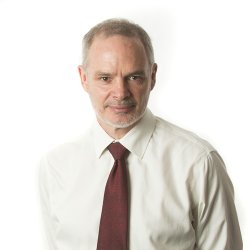
Professor Andrew Crocombe
About
Biography
I am a Professor here at the University of Surrey.
ResearchResearch interests
- Adhesive bonding
- Composite Materials
- Biomechanics
- Damage Modelling
Research interests
- Adhesive bonding
- Composite Materials
- Biomechanics
- Damage Modelling
Publications
A prosthetic socket used by a lower limb amputee should accommodate the patient’s geometry and biomechanical needs. The creation of a geometrically accurate subject-specific finite element model can be used to provide a better understanding of the load transfer between socket and limb. There has been a limited number of finite element studies of trans-femoral sockets with all current models only including the femur and ignoring the pelvis. This study looked to evaluate the effect that including the pelvic bone as well as the femur in a finite element model has on the contact interface between the prosthetic socket and residual limb. This was done by creating a finite element model from a computerised tomography scan of a trans-femoral amputee. This model included three-dimensional geometry, nonlinear material properties and frictional contact between the residual limb and prosthetic socket. It was found that without the pelvic bone the contact pressures peaked at the distal end region of the residual limb (peak of 95 kPa). However by including the pelvic bone the contact pressures were instead concentrated at the ischial loading region (peak of 364 kPa). The shear stresses experienced on the socket-residual limb interface were also simulated. The results obtained in this study can be used to provide more of an understanding of the loading on the residual limb for the design and creation of future trans-femoral sockets.
A chirped fibre Bragg grating (CFBG) optical sensor has been used to detect delamination growth in an ENF specimen. CFBG sensors, with a sensor length of 60 mm, have been embedded within ENF specimens fabricated from out-of-autoclave CFRP. Delaminations have been propagated within the specimen from an insert embedded at the specimen midplane during manufacture. The sensor has been interrogated with the specimen subjected to four-point loading, and the perturbations detected within the reflected spectra of the sensor are in reasonable agreement with the physical position of the delaminations measured at the coupon edges. The prediction of the reflected spectrum for one delamination length, using a combination of 3-D finite-element analysis and commercial software for predicting FBG spectra, is in qualitative agreement with the experimental results. Better quantitative agreement is expected to require a more refined finite-element model of the ENF specimen.
PURPOSE: The hypothesis of this study is that all-polyethylene (APE) tibial implants offer a biomechanical profile similar to metal-backed tray (MBT). There are significant financial implications, in selected patient groups, if APE can be deemed to perform as well as MBT. METHODS: Using a finite element analysis of CAD models provided by DePuy (Leeds), stress distributions were investigated for both an APE and MBT tibial implant. The performance was assessed for cancellous bone at 700 MPa (normal) and at 350 MPa (less stiff). Plots were recorded along the length of the tibia, showing the loads carried by the bone (cortical and cancellous), the implant interface, cement interface and the stem. von Mises stress distributions and percentage volumes were used to assess bone resorption and hence potential for failure (fracture). RESULTS: Higher stress shielding (resorption) occurred around the keel and stem of the MBT revealing greater potential for bone loss in these areas. APE had no areas of bone resorption (being more flexible resulting in less stress shielding). The stiffer MBT carries a higher proportion of the load down the stem. MBT stress in cancellous bone is lower than APE, as load is distributed to the cortical rim. APE has a marginally favourable strain state in cancellous bone and spreads loads more at the cement interface than MBT. CONCLUSION: Modern-day APE bearings may be superior to previously designed implants due to improvements in manufacturing. In the correct patient group, this could offer substantial cost savings.
