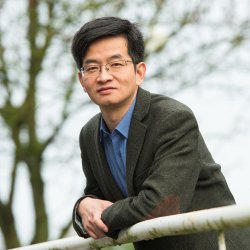
Professor Charley Wu
About
Biography
Prof. Chuan-Yu (Charley) Wu is a professor in Chemical Engineering at the Department of Chemical and Process Engineering and the coordinator of the Unilever-IPE-Surrey collaborative doctoral training programme in sustainable manufacture, multi-scale modelling, formulation and product engineering. He was also the coordinator of a EU FP7 Initial Training Network (ITN) consortium (€3.8M) on the development of in silico models for roll compaction, which consists of 10 full partners and 4 associate partners from 8 EU countries. He has expertise in discrete element analysis, multiscale modelling and simulations, pharmaceutical engineering, particle technology and granular dynamics. Prof. Wu has been working closely with global pharmaceutical companies over the last 10 years and has run industrial collaborative research projects with Pfizer, AstraZeneca, MSD and Sanofi in developing advanced numerical modelling techniques for pharmaceutical application and established a strong link with the global pharmaceutical industry.
Prof. Wu is currently an executive editor for Powder Technology. He co-authored a monograph on “Particle Technology and Engineering” published by Elsevier and edited two books entitled “Discrete Element Modelling of Particulate Media” and “Particulate Materials: Synthesis, Characterisation, Processing and Modelling” published by RSC publishing. He also edited five journal special issues and published over 100 scientific papers with an H-index of 18. He has given more than 30 invited presentations and seminars at international conferences, global pharmaceutical companies and universities worldwide. Prof. Wu is a member of the advisory and editorial board for “Particuology”, “Acta Pharmaceutica Sinica B (APSB) ” and “Journal of Engineering”.
Prof. Wu is also a grant assessor for ESPRC, Royal Society, European Research Council, French research council (ANR), Canada Research Council, China National Science Foundation and Romania Research Council. He also served as a PhD examiner for the universities of Cambridge, Edinburgh, Birmingham, Leicester, Leeds and Sheffield in the UK, the University of New South Wales and Monash University in Australia, and Abo Akademi University in Finland.
Prof. Wu organized five conferences as the chairman in the fields of particle technology and discrete element modelling (Die compaction and Roll Compaction, 2007; UK-China Particle Technology Forum III, 2009; International Symposium on Discrete Element Modelling, 2012, PARTEC, 2013, Particulate Processing in Pharmaceutical Industry IV, 2014) and is a member of the international advisory and scientific committees for three international conference series (ECI conference on Particulate Processing in Pharmaceutical Industry; UK-China Particle Technology Forum; Coupled Problems).
Areas of specialism
My qualifications
ResearchResearch projects
IPROCOM (The development of in silico process models for roll compaction) is a multidisciplinary and inter-sectoral consortium funded by European Commission under the FP7-PEOPLE-2012-ITN Programme. The goal of IPROCOM is to address scientific and technology challenges in the manufacture of particulate products (pharmaceuticals, catalyst pellets, detergent tablets, fertilizer, biomass and metal components) through a coordinated and structured research training programme.
In particular, IPROCOM aims to develop robust in silico process models that can be used to predict the properties of intermediate (ribbons/granules) and final products (tablets/pellets/components) based on the properties of individual particles and to provide structured training for the next generation of researchers who will comprehend such models, associated knowledge and techniques and apply them to a number of particulate products manufacturing industries.
IPROCOM consortium brings together experts from engineering, pharmaceutical science, materials science and computer science disciplines from 10 full partners and 4 associate partners specializing pharmaceutical development, machine manufacturing, multimedia & science communications.
Structured research training in IPROCOM consists of 3 complementary work packages: i) process understanding through systematic experimental investigation, ii) multiscale modeling with discrete element methods (DEM) & Finite element methods (FEM) and iii) intelligent modeling with artificial neural networks, evolutionary computation and other heuristic techniques.
THERMOPCPowder compaction is a widely used manufacturing technique for producing high quality particulate products. Depending on the processing methods, there are two types of powder compaction: roll compaction and die compaction, which have been used either in combination or separately to produce certain particulate products. Powder compaction has distinctive advantages such as cost effectiveness, low waste, continuous process with high productivity and easy online controls. Whilst the same process could be used in manufacturing high value-added products with heat sensitive materials, such as organic materials and polymers, its implementation is significantly hindered by the accumulation of heat, which can significantly degrade heat sensitive materials during the manufacturing processes. THERMOPC is an EC FP7 project funded through the Marie Curie Intra-European Fellowship (IEF) scheme, and employs an inter-disciplinary approach to understand the fundamental mechanisms of powder compaction processes and to develop predictive computational tools for modelling the thermomechanical behaviour during powder compaction.
The movement of solid-liquid suspensions in pipes and vessels is a generic complex problem which is commercially challenging and technically important. Industrial applications are numerous, e.g. chemicals, consumer goods, food, pharmaceuticals, oil, mining, river engineering, construction, power generation, biotechnology and biomedical. Despite such large markets, industrial practice and processes are neither efficient nor optimal because of a severe lack of fundamental understanding of these flows. Such flows involve complex phenomena on a wide range of scales as flow conduits generally vary from the micron scale to the centimetre scale, and vessels vary from the millilitre scale to the cubic metre scale. Flows may be turbulent or viscous and the carrier fluid may exhibit complex non-Newtonian rheology. Particles occur in various shapes, sizes, densities, bulk and surface properties which exacerbates the complexity of the problem.
The design of processes for conveying or processing solid-liquid suspensions requires information about particle behaviour such as particle trajectory, radial migration across streamlines, particle velocity distribution, and solids distribution. There are, however, huge practical difficulties in imaging solid-liquid flows and measuring local fluid and solid velocities, since little of the available instrumentation is applicable. Mixtures of practical interest are often concentrated and opaque so that flow visualisation is impossible, and particles may be deformable, breakable or prone to aggregation. Such complex phenomena are presently difficult to predict. They have hampered fundamental research and the development of rigorous holistic modelling strategies and, as a result, work has generally followed a piecemeal empirical approach.
This proposal will use a multiscale approach to study the flow of solid-liquid suspensions including fluids of complex non-Newtonian rheology and particles with complex properties: (i) experimentally via a unique and accurate Lagrangian technique of positron emission particle tracking, which can measure local 3-D phase velocities as well as phase distribution in opaque systems; and (ii) by developing and validating novel modelling approaches to predict such flows including detailed interactions between particles, fluid and walls. A number of advanced modelling techniques will be used including principally the Discrete Element Method (DEM), Computational Fluid Dynamics (CFD), Smooth Particle Hydrodynamics (SPH), Lattice Boltzmann Method (LBM) and Coarse-Grained Molecular Dynamics (CGMD).
None of these methodologies on its own, however, is able to effectively model these complex flows as they all enjoy strengths as well as weaknesses. We will, therefore, exploit the strengths of each technique by assembling these methods in an efficient hybrid fashion to produce an integrated multiscale modular framework to be made available free of charge within the unique and well-known open source code DL_MESO. Thus, we will evaluate the best hybrid approaches and develop a paradigm for modelling these complex flows by mapping the model hybrids against flow characteristics.
The use of a hybrid modelling methodology and a multiscale approach to include concentrated turbulent flows, fluids of non-Newtonian rheology, particles of complex shapes and properties will produce a quantum leap advance in the modelling of these complex flows. In the medium to long-term, the findings from this work should improve the competitiveness of the UK solid-liquid processing technologies. Our industrial and academic partners, however, will be able to draw immediate benefits through engagement with the project.
Many industrial processing operations depend on feed materials that are fine powders with poor handling characteristics, which have to be rectified by granulation to form coarser granules. Generally wet granulation is employed, in which a binder is added to the powder in a mixer usually in batch processes. Continuous Twin Screw Granulation (TSG) has considerable potential, eg in the pharmaceutical sector, because of the flexibility in throughput and equipment design, reproducibility, short residence times, smaller liquid/solid ratios and also the ability to granulate difficult to process formulations. However, there remain significant technical issues that limit its widespread use and a greater understanding of the process is required to meet regulatory requirements. Moreover, encapsulated APIs (Active Pharmaceutical Ingredients) are of increasing interest and the development of a TSG process that did not damage such encapsulates would significantly extend applications.
Experimental optimisation of TSG is expensive and often sub-optimal because of the high costs of APIs and does not lead to a more generic understanding of the process. Computational modelling of the behaviour of individual feed particles during the process will overcome these limitations. The Distinct Element Method (DEM) is the most widely used method but has rarely been applied to the number of particles in a TSG extruder (~ 55 million) and such examples involve simplified interparticle interactions e.g. by assuming that the particles are smooth and spherical and any liquid is present as discrete bridges rather than the greater saturation states associated with granulation. The project will be based on a multiscale strategy to develop advanced interaction laws that are more representative of real systems. The bulk and interfacial properties of a swelling particulate binder such as microcrystalline cellulose will be modelled using Coarse-grained Molecular Dynamics to derive inputs into a meso-scale Finite Discrete Element Method model of formulations that include hard particles and a viscous polymeric binder (hydroxypropylcellulose). Elastic particles (e.g. lactose and encapsulates) with viscous binder formulations will be modelled using the Fast Multi-pole Boundary Element Method. These micro- and meso-scale models will be used to provide closure for a DEM model of TSG. It will involve collaboration with the Chinese Academy of Science, which has pioneered the application of massively parallel high performance computing with GPU clusters to discrete modelling such as DEM, albeit with existing simpler interaction laws. An extensive experimental programme will be deployed to measure physical inputs and validate the models. The screw design and operating conditions of TSG for the formulations considered will be optimised using DEM and the results validated empirically. Optimisation criteria will include the granule size distribution, the quality of tablets for granules produced from the lactose formulation and the minimisation of damage to encapsulates.
The primary benefit will be to provide a modelling toolbox for TSG for enabling more rapid and cost-effective optimisation, and allow encapsulated APIs to be processed. Detailed data post-processing will elucidate mechanistic information that will be used to develop regime performance maps. The multiscale modelling will have applications to a wide range of multiphase systems as exemplified by a large fraction of consumer products, catalyst pastes for extrusion processes, and agriculture products such as pesticides. The micro- and mesoscopic methods have generic applications for studying the bulk and interfacial behaviour of hard and soft particles and also droplets in emulsions. The combination of advanced modelling and implementation on massively parallel high performance GPU clusters will allow unprecedented applications to multiphase systems of enormous complexity.
Powder compaction is a common manufacturing process for a wide range of products including pharmaceutical and detergent tablets, catalyst pellets, fertilizer, biomass, ceramic and metallic components, due to its distinctive advantages such as cost effectiveness, low waste, continuous operation with high productivity and easy online controls. In this process, dry powders are fed into a die then compressed under high pressures to produce coherent compacts. Powder compaction can be divided into three distinct stages: die filling, compaction and ejection. Powder behaviour during die filling plays a dominant role in controlling the performance of subsequent processes and the quality of final products, as it determines the pre-compaction conditions (e.g. density distribution, composition distribution, packing patterns). Moreover, any defects induced during die filling (such as segregation, insufficient filling) will have a detrimental impact on the properties of the products. It has hence attracted an increasing interest in the scientific community over the last decade.
The goals of this project are i) to explore the dominating physics using a combined numerical and experimental approach and ii) to develop testing procedures for die filling and compaction of aerated fine powders. To achieve these goals, the following research objectives are set:
1) To perform a systematic numerical analysis of die filling using advanced DEM-CFD and to identify the most important factors controlling powder behaviour during die filling;
2) To establish a robust DEM-CFD model for die filling, which can be used by end users;
3) To develop a model die filling experimental rig that will be used to validate the numerical models and also utilized as a simple test platform for characterizing aerated fine powders for die filling and compaction.
DECRON - Development of eco-friendly ironmaking processes based on GPU-enhanced DEM-CFD modellingBlast furnaces are widely used in the iron-making industry. The running of blast furnaces consumes 60% energy of whole steel industry and is primarily responsible for the CO2 blueprints in steel plants. As the steel industry is suffering much with the increase iron ore prices and global economy recession in recent years, it has now become a urgent need to adopt innovative approaches to reduce the production cost in iron-making. It is well recognized that the development of eco-friendly steel plants are urgently demanded. DECRON provides a unique and timely opportunity to bring together the fellow’s research experience in the high performance computing, GPU and discrete element modelling (DEM) with the supervisor’s extensive experience in coupled DEM with computational fluid dynamics (DEM-CFD), particle flow, packing and segregation. This will result in the development of novel charging methods for blast furnaces based upon a thorough micro-mechanistic understanding of the process using GPU-enhanced DEM-CFD, and lead to more precision and better controlled charging systems for blast furnaces. DECRON will for the first time devise an indisputable technological innovation and establish feasible strategies to achieve controlled burden distribution in blast furnaces, which will maximise energy efficiency and reduce CO2 emission in iron-making processes.
The Development Of Predictive Models For Bilayer Pharmaceutical FormulationsThere is an increasing interest in developing bilayer tablets as an oral dosage form for controlled release of pharmaceutical drugs, due to their distinctive functional advantages. This project will seek to improve understanding of the link between interfacial characteristics and bilayer adhesion, thus allowing refinement of formulation /process strategies to maximise bilayer adhesion. The overall aims of this research project are i) to explore the delamination mechanisms during the manufacture process of bilayer pharmaceutical formulations; and ii) to develop predictive formulation and process development tools for bilayer tablets based on a thorough understanding of delamination mechanisms.
Indicators of esteem
Proposal Reviewer: European Research Council (ERC); National Science Foundation of China (NSFC); Natural Sciences and Engineering Research Council of Canada; The Executive Agency for Higher Education, Research, Development and Innovation, Romania; French National Research Agency (ANR); Qatar National Research Fund (QNRF).
Member of EPSRC College (2005-)
Guest Editor: Powder Technology, Particuology, Granular Matter, Materials.
Editorial Board Member: Particuology, Journal of Engineering.
PhD Examiner: The universities of Cambridge, Imperial College, Edinburgh, Southampton, Birmingham, Sheffield, Leicester, Leeds, Newcastle, Surrey and Glasgow Caledonian University in the UK; Abo Akademi University in Finland; University of New South Wales \& Monash University in Australia; University of Toulouse in France.
Opponent for PhD thesis public defence: Abo Akademi University, Finland; Ecole Des Mines, Albi, France
Peer Reviewer: Powder Technology, AICHE J, Chemical Engineering Science, Proceedings of the Royal Society London, International Journal of Pharmaceuticals, Journal of Pharmaceutical Science.
Expert Consultant: In the field of X-ray Computed Tomography for pharmaceutical solid oral dosage forms.
Research projects
IPROCOM (The development of in silico process models for roll compaction) is a multidisciplinary and inter-sectoral consortium funded by European Commission under the FP7-PEOPLE-2012-ITN Programme. The goal of IPROCOM is to address scientific and technology challenges in the manufacture of particulate products (pharmaceuticals, catalyst pellets, detergent tablets, fertilizer, biomass and metal components) through a coordinated and structured research training programme.
In particular, IPROCOM aims to develop robust in silico process models that can be used to predict the properties of intermediate (ribbons/granules) and final products (tablets/pellets/components) based on the properties of individual particles and to provide structured training for the next generation of researchers who will comprehend such models, associated knowledge and techniques and apply them to a number of particulate products manufacturing industries.
