomedical Engineering.About
Biography
Dr Matthew Oldfield is a Lecturer in Mechanical Engineering within the Department of Mechanical Engineering Sciences. He joined the University of Surrey in 2016 and is part of the Centre for Biomedical Engineering.
Dr Oldfield gained an MEng in Mechanical Engineering from the University of Liverpool. Staying at the University, he obtained his PhD on the 'Harmonic Excitation of Bolted Joints' in the Structural Mechanics group. Following his PhD, he spent two years working in the Civil Service before re-entering academic life at Brunel University. While there, in two postdoctoral positions, he investigated the optimal design of inertial, piezoelectric MEMs devices and the use of pattern recognition techniques in the dynamic analysis of structures.
After leaving Brunel University, Dr Oldfield took a position in the Mechatronics in Medicine Laboratory at Imperial College. In a group focussing on medical applications of robotic technology, his main work was numerical modelling in a team developing a steerable needle for use in neurosurgery. He investigated finite element modelling of needle cutting and the interactions allowing a soft surgical catheter to navigate tissue. The experimental validation of this work has also led to an interest in digital image correlation measurement techniques and the properties of soft solids. Dr Oldfield was part of a team that developed methods to analyse the insertion mechanics of a needle, inside a soft tissue phantom, with sub-millimetre resolution. While with the Mechatronics in Medicine Laboratory, he also led a project team that produced a novel retraction device for thyroid surgery performed with the daVinci robot.
Following seven years at Imperial College, Dr Oldfield left to take up his position, here, at the University of Surrey.
Supervision
Postgraduate research supervision
PhD student in Biomechanics
EngD students as part of the Centre for Doctoral Training in Micro- and NanoMaterials and Technologies
Publications
Military personnel use protective armour systems that are frequently exposed to low-level damage, such as non-ballistic impact, wear-and-tear from everyday use, and damage during storage of equipment. The extent to which such low-level pre-damage could affect the performance of an armour system is unknown. In this work, low-level pre-damage has been introduced into a Kevlar/phenolic resin-starved composite panel using tensile loading. The tensile stress-strain behaviour of this eight-layer material has been investigated and has been found to have two distinct regions; these have been understood in terms of the microstructure and damage within the composite panels investigated using micro-computed tomography and digital image correlation. Ballistic testing carried out on pristine (control) and pre-damaged panels did not indicate any difference in the V50 ballistic performance. However, an indication of a difference in response to ballistic impact was observed; the area of maximal local out-ofplane deformation for the pre-damaged panels was found to be twice that of the control panels, and the global out-of-plane deformation across the panel was also larger.
The Arthritis patients and aging population has challenged society to develop safer, independent living environments. Falls, associated injuries, and delays in fall treatment are major causes of morbidity and death in older adults. Therefore, fall detection systems are fundamental to reducing fall risks and building safer environments. Designing fall detection systems is an emerging field of research. The development of the system relies on a sensing mechanism, processing unit, and communication to alert the emergency facilities. Each module is crucial in providing a cost-effective, accurate, reliable, and robust solution. Technological advancements in fall detection systems, particularly wearable and non-wearable devices, offer promising solutions. Wearable systems are prevalent due to their cost-effectiveness and ease of installation, but they canbe unreliable if not worn consistently. Non-wearable systems, including smart flooring, provide continuous monitoring but are expensive and complex to maintain. This article reviews the development and deployment of fall detection technologies, examining their practical limitations and emphasizing floor-based detection systems as a viable solution for fostering independent living among older adults.
This study harnesses advanced Bayesian optimisation techniques for the intricate design of structures, poised for application as compliant flooring unit cells, as shown to reduce fall injuries in older people[1]. Inspired by the foundational research detailed in studies[2][3], our exploration delves into a design space encompassing eight key variables, contributing to a broad spectrum of geometric variations. In constitutive modelling of unit cells, we adopt the Neo-Hookean model for its effectiveness in mirroring rubber-like materials' intrinsic properties. A key element of our approach involves acknowledging and addressing uncertainty, emanating from variations in material properties and geometric imperfections. The study rigorously explores the behaviour of these structures under 2D loading conditions , examining various ratios of compression and shear forces. Employing the Bayesian optimisation algorithm, the design iteratively progresses towards an optimal configuration, driven by a comprehensive set of objective functions, which are formulated to achieve an balance between structural stiffness, critical buckling load, and the energy absorption. The effectiveness of the obtained designs is validated by mechanical testing of specimens, manufactured utilizing rubber casting and 3D printing. This study highlights the efficacy of Bayesian optimization in design, particularly under diverse loading conditions and in the presence of uncertainty. It provides valuable insights into the method's ability to improve the resilience and adaptability of structures, representing a notable advancement in the field.