This paper describes progress towards developing design guidelines for a number of composite bonded joints in aerospace applications. The premise of a universal failure criterion is impractical given the number of adherend-adhesive configurations and layups available. However, for a finite number of joint configurations, design rules can be developed based on experimental test data and detailed finite element (FE) modelling. By using these techniques rather than the traditional overly conservative knock down factors, more of the performance of composite bonded joints can be accessed. The work presented here experimentally studied the effect of the substrate layup, adhesive type and adhesive thickness on double-lap joint (DLJ) strength. The corresponding failure surfaces were analysed and failure modes identified. Following this, detailed FE models were developed to identify the trends associated with altering joint parameters. Finally, the stresses and strains within the adhesive and substrate were analysed at the joints respective failure loads to identify critical parameters. These parameters can provide an insight as to the stress state of the joint at failure or near failure loads, and hence its true performance.
Therapeutic use of high-amplitude pressure waves, or shock wave therapy (SWT), is emerging as a popular method for treating musculoskeletal disorders. However, the mechanism(s) through which this technique promotes healing are unclear. Finite element models of a shock wave source and the foot were constructed to gain a better understanding of the mechanical stimuli that SWT produces in the context of plantar fasciitis treatment. The model of the shock wave source was based on the geometry of an actual radial shock wave device, in which pressure waves are generated through the collision of two metallic objects: a projectile and an applicator. The foot model was based on the geometry reconstructed from magnetic resonance images of a volunteer and it comprised bones, cartilage, soft tissue, plantar fascia, and Achilles tendon. Dynamic simulations were conducted of a single and of two successive shock wave pulses administered to the foot. The collision between the projectile and the applicator resulted in a stress wave in the applicator. This wave was transmitted into the soft tissue in the form of compression-rarefaction pressure waves with an amplitude of the order of several MPa. The negative pressure at the plantar fascia reached values of over 1.5 MPa, which could be sufficient to generate cavitation in the tissue. The results also show that multiple shock wave pulses may have a cumulative effect in terms of strain energy accumulation in the foot.
© 2014 Wolters Kluwer Health | Lippincott Williams & Wilkins.Background: The cement-bone interface has been well studied as the weakest link where initiation of long-term aseptic loosening occurs in cemented arthroplasty. During total knee replacement, one is often confronted with eburnated bone in patients with severe arthritis. We aimed to study shear strength of the eburnated cement-bone interface and the effect of varied surface topology of eburnated bone on this interface strength. Methods: We used blocks of ebony wood to simulate eburnated bone. They were engineered to produce three surface topologies: smooth, drill holes, and cross-hatch pattern. These were cemented to metal (steel) blocks. Each specimen was then mounted onto a loading machine that created a shear force at the simulated cement-bone interface. Force displacement curves were recorded for all specimens until interface failure. Results: The smooth surfaced blocks were found to fail at the cement-wood (bone) interface at an average force of 0.5 MPa. Both the other surface topology alterations resulted in an increased ability to withstand force (average 3.7 MPa) before failure. Examination of the failed specimens revealed a combination of failure at both interfaces as well as cement deformation. Conclusions: One must alter the smooth surface of eburnated bone when dealing with bone defects in cemented arthroplasty. The pattern employed does not make a difference to the strength of the construct. The resulting mechanical bond of the cement with bone is as strong as any component in the metal-cement-bone construct.
Loosening and migration of tibial prostheses have been identified as causes of early total knee replacement (TKR) failure. The problem is made more complex when defects occur in the proximal tibia compromising fixation and alignment. Clinical studies using metal augments have shown these to be an alternative to other means of defect treatment. Finite element (FE) analysis can be used to identify regions that may be prone to loosening and migration. In the current work, 3D FE models of TKR uncontained type-2 defects treated with block augments have been constructed and analysed. It has been shown that a metal augment is the most suitable. The use of bone cement (PMMA) to fill proximal defects is not considered suitable as stresses carried by the cement block exceed those of the fatigue limit of bone cement. It has been shown that the stresses in the proximal cancellous bone of block-augmented models are significantly below levels likely to cause damage due to overloading. Furthermore, the use of stem extensions has been shown to reduce the cancellous bone stresses in the proximal region thus increasing the likelihood of bone resorption. Given this, it is recommended that stem extensions are not required unless necessary to mitigate some other problem.