IPROCOM consortium brings together experts from engineering, pharmaceutical science, materials science and computer science disciplines from 10 full partners and 4 associate partners specializing pharmaceutical development, machine manufacturing, multimedia & science communications.
Structured research training in IPROCOM consists of 3 complementary work packages: i) process understanding through systematic experimental investigation, ii) multiscale modeling with discrete element methods (DEM) & Finite element methods (FEM) and iii) intelligent modeling with artificial neural networks, evolutionary computation and other heuristic techniques.
Powder compaction is a widely used manufacturing technique for producing high quality particulate products. Depending on the processing methods, there are two types of powder compaction: roll compaction and die compaction, which have been used either in combination or separately to produce certain particulate products. Powder compaction has distinctive advantages such as cost effectiveness, low waste, continuous process with high productivity and easy online controls. Whilst the same process could be used in manufacturing high value-added products with heat sensitive materials, such as organic materials and polymers, its implementation is significantly hindered by the accumulation of heat, which can significantly degrade heat sensitive materials during the manufacturing processes. THERMOPC is an EC FP7 project funded through the Marie Curie Intra-European Fellowship (IEF) scheme, and employs an inter-disciplinary approach to understand the fundamental mechanisms of powder compaction processes and to develop predictive computational tools for modelling the thermomechanical behaviour during powder compaction.
The movement of solid-liquid suspensions in pipes and vessels is a generic complex problem which is commercially challenging and technically important. Industrial applications are numerous, e.g. chemicals, consumer goods, food, pharmaceuticals, oil, mining, river engineering, construction, power generation, biotechnology and biomedical. Despite such large markets, industrial practice and processes are neither efficient nor optimal because of a severe lack of fundamental understanding of these flows. Such flows involve complex phenomena on a wide range of scales as flow conduits generally vary from the micron scale to the centimetre scale, and vessels vary from the millilitre scale to the cubic metre scale. Flows may be turbulent or viscous and the carrier fluid may exhibit complex non-Newtonian rheology. Particles occur in various shapes, sizes, densities, bulk and surface properties which exacerbates the complexity of the problem.
The design of processes for conveying or processing solid-liquid suspensions requires information about particle behaviour such as particle trajectory, radial migration across streamlines, particle velocity distribution, and solids distribution. There are, however, huge practical difficulties in imaging solid-liquid flows and measuring local fluid and solid velocities, since little of the available instrumentation is applicable. Mixtures of practical interest are often concentrated and opaque so that flow visualisation is impossible, and particles may be deformable, breakable or prone to aggregation. Such complex phenomena are presently difficult to predict. They have hampered fundamental research and the development of rigorous holistic modelling strategies and, as a result, work has generally followed a piecemeal empirical approach.
This proposal will use a multiscale approach to study the flow of solid-liquid suspensions including fluids of complex non-Newtonian rheology and particles with complex properties: (i) experimentally via a unique and accurate Lagrangian technique of positron emission particle tracking, which can measure local 3-D phase velocities as well as phase distribution in opaque systems; and (ii) by developing and validating novel modelling approaches to predict such flows including detailed interactions between particles, fluid and walls. A number of advanced modelling techniques will be used including principally the Discrete Element Method (DEM), Computational Fluid Dynamics (CFD), Smooth Particle Hydrodynamics (SPH), Lattice Boltzmann Method (LBM) and Coarse-Grained Molecular Dynamics (CGMD).
None of these methodologies on its own, however, is able to effectively model these complex flows as they all enjoy strengths as well as weaknesses. We will, therefore, exploit the strengths of each technique by assembling these methods in an efficient hybrid fashion to produce an integrated multiscale modular framework to be made available free of charge within the unique and well-known open source code DL_MESO. Thus, we will evaluate the best hybrid approaches and develop a paradigm for modelling these complex flows by mapping the model hybrids against flow characteristics.
The use of a hybrid modelling methodology and a multiscale approach to include concentrated turbulent flows, fluids of non-Newtonian rheology, particles of complex shapes and properties will produce a quantum leap advance in the modelling of these complex flows. In the medium to long-term, the findings from this work should improve the competitiveness of the UK solid-liquid processing technologies. Our industrial and academic partners, however, will be able to draw immediate benefits through engagement with the project.
Many industrial processing operations depend on feed materials that are fine powders with poor handling characteristics, which have to be rectified by granulation to form coarser granules. Generally wet granulation is employed, in which a binder is added to the powder in a mixer usually in batch processes. Continuous Twin Screw Granulation (TSG) has considerable potential, eg in the pharmaceutical sector, because of the flexibility in throughput and equipment design, reproducibility, short residence times, smaller liquid/solid ratios and also the ability to granulate difficult to process formulations. However, there remain significant technical issues that limit its widespread use and a greater understanding of the process is required to meet regulatory requirements. Moreover, encapsulated APIs (Active Pharmaceutical Ingredients) are of increasing interest and the development of a TSG process that did not damage such encapsulates would significantly extend applications.
Experimental optimisation of TSG is expensive and often sub-optimal because of the high costs of APIs and does not lead to a more generic understanding of the process. Computational modelling of the behaviour of individual feed particles during the process will overcome these limitations. The Distinct Element Method (DEM) is the most widely used method but has rarely been applied to the number of particles in a TSG extruder (~ 55 million) and such examples involve simplified interparticle interactions e.g. by assuming that the particles are smooth and spherical and any liquid is present as discrete bridges rather than the greater saturation states associated with granulation. The project will be based on a multiscale strategy to develop advanced interaction laws that are more representative of real systems. The bulk and interfacial properties of a swelling particulate binder such as microcrystalline cellulose will be modelled using Coarse-grained Molecular Dynamics to derive inputs into a meso-scale Finite Discrete Element Method model of formulations that include hard particles and a viscous polymeric binder (hydroxypropylcellulose). Elastic particles (e.g. lactose and encapsulates) with viscous binder formulations will be modelled using the Fast Multi-pole Boundary Element Method. These micro- and meso-scale models will be used to provide closure for a DEM model of TSG. It will involve collaboration with the Chinese Academy of Science, which has pioneered the application of massively parallel high performance computing with GPU clusters to discrete modelling such as DEM, albeit with existing simpler interaction laws. An extensive experimental programme will be deployed to measure physical inputs and validate the models. The screw design and operating conditions of TSG for the formulations considered will be optimised using DEM and the results validated empirically. Optimisation criteria will include the granule size distribution, the quality of tablets for granules produced from the lactose formulation and the minimisation of damage to encapsulates.
The primary benefit will be to provide a modelling toolbox for TSG for enabling more rapid and cost-effective optimisation, and allow encapsulated APIs to be processed. Detailed data post-processing will elucidate mechanistic information that will be used to develop regime performance maps. The multiscale modelling will have applications to a wide range of multiphase systems as exemplified by a large fraction of consumer products, catalyst pastes for extrusion processes, and agriculture products such as pesticides. The micro- and mesoscopic methods have generic applications for studying the bulk and interfacial behaviour of hard and soft particles and also droplets in emulsions. The combination of advanced modelling and implementation on massively parallel high performance GPU clusters will allow unprecedented applications to multiphase systems of enormous complexity.
Powder compaction is a common manufacturing process for a wide range of products including pharmaceutical and detergent tablets, catalyst pellets, fertilizer, biomass, ceramic and metallic components, due to its distinctive advantages such as cost effectiveness, low waste, continuous operation with high productivity and easy online controls. In this process, dry powders are fed into a die then compressed under high pressures to produce coherent compacts. Powder compaction can be divided into three distinct stages: die filling, compaction and ejection. Powder behaviour during die filling plays a dominant role in controlling the performance of subsequent processes and the quality of final products, as it determines the pre-compaction conditions (e.g. density distribution, composition distribution, packing patterns). Moreover, any defects induced during die filling (such as segregation, insufficient filling) will have a detrimental impact on the properties of the products. It has hence attracted an increasing interest in the scientific community over the last decade.
The goals of this project are i) to explore the dominating physics using a combined numerical and experimental approach and ii) to develop testing procedures for die filling and compaction of aerated fine powders. To achieve these goals, the following research objectives are set:
1) To perform a systematic numerical analysis of die filling using advanced DEM-CFD and to identify the most important factors controlling powder behaviour during die filling;
2) To establish a robust DEM-CFD model for die filling, which can be used by end users;
3) To develop a model die filling experimental rig that will be used to validate the numerical models and also utilized as a simple test platform for characterizing aerated fine powders for die filling and compaction.
Blast furnaces are widely used in the iron-making industry. The running of blast furnaces consumes 60% energy of whole steel industry and is primarily responsible for the CO2 blueprints in steel plants. As the steel industry is suffering much with the increase iron ore prices and global economy recession in recent years, it has now become a urgent need to adopt innovative approaches to reduce the production cost in iron-making. It is well recognized that the development of eco-friendly steel plants are urgently demanded. DECRON provides a unique and timely opportunity to bring together the fellow’s research experience in the high performance computing, GPU and discrete element modelling (DEM) with the supervisor’s extensive experience in coupled DEM with computational fluid dynamics (DEM-CFD), particle flow, packing and segregation. This will result in the development of novel charging methods for blast furnaces based upon a thorough micro-mechanistic understanding of the process using GPU-enhanced DEM-CFD, and lead to more precision and better controlled charging systems for blast furnaces. DECRON will for the first time devise an indisputable technological innovation and establish feasible strategies to achieve controlled burden distribution in blast furnaces, which will maximise energy efficiency and reduce CO2 emission in iron-making processes.
There is an increasing interest in developing bilayer tablets as an oral dosage form for controlled release of pharmaceutical drugs, due to their distinctive functional advantages. This project will seek to improve understanding of the link between interfacial characteristics and bilayer adhesion, thus allowing refinement of formulation /process strategies to maximise bilayer adhesion. The overall aims of this research project are i) to explore the delamination mechanisms during the manufacture process of bilayer pharmaceutical formulations; and ii) to develop predictive formulation and process development tools for bilayer tablets based on a thorough understanding of delamination mechanisms.
Indicators of esteem
Proposal Reviewer: European Research Council (ERC); National Science Foundation of China (NSFC); Natural Sciences and Engineering Research Council of Canada; The Executive Agency for Higher Education, Research, Development and Innovation, Romania; French National Research Agency (ANR); Qatar National Research Fund (QNRF).
Member of EPSRC College (2005-)
Guest Editor: Powder Technology, Particuology, Granular Matter, Materials.
Editorial Board Member: Particuology, Journal of Engineering.
PhD Examiner: The universities of Cambridge, Imperial College, Edinburgh, Southampton, Birmingham, Sheffield, Leicester, Leeds, Newcastle, Surrey and Glasgow Caledonian University in the UK; Abo Akademi University in Finland; University of New South Wales \& Monash University in Australia; University of Toulouse in France.
Opponent for PhD thesis public defence: Abo Akademi University, Finland; Ecole Des Mines, Albi, France
Peer Reviewer: Powder Technology, AICHE J, Chemical Engineering Science, Proceedings of the Royal Society London, International Journal of Pharmaceuticals, Journal of Pharmaceutical Science.
Expert Consultant: In the field of X-ray Computed Tomography for pharmaceutical solid oral dosage forms.
Teaching
Chemical Reaction Engineering and Numerical Methods (Module Coordinator, 2013- 2016)
Equipment Design (2013-2016)
Multidisciplinary Design Project (MDDP, 2013-2015)
Transferable Skills (2013-2014)
Research Methods and Projects (2016)
Chemical Product Design (2017-)
Numerical Methods (2018-)
Multiphase Systems (2007-2012)
Mass Transfer (2009-2012)
Functional Products (2006-2007)
Powder Handling and Processing (Module Coordinator, 2006-2012).
Sustainable development goals
My research interests are related to the following:
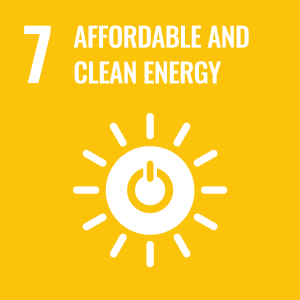
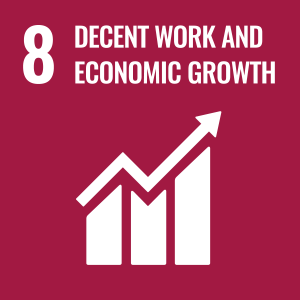
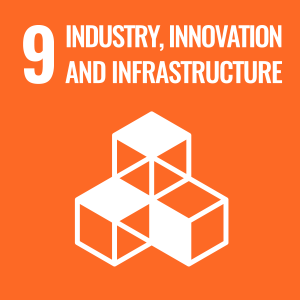
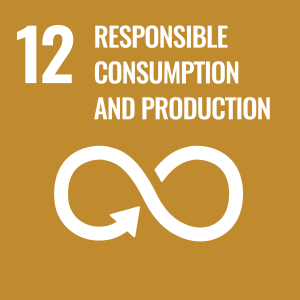
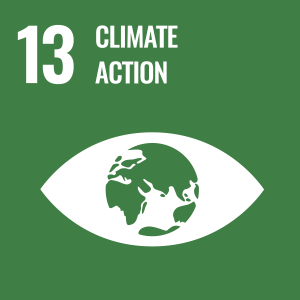

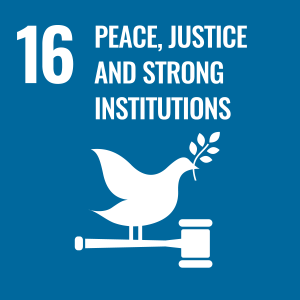
Publications
The tensile strength is an important material attribute of granular products, and diametrical compression is one of the most common methods to determine the tensile strength of the agglomerate. In this study, three-dimensional diametrical compression tests of annular agglomerates with various bonding strengths, i.e. interfacial energies and internal holes, are for the first time modelled by the Discrete Element Method (DEM) with the JKR theory. The fracture patterns and tensile strengths of annular specimens are analysed and compared with those of disc specimens. It is found that annular specimens show complete tension failures with progressive fractures along the loading diameter towards the central hole, while the disc specimens show wedge-shaped shear fractures near the platens. The results also show that the tensile strengths of annular specimens are linear with the surface energy, whereas increase with the size of internal hole and then decrease with the size of internal hole. A dimensionless parameter is introduced to analyse the failure mechanism of the agglomerate. This parameter quantifies the ratio between the external force exerted by the platens and the cohesive force among bonded particles. The proposed parameter emphasises the crucial influence of the internal hole size of an annular agglomerate and bonding capacity on its tensile strength.
Granular materials transition between unjammed (deformable) and jammed (rigid) states when adjusting their packing density. Here, we report on experiments demonstrating that the same kind of phase transition can be alternatively achieved through temperature-controlled particle shape change. Using a confined system of randomly-packed rod-like particles made of shape memory alloy (SMA), we exploit that shape recovery of these bent rods with rising temperature at a constant packing density leads to a jammed state. The responsible physical processes are elucidated with numerical simulations based on the Discrete Element Method. As an exemplary application of the uncovered mechanism, we engineer a smart clamp that can actively grip or release an object through the thermo-induced jamming or unjamming of the granular material, and robustly so under cyclic temperature changes. In the jammed state, its load-bearing capability surpasses the total SMA weight by a tunable margin, up to over 800-fold. The clamping design paves the way towards a new kind of functional devices based on the thermo-responsive jamming of shape memory granular materials. Granular materials transition between unjammed and jammed states when adjusting their packing density. Here, authors find that the same kind of phase transition can be alternatively achieved through temperature-controlled particle shape change.