Armour which is manufactured and distributed for personnel, vehicle and structural protection, primarily for military or policing applications, undergoes stringent testing to ensure that it can meet the demands of a range of impact scenarios. However, the effects of repetitive low-level damage are not fully understood and, in order to maintain a given level of protection, armour is recalled and replaced periodically, which is costly, and may be unnecessary. This paper reports preliminary studies on the relationship between minor damage and the resulting impact resistance of a woven fabric reinforced composite laminate (E-glass with epoxy resin). Specimens were subjected to displacement-controlled fatigue tests to introduce dispersed damage before being subjected to quasi-static indentation testing. The results showed that during penetration of the specimens, the peak load was reduced by approximately 10% for the pre-fatigued specimens, compared to the non-fatigued specimens, and there was some indication the energy absorption also reduced. It is proposed that the development of fibre fractures during the pre-fatigue of the specimens is the origin of these changes.
Aluminium inserts are frequently embedded within the composite sandwich structures used in modern sports cars. Since the inserts are used for attaching safety-critical components to the structure, the adhesion between the metal and composite needs to be strong and durable. The bond is achieved through an epoxy resin system. However, when the resin includes an internal mould release agent (IMR) to facilitate the demoulding process of the structure, the adhesion between the inserts and the composite structure can be compromised. In addition, inserts can be exposed to high treatment temperatures. As such, to ensure that high adhesion performance can still be achieved, an appropriate surface treatment should be applied on the inserts. In this paper, four commercially available surface treatments for aluminium inserts were assessed using single lap joint (SLJ) and double cantilever beam (DCB) tests. Moreover, to investigate the influence of the IMR and the high-temperature process on the joint properties, four sample manufacturing methods were used to prepare the SLJ samples: without IMR and without high-temperature process (Method 1), with IMR (Method 2), with high-temperature process (Method 3) and with both IMR and high-temperature process (Method 4). The DCB samples were only prepared using Method 4. The locus of failure for the SLJ samples prepared with Method 4 was evaluated by using X-ray photoelectron spectroscopy (XPS) and optical microscopy. It was found that a silane-based primer was sensitive to the use of both the IMR and high temperature (31% drop in the lap joint strength when both applied). A cataphoretic electrocoat was also investigated and only deteriorated when exposed to high temperature (up to 40% decrease in the lap joint strength). An epoxy-based primer did not show a significant sensitivity to the IMR, however, when exposed to high-temperatures, the joint became even stronger (up to 15% increase in the lap joint strength).
The mobility of soft tissue can cause inaccurate needle insertions. Particularly in steering applications that employ thin and flexible needles, large deviations can occur between pre-operative images of the patient, from which a procedure is planned, and the intra-operative scene, where a procedure is executed. Although many approaches for reducing tissue motion focus on external constraining or manipulation, little attention has been paid to the way the needle is inserted and actuated within soft tissue. Using our biologically inspired steerable needle, we present a method of reducing the disruptiveness of insertions by mimicking the burrowing mechanism of ovipositing wasps. Internal displacements and strains in three dimensions within a soft tissue phantom are measured at the needle interface, using a scanning laser-based image correlation technique. Compared to a conventional insertion method with an equally sized needle, overall displacements and strains in the needle vicinity are reduced by 30% and 41%, respectively. The results show that, for a given net speed, needle insertion can be made significantly less disruptive with respect to its surroundings by employing our biologically inspired solution. This will have significant impact on both the safety and targeting accuracy of percutaneous interventions along both straight and curved trajectories.
The rise and advancement of minimally invasive surgery (MIS) has significantly improved patient outcomes, yet its technical challenges-such as tissue manipulation and tissue retraction-are not yet overcome. Robotic surgery offers some compensation for the ergonomic challenges, as retraction typically requires an extra robotic arm, which makes the complete system more costly. Our research aimed to explore the potential of rapidly deployable structures for soft tissue actuation and retraction, developing clinical and technical requirements and putting forward a critically evaluated concept design. With systematic measurements, we aimed to assess the load capacities and force tolerance of different magnetic constructions. Experimental and simulation work was conducted on the magnetic coupling technology to investigate the conditions where the clinically required lifting force of 11.25 N could be achieved for liver retraction. Various structure designs were investigated and tested with N52 neodymium magnets to create stable mechanisms for tissue retraction. The simplified design of a new MIS laparoscopic instrument was developed, including a deployable structure connecting the three internal rod magnets with joints and linkages that could act as an actuator for liver retraction. The deployable structure was designed to anchor strings or bands that could facilitate the lifting or sideways folding of the liver creating sufficient workspace for the target upper abdominal procedures. The critical analysis of the project concluded a notable potential of the developed solution for achieving improved liver retraction with minimal tissue damage and minimal distraction of the surgeon from the main focus of the operation, which could be beneficial, in principle, even at robot-assisted procedures.