The present paper is concerned with modelling damage and fracture in notched woven fabric composites. Previous experimental work has shown that damage at a notch in a variety of GFRP and CFRP composites based on woven fabric reinforcement comprises matrix damage and fibre tow fracture along the plane of maximum stress. It is these experimental observations that inform the failure modelling developed here, in which a cohesive zone approach is used within a 2- D finite element framework. The cohesive zone parameters are based on previously reported experimental measurements for the strength and toughness of the woven fabric materials under investigation. The approach is shown to provide predictions of notched strength that are in very good agreement (less than 11% discrepancy) with experimental results from the literature for a range of GFRP and CFRP woven fabric systems. © (2014) Trans Tech Publications, Switzerland.
Composite sandwich structures are well-suited for applications requiring high bending strength, flexural rigidity, crashworthiness, and light weight. However, skin-core debonding and core failure remain a barrier to optimal structural performance when polymeric foams are used as core materials. Suppressing or compartmentalising these failure modes can enhance the structural integrity of sandwich structures. In this paper, the flexural response of a sandwich structure was improved by adding carbon fibre-reinforced plastic in the form of through-thickness ribs during the manufacturing process. The effect of the position of the ribs was investigated using a quasi-static three-point bend test. A camera was used to capture failure events, while the digital image correlation technique provided the full-strain field at different stages of loading. Improved flexural performance was obtained when a reinforcement was placed on either side of the loading roller. With this configuration, skin-core debonding was restricted to a confined portion of the panel, resulting in a more localised and stable fracture process, which involved enhanced foam crushing and hardening. A simple FEA approach has been adopted in this paper and has proven to be an effective approach for capturing the details of the failure process, including the debonding in the composite foam structures, without the need for complex and computationally expensive interface modelling.
Digital Image Correlation (DIC) can be used to obtain full-field strain information of specimens under load. Through analysis of the resultant strain-contours, defects such as delaminations in composite materials can be detected based on their effect on the deformation behaviour. This paper focuses on the use of DIC to detect the presence of fully embedded artificial delaminations, introduced during the manufacturing process, inside a flat panel specimen under three-point bending. Two types of delamination insert have been considered: an insert containing two sealed pieces of PTFE, and an insert consisting of a single sheet of PTFE in combination with a stress-raiser. When tested in three-point bending, the position and approximate size of the delaminations were clearly visible due to the presence of a plateaux in the longitudinal surface strain profile. Finite element modelling predictions were in good agreement with the DIC measurements for both types of artificial delamination.
In previous work we have used a two-dimensional finite element model to predict the strength of GFRP woven fabric double-lap joint bolted joints that fail in the net-tension mode. The failure criterion was based on a fracture mechanics approach, incorporated within a XFEM framework, developed and validated previously for open-hole failure. Results were compared with experimental data obtained from clamped joints. While agreement between model and experiment showed promise, there are features of the problem, in particular the effect of bolt clamp-up and the associated load transfer as a result of friction, which cannot necessarily be captured with the limits of a two-dimensional model. The present work has therefore developed a three-dimensional model and applied it to the same data set. The effect of clamp-up torque is incorporated by modelling the bolt and washers and introducing a bolt tension, which enables the influence on frictional load transfer and the in-plane stress distributions to be incorporated within the model. The predictions for joint strength were in good agreement with experimental data up to the values of w/d for which the failure mechanism was observed experimentally to change to the bearing failure mode. Copyright © (2012) Asian-Australasian Association for Composite Materials (AACM).
Debonding between the skins and the core in a sandwich structure is a critical failure mode in automotive applications; once debonding occurs, the load carrying capacity of a sandwich structure drastically decreases. In the present paper, the effect of using three core materials, with different cell characteristics, on the interfacial strength between the foam cores and a CFRP skin is investigated through mechanical testing and numerical modelling. A key finding is that foams with a coarse cellular structure favour a high resin uptake at the interface during the manufacturing process, which results in a stronger interfacial bonding between the foam and the CFRP. During Mode I loading, the thick resin layer at the interface postpones crack initiation and kinking in the core, whilst under Mode II, this resin layer delays the collapse in compression of foam cells under the crack tip. Thus, the importance of including this thick resin layer in the FE modelling was demonstrated. Finally, as the CZM was shown to be unable to predict the unstable crack propagation within the core, an alternative approach was suggested which has the significant benefit of not requiring experimental testing of the interface between the skin and the core.
