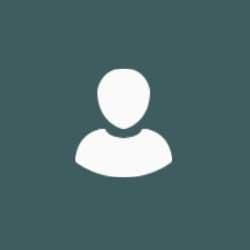
Dr Arman Burkitbayev
About
My research project
Battery thermal management system in electric vehiclesThe aim of the project is to develop a novel hybrid battery thermal management system based on heat pipes for electric vehicles.
Supervisors
The aim of the project is to develop a novel hybrid battery thermal management system based on heat pipes for electric vehicles.
Publications
•Heat generation of Lithium ion batteries and consequences of thermal instability.•Capability of heat pipes in maintaining thermal stability of Li-ion cells.•Gaps in heat pipe based battery thermal management.•Current status, challenges and future direction of heat pipe based battery thermal management. Heat pipes are currently attracting increasing interest in thermal management of Electric vehicle (EV) and Hybrid electric vehicle (HEV) battery packs due to its superconductive capability, robustness, low maintenance and longevity. With the focus of battery thermal management directed towards both convective and conductive cooling, a significant number of research, both experimental and numerical investigations have been performed during the past decade. However, heat pipe based battery thermal management systems (HP-BTMS) are yet to be commercialized due to lack of understanding their limitations during rapid heat fluctuations and adverse environmental conditions, performance under multiple heat loads, failure criteria in the context of battery thermal management and lack of simple and versatile thermal models to accurately predict the battery thermal performance at module and pack level. This comprehensive review highlights the different heat generation mechanisms of Li-ion batteries and their resulting consequences, followed by the operating principles of heat pipes along with background and shortcomings related to heat pipe based battery thermal management, for the mere purpose of further development of this promising thermal management system. Different heat pipe based thermal management systems developed during the last decade along with their modelling approaches, including the methods adopted for enhancing heat transfer are critically analysed. Heat pipes have demonstrated to be an effective approach in maintaining optimum cell surface temperature, however, several areas require attention if this system is to be commercialized. Niche types of heat pipes such as pulsating heat pipes, loop heat pipe, mini/micro heat pipe have also been reviewed and their advantages, disadvantages, and challenges in the context of BTMS are discussed. Finally, the current status, challenges and prospects of the future direction in HP-BTMS are highlighted.
A thermal management system for lithium-ion batteries is an essential requirement for electric vehicle operation due to the large amount of heat generated by these cylindrical batteries during fast charging/discharging. Previously, researchers have focused mostly on pouch and prismatic cells with heat pipes arranged in the horizontal direction. The current study introduces a novel vertically-oriented heat-pipe-based hybrid cooling battery thermal management system (BTMS) that numerically evaluates the thermal performance of the cylindrical batteries and the flow pattern within the cooling channel at C rates as high as 8C. The model was experimentally validated using five round heat pipes in a vertical orientation utilizing the effect of gravity to assist condensate flow through the heat pipe. The heat pipes were arranged in a staggered pattern to improve the overall heat transfer performance by means of forced convective cooling. This design allowed for maximizing the heat transfer process despite the lack of contact between the cylindrical-shaped batteries and round-shaped heat pipes. During this study, the temperatures of the evaporator end and the condenser end of the heat pipes and battery surfaces were monitored, and the thermal performances of the system were determined at varying inlet cooling liquid temperatures (15, 20, 25 °C) and high rates of 4C and 8C. Representatively, the proposed hybrid BTMS could maintain a maximum battery surface temperature of around 64 °C and a temperature difference between cells under 2.5 °C when the inlet velocity was 0.33 L/min and the cooling liquid temperature was 25 °C. The high temperatures reached the fourth and fifth heat pipes because they are part of the backflow design and are affected by backflow temperature. Nevertheless, the current design shows that the proposed system can maintain battery surface temperatures well within 5 °C.