Tablet is an effective system for delivering probiotics into the gastrointestinal tract. However, the mechanical stress, combined with the local heating generated during compaction, pose challenges to maintaining probiotic viability. Evaluating probiotic viability under various compression conditions is necessary to optimise the tabletting process. However, testing each scenario individually significantly increases development time and costs. Hence, it is of scientific and industrial importance to develop predictive models for assessing probiotic viability during compaction. In this study, a finite element (FE) model integrating the modified Drucker-Prager Cap (DPC) model with a thermal tolerance model was developed for the first time to predict the probiotic viability during powder compaction. The capability of the model in predicting mechanical behaviour, thermal response, and probiotic viability was demonstrated through comparison with experimental measurements. FE analysis revealed that the viability of the probiotic Lactobacillus gasseri (L. gasseri KS-13) decreases as the compression pressure increases, as observed experimentally. Furthermore, it is also found that pre-compression is an effective method to enhance the viability of probiotics during compaction.
All-solid-state lithium batteries (ASSLBs) are a promising next generation energy storage technology comparing to conventional lithium-ion batteries (LIBs). Although ASSLBs have high thermal stability, thermal degradation and thermal runaway can still occur. The thermal characteristics of the cathode of ASSLBs play a crucial role in maintaining the stability of the interface with the electrolyte. It is important to understand the thermal characteristics of ASSLBs, which is highly associated with specific microstructure geometrics of composite cathodes. Here, this paper presents a 3D lattice Boltzmann heat conduction model to simulate the effective thermal conductivity (ETC) of the multiphase solid-state cathodes, which is composed of active material LCO (LiCoO2) and solid electrolyte LLZO (Li7La3Zr2O12), generated using the discrete element method (DEM) with different porosities, volumetric ratios, particle size ratios, and various composite tortuosities. The findings indicate that porosity, volumetric fraction, and particle size all exert the decisive factor on ETC. Tortuosity emerges as a non-negligible factor influencing thermal conductivity, highlighting the importance of microstructural optimization. •LBM modelling of heat conduction in cathode microstructures of ASSLBs generated using DEM.•An equivalent packed particles heat conduction experiment for model validation.•Porosity and component volume fraction dominantly influence the heat conduction in cathodes.•Particle size and tortuosity are intertwined and have non-negligible effect on heat conduction.
We perform numerical simulations on inertial migration of a non-neutrally buoyant particle with a density ratio 0.98~ 1.02 in a linear shear flow dominated channel with a Reynolds number up to 500 in presence of thermal convection using a double-population lattice Boltzmann method. It is found that under the isothermal condition, the particle with a larger density difference from the fluid will either settle to the bottom of the channel or float to the top of the channel, while the particle with a smaller particle-fluid density difference remains suspended in the channel due to the inertial lift force. The presence of thermal convection (characterised by the Grashof number G r ) induces an additional downward lift force, which results in distinctive migration behaviours that depend on whether the particle density is larger or smaller than that of the fluid. For particle heavier than the fluid, the settling is enhanced by thermal convection due to the synergistic effect of the thermal lift force and the gravitational force. The critical Reynolds number for lifting the particle increases compared with the isothermal case and is linearly correlated with the dimensionless density ratio ( σ ) . On the other hand, for particle lighter than the fluid, an empirical dimensionless number G r ∗ , defined as G r / [ σ ( 1.59 R e + 9.31 ) ] , is introduced to characterise the particle migration. It is discovered that the particle’s equilibrium position depends on whether it migrates to the top wall or remains suspended in the shear flow under the isothermal condition. For the former case, when thermal convection is introduced, the particle keeps staying at the top wall when G r ∗ l e s s t h a n 1 , and becomes suspended in the channel when G r ∗ g r e a t e r t h a n 1 .
© 2015. Milling is a critical process for controlling the properties of the granules produced by roll compaction. In the current study, the positron emission particle tracking (PEPT) technique was used to examine the milling kinematics of roll-compacted ribbons at various milling speeds. Microcrystalline cellulose (MCC, Avicel PH-102) was used as the model feed material and a radioactive particle (tracer) was mixed with the MCC powder and roll-compacted to form sample ribbons. They were then milled using an oscillating mill at various speeds and the kinematics of the ribbons (trajectory, velocity, and occupancy) were quantitatively determined using PEPT. A close examination of the PEPT data reveals that, for milling MCC PH-102 ribbons using the oscillating mill considered in this study, the milling speed plays an important role: at low values, the milling process is dominated by cooperative motion of the ribbons with the blade (i.e. the speeds of the ribbons and the blade are similar, and the ribbons move along with the blade) and the ribbons are milled primarily by abrasion; as the speed increases the ribbons undergo more random motion involving collisions that results in an increase in ribbon breakage and hence an increase in the milling efficiency. It is shown that the PEPT technique is a useful technique for examining milling kinematics of roll-compacted ribbons.
[Display omitted] •Friction-induced heat generation and heat transfer models are developed.•Thermal behaviours of particles and walls are experimentally and numerically analysed.•Effects of rotation speed on temperature rises on both particles and walls are examined. In many granular material handling processes, heat generation, and subsequent temperature rise, due to contacts between particles and surfaces is common. Aiming to explore this phenomenon, friction-induced heat generation and heat transfer models are developed and implemented into a Discrete Element Method (DEM) in this paper. The DEM models are validated qualitatively for the temperature distribution pattern and quantitatively for the evolution of particle temperature rise using data obtained experimentally. Moreover, the temperature distribution of the drum end plates obtained in the simulations shows the same annulus pattern observed in experiments. It is also found that increasing the rotation speed of the drum leads to an increase in the annular heated region of drum and in the net heat that particles obtain. In addition, a higher rotation speed leads to higher absolute fluctuations and lower relative variability of particle temperature.
The impact between particles or agglomerates and a device wall is considered as an important mechanism controlling the dispersion of active pharmaceutical ingredient (API) particles in dry powder inhalers (DPIs). In order to characterise the influencing factors and better understand the impact induced dispersion process for carrier-based DPIs, the impact behaviour between an agglomerate and a wall is systematically investigated using the discrete element method. In this study, a carrier-based agglomerate is initially formed and then allowed to impact with a target wall. The effects of impact velocity, impact angle and work of adhesion on the dispersion performance are analysed. It is shown that API particles in the near-wall regions are more likely to be dispersed due to the deceleration of the carrier particle resulted from the impact with the wall. It is also revealed that the dispersion ratio increases with increasing impact velocity and impact angle, indicating that the normal component of the impact velocity plays a dominant role on the dispersion. Furthermore, the impact induced dispersion performance for carrier-based DPI formulations can be well approximated using a cumulative Weibull distribution function that is governed by the ratio of overall impact energy and adhesion energy.
Large-scale gas-solid flow systems, e.g., fluidized beds, cyclone separators and pneumatic conveyors, are often encountered in chemical engineering. Numerical modeling technologies are widely applied for design and understanding of complex phenomena in these gas-solid flow systems, for which the coupled model of the discrete element method (DEM) and computational fluid dynamics is generally employed. However, application of the numerical simulations for these systems is still limited because the number of the particles that can be modeled (about several hundreds of thousand) is quite small comparing with the immeasurable number of particles used in the industrial processes, and not sufficient to fully understand the complex behavior in these processes. The coarse graining DEM is then developed to provide an alternative approach for modeling the real industrial processes. Accuracy of the coarse graining DEM has been proven for simple systems so far. In the present study, applicability of the coarse graining DEM for complex shaped domains is explored, for which typical industrial processes, such as fluidization with inserted tubes, and powder flow into a confined space, are considered. In these calculations, signed distance functions (SDF) and immersed boundary method (IBM) are used to model an arbitrary shape wall boundary in a gas-solid flow. Both numerical modeling using the coarse graining DEM and experimental investigation are performed with a thorough comparison between the experimental and numerical results. It is demonstrated that the coarse graining DEM is capable of accurately modeling of industrial gas-solid two-phase systems. Besides, this numerical approach is shown to provide valuable information such as pressure profile during powder injection and interaction between bubbles and structures in a fluidized bed.
Dry granulation is commonly used in the pharmaceutical industry for compressing heat and moisture sensitive feed materials into compacts, subsequently followed by milling. Population balance models (PBMs) are often used to explore the effects of milling conditions on the granule size distribution (GSD) but limited studies have investigated the effects of the feed material and ribbon properties on the resulting GSD. In this work, a variety of feed materials and ribbons with different mechanical properties were used to validate a mass-based bi-modal breakage function developed in a previous study (Olaleye et al., 2019). Ribbon like tablets (referred to as ribblets) with a range of precisely controlled porosities were produced using an Instron machine and pharmaceutical excipients including the microcrystalline cellulose MCC 101, MCC DG and a DCPA/MCC mixture. Roll compacted ribbons were also produced using MCC 102 and MCC DG excipients. The ribblets and ribbons were milled in an impact-dominated cutting mill and PBM parameters were obtained from the ribblet milling data. Mechanistic models related to the feed ribbon property were then developed. It was found that the PBM with the mass-based bi-modal breakage function can accurately predict the GSDs of both the milled ribblets and roll compacted ribbons. The model developed was successfully linked to ribbon properties such as porosity for the first time and the model parameter a that reflects the fines mode in the bi-modal breakage function increased linearly with ribblet porosity. This work demonstrates the versatility of the developed PBM and provides a systematic approach for describing the ribbon milling process.
Particle–fluid flows are ubiquitous in nature and industry. Understanding the dynamic behaviour of these complex flows becomes a rapidly developing interdisciplinary research focus. In this work, a numerical modelling approach for complex particle–fluid flows using the discrete element method coupled with the lattice Boltzmann method (DEM-LBM) is presented. The discrete element method and the lattice Boltzmann method, as well as the coupling techniques, are discussed in detail. The DEM-LBM is thoroughly validated for typical benchmark cases: the single-phase Poiseuille flow, the gravitational settling and the drag force on a fixed particle. In order to demonstrate the potential and applicability of DEM-LBM, three case studies are performed, which include the inertial migration of dense particle suspensions, the agglomeration of adhesive particle flows in channel flow and the sedimentation of particles in cavity flow. It is shown that DEM-LBM is a robust numerical approach for analysing complex particle–fluid flows.
The penetration of a plate into granular media was analyzed, and the effects of particle–plate and particle–particle frictions, penetration direction, and initial plate orientation were examined. Results showed that stress was directly proportional to immersion depth for frictionless particles but jumped at the bed surface and then increased linearly for frictional particles. Moreover, stress was mostly independent of the penetration direction when the plate was frictionless. However, initial orientation always had an effect regardless of whether the plate was frictional or frictionless. Furthermore, a theoretical model was developed for stress analysis. This model revealed that friction on the plate essentially affected stress via changing the push angle of the particles that were in contact with the plate.
Dry granulation through roll compaction followed by milling is a widely used pharmaceutical process. The material properties of powders and the roll compaction process conditions affect the strength of ribbons, and subsequently the granule size distribution (GSD). Accurate prediction of the granule size distribution from milling of ribbons with different properties is essential for ensuring tablet quality in the final compaction stage. In this study, MCC, PH-102 ribbons with precisely controlled porosities were produced and milled in a cutting mill and granule size distribution was analysed using QicPic. A population balance model with a new breakage function based on the Weibull function was developed to model the ribbon milling process. Eight model parameters were initially obtained for each ribbon porosity and very good agreement between the model and experimental results was obtained. Sensitivity analysis was then performed and thus reduced the number of model parameters that changed with ribbon porosity to two in the breakage function. The refined model was able to predict the granule size distribution both within and outside the experimental boundaries. It was shown that the model developed in this study has a great potential for predicting granule properties and therefore the optimisation of the dry granulation process.
Flow performance of pharmaceutical powders dictates various manufacturing processes, such as blending, filling and tableting, and is determined by not only material properties but also environmental conditions, such as relative humidity and temperature. In this study, the effect of moisture content on flow performance of two commonly used pharmaceutical excipients (mannitol and dicalcium phosphate anhydrous) during die filling was investigated. A rotary die filling system was employed and the die filling efficiency was assessed using the concept of critical filling velocity. Powder flowability was also characterised using a dynamic flow tester and a shear cell tester. It was found that, with increasing moisture content, the flow parameters, including the basic flow energy, the average pressure drop and the cohesion, increased first and then decreased from a maximum at 50% relative humidity (RH). For both mannitol and dicalcium phosphate anhydrous (DCPA), when the relative humidity is high (say >50%) and the cohesion due to the formation of liquid bridges dominates, the critical filling velocity increases as the moisture content increases. While at a low relative humidity (e.g. 15%), a strong electrostatic attraction between particles was observed, which has a significant impact on the flow properties and the die filling performance of the powders. [Display omitted]
Triboelectrification due to frictional contacts between particles and surfaces is prevalent in many powder handling processes. Aiming to explore the friction-induced electrostatic charging behavior, a discrete element method (DEM) is developed for the first time in the current article, in which a frictional charging model and electrostatic interaction models are implemented. The charge accumulation on both the particles and the surface in a rotational container is then analyzed numerically and experimentally to evaluate the developed DEM. The numerical results for the frictional electrification between insulant particles and an insulant wall agree well with the experimental measurement. It is also shown that both the net charge on the particles and the degree of the particle dispersion are a function of the charging time. Moreover, it is revealed that the friction-induced particle charge enhances particle dispersion, and increases the granular temperature due to the electrostatic interactions.
As one of the commonly-used solid dosage forms, pharmaceutical tablets have been widely used to deliver active drugs into the human body, satisfying patient’s therapeutic requirements. To manufacture tablets of good quality, diluent powders are generally used in formulation development to increase the bulk of formulations and to bind other inactive ingredients with the active pharmaceutical ingredients (APIs). For formulations of a low API dose, the drug products generally consist of a large fraction of diluent powders. Hence, the attributes of diluents become extremely important and can significantly influence the final product property. Therefore, it is essential to accurately characterise the mechanical properties of the diluents and to thoroughly understand how their mechanical properties affect the manufacturing performance and properties of the final products, which will build a sound scientific basis for formulation design and product development. In this study, a comprehensive evaluation of the mechanical properties of the widely-used pharmaceutical diluent powders, including microcrystalline cellulose (MCC) powders with different grades (i.e., Avicel PH 101, Avicel PH 102, and DG), mannitol SD 100, lactose monohydrate, and dibasic calcium phosphate, were performed. The powder compressibility was assessed with Heckel and Kawakita analyses. The material elastic recovery during decompression and in storage was investigated through monitoring the change in the dimensions of the compressed tablets over time. The powder hygroscopicity was also evaluated to examine the water absorption ability of powders from the surroundings. It was shown that the MCC tablets exhibited continuous volume expansion after ejection, which is believed to be induced by (1) water absorption from the surrounding, and (2) elastic recovery. However, mannitol tablets showed volume expansion immediately after ejection, followed by the material shrinkage in storage. It is anticipated that the expansion was induced by elastic recovery to a limited extent, while the shrinkage was primarily due to the solidification during storage. It was also found that, for all powders considered, the powder compressibility and the elastic recovery depended significantly on the particle breakage tendency: a decrease in the particle breakage tendency led to a slight decrease in the powder compressibility and a significant drop in immediate elastic recovery. This implies that the particle breakage tendency is a critical material attribute in controlling the compression behaviour of pharmaceutical powders.