By the means of finite element analysis (FEa), biomechanical behaviors of human mandible have been widely studied over decades. Many different types of simulation of muscle forces have been employed in studies to increase the reality of mastication environment. Among these studies, Cruz et al (2003)'s calculation of muscle forces was well accepted. However, these simulations have not been verified experimentally as seen in literatures. In this study, a three dimensional (3D) finite element model of human mandible was created from CT images of a cadaver mandible bone. 4 pairs of muscle forces was applied to this 3D model based on a calculation by using Cruz et al (2003)'s method. The exact cadaver bone was used in an experimental testing rig to evaluate strain distribution and, hence, to verify the results of FEa. A set of different sizes of loads which matches with the one used in FE study was applied to the cadaver bone. Strain gauges were employed to gain data of strain distribution on the bone. The experimental result shows that the trend of stress/strain during increase or decrease of muscle forces coincides with FE result. This verifies the masticator muscle force calculation of Cruz et al (2003) to be correct.
A 2-D finite element model has been developed to simulate crack growth (net-tension and shear-out failures) in composite bolted joints. Results from the model have been compared with a similar approach from the literature and experimental data for a woven fabric system. Agreement is reasonable in each case.
Two polymeric foams have been characterised to develop a simple calibration process for extracting the parameters which are required by the material model available in the commercial FE package Abaqus. Indentation tests with DIC were conducted to study the validity of the proposed method.
Advanced structural adhesives are now an important joining technique in automobile and aerospace applications. The perceived uncertainty in the long-term structural performance of bonded members when subjected to static/fatigue loads in aggressive environments is probably restricting an even more widespread use of this joining technology. In this article, the effect of moisture on the static and fatigue resistances of adhesively bonded laminate joints was investigated. Experimental tests were performed on both aged and unaged adhesively bonded laminate joints for static and fatigue responses. Further, using a cohesive zone approach for the adhesive bondlines, a combined diffusion–stress analysis was developed to predict the progressive damage observed in the joints tested experimentally. The numerical predictions were found to be in good agreement with the experimental test results.
Polymeric foams are used extensively as the core of sandwich structures in automotive and aerospace industries. Normally, several experiments are necessary to obtain the required properties to model the response of crushable foams using finite element analysis (FEA). Hence, this research aims to develop a simple and reliable calibration process for extracting the physical parameters which are required by the material model available in the commercial FE package Abaqus. To do this, a set of experimental tests, including uniaxial compression, uniaxial tension and shear punch tests, is proposed. All the experimental tests were also simulated, and generally, good correlations between experiments and numerical models were obtained. The validity of the overall approach was finally demonstrated using an indentation test in which the foam was subjected to a more complex mixed mode loading. During these indentation tests, digital image correlation was used to observe full-field strain distribution in the foam under the indenter. Good agreement between the experimental results and the numerical predictions was found for load–displacement response, failure mode and strain distribution.
Delamination growth within transparent, unidirectionally reinforced glass fibre/epoxy doublecantilever beam (DCB) specimens has been monitored using a surface-mounted chirped fibre Bragg grating (CFBG) sensor. The specimens were tested using a constant displacement rate, with the delamination length being measured using (i) surface-mounted CFBG sensors, (ii) in situ photography, and (iii) surface-mounted strain gauges. The DCB specimens showed characteristics typical of such material, with the development of extensive fibre bridging and pronounced R-curve behaviour. A distinct perturbation in the reflected spectra, when monitoring the delamination growth using the CFBG sensors, was indicative of the location of the delamination front during the test. The in situ photographs and the surface strain measurements provided by the strain gauges were used to predict the experimentally determined CFBG reflected spectra, with good agreement between prediction and experiment. These results enabled the delamination length to be measured using the CFBG sensor technique to within 4 mm over the 60 mm sensor length.
