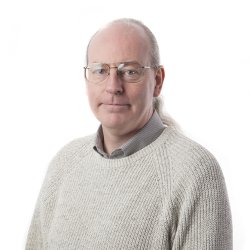
John Doherty
About
Biography
John Doherty is based within the Centre for Aerodynamics & Environmental Flow at the University of Surrey. His research interests cover aerodynamic and multidisciplinary design optimisation, novel air-vehicle conceptual design, propulsion installation aerodynamics and hybrid/electric aircraft and UAS.
John’s research career began within the Aerodynamics Department at RAE Farnborough, where he initially developed novel geometry modelling and CFD approaches for supporting novel aircraft conceptual design. This research extended into development of early 3D CFD design optimisation capabilities, which were subsequently used widely in the aerospace (MOD, BAES, Airbus) and motorsport communities. At DERA and subsequently QinetiQ, he focussed on multidisciplinary integration and optimisation, combined with novel decision support developments and systems engineering approaches. The resulting MDO capabilities played a key role in demonstrating both the feasibility and relevance of multidisciplinary design optimisation for industry. He has worked closely with a wide variety of industrial partners, through UK and international research projects. He moved to the University of Surrey in 2012.
ResearchResearch interests
- Aerodynamic CFD optimisation
- Multidisciplinary Design Optimisation
- Conceptual design and innovation
- Propulsion installation aerodynamics
- Electric ducted fan aerodynamics
Research interests
- Aerodynamic CFD optimisation
- Multidisciplinary Design Optimisation
- Conceptual design and innovation
- Propulsion installation aerodynamics
- Electric ducted fan aerodynamics
Teaching
ENG3197 Vehicle Aerodynamics
ENG3162 Aircraft Design Group Projects
ENG2087 Design, Make and Evaluate Projects
ENG3163/ENGM247 Individual Projects
Industrial Placement Visiting Tutor
Publications
A novel three-dimensional technique for correcting wind tunnel measurements for wall interference has been developed. The flow around the test body and its wake is approximated as a series of inviscid singularities, while the wind tunnel walls and model support are approximated using a panel method. A nonlinear least-squares approach with trust-region reflective optimization is then used to obtain the strength and locations of singularities together with the domain boundary panel strengths by fitting to measured wall pressures. The technique is demonstrated using computational fluid dynamics for the test case of a well-documented slender delta wing body with high blockage and validated against both experiments and legacy data. The nonlinear least-squares wall correction method is shown to demonstrate a significant improvement in wall corrections compared to the classical two-variable technique.
A novel approach to correcting the effects of wall interference has been developed for low-speed closed-wall wind tunnels using a nonlinear least-squares optimization process independent of the model geometry. Potential flow singularities are used to represent the test object, and the method of images is used to represent the tunnel walls. Trust-region reflective optimization enables the locations and strengths of singularities to be determined iteratively with only wall pressure measurements as independent inputs. Results are obtained from a range of two-dimensional and three-dimensional airfoil test cases using both computational fluid dynamics simulations and wind tunnel experiments, including a NACA 0012 with deployed spoiler, a NACA 0015, a NACA 4415, and a McDonnell Douglas 30P30N high-lift configuration. The nonlinear least-squares wall-correction method is shown to demonstrate a considerable improvement over the conventional two-variable technique.
For multi-scenario airfoil shape optimization problems, an evaluation of a single airfoil is based on its full-scenario drag landscape. To obtain the full-scenario drag landscape, a large number of computational fluid dynamic simulations for different operating conditions must be conducted. Since a single computational fluid dynamic simulation is often time-consuming, evaluations for multi-scenario airfoil shape optimization will be computationally highly intensive. Although surrogate-assisted evolutionary algorithms have been widely applied to expensive optimization problems, existing surrogate-assisted evolutionary algorithms cannot be directly applied to multi-scenario airfoil shape optimization. Instead of using surrogate models to directly approximate the multi-scenario evaluations, we employ a hierarchical surrogate model consisting of a K-nearest neighbors classifier and a Kriging model to approximate the full-scenario drag landscape for each candidate design during the optimization. Then, the fitness of the candidate design is evaluated based on the approximated drag landscape to reduce the computational cost. The proposed hierarchical surrogate model is embedded in the covariance matrix adaptation evolution strategy and applied to the RAE2822 airfoil design problem. Our experimental results show that the proposed algorithm is able to obtain an airfoil design with limited computational cost that perform well in different operating conditions.