© 2014 Elsevier Ltd. The electrostatic charge can be transferred between particles during collisions. The particle shape plays an important role and, in the current study, the charge accumulation and distribution on elongated particles in a vibrating container are investigated using a discrete element method, in which a contact electrification model is implemented. The elongated particle geometry is modelled using a multi-sphere approach. Five different shapes are considered and characterized using a shape factor, δ, which is defined as the ratio of the difference of the radii between the distal sphere and central sphere to the mean radius of the particle. It is found that the net charge on the central sphere is greater than that on the distal sphere when δ0, greater net charge is accumulated on the larger distal sphere. The maximum surface charge difference between the distal and central sphere increases as the shape factor increases. The net charge of the granular system with different particle shapes achieves an equilibrium state during the vibrating process. This accumulating process follows an exponential trend.
Application of numerical simulations are desired to improve the quality of powder products and to optimize the production process in powder die-filling. In the powder die-filling, complex gas-solid interaction should be simulated since the solid particles are significantly influenced by the gas flow under moving wall boundary. The discrete element method (DEM) coupled with computational fluid dynamics (CFD) has been widely utilized in the simulation of gas-solid flows, and the adequacy has been proved through countless studies. On the other hand, the existing DEM-CFD method is extremely difficult to simulate the gas-solid flow where the wall boundary is moving. Besides, in the existing DEM-CFD method, huge number of computational particles cannot be simulated on a single PC. Hence, numerical simulations of the industrial powder die-filling becomes a challenging topic from a viewpoint of evolution of the DEM-CFD method, because modeling of the moving wall boundary as well as modeling of large number of computational particles should be considered simultaneously. Very recently, the authors' group has developed the Integrated DEM-CFD method including the arbitrary shape wall boundary model and the scaling law model. In the Integrated DEM-CFD method, the wall boundary is modeled by the signed distance functions and the immersed boundary method, and besides the coarse graining DEM is employed as the scaling law model. Adequacy of the Integrated DEM-CFD method has been proved through verification tests. In the current study, applicability of the Integrated DEM-CFD method is examined in the powder die-filling. Adequacy of the Integrated DEM-CFD method is shown by agreement between the original particle system and the coarse graining particle system in the powder die-filling. Through the verification tests, macroscopic characteristics of the powder die-filling are shown to be reproduced by the Integrated DEM-CFD method. Consequently, the Integrated DEM-CFD method is illustrated to be effective for the simulation of the industrial powder die-filling systems. [Display omitted]
The use of desktop X ray microtomography (XMT) to characterize randomly packed pharmacheutical particulate systems was discussed. The XMT work was performed using a 1072 Sky Scan desktop system. Glass spheres were used for the particle packing experiment with an average particle size of 200 μm transferred to borosilicate glass capillary tubes of 3 mm diameter. The 2D X-ray tomography images showed clearly defined spheres contained in capillary tube.
Ribbon milling is a critical step in dry granulation using roll compaction as it determines the properties of granules, and subsequently the properties of final products. During ribbon milling, fragmentation of ribbons or flakes (i.e. compressed agglomerates from dry powders) are induced by either impact or abrasion. Understanding these fragmentation mechanisms is critical in optimising ribbon milling processes. In the current study, the discrete element method (DEM) was used to model fragmentation at the microscopic level, providing a detailed insight into the underlying breakage mechanism. In DEM modelling, virtual ribbons were created by introducing an appropriate interfacial energy using the cohesive particle model. A set of three-dimensional parallelepiped ribbons with solid fraction φ=0.7422 and surface energies ranging from γ=0.03 J⁄m^2 and γ=2 J⁄m^2 were created and then fractured during impacts with a plane at various impact velocities, in order to model impact dominated milling. The fragmentation rate, and the number and size of fragments (i.e. granules) resulting from the breakage of a ribbon during the impact were determined. The DEM simulations showed that the granules size distribution had a bimodal pattern and there was a strong correlation between the size of fines generated from fragmentation during impact and the size of the feed powder (i.e. the size of the primary particles in this study), which was consistent with the observation from physical experiments. Two quantities were calculated from the DEM simulations: the number of fragments p and the fraction of fines z for each breakage event which can be used as input parameters for population balance models (PBM) to develop a DEM-PBM modelling framework.
In this study a hybrid numerical framework for modelling solid-liquid multiphase flow is established with a single-relaxation-time lattice Boltzmann method and the discrete element method implemented with the Hertz contact theory. The numerical framework is then employed to systematically explore the effect of particle concentration on the inertial migration of neutrally buoyant particle suspensions in planar Poiseuille flow. The results show that the influence of particle concentration on the migration is primarily determined by the characteristic channel Reynolds number Re0. For relatively low Re0 (Re0˂20), the migration behaviour can only be observed at a very low particle concentration (≤5%). However, when Re0˃20 the migration behaviour can be observed at a high concentration (≥20%). Furthermore, a focusing number Fc is proposed to characterise the degree of inertial migration. It was found that the inertial migration can be classified into three regimes depending on two critical values of the focusing number, Fc+ and Fc-: i) when Fc˃Fc+, a full inertial migration occurs; ii) when Fc˂Fc-, particles are laterally unfocused; iii) when Fc-˂Fc˂Fc+, a partially inertial migration takes place.
The reduction of raw materials into particulate form using grinding mills is an energy and cost intensive task. Optimization of grinding processes is not trivial as obtaining information on the dynamics of media in the mill via experimental means is extremely difficult due to the harsh environment inside, thus computational modeling is the most feasible option to obtain information on the dynamics of the media. However the computational cost of modeling each particle is high, resulting in the shape of the media being approximated by simple shapes and in most cases a reduction in the size of the mill. Even with these simplifications typical simulations take many weeks to months to complete making it unfeasible for quick design prototyping and process optimization. In the last decade the Graphical Processor Unit (GPU) has enabled large scale simulations of tens of millions of spheres in ball mills using the Blaze-DEM GPU code. Recently this code was expanded to provide detailed contact detection for polyhedra using the volume overlap method which is the most accurate approach amongst commercial and academic codes. In this study we firstly validate the code against experiment for polyhedral both as well as spherical particles. We then perform a number of simulations to study the effect of particle shape, in particular angularity and aspect ratio. We clearly demonstrate the importance of accurate particle shape representation in mill simulations by comparing charge profile, power draw and force network for various polyhedra approximations against spheres.
•The equilibrium position is located below the centerline when both walls are hot.•The equilibrium positions are well characterised by the Richardson number and size ratio.•Bifurcation of the equilibrium position occurs when the temperature of two walls are different.•The critical Reynolds number at the transition point follows a power law of the size ratio. A numerical investigation of lateral migration of a neutrally buoyant particle in Couette flow with two different thermal boundary conditions is performed using a lattice Boltzmann method coupled with a discrete element method. The effects of the channel Reynolds number (Re), the Grashof number (Gr) as well as the particle size on the migration behaviour are explored in detail. It was found that when both the top and bottom walls are hot, the equilibrium positions are located below the centerline for all the particle sizes studied, which can be well characterised using a dimensionless force ratio determined by the Richardson number (Ri=Gr/Re2) and the confinement ratio. With the increase of the force ratio, the equilibrium position moves towards the bottom wall. On the other hand, when the top wall is cold and the bottom wall is hot, a transition of the equilibrium position is observed, which switches from below the centerline to above the centerline as the particle size is increased above a certain threshold. It is discovered that the critical Reynolds number at transition can be well described by a power law of the confinement ratio. Furthermore, it is also found that the variation of the equilibrium positions above the centerline is governed by a new dimensionless parameter Gr/Re for a fixed particle size, which is attributed to the finite size effect.
Diffusion-induced swelling or shrinkage of particles is ubiquitous in many industrial processes and nature. Aiming to rigorously model these deformable particles, a microscopic model that considers the microstructural evolution of individual particles is developed for the first time and implemented into the discrete element method (DEM), which is experimentally validated. The robustness of this model is also evaluated by comparing its performance with a macroscopic diffusion-induced swelling model and a phenomenological swelling model. The swelling behaviours of a single particle and particle beds of various configurations in water are then analysed. It is shown that the microscopic swelling model and the phenomenological swelling model can better describe the swellings of single particle and particle beds than the macroscopic swelling model. Moreover, the microscopic swelling model can not only reproduce the phenomena of volume expansion of particles but also well predict the microstructural evolution of individual particles, as observed experimentally. Furthermore, the microscopic swelling model is capable of describing the shrinkage processes and the particle-particle diffusions of swellable particles. It is hence demonstrated that DEM with the microscopic swelling model, which captures the microscopic physical mechanisms of particle swelling and the microstructural change of swelling particles, could be a useful tool for modelling swellable granular materials in various industrial processes.
Electrostatic phenomena, including contact electrification and electrostatic interactions, can influence the dynamic behaviors of particles in fluidization. In this paper, a discrete element method coupled with computational fluid dynamics is advanced with implementation of contact electrification and electrostatic interaction models to investigate electrostatic phenomena and dynamic behaviors of particles in fluidization. Two fluidization cases are investigated: (i) only contact electrification is considered and (ii) both contact electrification and electrostatic interactions are considered. In both cases, particles with different work functions are bi-charged. Agglomerates of bi-charged particles are formed when electrostatic interactions are considered. When the gas velocity is large enough to break the agglomerate, the accumulation of charge is faster than the case that electrostatic interactions are negligible. However, a smaller gas velocity leads to a higher coordination number but slower increase of the charge.
An optimum carrier rugosity is essential to achieve a satisfying drug deposition efficiency for the carrier based dry powder inhalation (DPI). Therefore, a non-organic spray drying technique was firstly used to prepare nanoporous mannitol with small asperities to enhance the DPI aerosolization performance. Ammonium carbonate was used as a pore-forming agent since it decomposed with volatile during preparation. It was found that only the porous structure, and hence the specific surface area and carrier density were changed at different ammonium carbonate concentration. Furthermore, the carrier density was used as an indication of porosity to correlate with drug aerosolization. A good correlation between the carrier density and fine particle fraction (FPF) (r(2)=0.9579) was established, suggesting that the deposition efficiency increased with the decreased carrier density. Nanoporous mannitol with a mean pore size of about 6 nm exhibited 0.24-fold carrier density while 2.16-fold FPF value of the nonporous mannitol. The enhanced deposition efficiency was further confirmed from the pharmacokinetic studies since the nanoporous mannitol exhibited a significantly higher AUC(0-8h) value than the nonporous mannitol and commercial product Pulmicort. Therefore, surface modification by preparing nanoporous carrier through non-organic spray drying showed to be a facile approach to enhance the DPI aerosolization performance.
In this work, a computational intelligence (CI) technique named flexible neural tree (FNT) was developed to predict die filling performance of pharmaceutical granules and to identify significant die filling process variables. FNT resembles feedforward neural network, which creates a tree-like structure by using genetic programming. To improve accuracy, FNT parameters were optimized by using differential evolution algorithm. The performance of the FNT-based CI model was evaluated and compared with other CI techniques: multilayer perceptron, Gaussian process regression, and reduced error pruning tree. The accuracy of the CI model was evaluated experimentally using die filling as a case study. The die filling experiments were performed using a model shoe system and three different grades of microcrystalline cellulose (MCC) powders (MCC PH 101, MCC PH 102, and MCC DG). The feed powders were roll-compacted and milled into granules. The granules were then sieved into samples of various size classes. The mass of granules deposited into the die at different shoe speeds was measured. From these experiments, a dataset consisting true density, mean diameter (d50), granule size, and shoe speed as the inputs and the deposited mass as the output was generated. Cross-validation (CV) methods such as 10FCV and 5x2FCV were applied to develop and to validate the predictive models. It was found that the FNT based CI model (in the cases of both CV methods) performed much better than other CI models. Additionally, it was observed that process variables such as the granule size and the shoe speed had a higher impact on the predictability than that of the powder property such as d50. Furthermore, validation of model prediction with experimental data showed that the die filling behavior of coarse granules could be better predicted than that of fine granules.
Ultrafine particle processing system (UPPS) was developed previously by our group to provide a new solution to microsphere fabrication. The UPPS was supposed to possess many featured advantages, but the microsphere formation mechanism during UPPS processing was still unknown. The objective of this study was to perform the formation mechanism investigation and in vitro evaluation on risperidone-containing poly(d, l-lactic-co-glycolic acid) microspheres (RIS-PLGA MS) fabricated by UPPS. Evaporation profile and viscosity of the PLGA-containing solutions were considered as the critical factors for the microsphere formation mechanism and were determined in present study. The formation mechanism of RIS-PLGA MS was put forward by semiquantitative analysis on the basis of the evaporation profile, viscosity, and scanning electron microscopy results. It was established that the evaporation profile and viscosity would have an impact on the evaporation velocity and PLGA molecular diffusion velocity during solidification process, resulting in different appearance of the microspheres. Furthermore, comprehensive in vitro evaluations of RIS-PLGA MS were conducted, including particle size distribution, micromeritics, morphology, drug loading, encapsulation efficiency, residual organic solvent, syringeability, and in vitro release behavior. The results revealed that RIS-PLGA MS was a promising candidate for intramuscular administration, and meanwhile UPPS was a qualified technology for microsphere production.
Rotary tabletting presses are widely used to produce tablets in the pharmaceutical industry. In the tabletting process using a rotary press, rotary die filling is one of critical process steps, as powder behaviour during die filling dictates the quality of final products, such as dosage and weight variations. It is hence of importance to understand powder flow behaviour during rotary die filling. The purpose of this study is to identify the critical process parameters and material attributes that determine the die filling performance. For this purpose, a model rotary die filling system with a paddle feeder was constructed to mimic the powder feeding process in a typical rotary press. Using this model system, the effects of turret speed and paddle speed on die filling behaviour were investigated. Three grades of microcrystalline cellulose powders were considered. It was found that the turret speed has a more pivotal role in controlling the die filling performance than the paddle speed. In addition, it is demonstrated that powder flowability has a great impact on the fill weight variation, and a higher weight variation is induced for the powders with poorer flowability.
The inability of cohesive powders to flow consistently and reliably is a major cause of process downtime and reduced efficiency across a wide range of powder processing industries. Most methods to assess powder flowability fail at low consolidation pressures (
© 2015 Elsevier B.V. Contact electrification is generally referred to as the charge transfer process between particles during collisions. The transferred charge can be accumulated on the surface of the particles especially for insulating materials with irregular shapes, which can lead to a non-uniform charge distribution and eventually affects the charge accumulation process. In this study, in order to investigate the influence of the particle shape on contact electrification, a sphere-tree multi-sphere method and a contact electrification model are implemented into the discrete element method (DEM) to model the charging process of irregular particles in a rotating drum. Irregular particles with various Sauter mean diameters but the same maximum diameter and equivalent volume diameters are considered. The charge distribution and accumulation on the particles are investigated. It is found that the charge transfer originates from the contact between the particle and the drum due to the contact potential difference and initially takes place primarily at the region near the wall of the drum. The charge eventually propagates to the entire granular bed. The charge of the particles increases exponentially to an equilibrium value. For particles with the same maximum diameter, a larger charging coefficient is obtained for the particles with smaller Sauter mean diameters and sphericities, which leads to a faster charge accumulation, while for particles with the same equivalent volume diameter and fill ratio, similar charging coefficients are observed. A non-uniform intra-particle charge distribution is induced on each individual multi-sphere particle.