Experimental studies have been undertaken to investigate the static and fatigue responses of metal laminate doublers (MLD) joints under tension loading after ageing in deionised water at a temperature of 50 °C up to 2 years. It was found that absorbed water did not have a significant effect on the static and fatigue degradation of the MLD; however, corrosion pits located on the aluminium surfaces caused a reduction in fatigue life. Inevitably, the laminate contained butts where co-planar aluminium sheets were joined, and it was found that the position of the butt affected the static response of the MLD but, due to a restricted data set, it has not been possible to assess the effect under fatigue loading. The backface strain technique in conjunction with video microscopy has been utilised to monitor the damage of the adhesive bondlines, the butts and the aluminium layers and successfully identified both the localised and the global damage in the MLD. Most of fatigue failures initiated at the stringer bondline edge and at the aluminium layers where the butt was located. A careful design should be made to reduce the stress concentration at the stringer edge and to avoid positioning the butts at the upper layer of aluminium close to the stringer edge.
Experimental and numerical studies have been undertaken on metal laminate (ML) doublers and hybrid fibre-metal (aluminium-Glare) laminate (FML) doublers to investigate their static and fatigue response under tension loading. Inevitably sheets in these laminates butt together and these butts can affect the joint strength. Progressive damage modelling, including the damage in the adhesive bondline, the butt, the metal and the fibre has been undertaken in both static and fatigue loading. This modelling was found to be in good agreement with the experiment data in terms both of the strength and the failure mechanisms. In ML, the butt influenced the static and fatigue response. In hybrid FML, the specimens either have the fibres parallel to the loading direction (spanwise) or perpendicular to the loading direction (chordwise). The spanwise specimen was found to have the highest strength followed by chordwise specimens without butts and finally chordwise specimens with butts. The most critical position for a butt was found to be adjacent to the doubler end. Without butts the static strength for spanwise and chordwise specimens was controlled by the failure in the Glare layer whilst the fatigue failure was precipitated by failure in the aluminium sheet. © 2012 Elsevier Ltd.
Recent work has shown that a simple rule-of-mixtures approach may be used to predict the stress strain behaviour of a cross-ply metal matrix composite (MMC) laminate. However, the low-strain behaviour was not predicted accurately, probably because thermal residual stresses are obviously not included in such an approach. To increase the understanding of the limitations of the rule-of-mixtures approach for predicting the stress-strain response, the residual strain-state of the fibre reinforcement has been determined using an etching technique (henceforth referred to as the ‘total etch removal method’), and results have been compared both with finite element modelling and with thermal residual strain measurements derived from stress-strain curves. The results show that the residual strain distribution in a cross-ply composite may be more complex than previously thought, with the fibres in internal 00 plies having considerably higher thermal residual strains than fibres in external plies. The results confirm that the rule-of-mixtures approximation can be used, with some reservations with regard to the low strain behaviour.
Improved walking comfort has been linked with better bio-mimicking of the prosthetic ankle. This study investigated if a hydraulic ankle/foot can provide enough motion in both the sagittal and frontal planes during level and camber walking and if the hydraulic ankle/foot better mimics the biological ankle moment pattern compared with a fixed ankle/foot device. Five active male unilateral trans-femoral amputees performed level ground walking at normal and fast speeds and 2.5Ê camber walking in both directions using their own prostheses fitted with an ªEchelonº hydraulic ankle/foot and an ªEspritº fixed ankle/foot. Ankle angles and the Trend Symmetry Index of the ankle moments were compared between prostheses and walking conditions. Significant differences between prostheses were found in the stance plantarflexion and dorsiflexion peaks with a greater range of motion being reached with the Echelon foot. The Echelon foot also showed significantly improved bio-mimicry of the ankle resistance moment in all walking conditions, either compared with the intact side of the same subject or with the ªnormalº mean curve from non-amputees. During camber walking, both types of ankle/foot devices showed similar changes in the frontal plane ankle angles. Results from a questionnaire showed the subjects were more satisfied with Echelon foot.