Minimax optimization is a widely-used formulation for robust design in multiple operating or environmental scenarios, where the worst-case performance among multiple scenarios is the optimization objective requiring a large number of quality assessments. Consequently, minimax optimization using evolutionary algorithms becomes prohibitive when each quality assessment involves computationally expensive numerical simulations or costly physical experiments. This work employs evolutionary multitasking optimization and surrogate techniques to address the challenges of the high-dimensional search space and high computation cost. To this end, finding the worst-case scenario for different candidate solutions is considered as the optimization of multiple problems that can be solved simultaneously using the evolutionary multi-tasking optimization approach. In order to further speed up the proposed algorithm, a surrogate model in the joint space of the decision and scenario spaces is built to replace part of the expensive function evaluations. A generation-based model management strategy using a statistical hypothesis test is designed to manage the surrogate model. Experimental results on both benchmark problems and an airfoil design application indicate that the proposed algorithm can find satisfactory solutions with a very limited computational budget.
Life cycle cost (LCC) is truly representative to the total cost of an aircraft through its life cycle. It is usually used for estimating the cost-effectiveness of an aircraft design. For enabling LCC estimation at early stage, A LCC model have been being developed for aircraft wing under the umbrella of Integrated Wing Advanced Technology Validation Programme in United Kingdom. Object-oriented and hierarchical approaches are used for LCC modelling. The cost estimation is based on bottom-up approach. The developed LCC model is generic, and can be customized and applied for estimating the costs of other aircraft systems. © 2008 Springer-Verlag London Limited.
Material of aluminium alloys is a typical material applied in Aerospace Engineering. In order to conduct life cycle assessment of aluminium, a module based on Microsoft Excel has been developed. Through this module, COSTing Life-cycle In material ProcesseS (COSTLIPS) can be made. This paper presents the methodology to the development of the COSTLIPS and its results of estimation based on typical processes for manufacturing aluminium components. Through the COSTLIPS, it can be estimated not only processing costs, but also materials input and output, energy consumed, and wastes emitted. COSTLIPS could be a useful tool to help understand economic, energy and environmental impacts when an aluminium component/part used in engineering. Copyright © 2008 by the American Institute of Aeronautics and Astronautics, Inc. All rights reserved.
Torque-fill capability during gearshifts is an important customer requirement in automated transmission systems. This functionality can be achieved through transmission system layouts (e.g., based on dual-clutch technology) characterized by significant mechanical complexity, and hence with relatively high cost and mass. This paper describes a parallel hybrid electric drivetrain concept, based on the integration of an electric motor drive into a relatively simple six-speed automated manual transmission. The resulting hybrid electric drivetrain actuates the torque-fill function through control of the electric motor torque during the gearshifts on the engine side of the drivetrain. An optimal controller, based on the off-line computation of the control gain profiles, is presented for the clutch re-engagement phase. The novel controller allows computationally efficient consideration of clutch energy dissipation during the clutch re-engagement phase of the gearshift. The performance with the optimal controller is contrasted with that of two conventional clutch engagement controllers, along a set of gearshifts simulated with an experimentally validated vehicle model.
Aluminium is extensively applied in aerospace industry, however, uncertainties lie in all activities of its production. In this paper, risk assessment for cost estimates in aluminium lifecycle is investigated. Through the in-house module, COSTLIPS (COSTing Life-cycle In material ProcesseS), probabilities of typical processes for aluminium production are estimated. Approach of probability distribution functions and three-point estimates is used to estimate statistical parameters of the costs for different processes. Example results show that the COSTLIPS can be used for costing of aluminium production processes including risk analysis. This would be useful for material selection and evaluation in aircraft design and manufacture in term of cost estimation. Copyright © 2008 by the American Institute of Aeronautics and Astronautics, Inc.