Thermal properties of powders are critical material attributes that control temperature rise during tableting and roll compaction. In this study, various analytical methods were used to measure the thermal properties of widely used pharmaceutical excipients including microcrystalline cellulose (MCC) of three different grades (Avicel PH 101; Avicel PH 102 and Avicel DG), lactose and mannitol. The effect of relative density on the measured thermal properties was investigated by compressing the powders into specimen of different relative densities. Differential thermal analysis (DTA) was employed to explore endothermic or exothermic events in the temperature range endured during typical pharmaceutical manufacturing processes, such as tabletting and roll compaction. Thermogravimetric analysis (TGA) was performed to analyse the water/solvent content, either in the form as solvates or as loosely bound molecules on the particle surface. Thermal conductivity analysis (TCA) was conducted to measure thermal conductivity and volumetric heat capacity. It is shown that, for the MCC powders, almost no changes in morphology or structural changes were observed during heating to temperatures up to 200 °C. An increase in relative density or temperature leads to a high thermal conductivity and the volumetric heat capacity. Among all MCC powders considered, Avicel DG showed the highest increase in thermal conductivity and the volumetric heat capacity, but this heat capacity was not sensitive to the measurement temperature. For lactose and mannitol, some endothermic events occurred during heating. The thermal conductivity increased with the increase in temperature and relative density. A model was also developed to describe the variation of the thermal conductivity and the volumetric heat capacity with the relative density and the temperature. It was shown that the empirical model can well predict the dependency of the thermal conductivity and the volumetric heat capacity on the relative density and the temperature.
Hoppers and silos are widely used in storing powders in various industries, such as agricultural, chemical, food and pharmaceutical industries. It is of practical importance to design hoppers and silos to ensure smooth discharge of bulk solids from these devices, and to minimise the occurrence of arching, blockage and build-up of materials around the walls. However, due to the complex nature of bulk solids, arching behaviour of bulk solids in silos and hoppers is still not well understood. In this study, a combined experimental and numerical study was performed to explore the transition from non-flow to flow of bulk solids from a flat bottom hopper. Glass beads of various sizes were considered and the minimal orifice size through which these materials can be discharged was determined experimentally using a FlodexTM
Roller compaction followed by milling of the generated ribbons is a typical dry granulation route. It is desirable to be able to predict the size distribution of the granules exiting the mill based on the ribbon properties and mill operational conditions. Two DEM-PBM approaches for predicting this size distribution are compared; a direct approach where the size distribution is experimentally determined, and an indirect approach where the successive change in size distribution due to each stressing event is determined mathematically by the PBM. The experimental component of the direct approach assumes shear deformation to be the dominant breakage mechanism. This approach provides a reasonable agreement to experimental data, though the influence of mill parameters is not experimentally tested. When considering breakage to be driven by impact, the indirect approach predicts the correct magnitude of fines generation, though incorrectly predicts the fine fraction to increase with impeller speed. When abrasion is assumed to be the dominant breakage mechanism, the indirect approach suggests the same trend, though with a less pronounced effect of impeller speed and a closer agreement to experimental data. Prediction accuracy is expected to improve by considering distributions of stressing conditions and material strength, the latter being explicitly captured in the experimental component of the direct method. Furthermore, the direct method accounts for the variable loading conditions of the fragments in the mill.
[Display omitted] •The GPU-based DEM approach is used to study the lab-scale die filling system.•The numerical model is calibrated and validated well with experimental data.•The stirrer occupying a specific space and reducing the effective discharge area.•Flow patterns of the free-flowing powder during die filling process is analyzed. Understanding die filling behaviour of powders is critical in developing optimal formulation and processes in various industries, such as pharmaceuticals and fine chemicals. In this paper, forced die filling is analysed using a graphics processing unit (GPU) based discrete element method (DEM), for which a powder feeder equipped with a wired stirrer is considered. The influences of operating parameters, such as the initial powder bed height, the filling speed, and the stirrer speed, on the die filling performance are systematically explored. It is shown that a larger initial powder bed height leads to a higher filling ratio, which can be attributed to a higher filling intensity; while the deposited particle mass in the die is almost independent of the powder bed height, when the initial fill level is larger than a critical bed height. Additionally, the filling ratio slightly increases with the increase of stirrer speed for cases with a stirrer, while the filling ratios are lower than that without a stirrer, which is attributed to the stirrer occupying some space above the die and reducing the effective discharge area. The obtained results can provide useful information for optimising the feeder system design and the operating condition.
Milling is commonly used for controlling the size distribution of granules in the pharmaceutical dry granulation process. A thorough understanding of the breakage of single compacts is crucial in unravelling the complex interactions that exist between different pharmaceutical feed materials and the mill process conditions. However, limited studies in the literature have examined the impact breakage of single pharmaceutical compacts. In this study, pharmaceutical powders including the microcrystalline MCC 101, MCC 102 and MCC DG were compressed at different pressures and tablets with different porosities and thicknesses were produced. Impact breakage tests were conducted in an air gun and the tablet impact velocities and breakage patterns were analysed using a Phantom ultrahigh-speed camera. It was observed that the tablet breakage rate and the amount of fines reduced as the tablet porosity decreased. In addition, thin tablets with low porosity exhibited semi-brittle fracture and less intense crack propagation while thick tablets with high porosity primarily disintegrated into fine fragments. Thus, this study provides a better understanding of the breakage behaviour of different pharmaceutical materials and can potentially be used to describe the breakage modes of compacts in the ribbon milling processes.
As one of critical process steps during pharmaceutical tabletting, rotary die filling is still not well understood. To address this issue, a model rotary die filling system with a paddle feeder was developed to closely mimic the industrial process. Using this model system, the performance of various pharmaceutical powders at different turret and paddle speeds was evaluated, and the dependence of fill variation on process conditions and material properties was examined. A comprehensive dataset was created and reported here to show the effects of material and process parameters on the die filling performance and the filling consistency. It is believed that the data can also be used for data-driven process modelling and for developing robust machine learning models for pharmaceutical manufacturing.
Twin screw granulation (TSG) is increasingly used to produce granules in various industries, such as food, pharmaceutical, and fine chemicals. However, there is a large parametric space in terms of screw designs, formulation properties and operating conditions, so how to maximise the production throughput while maintaining consistent product quality is not a trivial task and still needs further investigation. In this study, the TSG process was systematically analysed using a discrete element method (DEM) based on the graphics processor unit (GPU) architectures that can provide not only macroscopic information but also microscopic insights into the complicated TSG process. In particular, the particle flow profiles and residence time distributions were obtained from the simulations and analysed in details. The effects of particle size and screw speed on flow behaviour of particles in TSG were also explored. It was shown that the mean residence time and its variance in the granulator decreased with increasing particle size and screw speed. The E-curves of the residence time with larger particle size at higher screw speed had a narrower spread, implying that particles with a larger size had similar residence time in the twin screw granulator. In addition, the cumulative distribution function, the F-curves, showed a higher increasing rate for larger particles and higher screw speeds, indicating a faster conveying efficiency. (C) 2020 Elsevier B.V. All rights reserved.
Granular material (GM) is the second most manipulated substance in the world and is present in most industries either as raw materials or finished products. Often the temperature of the granular material needs to be manipulated for example in the case of heating iron ore to induce a phase change or to be kept within a certain temperature range in the case of pharmaceutical powders and food products. Thus a detailed understanding of how heat is transferred in granular materials is essential. The most feasible numerical approach to study heat transfer in granular materials is using the discrete element method (DEM), where each particle is explicitly modeled. In terms of conductive heat transfer particle shape can be expected to have a significant effect on the heating of granular materials, due to the nature of the grain to grain contacts and packing topology which control the heat flow paths and the rate that heat is conducted along these. This paper considers the effect of particle shape on heat conduction in thermally simple or low Biot number granular materials using a polyhedral particle representation. The volume based contact model for granular heat conduction is firstly verified against the analytical solution for solid heat conduction as well as experiment with cubic particles. The resulting model is then used to study the effect of particle shape on the effective thermal conductivity (ETC) and heat distribution within packed stationary beds. It was found that for irregularly shaped (polyhedral) particles the ETC does not have a linear relationship with the packing density as found in previous studies with spherical and ellipsoidal shaped particles. Rather that there is an exponential dependence on the micro-structural quantities of contact area and isotropy, with non-homogeneity in the packing density resulting in complex conduction paths and dead zones affecting conduction thru the bed. Crown Copyright (C) 2020 Published by Elsevier Ltd. All rights reserved.
In this study, a multi-fidelity surrogate modeling method based on physics-informed neural network (PINN) was proposed, which integrates high-fidelity simulation data and low-fidelity governing equations described by differential equations. By leveraging governing equations in the training of deep neural networks, the reliance on large amount of data has been relaxed. In the meantime, imposing physical laws ensures that the achieved surrogate models have clear physical meanings, which also improves the extrapolation performance of the models. Herein, the proposed multi-fidelity PINN surrogate modeling method was implemented to the simulation of the startup phase of a continuous stirred-tank reactor (CSTR) for illustrating its feasibility and advantages. From the computer experiment results, it is observed that the proposed method successfully reduced the sample size needed in model training and significantly improved the model extrapolation performance, facilitating its potential industrial applications.
During twin screw granulation (TSG), small particles, which generally have irregular shapes, agglomerate together to form larger granules with improved properties. However, how particle shape impacts the conveying characteristics during TSG is not explored nor well understood. In this study, a graphic processor units (GPUs) enhanced discrete element method (DEM) is adopted to examine the effect of particle shape on the conveying characteristics in a full scale twin screw granulator for the first time. It is found that TSG with spherical particles has the smallest particle retention number, mean residence time, and power consumption; while for TSG with hexagonal prism (Hexp) shaped particles the largest particle retention number is obtained, and TSG with cubic particles requires the highest power consumption. Furthermore, spherical particles exhibit a flow pattern closer to an ideal plug flow, while cubic particles present a flow pattern approaching a perfect mixing. It is demonstrated that the GPU-enhanced DEM is capable of simulating the complex TSG process in a full-scale twin screw granulator with non-spherical particles.
In blast furnaces, burden topography and packing density affect the stability of the burden, permeability of gas flow as well as the heat transfer efficiency. A fundamental understanding of the influence and interaction of coke and ore particles on the burden topography and packing density is therefore essential, in particular the influence of particle shape polydispersity and particle size polydispersity. In this paper we analyze the effect of particle shape and size polydispersity on the coke and ore charge distribution inside a bell-less blast furnace using the discrete element method (DEM). We first validate experimentally the polyhedral particle model with a simplified lab-scale charging experiment. A comparative study between spheres, with rolling friction to account for shape, and polyhedra is conducted for shape and size polydisperse particle systems. It was found that shape polydispersity mainly influenced the topography of the burden, whereas the size polydispersity mainly influenced the inter-layer percolation, i.e. localized particle diffusion, hence the local spatial packing density. The differences between the spherical particle models and polyhedral particle models on the burden topography are also quantitatively and qualitatively presented, especially on the role of particle shape on the push-up of coke in the centre. This study demonstrates that modelling particle shape effects using spheres with rolling friction is insufficient to fully describe the complex behaviour of shaped particles in a blast furnace, as the particle shape has a noteworthy influence on the burden characteristics.
The rheological behaviour of a dense granular bed under dynamic conditions is investigated by simulating granular flow in the FT4 powder rheometer using the Discrete Element Method. The distribution of the prevailing stresses and strain rates in the granular bed, and their dependence on material properties and blade operational conditions, are analysed. The shear stress was found to be approximately constant in the radial direction along the blade but dissipates in the circumferential direction away from the blade. Analogously, the strain rate decreases with increasing angular distance away from the blade as the bed becomes less dynamic. An increase in the blade tip speed, particle aspect ratio and interfacial energy results in an increase in the average shear stress in the granular bed. A predictive model is proposed to compute the average shear stress in the granular bed based on the blade torque by considering the effects of blade tip speed, particle aspect ratio and interfacial energy. [Display omitted] •Rheological response of granular materials in the FT4 rheometer is analysed.•Shear stress and strain rate dissipates away from the blade.•Shear stress is approximately constant radially along the blade.•Increasing tip speed, aspect ratio and interfacial energy increases the shear stress.•A predictive model is proposed to calculate the shear stress from the blade torque.
ABSTRACT Glaucoma is an ocular disease featuring increased intraocular pressure (IOP) and its primary treatment strategy is to lower IOP by medication. Current ocular drug delivery in treating glaucoma is confronting a variety of challenges, such as low corneal permeability and bioavailability due to the unique anatomical structure of the human eye. To tackle these challenges, a cubosome drug delivery system for glaucoma treatment was constructed for timolol maleate (TM) in this study. The TM cubosomes (liquid crystalline nanoparticles) were prepared using glycerol monooleate and poloxamer 407 via high-pressure homogenization. These constructed nanoparticles appeared spherical using transmission electron microscopy and had an average particle size of 142 nm, zeta potential of −6.27 mV, and over 85% encapsulation efficiency. Moreover, using polarized light microscopy and small-angle X-ray scattering (SAXS), it was shown that the TM cubosomes have cubic liquid crystalline D-type (Pn3m) structure, which provides good physicochemical stability and high encapsulation efficiency. Ex vivo corneal permeability experiments showed that the total amount of TM cubosomes penetrated was higher than the commercially available eye drops. In addition, in vivo studies revealed that TM cubosomes reduced the IOP in rabbits from 27.8∼39.7 to 21.4∼32.6 mmHg after 1-week administration and had a longer retention time and better lower-IOP effect than the commercial TM eye drops. Furthermore, neither cytotoxicity nor histological impairment in the rabbit corneas was observed. This study suggests that cubosomes are capable of increasing the corneal permeability and bioavailability of TM and have great potential for ocular disease treatment.
Ball indentation is a technique capable of assessing powder flowability down to very low consolidation stresses (≤1 kPa). With this method, powder flowability is determined by measuring the hardness of a powder bed, which allows the unconfined yield strength to be inferred via the constraint factor. The latter is well established for continuum materials, whereas for particulate systems its dependency on stress level and powder properties is not well defined. This work investigates these factors by simulating the ball indentation method using DEM. The constraint factor is shown to be independent of pre-consolidation stress. Constraint factor generally increases with interface energy for relatively cohesion-less powders, though not for cohesive powders. An increase in plastic yield stress leads to a decrease in the constraint factor. Increasing the coefficient of interparticle static friction reduces the constraint factor, while increasing the coefficient of inter-particle rolling friction significantly increases the constraint factor.