Penetration of a flexible and steerable needle into a soft target material is a complex problem to be modelled, involving several mechanical challenges. In the present paper, an adaptive finite element algorithm is developed to simulate the penetration of a steerable needle in brain-like gelatine material, where the penetration path is not predetermined. The geometry of the needle tip induces asymmetric tractions along the tool–substrate frictional interfaces, generating a bending action on the needle in addition to combined normal and shear loading in the region where fracture takes place during penetration. The fracture process is described by a cohesive zone model, and the direction of crack propagation is determined by the distribution of strain energy density in the tissue surrounding the tip. Simulation results of deep needle penetration for a programmable bevel-tip needle design, where steering can be controlled by changing the offset between interlocked needle segments, are mainly discussed in terms of penetration force versus displacement along with a detailed description of the needle tip trajectories. It is shown that such results are strongly dependent on the relative stiffness of needle and tissue and on the tip offset. The simulated relationship between programmable bevel offset and needle curvature is found to be approximately linear, confirming empirical results derived experimentally in a previous work. The proposed model enables a detailed analysis of the tool–tissue interactions during needle penetration, providing a reliable means to optimise the design of surgical catheters and aid pre-operative planning.
Minimally Invasive Surgery (MIS) needs continuous tool design innovation to support and facilitate the complex task executions of surgeons. In this article, an easily deployable magnetic structure design is presented, which is developed to retract the liver during MIS procedures. During the concept designing phase, a most critical research question, the stability of magnetic anchoring was investigated and analyzed through various experiments. The clinically relevant pulling forces have been applied to N52 neodymium magnets in different size, shape and arrangement to derive the maximum force certain retractor designs could withheld. The numeric results confirmed that the distributed load arrangement would be able to perform a stable human liver retraction. Magnetic encoring technology could have a significant future, encouraging other researchers to investigate the potential of magnetic tissue retraction in MIS procedures that could lead to the development of specialized tools for human clinical deployment.
X-ray sources are used for both scientific instrumentation and inspection applications. In X-ray photoelectron spectroscopy (XPS), aluminum Kα X-rays are generated through electron beam irradiation of a copper-based X-ray anode incorporating a thin surface layer of aluminum. The maximum power operation of the X-ray anode is limited by the relatively low melting point of the aluminum. Hence, optimization of the materials and design of the X-ray anode to transfer heat away from the aluminum thin film is key to maximizing performance. Finite element analysis has been employed to model the heat transfer of a water-cooled copper-based X-ray anode with and without the use of a CVD (chemical vapour deposited) diamond heat spreader. The modeling approach was to construct a representative baseline model, and then to vary different parameters systematically, solving for a steady state thermal condition, and observing the effect of on the maximum temperature attained. The model indicates that a CVD diamond heat spreader (with isotropic thermal properties) brazed into the copper body reduces the maximum temperature in the 4 μm aluminum layer from 613 °C to 301 °C. Introducing realistic anisotropy in the TC (thermal conductivity) of the CVD diamond has no significant effect on heat transfer if the aluminum film is on the CVD diamond growth face (with the highest TC). However, if the aluminum layer is on the CVD diamond nucleation face (with the lowest TC), the maximum temperature is 575 °C. Implications for anode design are discussed.
Puncturing blood vessels during percutaneous intervention in minimally invasive brain surgery can be a life threatening complication. Embedding a forward looking sensor in a rigid needle has been proposed to tackle this problem but, when using a rigid needle, the procedure needs to be interrupted and the needle extracted if a vessel is detected. As an alternative, we propose a novel optical method to detect a vessel in front of a steerable needle. The needle itself is based on a biomimetic, multi-segment design featuring four hollow working channels. Initially, a laser Doppler flowmetry probe is characterized in a tissue phantom with optical properties mimicking those of human gray matter. Experiments are performed to show that the probe has a 2.1 mm penetration depth and a 1 mm off-axis detection range for a blood vessel phantom with 5 mm s−1 flow velocity. This outcome demonstrates that the probe fulfills the minimum requirements for it to be used in conjunction with our needle. A pair of Doppler probes is then embedded in two of the four working channels of the needle and vessel reconstruction is performed using successive measurements to determine the depth and the off-axis position of the vessel from each laser Doppler probe. The off-axis position from each Doppler probe is then used to generate a 'detection circle' per probe, and vessel orientation is predicted using tangent lines between the two. The vessel reconstruction has a depth root mean square error (RMSE) of 0.3 mm and an RMSE of 15° in the angular prediction, showing real promise for a future clinical application of this detection system.
During minimally invasive surgical procedures, it is often important to deliver needles to particular tissue volumes. Needles, when interacting with a substrate, cause deformation and target motion. To reduce reliance on compensatory intra-operative imaging, a needle design and novel delivery mechanism is proposed. Three-dimensional finite element simulations of a multi-segment needle inserted into a pre-existing crack are presented. The motion profiles of the needle segments are varied to identify methods that reduce target motion. Experiments are then performed by inserting a needle into a gelatine tissue phantom and measuring the internal target motion using digital image correlation. Simulations indicate that target motion is reduced when needle segments are stroked cyclically and utilise a small amount of retraction instead of being held stationary. Results are confirmed experimentally by statistically significant target motion reductions of more than 8% during cyclic strokes and 29% when also incorporating retraction, with the same net insertion speed. By using a multi-segment needle and taking advantage of frictional interactions on the needle surface, it is demonstrated that target motion ahead of an advancing needle can be substantially reduced.