Aluminium alloys are a key series of metallic materials used in aerospace engineering. Life cycle of aluminium consists of a series of independent product processes including, for example, bauxite mining, bauxite refining, smelting, casting, forming, performing, and disposal. In order to understand the life cycle cost of aluminium, an in-house module for costing of life cycle in material processes has been developed. The object oriented costing approach is suggested and adopted. Based on survey data and engineering analysis of the processing, cost estimating relationships are established. Through the module, costs for various processes of aluminium production can be estimated. Example results show that the module could be a useful tool for costing life cycle of aluminium, or for estimating costs for an aluminium component with an individual process. Copyright © 2008 by the American Institute of Aeronautics and Astronautics, Inc.
A novel approach to correcting the effects of wall interference has been developed for closed-wall wind tunnels using a nonlinear least squares optimisation process that is independent of model geometry. Potential flow singularities are used to represent the test object and the method of images is used to represent the tunnel walls. The present approach makes use of trust-region reflective optimisation to allow the locations and strengths of singularities to be determined iteratively with only wall pressure measurements as independent inputs. The technique has been validated using CFD simulations of flow around canonical shapes in both free and wall-bounded conditions at blockages of 5 % to 20 %. Comparisons are drawn to the two-variable method, with demonstrated improvements across the range of bodies considered. A major source of error in wind tunnel testing arises from the interference effects between the wind tunnel walls and the test model. In a closed-wall tunnel, boundary layer growth along the walls results in a pressure gradient along the length of the tunnel referred to as horizontal buoyancy [1]-although the effects of this are typically mitigated through facility design. For a lifting model, the general redirection of the flow downwards is constrained by the tunnel floor, resulting in an induced upwash known as lift interference. The walls also impose a flow constraint in the region around the model and its wake, causing a local increase in streamwise velocity, affecting the aerodynamic forces and moments experienced by the model. It is imperative that wind tunnel test data be corrected for these effects, as aircraft design demands very low uncertainty from wind tunnel data [2]. One of the most widely-used correction techniques in wind tunnel testing is the two-variable (2V) method [3]. By defining a control volume bounded by the tunnel walls and by arbitrary upstream and downstream planes, the strength of all sources and sinks representing the tunnel walls can be obtained from the potential flux using the divergence theorem. To obtain a unique solution, two independent flow variables at the bounding surface are needed: for closed wall tunnels this may be taken as the streamwise velocity, and wall-normal velocity equal to zero due to the assumed imper-meability of the walls. The key advantage of this technique is that it can determine the interference flow field independently of any model representation. However, in order to do this, this technique normally requires a large number of wall pressure measurements (typically n ≈ 100) in order to obtain a sufficiently resolved solution. Contrary to the approach taken by the 2V method, the wall pressure signature technique provides estimates of the interference flow field by modelling the object in the wind tunnel and its wake as the superposition of source, sink and doublet elements centrally located along the tunnel axis [4]. This technique has the advantage of requiring significantly fewer measurements to obtain a unique solution (typically, n ≲ 20 [5]). However, the wall pressure-signature technique does not capture upwash corrections particularly well, as the blockage is assumed to be axisymmetric. The technique
The work presented here is an on-going part of the UK Department for Business, Enterprise & Regulatory Reform (DBERR)/Industry funded Integrated Wing programme. In particular within the Configuration Optimisation and Integration sub-task, work funded by DBERR and QinetiQ is focused on assessment of a multi-disciplinary design optimisation (MDO) approach for supporting conceptual design. This approach can potentially satisfy the requirements for general applicability and accuracy through use of high-fidelity, physicsbased simulation, but it is essential to demonstrate that the approach represents a practical method which can be automated and fast enough to meet the turn-around times required within conceptual design. In particular it is necessary to identify the level of detail which must be incorporated into MDO to provide a balance between accuracy, generality and speed. In order to help identify this necessary level of detail, a baseline MDO capability has been established which will be incrementally enhanced through improvements to the modelling of specific technologies and systems. The study will also provide an indication of how an aircraft configuration, designed using MDO, changes as a result of the impact of integrating different technologies and systems. This latter outcome supports a key objective for the Integrated Wing programme by potentially helping to identify those technologies and systems which can lead to a step change in performance for future civil aircraft. This paper presents progress towards these goals, including a description of the MDO approach being followed and the integration of additional technologies and systems into the process. © 2007 by QinetiQ Ltd.