The suitable powder flowability is critical to the success of powder spreading processes in powder-bed additive manufacturing (AM). There are several methods to test powder flowability, but the powder flowing is more complex in spreading processes and cannot be fully characterized with any single test method. Twelve kinds of powders which are widely used in AM are considered, and their flowabilities are measured. Besides the size and shape features of powders are described, the compressibility, shear and dynamic flow energy indexes of powders are measured by a FT4 powder rheometer. A comprehensive evaluation index (CEI) for evaluating powder flowability is proposed based on the principal component analysis of the test results, and reveals the impacts of powder surface modification and gradation on powder flowability. The CEI has a stronger correlation with the avalanche angle during powder spreading processes than other indexes, which is suitable to evaluate powder flowability in AM. [Display omitted] •A comprehensive evaluation index is proposed by the PCA of powder rheology results.•The powder flowability is ranked by the comprehensive evaluation index.•Surface modification of powder can improve their flowabilities.•The powder gradation impacts their flowabilities.
Friction is a critical factor in shear flow of granular materials. Therefore, understanding and quantification of frictional behaviour of granular materials is necessary for accurate predictive models of shear flow behaviour. In this study, the effect of sliding velocity and normal load on the sliding friction coefficient is experimentally determined by shearing two layers of dry spherical glass particles over one another for a range of sliding velocities from 10 to 300 mm/s, and normal loads of 1.2 to 4.8 N. The friction between the glass surfaces shows a strong velocity-dependent effect, however, the effect of normal load is less significant. Based on the experimental results, a velocity-dependent sliding friction is implemented into DEM to simulate the shear response of spherical particles in the FT4 Powder Rheometer for a range of strain rates; spanning the transition from quasi-static to intermediate flow regimes. The accuracy of the variable friction model and the conventional constant friction model to predict shear flow behaviour in the FT4 Powder Rheometer over a wide range of strain rates is examined. It is demonstrated that the constant friction model only provides accurate prediction of the flow energy over a narrow range of strain rates, whereas the velocity-dependent friction model gives a better prediction of the experimental flow energy over a relatively wider range of strain rates. [Display omitted] •Sliding friction dependency on force and velocity was tested for glass beads•Shearing tests revealed velocity-strengthening behaviour•The normal force effect on sliding friction was found to be less significant•FT4 flow energy was evaluated in DEM with/without velocity-dependent friction•Velocity-dependent model is more accurate over a wide strain rate range
Ethyl cellulose (EC) based microparticles (MPs) could provide sustained release for Huperzine A. The drug release mechanism of MPs was exploited to achieve an ideal drug release profile. We previously found that the wettability of MPs greatly contributed to facilitating drug release, which was detailed in a research article entitled “Huperzine A loaded multiparticulate disintegrating tablet: Drug release mechanism of ethyl cellulose microparticles and pharmacokinetic study” (Peng et al., 2019) [1]. In this article, the influence of different polymers and drugs on the drug release behavior was investigated to broaden or compensate this finding. Besides, powder characterization of MPs was used to evaluate the further application of MPs for tablets.
Understanding the dependence of the strength of agglomerates on material properties, interfacial properties and structure of the agglomerate is critical in many processes involving agglomerates. For example, in the manufacturing of pharmaceutical tablets and pellets with dry granulation, understanding the relationship between the ribbon properties and the properties of the granules is critical in controlling the granulation behaviour, and the ribbon properties (e.g. tensile strength and density distribution) is determined by the material properties of the feed powders, interfacial properties between particles and the process condition, which determine the structure of the ribbons. This study aims to investigate the effect of the surface energy and porosity on the bending strength of pharmaceutical ribbons, for which three-dimensional discrete element modelling with a cohesive particle model based upon the JKR theory was performed. Simulations were carried out using specimens of various porosities and surface energies. The dependence of the bending strength on the surface energy and the ribbon porosity was examined. It was found that there is a strong correlation between the bending strength with porosity and surface energy. In particular, the bending strength is proportional to the surface energy and is an exponential function of the porosity.
In this paper, die filling from a stationary shoe in vacuum and in air was analysed using a coupled discrete element method (DEM) and computational fluid dynamics (CFD) code in which the powder is modelled using DEM while the air is analysed using CFD, and the airparticle interaction is considered. The influence of particle size and size distribution on the flow behaviour was also explored. It has been demonstrated that the coupled DEM/CFD is capable of simulating the complex interaction between the air and the powder during die filling. The numerical simulations have revealed that the presence of air during die filling has a significant impact on the powder flow behaviour, especially for the system with smaller particle sizes.
The oral drug delivery system using bilayer (or multilayer) tablets has become more commonly used in therapeutic strategies. However, one of the most common problems associated with bilayer tablets is the insufficient interfacial strength between layers, which leads to product failure during manufacturing. Therefore, it is important to better understand the interfacial strength of bilayer pharmaceutical tablets. For this purpose, in this study, the interfacial strength of bilayer tablets made of microcrystalline cellulose (MCC PH 102) at various manufacturing conditions was systematically examined. Three cases were considered: (1) the effect of interfacial curvature on the interfacial strength, for which the interfaces between two layers with different curvatures were produced using flat, convex and concave punches. (2) The effect of water content on the interfacial strength, for which the powder was conditioned at various relative humidity before being used to produce bilayer tablets. (3) The effect of the particle size of the powder used in first layer on the interfacial strength, for which the feed powder was sieved to obtain powders with specific particle sizes that were then used to produce the first layer of the bilayer tablets. For all cases considered, direct tensile tests were performed to measure the tablet interfacial strength. It is found that the interfacial curvature, the water content and the particle size in the first layer affected the interfacial strength significantly. It is also shown that the tablet interfacial strength was increased when larger particles were used in the first layer, or when curved punches (i.e. either convex or concave punches) were used to produce curved interfaces with increased interfacial areas. In addition, a higher interfacial strength can also be achieved by properly controlling water content in the powder.
Triboelectric charging and electrostatic interactions are commonly encountered in many powder handling processes. In this paper, the electrostatic behaviours of particles in a rotating spherical container were examined, in particular, the electrostatic dispersion of particles was recorded with a camera and then quantitatively analysed. The effects of the Coulomb's repulsive force and the attractive image force on the degree of particle dispersion, the motion of individual particles, formation and geometrical shape of particle clusters were analysed. The results show that the degree of particle dispersion increases with the charging time until it achieves a saturation value. The particle cluster formation undergoes five distinctive regimes and is governed by the external forces from the container wall, while the collective effect of both the extra-particle force and the Coulomb's repulsive force determines the evolution of the cluster shape. [Display omitted] •Electrostatic dispersion of particles was recorded and quantitatively analysed.•Effects of electrostatic repulsive and attractive force on particle dispersion were studied.•Five regimes for motion of particles and shape of particle clusters were observed.
In this paper, the compaction of lactose powder, a typical pharmaceutical excipient, is modelled using finite element methods (FEM) in which the powder is represented by an elastic-plastic continuum medium following Drucker-Prager Cap yield criteria. In a recent numerical and experimental study by the present authors [1], it was found that cone-shaped capping failure occurs during compaction of flat-faced round tablets, and that cone capping is associated with intensive shear band formation during the decompression stage. It is hence instructive to explore possible approaches that might alleviate the propensity for capping. Two approaches to alleviate capping were therefore investigated through finite element analysis: (i) altering the surfaces of the punches, i.e. to make convex tablets using the same material properties, and (ii) altering the material properties, i.e. changing the elasticity of the materials. It was found that capping still takes place even if the surface curvatures of the punches are altered. These predictions have been confirmed by physical experiments using a compaction simulator. The experiments have also demonstrated convincingly that the capping occurs during decompression. The second approach has been investigated in such a way that only the Young's modulus of the powder is changed to values twice and one-half that of lactose. Numerical results reveal that intensive shear bands are still developed during decompression even when the material properties are changed in this way. This implies that similar capping patterns are still possible for those materials. It is anticipated that the reason that some pharmaceutical excipients, such as microcrystalline cellulose (Avicel PH-102), do not cap is because of the high bonding strength of such materials (which can be generally characterised by tensile strength) [2].
Continuous powder blending is an essential operation during continuous pharmaceutical manufacturing. However, the complex granular dynamics in the blender is still poorly understood. This study employs a graphic processor unit (GPU) enhanced discrete element method (DEM) to analyse the granular dynamics in a continuous blender. Numerical results indicate that only a small fraction of powder distributes in the upper region of the blender, while most of that distributes in the middle and lower regions. Besides, a higher impeller speed leads to a smaller hold-up mass and a shorter mean residence time. Interestingly, the maximum number of blade passes is achieved at an intermediate impeller speed. There are two distinct regimes during continuous blending: i) a shearing regime at low impeller speeds; and ii) a dynamic regime at high impeller speeds. This study demonstrates that the GPU-enhanced DEM can be a robust tool for analysing powder flow during continuous pharmaceutical manufacturing. [Display omitted] •GPU-enhanced DEM analysis on the full-scale continuous blending is performed.•Impeller speed has a significant impact on the powder flow in the inclined blender.•At steady-state, powder mainly distributes in the middle and bottom zones of blender.•Maximum number of blade passes can be achieved at an intermediate impeller speed.
Sedimentation of particle suspensions in a channel flow into a cavity is analysed numerically using a lattice Boltzmann method coupled with a discrete element method. The work focuses on the entrapment of particles inside a confined cavity and the particle dynamics after entrapment. A close examination of the particle motions reveals three distinct dynamic behaviours: i) resuspension, ii) circulation in the central vortex and iii) deposition to the rear edge of the cavity. The effects of fluid inertia, particle density and cavity size on the infiltration and resuspension behaviours are systematically investigated. The results show that decreasing the Reynolds number, and increasing the length and depth of the cavity all lead to an increase in the trap efficiency. Three distinctive regimes with respect to the trap efficiency were then identified by deriving an empirical dimensionless trap number Tp: a resuspension regime when Tp 2.5.
Granular flows are characterised by particle interactions that involve sliding and collisions. In such events, heat is generated from friction and plastic deformation. Despite the importance of such self-heating mechanisms, our understanding of the fundamental principles of heat generation from friction and plastic dissipation is still limited. This work explores this problem at the particle level for oblique impacts between a spherical particle and a rigid substrate. In the first part, theoretical models and a finite element method (FEM) model are used to predict the amount of heat generated and contact temperatures at various impact angles. The theoretical and the FEM models are in good agreement for all impact cases considered. A parametric study of the influence on heat generation and temperature distributions is also carried out. It is shown that the temperature profiles are dependent not only on the amount of the generated heat but also on the material's thermal properties, such as thermal conductivity and specific head capacity. Apart from a good insight into heat generation during oblique impacts, this study also identifies simple theoretical solutions that can be used in other numerical tools, such as discrete element methods, for studying heat generation problems in bulk granular flows.
In this paper, the deformation of compliant microcapsules is studied in narrow constrictions using a hybrid particle-based model. The model combines the Smoothed Particle Hydrodynamic (SPH) method for modelling fluid flow and the Mass Spring Model (MSM) for simulating deformable membranes. The model is initially validated for the dynamics of microcapsules in shear flow. Then, several quantitative parameters such as the deformation index, frontal tip and rear tail curvatures and the passage time are introduced and their variations are studied with respect to capillary number and constriction size. Subsequently, a dependency analysis is performed on these quantitative parameters and some recommendations are made on fabrication of microfluidic devices and analysis of microcapsules for extracting their mechanical properties. It is revealed that the deformation index and frontal tip and rear tail curvatures are the most suitable parameters for correlating the elastic properties to the dynamics of microcapsules.
The flowability and dispersion behavior are two important physicochemical properties of pharmaceutical formulations for dry powder inhalers (DPIs). They are usually affected by the environmental conditions, such as temperature and relative humidity (RH). However, very few studies have been focused on the relationship between the two properties and their dependence on RH during storage. In this research, model pharmaceutical formulations were prepared using mixtures of coarse and fine lactose. The fractions of fines in the mixtures were 0%, 5%, 10% and 20%, respectively. These blends were stored at four different RH, 0%, 30%, 58% and 85%, for 48 hours. The FT4 Powder Rheometer was used to evaluate the powder flowability, and the Malvern Spraytec® laser diffraction system was employed to assess the powder dispersion performance. The results indicated that both the flow and dispersion properties of lactose blends deteriorate after being stored at 85% RH, but improved after being conditioned at 58% RH. The fine particle fractions (FPFs) of the blends with 5% and 10% fine fractions and the as-received coarse lactose decreased when they were conditioned at 30% RH. For the blend with 20 % fine fraction, a high RH during storage (i.e., 85%RH) affected the dispersion property, but had a limited influence on its flowability. While, for the coarse lactose powder, the different RH conditions only affected its flowability, but not the dispersion results. A strong correlation between the powder flowability and its dispersion performance was found.
Contact electrification occurs in many powder handling processes and involves electrostatic charges that are transferred between contacting particles during collisions. In the current paper, a successive condenser model was developed and implemented into a discrete element method coupled with computational fluid dynamics (DEM-CFD) to analyse the charge transfer during powder processing. The numerical results for the contact electrification between a dielectric particle and a neutral conductive surface were in excellent agreement with experimental data reported in the literature. It was also shown that, during single collisions, the transferred charge is proportional to the maximum contact area but decreases linearly as the initial charge of the particle increases. In a successive impact process, charge accumulation on a particle increases exponentially with the number of collisions and eventually reaches an equilibrium state. During these processes, larger particles gain higher steady state charge but the charge-to-mass ratio is smaller. Nevertheless, particles of different sizes have identical surface charge density and charging coefficient when the impact velocity is identical. In the case of gas fluidization, the electrostatic charge gradually accumulates on particles and eventually reaches an equilibrium state. Non-uniform charge distribution is generally induced. A higher superficial gas velocity results in a faster charge accumulation due to increased collision frequency and impact velocity. © 2013 Elsevier B.V.
In dry granulation, fine cohesive powders are compacted into large multi-particle entities, i.e., briquettes, flakes or ribbons. The powder compaction is generally followed by milling, a size reduction process, which is crucial to obtain the desired granule size or properties. Abrasion and impact are two primary mechanisms of comminution in ribbon milling, but they are not completely understood. The aim of this paper was hence to investigate numerically the fragmentation process induced by abrasion during ribbon milling. The discrete element method (DEM) was employed to simulate abrasion tests, for which three-dimensional parallelepiped ribbons were generated using auto-adhesive elastic spheres. The fragmentation rate, and the fragments size and number were determined for various surface energies and abrasive velocities. The DEM results showed that the mass-equivalent fragment size distributions were bi-modal, similar to the experimental observations and the numerical results for impact-dominated ribbon milling reported in the literature. In addition, two quantities were determined from the DEM analysis, i.e. the number of large fragments and the fraction of fines, which was then integrated into the population balance models (PBM) so that a DEM-PBM multiscale modelling framework was developed to predict the granule size distribution during ribbon milling. The DEM-PBM results were compared with the experimental results reported in the literature, and a broad agreement was obtained, implying the proposed DEM-PBM can be used to analyse the ribbon milling behaviour.
