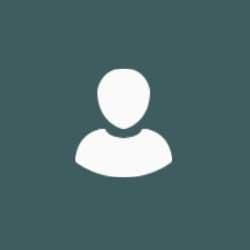
Dapeng Zhang
Academic and research departments
School of Chemistry and Chemical Engineering, Faculty of Engineering and Physical Sciences.About
My research project
.
.
Publications
The effect of flow in an ultrasonic reactor is an important consideration for practical applications and for the scale-up of ultrasonic processing. Previous literature on the influence of flow on sonochemical activity has reported conflicting results. Therefore, this work examined the effect of overhead stirring at four different frequencies, 40, 376, 995 and 1179 kHz, in two different reactor configurations. Comparable power settings were utilised to elucidate the underlying mechanisms of interactions between the flow and sonochemical activity. The sonochemical activity was determined by the yield of hydrogen peroxide, measured by iodide dosimetry, and the active region was visualised with sonochemiluminescence imaging. The overhead stirring in the low frequency reactor altered the yield of hydrogen peroxide so it produced the maximum yield out of the four frequencies. The increase in hydrogen peroxide yield was attributed to a reduction in coalescence at 40 kHz. However at the higher frequencies, coalescence was not found to be the main reason behind the observed reductions in sonochemical yield. Rather the prevention of wave propagation and the reduction of the standing wave portion of the field were considered.
The parameters, including ultrasonic frequency, still versus stirring, biomass particle size and biomass loading were concurrently investigated for the ultrasonic treatment of wheat straw. Experiments were conducted at three different frequencies; 40, 376, and 995kHz using three different solid to liquid ratios, 1/50, 1/20, and 1/15(g/ml), with and without mechanical stirring. Additional treatments in different particle size ranges, 0-0.5, 0.5-1, and 1-2mm were performed at the solid to liquid ratio of 1/20(g/ml). Fractionation was improved at 40 and 995kHz via different mechanisms. Delignification was favored at the ultrasonic treatment frequency of 40kHz, biomass loading 1/20(g/ml) with stirring and particle size range of 0.5-1mm. However at 995kHz carbohydrate solubilization was favored, especially in the particle size range of
The conversion of lignocellulosic biomass for biofuels and biorefinery applications is limited due to the cost of pretreatment to separate or access the biomass's three main usable components, cellulose, hemicellulose, and lignin. After pretreatment, each component may be utilized via chemical conversion, hydrolysis, and/or fermentation. In this review we aim first, to identify the current status-quo of knowledge of the parametric effects of ultrasound, second, to evaluate the potential of ultrasound as a pretreatment and fractionation method of lignocellulose, and last, to identify the challenges that this technology faces. Ultrasound produces chemical and physical effects which were both found to augment the pretreatment of lignocellulose via delignification and surface erosion. The magnitudes of these effects are altered when the ultrasonic field is influenced by parameters such as solvent, ultrasonic frequency, and reactor geometry and type. Therefore, the implementation of ultrasound for the pretreatment of lignocellulose must consider the variation of ultrasonic influences to capitalize on the key effects of ultrasound. Currently the literature is dominated by low frequency ultrasonic treatment, coupled with alkaline solutions. High frequency ultrasound, oxidizing solutions, and use of combined alternative augmentation techniques show promise for the reduction of energy consumed and synergistic enhancement of ultrasonic treatment. Furthermore, feedstock characteristics, reactor configuration, kinetics, and the ultrasonic environment should be considered. © 2013 American Chemical Society.