The QinetiQ Aerospace Consultancy group has been actively developing and applying process automation and optimisation capabilities in support of air vehicle assessment and design for over 20 years. These capabilities have evolved greatly during this timeframe from their initial origins as research activities, into mature capabilities for underpinning decision making in both civil and military air vehicle projects. In parallel the same generic approaches have also found usage in weapons, maritime and motorsport design. In recent years effort has focussed on enhancing a number of different, but complementary, capabilities at QinetiQ, each of which have different advantages and disadvantages, but which together better address the needs of air vehicle assessment and design. These capabilities are linked by a common requirement to assess widely differing characteristics concurrently, in order to model the consequences of design decisions, such as technology and system choices, in terms of the overall impact on an air vehicle project. This paper describes these tools in the context of their use within the Integrated Wing project.
As conventional aircraft designs approach their limits in terms of efficiency and emissions, a drastic change to the architecture of conventional platforms is required if the environmental targets of the next several decades are to be met. Boundary Layer Ingestion is one of industry’s most promising answers to the challenges of the future, identifying a potential step-change in performance in more integrated propulsion and airframe systems. This paper investigates the behaviour of a boundary layer ingesting solution of a closely embedded wing-electric ducted fan design, with focus on the implications of the aerodynamic coupling on the individual performance of both the aerodynamic and propulsive elements as well as on the assessment of the reliability of a low order panel code method. Wind tunnel testing was undertaken to understand the flow physics at different combinations of airframe and propulsor operating conditions; in addition, part of the data used for the experimental validation of a panel method model for predicting the upstream inlet flow conditions. It was found that there were clear local and extended upstream effects of the propulsor on the performance of the aerodynamic surface, resulting from the different combinations of suction strength and nacelle blockage. Similar trends were observed in the numerical code predictions, and identified limitations of the methodology in defining the experimental boundary conditions of the propulsor to be imposed in CFD. The study of the response of the propulsor to varying inlet boundary conditions, created by varying wing angles of attack was also carried out, however, small changes in flow velocity combined with measurement errors of the current system, prevented any solid conclusions being drawn about the impact of distorted inlet flow on propulsor performance.
During the early stages of aircraft design it is typically the case that potential solutions are down-selected based upon a relatively low level of supporting information. It is also often the case that major airframe characteristics are effectively fixed by the time serious consideration is given to the integration of aircraft systems. As a result, the integration of systems may be significantly more complex and may lead to greater performance penalties than would be the case if these integration requirements were better addressed during early design. The evolution of new capabilities for supporting early aircraft design, based upon Multi-disciplinary Design Optimisation (MDO) toolsets, can potentially enable more complex requirements to be directly addressed in early design. In order to assess the potential opportunities resulting from the use of MDO, consideration has been given to the requirement for improved modelling of fuel systems within early civil aircraft wing design. Details of the MDO approach used are presented. Enhancements to the MDO method, associated with the integration of fuel tanks within the wing subject to uncontained engine rotor failure (UERF) considerations, are described. The results of an initial parametric variation study are presented. The reported work has been carried out as part of the Integrated Wing collaborative programme, which is part funded by the UK Department for Business, Enterprise & Regulatory Reform (DBERR). Copyright © 2009 by QinetiQ Ltd.
Aluminium alloys are a series of traditional materials applied in aerospace industry. Composite materials have been being used to replace some aluminium alloys in airframe structures. To select a cost-efficient material in aerospace design, a framework for systematic assessment of composites and aluminium is therefore suggested. Through evaluation of 3Ps which represent prices, properties and processing of material, life cycle assessment of aluminium and composite could be made. By comparison of and trade-off the listed baselines of 3Ps, an economic, rational, available and useful material can be logically selected. © 2008 Springer-Verlag London Limited.