Probiotics are live microorganisms known for conferring health benefits through the improvement or restoration of gut microbiota, and tablet is one of the commonly used forms to deliver them. Ensuring the viability of probiotics within tablets is a crucial quality consideration. However, maintaining probiotic viability during tabletting is challenging due to potential lethal mechanisms. Therefore, it is critical to understand the lethal mechanisms behind and determine effective preventive strategies when developing probiotic tablets. In this study, two primary lethal mechanisms are identified during tabletting: mechanical stress and local heating. This review also underscores effective preventive strategies to mitigate their impact during formulation development and the tabletting process. Key approaches include formulation design and process optimisation, encompassing choice of excipient, probiotics/excipients ratio, and compression speed/pressure/profile. By presenting an overview of these lethal mechanisms and corresponding preventive strategies, this paper aims to provide a valuable guideline for the development of probiotic tablets.
Mixing of particulate systems is an important process to achieve uniformity, in particular pharmaceutical processes that requires the same amount of active ingredient per tablet. Several mixing processes exist, this study is concerned with mechanical mixing of crystalline particles using a four-blade mixer. Although numerical investigations of mixing using four-blades have been conducted, the simplification of particle shape to spherical or rounded superquadric particle systems is universal across these studies. Consequently. we quantify the effect of particle shape, that include round shapes and sharp edged polyhedral shapes, on the mixing kinematics (Lacey Mixing Index bounded by 0 and 1) that include radial and axial mixing as well as the inter-particle force chain network in a numerical study. We consider six 100 000 particles systems that include spheres, cubes, scaled hexagonal prism, bilunabirotunda, truncated tetrahedra, and a mixed particle system. This is in addition to two six million particle systems consisting of sphere and truncated tetrahedra particles that we can simulate within a realistic time frame due to GPU computing. We found that spherical particles mixed the fastest with Lacey mixing indices of up to 0.9, while polyhedral shaped particle systems mixing indexes varied between 0.65 and 0.87, for the same mixing times. In general, to obtain a similar mixing index (of 0.7), polyhedral shaped particle systems needed to be mixed for 50% longer than a spherical particle system which is concerning given the predominant use of spherical particles in mixing studies.
Roll compaction is a critical unit operation in the pharmaceutical manufacture. During roll compaction, a change in the internal energy of powder due to applying of external work from the rolls can generate heat and cause an increase in the temperature of the powder, which can subsequently affect the roll compaction behaviour and the quality of ribbons. Thus, it is crucial to understand the thermal response of pharmaceutical formulations during roll compaction. This study hence aims to examine the evolution of temperature and density in powders during roll compaction. For this purpose, a systematic experimental study is performed using the peripheral quantitative computed tomography (PQCT), for the first time, and the thermographic method to investigate the thermomechanical behaviour of pharmaceutical powders during roll compaction. A finite element model is also developed to describe the transformation of irreversible compression work to heat as well as the energy dissipation due to the wall friction, and to predict the thermomechanical behaviour. In particular, the effect of roll speeds on the thermomechanical behaviour of powders during roll compaction is examined. It was shown that at low roll speeds, the highest temperature is reached inside of the compacted powder. As the roll speed increases, more heat is generated on the ribbon surfaces due to the powder-wall friction, while the density of ribbon deceases. It was found that the density and the temperature at the ribbon centre, were generally higher than that near to the edge, for roll compaction with fixed cheek plates.
Die filling is a critical process step in pharmaceutical tablet manufacturing. Mass and content uniformity of the tablets as well as production throughput depend upon the die filling performance of the formulations. The efficiency of the die filling process is influenced by powder properties, such as flowability, cohesion, particle size and morphology, as well as the process conditions. It is hence important to understand the influence of powder properties on the die filling performance. The purpose of the present study is to identify the critical material attributes that determine the efficiency of die filling. For this purpose, a model rotary die filling system was developed to mimic the die filling process in a typical rotary tablet press. The system consists of a round die table of 500 mm diameter, equipped with a rectangular die. The die table can rotate at an equivalent translational velocity of up to 1.5 m/s. The filling occurs when the die passes through a stationary shoe positioned above the die table. Using this system, die filling behaviours of 7 commonly used pharmaceutical excipients with various material characteristics (e.g. particle size distribution, sphericity and morphology) and flow properties were examined. The efficiency of die filling is evaluated using the concept of critical filling velocity. It was found that the critical filling velocity is strongly dependent on such properties as cohesion, flowability, average particle size and air sensitivity index. In particular, the critical filling velocity increases proportionally as the mean particle size, flow function, air permeability and air sensitivity index increase, while it decreases with the increase of specific energy and cohesion.
Pharmaceutical tablets are the most popular dosage form for drug delivery. The tablets are generally produced by compacting dry powders. During pharmaceutical powder compaction, the tablets produced need to sustain their integrity during the process and have to be strong enough to sustain any possible load experienced during the post-compaction processes, such as coating, packing and handling. Hence, any defects, such as chipping, capping and laminating, are not tolerable during pharmaceutical powder compaction. However, such defects are common problems during the tabletting process. Therefore, understanding the failure mechanisms of these defects has attracted considerable attention. In this paper, only the mechanisms of capping were considered. Previous studies on capping during pharmaceutical powder compaction have been reviewed. Capping mechanisms have been further explored by conducting a combined experimental and computational study on pharmaceutical powder compaction. An instrumented hydraulic press (also known as compaction simulator) has been used to investigate the powder behaviour during the compaction. In addition, an instrumented die has also been used, which enable the material properties to be extracted for some real pharmaceutical powders. Close attentions have been paid to the occurrence of capping during tabletting. An X-ray Computed Microtomography system has also used to examine the internal failure patterns of the tablets produced using the compactions simulator. Furthermore, pharmaceutical powder compaction has also been analysed using finite element (FE) methods, in which the powder was modelled as an elastic-plastic continuum medium following Drucker-Prager-Cap yield criteria and the material properties were determined from the uniaxial compaction with an instrumented die. In both experimental and numerical studies, cylindrical tablets with different surface curvatures, including Flat-face round tablets and convex tablets, were considered. From the experimental observation, it is clear that different capping patterns were obtained for different shaped tablets: cone-shaped capping for flat-faced tablets and normal capping with essentially horizontal failure surface for convex tablets. It was also observed in the experiments that capping takes place at the early stage of decompression (unloading), i.e., the top punch begins to withdraw. Close examination of FEA results reveals that the capping is associated with an intensive shear band developed at the early stage of unloading for all cases considered. Therefore, the combined experimental and numerical studies demonstrated that the intensive shear bands developed at the early stage of unloading are responsible for the occurrence of capping.
Positron Emission Particle Tracking (PEPT) is a non-invasive technique which enables quantitative information on the position and 3D motion of a tracer particle during processing to be determined at high frequencies. This technique has been successfully used to investigate powder behaviour during mixing, fluidization, granulation, etc. In this study, PEPT was employed to examine the flow behaviour of powders during die filling. Time histories of displacement and velocity of traced particles were determined. It has been found that the measured displacement and velocity in the moving direction of the feed shoe corresponds very well with the specified shoe motion, demonstrating that the motion of particles during die filling can be accurately determined using PEPT. This will provide useful information to fully understand the die filling process.
Dry granulation through roll compaction is a technology commonly used in the pharmaceutical industry for producing roll compacted ribbons. The significance of the feed screw speed and roll speed during ribbon production was highlighted in recent publications. However, previous studies focused primarily on the individual effects of either the feed screw speed or roll speed on ribbon porosity, and the synergetic effect of these parameters was rarely examined. The aim of this study therefore was to investigate the effects of the screw-to-roll speed ratio on the porosity of roll compacted ribbons, produced at different roll compaction conditions using the microcrystalline cellulose MCC, Avicel PH-102 feed material. It was observed that ribbon porosity decreased linearly with increasing screw-to-roll speed ratio. Furthermore, an increase in the speed ratio led to an increase in the roll gap and mass throughput while a decrease in the screw constant was observed. Thus, this study demonstrates that the screw-to-roll speed ratio can be treated as one of the critical process parameters for controlling ribbon porosity and can also be used to determine the optimum operating regimes during roll compaction.
The oral drug delivery system using bilayer (or multilayer) tablets has been more commonly used in therapeutic strategies. However, one of the most common problems associated with bilayer tablets is the insufficient interfacial strength between layers, which leads to product failure during manufacturing. Therefore, it is important to better understand the interfacial strength of bilayer pharmaceutical tablets. For this purpose, in this study, the interfacial strength of bilayer tablets made of microcrystalline cellulose (MCC PH 102) at various manufacturing conditions was systematically examined. Three cases were considered to explore: (1) the effect of interfacial curvature on the interfacial strength, for which the interfaces between two layers with different curvatures were produced using flat, convex and concave punches. (2) The effect of water content on the interfacial strength, for which the powder was conditioned at various relative humidity before being used to produce bilayer tablets. (3) The effect of the particle size of the powder used in first layer on the interfacial strength, for which the feed powder was sieved to obtain powders with specific particle sizes that were then used to produce the first layer of the bilayer tablets. For all cases considered, direct tensile tests were performed to measure the tablet interfacial strength. It is found that the interfacial curvature, the water content and the particle size in the first layer affected the interfacial strength significantly. It is also shown that the tablet interfacial strength was increased when larger particles were used in the first layer, or when curved punches (i.e. either convex or concave punches) were used to produce curved interfaces with increased interfacial areas. In addition, a higher interfacial strength can also be achieved by properly controlling water content in the powder. [Display omitted] •Interfacial strength of bilayer tablets were directly measured using the direct tensile test.•The impact of moisture content, particle size and interface curvature on the interfacial strength was explored.•The interfacial strength was increased when larger particles were used for the first layer.•The interfacial strength was increased when curved punches were used to produce curved interfaces with increased interfacial area.•A higher interfacial strength can also be achieved with properly controlling the water content.
This paper provides experimental data on the temperature rise during granular flows in a small-scale rotating drum due to heat generation. All heat is believed to be generated by conversion of some mechanical energy, through mechanisms such as friction and collisions between particles and between particles and walls. Particles of different material types were used, while multiple rotation speeds were considered, and the drum was filled with different amounts of particles. The temperature of the granular materials inside the rotating drum was monitored using a thermal camera. The temperature increases at specific times of each experiment are presented in form of tables, along with the average and standard deviation of the repetitions of each setup configuration. The data can be used as a reference to set the operating conditions of rotating drums, in addition to calibrating numerical models and validating computer simulations.
We study the size-density/topology relations} in random packings of dry adhesive polydisperse microspheres with Gaussian and lognormal size distributions through a geometric tessellation. We find that the dependence of the neighbour number on the centric particle size is always quasilinear, regardless of the size distribution, the size span or interparticle adhesion. The average local packing fraction as a function of normalized particle size for different size variances is well regressed on the same profile, which increases to larger values as the relative strength of adhesion decreases. The variations of the local coordination number with the particle size converge onto a single curve for all the adhesive particles, but gradually transfer to another branch for non-adhesive particles. Such adhesion induced size-density/topology relations} are interpreted theoretically with a modified geometrical "granocentric" model, where the model parameters are dependent on a single dimensionless adhesion number. Our findings, together with the modified theory, provide a more unified perspective on the substantial geometry of amorphous polydisperse systems, especially those with fairly loose structures.
A particle-scale breakage model for impact milling has been proposed by Vogel and Peukert based on single particle impact experiments. Their model provides a good starting point for extension to dynamic systems, since it successfully separates the effects of material properties from the milling operating conditions. In the current study, a rigorous way to incorporate such a single particle breakage model into a dynamic population balance model is proposed by considering the particle breakages under different numbers of successive impacts, each with distinct impact rates, breakage probabilities, and breakage functions. The new model was developed within both Process System Enterprise's gSOLIDS and MathWorks' MATLAB software and has been verified with experimental data. Notably good matches between the predicted and experimental data were obtained.
Powder compaction is widely used to manufacture a wide range of particulate products. Understanding powder compaction behaviour is of practical importance to improve the efficiency of product development and the manufacturing performance. This paper briefly introduces the finite element method (FEM) that has been extensively used in modelling powder compaction, for which the DPC model is introduced. Typical finite element analysis results are presented to illustrate the capability of FEM in modelling powder deformation. It shows that non-uniform density and temperature distributions are generally obtained during powder compaction. In addition, the correlations between the fracture patterns observed experimentally with the stress distribution obtained using FEM are examined. It is shown that the stress distribution could provide useful information on the potential fracture patterns during powder compaction.
Powder compaction is widely used to manufacture particulate products (e.g. tablets and pellets), in which die filling is a critical stage governing the performance of the powder compaction process and the quality of finished products. In this paper, how the shape and orientation of the die affect powder flow behaviour during die filling is analysed using the discrete element method (DEM), in which powders are treated as a collection of individual particles. Die filling with dies of various shapes and orientation is considered, and die filling performance is evaluated in terms of the mass flow rate and the critical fill speed. It is found that the die filling efficiency during parallel filling into a die of large aspect ratio is generally low. This study also demonstrates that DEM is a useful tool for modelling die filling processes.
Segregation of granular materials is often induced by differences in size, density, shape and surface properties. Density and size-induced mixing and segregation of binary mixtures of glass beads and/or resin particles in the FT4 powder rheometer are investigated experimentally using a new FT4 methodology. The proposed methodology allows for quantification of mixing and segregation of components based on a mixing index. It is observed that the mixing index increases with increasing density and size ratio. Variation of flow energy and torque is related to the mixing and segregation of the mixture components, thus demonstrating that the FT4 powder rheometer may be used as a predictive tool for the tendency of mixture components to segregate under various stress conditions. Numerical analysis by DEM shows that for non-cohesive systems mixing and segregation occur by sifting of fines through interstitial gaps formed between coarse particles in the dilated region. For the non-cohesive system, higher blade tip speeds reduce the rate of mixing and minimise the segregation of different-sized components. Increasing the interfacial energy reduces the rate of mixing and alleviates the segregation of particles. For the cohesive systems, mixing occurs by rupture of cohesive fine clusters with the mixing index increasing with increasing blade tip speed owing to the higher shear stresses that break the agglomerates. [Display omitted] •Mixing and segregation of binary mixtures in the FT4 were investigated.•A new FT4 methodology was developed to quantify mixing and segregation.•Effects of size and density ratios and surface energy were investigated.•Mechanisms governing mixing and segregation were evaluated.•Mixing and segregation rates were related to FT4 flow energy.
Roll compaction is a commonly used dry granulation process in pharmaceutical, fine chemical and agrochemical industries for materials sensitive to heat or moisture. The ribbon density distribution plays an important role in controlling properties of granules (e.g. granule size distribution, porosity and strength). Accurate characterisation of ribbon density distribution is critical in process control and quality assurance. The terahertz imaging system has a great application potential in achieving this as the terahertz radiation has the ability to penetrate most of the pharmaceutical excipients and the refractive index reflects variations in density and chemical compositions. The aim of this study is to explore whether terahertz pulse imaging is a feasible technique for quantifying ribbon density distribution. A series of ribbons were made of two grades of microcrystalline cellulose (MCC), Avicel PH102 and DG, using a roll compactor at various process conditions and the ribbon density variation was investigated using terahertz imaging and sectioning methods. The density variations obtained from both methods were compared to explore the reliability and accuracy of the terahertz imaging system. An average refractive index is calculated from the refractive index values in the frequency range between 0.5 and 1.5 THz. It is shown that the refractive index gradually decreases from the middle of the ribbon towards to the edges. Variations of density distribution across the width of ribbon are also obtained using both the sectioning method and the terahertz imaging system. It is found that the terahertz imaging results are an excellent agreement with that obtained using the section method, demonstrating that terahertz imaging is a feasible and rapid tool to characterize ribbon density distributions.