The work presented here is an on-going part of the UK Department for Business, Enterprise & Regulatory Reform (DBERR)/Industry funded Integrated Wing programme. In particular within the Configuration Optimisation and Integration sub-task, work funded by DBERR and QinetiQ is focused on assessment of a multi-disciplinary design optimisation (MDO) approach for supporting conceptual design. This approach can potentially satisfy the requirements for general applicability and accuracy through use of high-fidelity, physics-based simulation, but it is essential to demonstrate that the approach represents a practical method which can be automated and fast enough to meet the turn-around times required within conceptual design. In particular it is necessary to identify the level of detail which must be incorporated into MDO to provide a balance between accuracy, generality and speed. In order to help identify this necessary level of detail, a baseline MDO capability has been established which will be incrementally enhanced through improvements to the modelling of specific technologies and systems. The study will also provide an indication of how an aircraft configuration, designed using MDO, changes as a result of the impact of integrating different technologies and systems. This latter outcome supports a key objective for the Integrated Wing programme by potentially helping to identify those technologies and systems which can lead to a step change in performance for future civil aircraft. This paper presents progress towards these goals, including a description of the MDO approach being followed and the integration of additional technologies and systems into the process.
Life Cycle Cost (LCC) is an important issue for aircraft design, and can be used for the development of trade studies. An Object-Oriented System Engineering (OOSE) approach has been developed to establish a LCC model architecture, and a bottom-up approach is adopted to conduct cost estimation. The established LCC model can represent the impact of technology, and can be supplemented by increasing the fidelity functional sub-models. The developed model is generic, and as such can be easily transferable for applications in other disciplines. Copyright © 2008 by the American Institute of Aeronautics and Astronautics, Inc.
This is an investigation for a more electric regional aircraft, considering the ATR 72 aircraft as an example and the electrification of its four double slotted flaps, which were estimated to require an energy of 540 Wh for takeoff and 1780 Wh for landing, with a maximum power requirement of 35.6 kW during landing. An analysis and evaluation of three energy harvesting systems has been carried out, which led to the recommendation of a combination of a piezoelectric and a thermoelectric harvesting system providing 65% and 17%, respectively, of the required energy for the actuators of the four flaps. The remaining energy may be provided by a solar energy harvesting photovoltaic system, which was calculated to have a maximum capacity of 12.8 kWh at maximum solar irradiance. It was estimated that a supercapacitor of 232 kg could provide the energy storage and power required for the four flaps, which proved to be 59% of the required weight of a lithium iron phosphate (LFP) battery while the supercapacitor also constitutes a safer option.
A number of transonic airfoils, designed using differing approaches, are evaluated over a wide range of operating conditions, using a tool for generating aerodynamic performance maps. Details of key performance boundaries are also extracted, including drag divergence and separation onset. The aerodynamic performance maps and boundaries, which are based upon extensive use of a rapid 2D CFD tool, are first demonstrated on an existing airfoil, for which the design condition is known and for which experimental data is available. Aerodynamic maps are then presented for a series of airfoils which are designed using a sonic plateau, inverse design approach. Further maps are presented for airfoils designed using single-point and multi-point optimization. The impact of the alternative design approaches is studied, using the performance maps and the resulting characteristics of the performance boundaries. In particular, the trade-off between drag divergence and the onset of separation, combined with viscous and wave drag development, is presented. The study provides some insights into the challenge of achieving a well posed optimization formulation for transonic airfoil design.
Many real-world optimization problems involve computationally intensive numerical simulations to accurately evaluate the quality of solutions. Usually the fidelity of the simulations can be controlled using certain parameters and there is a trade-off between simulation fidelity and computational cost, i.e., the higher the fidelity, the more complex the simulation will be. To reduce the computational time in simulation-driven optimization, it is a common practice to use multiple fidelity levels in search for the optimal solution. So far, not much work has been done in evolutionary optimization that considers multiple fidelity levels in fitness evaluations. In this work, we aim to develop test suites that are able to capture some important characteristics in real-world multi-fidelity optimization, thereby offering a useful benchmark for developing evolutionary algorithms for multi-fidelity optimization. To demonstrate the usefulness of the proposed test suite, three strategies for adapting the fidelity level of the test problems during optimization are suggested and embedded in a particle swarm optimization algorithm. Our simulation results indicate that the use of changing fidelity is able to enhance the performance and reduce the computational cost of the particle swarm optimization, which is desired in solving expensive optimization problems.
This work presents a summary of the results obtained during the activities developed within the GARTEUR AD/AG-52 group. GARTEUR stands for “Group for Aeronautical Research and Technology in Europe” and is a multinational organization that performs high quality, collaborative, precompetitive research in the field of aeronautics to improve technological competence of the European Aerospace Industry. The aim of the AG52 group was to make an evaluation and assessment of surrogate-based global optimization methods for aerodynamic shape design of aeronautical configurations. The structure of the paper is as follows: Sect. “Introduction” will introduce the state-of-the-art in surrogate-based optimization for aerodynamic design and Sect. “Definition of Common Test Cases and Methods” will detail the test cases selected in the AG52 group. Optimization results will be then showed in Sect. “Optimization Results”, and conclusions will be provided in the last section.
Research covers propulsion installation characteristics for novel air-vehicle configurations in the class of small missile/UAVs. A modular experimental model has been developed featuring a fully integrated tail mounted inline boundary layer ingesting (BLI) Electric Ducted Fan (EDF) propulsion system. The research aims to investigate the aerodynamic characteristics and gain understanding of the optimisation of a fully integrated propulsion system. A combination of experimental and validated CFD methods will be used to develop suitable performance metrics and optimisation approaches for in-line BLI EDFs, thus enabling the generation of a toolset to be applied in the future design and implementation of this class of propulsion system. Progress in both experimental design and computational analysis will be presented, including initial analysis of the overall flow physics, focussing on the upstream and downstream effect of the body boundary layer, the condition of the flow ingested into the fan and an assessment of the performance of the overall integrated EDF.
In recent years, the UK Ministry of Defence (MOD) has funded development, by QinetiQ and its predecessor organisations, of processes and tools to assess the performance of air vehicles, with the objective of maintaining status as an intelligent customer for a variety of air vehicle types. During this period, Operational Requirements have been evolving, requiring increased flexibility and the capability to produce accurate performance data for novel air vehicle concepts, including those which are not adequately represented by existing semi-empirical methods and databases. In order to explain the assessment process that has been developed, an example manned aircraft application is described. The component parts of the assessment process, and the underlying techniques and technologies are also described. Finally, indications are given of possible future directions.
Function evaluations of many real-world optimization problems are time or resource consuming, posing a serious challenge to the application of evolutionary algorithms to solve these problems. To address this challenge, the research on surrogate-assisted evolutionary algorithms has attracted increasing attention from both academia and industry over the past decades. However, most existing surrogate-assisted evolutionary algorithms either still require thousands of expensive function evaluations to obtain acceptable solutions, or are only applied to very low-dimensional problems. In this paper, a novel surrogateassisted particle swarm optimization inspired from committeebased active learning is proposed. In the proposed algorithm, a global model management strategy inspired from committeebased active learning is developed, which searches for the best and most uncertain solutions according to a surrogate ensemble using a particle swarm optimization algorithm and evaluates these solutions using the expensive objective function. In addition, a local surrogate model is built around the best solution obtained so far. Then a particle swarm optimization algorithm searches on the local surrogate to find its optimum and evaluates it. The evolutionary search using the global model management strategy switches to the local search once no further improvement can be observed, and vice versa. This iterative search process continues until the computational budget is exhausted. Experimental results comparing the proposed algorithm with a few state-of-the-art surrogate-assisted evolutionary algorithms on both benchmark problems up to 30 decision variables as well as an airfoil design problem demonstrate that the proposed algorithm is able to achieve better or competitive solutions with a limited budget of hundreds of exact function evaluations.
The potential use of electric motors to power engine simulators on wind tunnel models of commercial aircraft has been studied for some years at the QinetiQ 5m Wind Tunnel at Farnborough. Recently, motors with the required power density have become available, and design and production of a prototype engine simulator is currently being undertaken. The background, potential advantages of the system, design considerations and a progress report on the project is given within this paper.