Herein, the development of a 3D pore-scale lattice Boltzmann (LB) model for simulating the transport processes and electrochemical performance of the porous electrodes in Li-ion batteries is reported. The model captures the transport of ions, electrons, and liquid electrolyte species, coupled with the electrochemical reactions at the interface between the active material and the liquid electrolyte with complex boundary conditions. The model-predicted discharge curves of a realistic nickel-manganese-cobalt battery electrode are shown to be in good agreement with the experimental measurement on the same electrode, demonstrating the validity of the model prediction. The LB model is then applied to simulate a series of electrode structures generated using the discrete-element method, to understand the effects of particle size and distribution, porosity, pore size distribution, surface area, and tortuosity on the performance of the electrode. It is revealed that surface area and pore size distribution are the dominant factors for the performance, and electrodes with structured patterns are beneficial for achieving uniform local distribution of Li and current densities within the electrode. The LB model provides insightful understanding of spatial distribution of Li and local phenomenon in 3D electrode structures, and can be a useful tool for designing next-generation battery electrodes.
Granular flow is common in many industrial applications, and involves heat generation from frictional contacts and inelastic collisions between particles. The self-heating process is still poorly understood despite being intrinsic to many processes. This work, for the first time, explores this problem experimentally by quantifying the temperature rise of granular flows in a rotating drum with a robust methodology based on infrared thermography. Particles of four different materials (lead, steel, plastic and glass) are used in the experiments, at various rotation speeds and drum fill ratios. To assess the mechanical behaviour, the flow regime of every experiment was determined. It was inferred that particles with higher density tend to generate more heat. It was also revealed that increasing the rotation speed favours the temperature rise. At the same time, the fill ratio had the least influence on the thermal response of the particulate systems considered. [Display omitted] •The temperature rise of particles due to mechanical energy dissipation is quantified.•Infrared thermography is used to measure the temperature rise of particulate flows.•Different particle materials, rotation speeds, and fill ratios of the drum are used.•The flow regimes are identified and related to the Froude number and drum fill ratio.
Air flow and particle-particle/wall impacts are considered as two primary dispersion mechanisms for dry powder inhalers (DPIs). Hence, an understanding of these mechanisms is critical for the development of DPIs. In this study, a coupled DEM-CFD (discrete element method-computational fluid dynamics) is employed to investigate the influence of air flow on the dispersion performance of the carrier-based DPI formulations. A carrier-based agglomerate is initially formed and then dispersed in a uniformed air flow. It is found that air flow can drag API particles away from the carrier and those in the downstream air flow regions are prone to be dispersed. Furthermore, the influence of the air velocity and work of adhesion are also examined. It is shown that the dispersion number (i.e., the number of API particles detached from the carrier) increases with increasing air velocity, and decreases with increasing the work of adhesion, indicating that the DPI performance is controlled by the balance of the removal and adhesive forces. It is also shown that the cumulative Weibull distribution function can be used to describe the DPI performance, which is governed by the ratio of the fluid drag force to the pull-off force.
Aimed at addressing these challenges, this book contains a selection of papers discussing the state-of-the-art research in particulate materials science that were presented at the UK China Particle Technology Forum III held at Birmingham, ...
Understanding the adhesive interactions between active pharmaceutical ingredient (API) particles and carrier particles in dry powder inhalers (DPIs) is critical for the development of formulations and process design. In the current study, a discrete element method, which accounts for particle adhesion, is employed to investigate the attachment processes in DPIs. A critical velocity criterion is proposed to determine the lowest impact velocity at which two elastic autoadhesive spherical particles will rebound from each other during impact. Furthermore, the process of fine API particles adhering to a large carrier in a vibrating container is investigated. It was found that there are optimal amplitude and frequency for the vibration velocity that can maximise the number of particles contacting with the carrier (i.e. the contact number). The impact number and detachment number during the vibration process both increase with increasing vibration amplitude and frequency while the sticking efficiency decreases as the amplitude and frequency are increased. © 2013 Springer-Verlag Berlin Heidelberg.
Many granular materials change their volume as they absorb fluids. This phenomenon is called swelling and can be observed in a variety of solids, such as soils, wood, absorbent hygiene products (AHPs) and pharmaceutical excipients. Therefore, an in-depth understanding of grain swelling is of great importance. Since experimental investigations can often provide only limited information, while great insight could be gained from numerical modelling, rigorous numerical models for predicting particle swelling are required. Hence, the objective of this research is to develop and validate a Discrete Element Method (DEM) for swelling of particles. A first order kinetic model was employed to predict the volume expansion of a single grain and subsequently implemented in DEM. The validation of the model was accomplished by comparing the expansion with time of a packed bed made of super absorbent polymer (SAP) particles obtained numerically and experimentally. It was shown that the DEM model can accurately predict the bed expansion. The model was then employed to simulate the swelling of three different materials: superabsorbent polymer (SAP), rice and microcrystalline cellulose (MCC Avicel PH102). As expected, it is demonstrated that the material properties play a significant role on the swelling; the fastest to reach its maximum expansion is the granular bed made of MCC PH102, followed by SAP and rice. However, the highest swelling capacity is achieved with SAP. Moreover, a preliminary DEM analysis of the segregation in a swelling binary mixture is presented in this work. Results suggest that systems which contain a small number of particles, and thus are looser, are more prone to segregation. Future study could advance the developed model to analyse consequences of swelling phenomena in granular materials, such as segregation and heat generation.
[Display omitted] •Powder characteristics have a significant influence on powder flow behaviour during die filling.•For free-flowing powders, flow behaviours in linear and rotary die filling are similar.•For poor-flowing powders, a higher filling efficiency is achieved during linear die filling than rotary die filling. In the pharmaceutical industry, linear die filling is widely employed in R&D, while rotary die filling is very common in commercial production. It is not clear if powder die filling behaviour in a linear die filling system is representative of the flow performance in a rotary tablet press. In this study, a linear die filling system and a rotary die filling system were used to examine flow behaviours of both poor-flowing and free-flowing powders. It was found that the performance of poor-flowing powder in the linear die filling system is slightly better than that in the rotary die filling system, while the performance of free-flowing powders in the linear die filling system is similar to that in the rotary die filling system. Hence, it is suitable to use the linear die filling system to estimate the flow behaviour during rotary die filling with free-flowing powders, but caution needs to be taken when poor-flowing powders are used.
Dry granulation using roll compaction (DGRC) becomes increasingly adopted in the pharmaceutical industry due to its unique advantage of not requiring liquid binder and a subsequent drying process. However the DGRC process presents also some challenges, in particular, high fine fraction generated during the milling stage significantly limits its application. Although the fines produced can be recycled in practice, it may lead to poor content uniformity of the final product. At present there is a lack of mechanistic understanding of milling of roll compacted ribbons. For instance, it is not clear how fines are generated, what are the dominant mechanisms and controlling attributes and if any measurement technique can be used to characterise ribbon milling behaviour. Therefore, the aim of this paper was to assess if ribbon milling behaviour can be assessed using some characterization methods. For this purpose, friability was evaluated for ribbons made of microcrystalline cellulose (MCC) powders using a friability tester that was originally developed for characterising the tendency of pharmaceutical tablets to generate small pieces while being abraded. Granules were also produced by milling of the ribbons and their size distributions were analysed. The correlation between the fine fraction of the granules with ribbon friability was then explored. It was found that there was a strong correlation between ribbon friability and the fine fraction of granules generated during milling. This implies that friability tests can be performed to characterise ribbon milling behaviour, and ribbon friability provides a good indication of the fraction of fines generated during ribbon milling.
Solid pharmaceutical tablets can be manufactured via three processing technologies: direct compression, dry granulation and wet granulation before the final compaction process. Dry granulation using roll compaction generally involves production of ribbons, followed by milling to produce granules and the production of tablets. The mechanical properties of ribbons produced during roll compaction can influence breakage behaviour in a mill and hence the performance of a drug formulation. Therefore it is important to explore critical factors that determine the quality of ribbons. In this study, MCC Avicel PH-102 was used as the model powder for roll compaction and the critical operating factors affecting ribbon quality were studied. MCC 102 ribbons were manufactured at a range of process conditions (roll speed, feed screw speed and compaction pressure) using the TF mini roll compactor with a serrated die & punch (DPS), grooved roll surface. The key ribbon properties measured are the powder feed ratio (defined as the ratio of feed screw speed to that of roll speed) and mass throughput ratio (defined as the mass of ribbons produced in a given time to that of fines). The porosity of ribbons was observed to depend significantly on powder feed ratio into the compaction zone. Porosity remained constant at a fixed feed ratio irrespective of the absolute roll speed and the feed screw speed conditions used. Mass throughput ratio is another factor that was introduced to describe process efficiency i.e. to draw comparison between the amount of ribbons and fines. The amount of ribbons and fines generated at a given process condition depends significantly on the feed screw speed and the compaction pressure. In addition, ribbon porosity decreased with increasing pressure but there was negligible effect on ribbon porosity when excessively high pressure (> 60 bar) was used. Ribbon porosity was also observed to decrease with increasing feed screw speed but the converse is true with increasing roll speed. In conclusion, the impact of various roll compaction process parameters were critically investigated and a detailed insight into the main factors (powder feed and mass throughput ratios) that govern the behaviour of roll compacted ribbons was provided. In future, the focus is to relate these process properties (and ribbon porosity) to granule size distribution from a milling process.
Numerous practical applications of the Discrete Element Method (DEM) require a flexible description of particles that can account for irregular and non-convex particle shape features. Capturing the particle non-convexity is important since it allows to model the physical interlocking when the particles are in contact. To that end, the most flexible approach to capture the particle shape is via a polyhedron, which provides a faceted representation of any shape, albeit at a significant computational cost. In this study we present a decomposition approach to modeling non-convex polyhedral particles as an extension of an existing open source convex polyhedral discrete element code, BlazeDEM-GPU, which computes using general purpose graphical processing units (GPGPUs). Although the principle of decomposition of non-convex particles into convex particles is not new, its application by the discrete element modeling community has been rather limited. The non-convex extension of BlazeDEM-GPU was validated using a hopper flow experiment with identical convex and identical non-convex 3D printed particles. The experiment was designed around two sensitive flow points, with the convex particles following the intermittent flow and the nonconvex particles forming stable arches. It was demonstrated that the DEM simulations can be applied to reproduce both the convex and the non-convex flow behavior using the same parameter set. This study is a significant step towards general computing of non-convex particles for industrial-scale applications using the GPGPUs.
Flowability that quantifies the flow behaviour of powders is an important material attribute for such applications as packing, hopper flow and powder transport. It is also one of the critical material attributes of pharmaceutical formulations for solid dosage forms. It is anticipated that size enlargement via dry/wet granulation will improve the flowability of feed powders, but it is still unclear how significant the flowability can be enhanced. Therefore, in this study, an experimental investigation was performed to explore how dry granulation affects the flowability of pharmaceutical powders, such as microcrystalline cellulose (MCCs), mannitol and lactose. Both as-received powders and binary mixtures were considered. Granules of various sizes were produced using roll compaction followed by ribbon milling, and the flowability of as-received powders and produced granules was characterised using two methods: 1) the critical filling speed measured using a model die filling system and 2) the flow index measured using a Flodex tester. It was shown that the flowability increases as the size of the granules increases for all materials considered. Furthermore, it was found that there is a strong correlation between the critical filling speed and the flow index: the critical filling speed is proportional to the flow index to a power of − 5/2.
Die filling is an important process step in manufacturing of tablets. An important mechanism in the die filling process is suction that is developed with the downward motion of the bottom punch once the die is covered by powder. However, the contribution of suction to the die filling performance is still poorly understood. Hence, the present study aimed to experimentally investigate the flow behaviour of powders during suction filling. Four different types of pharmaceutical powders were used and a model suction filling system was developed. Effects of filling and suction velocities, as well as powder properties, on the efficiency of die filling were systematically investigated. Cohesive and free-flowing powders behaved differently at various filling-to-suction velocity ratios. The filling behaviour of cohesive powders was improved at high filling-to-suction ratios due to acceleration-induced densification. Free-flowing powders performed better at low filling-to suction ratios.
The present study investigated particle size-induced segregation during die filling of binary pharmaceutical blends, consisting of fine and coarse particles in various fractions. Coarse fraction was made of milled and sieved acetylsalicylic acid, whereas the fine fraction was mannitol. The die filling process was carried out in gravity filling and suction filling. The segregation was assessed through determination of the coarse component concentration using UV–Visible spectrophotometry. The obtained values of concentration, determined for ten units of identical volume inside the die, were used to calculate the segregation index (SI), which was an indicator of uniformity of the powder blend deposited into the die. It was found that high segregation tendency was generally observed during gravity filling at a low velocity, due to the effect of air drag, and during gravity filling at a high velocity, as it was carried out through three consecutive filling steps. The lowest segregation tendency was generally observed during suction filling at a low velocity. The horizontal segregation was mostly observed in the top layers of the die, due to mainly two mechanisms: coarse particles cascading down the heap formed by the powder in the final steps of die filling, which produces higher coarse concentration at the near side of the die, observed at low coarse concentration; or coarse particle cascading down the top surface of the flowing powder stream into the die, which increases the coarse concentration at the far end of the die.
The presence of liquids in particulate materials can have a significant effect on their bulk behaviour during processing and handling. It is well recognised that the bulk behaviour of particulate materials is dominated by the interactions between particles. Therefore, a thorough understanding of particle-particle interaction with the presence of liquids is critical in unravelling complex mechanics and physics of wet particulate materials. In the current study, a discrete element method for wet particulate systems was developed, in which a contact model for interactions with pendular liquid bridges between particles of different sizes was implemented. In order to evaluate the accuracy and robustness of the developed DEM, normal elastic impacts of wet particles with a wall were systematically analysed. It was shown that the DEM simulations can accurately reproduce the experimental observations reported in the literature. In addition, the DEM analysis was also in good agreement with the elastohydrodynamic model. It was further demonstrated that the rebound behaviour of wet particles is dominated by the Stokes number. There was a critical Stokes number, below which the particle will stick with the wall. For impacts with a Stokes number higher than the critical Stokes number, the coefficient of restitution increases as the stokes number increases for elastic particles. It was also found that the contact angle and surface tension played an insignificant role in the normal impact of wet particles, while the viscosity of the liquid has a dominant effect on the rebound behaviour.
Contact electrification and electrostatic interactions often occur in the fluidization process, which can significantly influence the dynamic behaviour of particles and the fluidization performance. In this study, a discrete element method coupled with computational fluid dynamics (DEM-CFD) is developed by implementing contact electrification and electrostatic interaction models and the combined effects of contact electrification and electrostatic interaction on fluidization are analysed. It is found that the charge of the particle system increase with the superficial gas velocity. Particles of different material properties (especially work function) can be bi-charged and form agglomerates. At low superficial gas velocities, the particle bed cannot be fully fluidized and the pressure drop tends to be stable rather than fluctuating as the gas flows through the micro-channels of agglomerates. However, at high superficial gas velocities, the agglomerates can break, inducing strong fluctuation of pressure drop. Clearly, the electrostatic phenomena and fluidization behaviour can mutually influence each other during the process.