The EMPAS collaborative project covered development and demonstration of an electric motor powered aero-engine simulator in the QinetiQ 5-metre wind-tunnel. As part of the project, the University of Surrey was responsible for background research and development of various flow measurement and system monitoring technologies, for use in the EMPAS windtunnel tests. Development of an integrated digital pressure rake system is presented, which has enabled assessment of duct flow characteristics and derivation of fan pressure ratio for the EMPAS system. A novel approach based on use of miniature, low cost microphones was developed, which successfully provided in-situ fan RPM measurement and highlighted several promising areas for future monitoring of fan/system health. A 7-hole pressure probe was used to great effect for extensive flow-field surveys, to investigate and validate the aerodynamic flow field effects associated with the aero-engine simulator. Wind-tunnel results from use of the microphone and 7-hole probe systems are analyzed and presented in detail.
This paper presents a series of transonic airfoils, designed using differing optimization approaches, which are evaluated over a wide range of operating conditions using global aerodynamic performance maps. Global drag rise boundaries, which are identified, modelled and directly optimized during design, include drag divergence and onset of wave drag. The AIAA ADODG Case 2 airfoil optimization case is used to compare the results of the new global performance design approach with conventional multi-point optimization. The impact of alternative design formulations is presented in terms of both global performance maps and selected drag rise characteristics around the Case 2 design condition. In particular, the trade-off between drag divergence and the preceding onset of wave drag is discussed. The new approach addresses the issue of early excessive drag creep, which is typically encountered for optimization focused on a narrow range of operating conditions. The study provides some further insights into how a well posed optimization formulation for transonic airfoil design can potentially be established.
In solving many real-world optimization problems, neither mathematical functions nor numerical simulations are available for evaluating the quality of candidate solutions. Instead, surrogate models must be built based on historical data to approximate the objective functions and no new data will be available during the optimization process. Such problems are known as offline data-driven optimization problems. Since the surrogate models solely depend on the given historical data, the optimization algorithm is able to search only in a very limited decision space during offline data-driven optimization. This paper proposes a new offline data-driven evolutionary algorithm to make the full use of the offline data to guide the search. To this end, a surrogate management strategy based on ensemble learning techniques developed in machine learning is adopted, which builds a large number of surrogate models before optimization and adaptively selects a small yet diverse subset of them during the optimization to achieve the best local approximation accuracy and reduce the computational complexity. Our experimental results on the benchmark problems and a transonic airfoil design example show that the proposed algorithm is able to handle offline data-driven optimization problems with up to 100 decision variables.
The aerodynamic characteristics of an aft-body, in-line mounted, boundary layer ingesting, electric ducted fan, propulsion installation system has been investigated through experimental and computational analysis. A modular wind-tunnel model allows variation in the geometry of the propulsion installation system to be assessed, in combination with fan speed. Various experimental measurement techniques, including LDA, seven-hole-probe and surface pressures are employed. The propulsion installation system has also been investigated using RANS CFD and comparison with experimental data is presented. An investigation of the boundary conditions for efficiently representing the fan in CFD is described. Initial results show reasonably good agreement between CFD and experiment, in terms of velocity profiles and surface pressures, but highlight remaining differences for cases exhibiting flow separation.
Copyright © 2015 SAE International.This paper discusses the torque-fill capability of a novel hybrid electric drivetrain for a high-performance passenger car, originally equipped with a dual-clutch transmission system, driven by an internal combustion engine. The paper presents the simulation models of the two drivetrains, including examples of experimental validation during upshifts. An important functionality of the electric motor drive within the novel drivetrain is to provide torque-fill during gearshifts when the vehicle is engine-driven. A gearshift performance indicator is introduced in the paper, and the two drivetrain layouts are assessed in terms of gearshift quality performance for a range of maneuvers.
An initial investigation of an optimisation based approach for design across a continuous range of operating conditions is presented. The objective for this 'operations based optimisation' approach is to avoid the need to choose critical design point conditions and associated weighting factors by tackling the overall operational performance instead. The approach integrates numerical optimisation, response surface modelling, CFD and operational simulation. An optimisation test bed involving the aerodynamic optimisation of a Champ Car rear wing assembly for reduced lap time using track simulation has been developed to assess the new optimisation approach. Details of the operations based optimisation approach and the Champ Car test bed are reported. Results generated using the new approach are presented and the wider potential of the approach for aerospace applications is discussed.