Late-stage fatigue damage of an E-glass/epoxy 3D orthogonal non-crimp textile composite loaded in the warp direction has been investigated using a combination of mechanical testing, X-ray micro computed tomography (μCT), optical microscopy and finite element modelling. Stiffness reduction and energy dissipated per cycle were found to be complementary measurements of damage accumulation, occurring in three stages: a first stage characterised by rapid changes, a more quiescent second stage, followed by a third stage where the (decreasing) stiffness and (increasing) energy dissipation change irregularly and then rapidly, to failure. Microscopy of specimens cycled into the transition between the second and third stages showed macroscopic accumulations of fibre fractures in sections of warp tows which lying adjacent to the surface weft tows which are crowned-over by the Z-tows. At these locations, the warp tow fibres are subjected to stress concentrations both from transverse weft tow matrix cracks and resin pocket cracks.
This article is the second part of a two-part article looking at carcass deflections, contact pressure and shear stress distributions for a steady-rolling, slipping and cambered tyre. In the first part, a previously described and validated finite-element (FE) model of a racing-car tyre is developed further to extract detailed results which are not easily obtainable through measurements on an actual tyre. Generally, these results aid in the understanding of contact patch characteristics. In particular, they form a basis for the development of a simpler physical tyre model, which forms the focus of this part of the article. The created simpler tyre model has the following three purposes: (i) to reduce computational demand while retaining accuracy, (ii) to allow identification of tyre model features that are fundamental to an accurate representation of the contact stresses and (iii) to create a facility for better understanding of tyre wear mechanisms and thermal effects. Results generated agree well with the physically realistic rolling-tyre behaviour demonstrated by the FE model. Also, the model results indicate that an accurate simulation of the contact stresses requires a detailed understanding of carcass deformation behaviour.
Digital Image Correlation (DIC) can be used to obtain full-field strain information on specimens under load. Through analysis of the resultant strain-contours, defects such as delaminations in composite materials can be detected, based on their effect on the deformation behaviour. This work focusses on the use of the DIC technique and two variations of active thermography (lock-in thermography and pulse thermography) for determining the lengths of delaminations in “milled-slot” specimens; for each technique, the measured delamination lengths have been compared with visually observed (i.e. photographed) delaminations grown under fatigue loading in transparent woven fabric GFRP specimens. In addition, the DIC results have been interpreted with the aid of a finite element model of the strain distribution in the milled-slot specimens. It has been found that the DIC technique provides a reasonably good method for measuring the length of the fatigue-grown delaminations after an empirical fit is applied, with the aid of the FE analysis, to overcome complications caused by fibre-bridging. On the other hand, the results using both lock-in and pulse thermography showed reasonable correlations with the visually observed (i.e. photographed) delamination lengths without the need for an empirical fit, although some post-processing of the data was required. For both thermography techniques, there were difficulties in determining the delamination lengths close to the edge of the milled slot.
Osseointegrated trans-femoral implant is a relatively new orthopaedic anchoring method for connecting a stump with a prosthesis. Through a follow-up study of a patient over six years, significant bone remodelling has been observed. Finite element (FE) simulations were carried out to investigate the relationship between the bone remodelling and the strain re-distribution around the trans-femoral osseointegrated implant system. An initial FE model representing the original status of the femur-implant assembly was created from CT scans of the subject prior to osseointegration. Follow-up X-ray images were acquired at various stages post-surgery, which allowed the changes in bone wall thickness to be measured. By updating the bone thickness in the initial model, a series of follow-up FE models were created. Representative load associated with the subject's body weight was applied to the models, and the strain re-distributions were calculated. The results showed that in order to minimise the adverse effect of bone remodelling, an osseointegration implant made by functionally gradient materials are preferred over homogeneous materials.
The FRP composite beam structure that is intended to represent deck prototype used in civil engineering construction is investigated. FRP composite material may have possible damage, which affect vibration structural integrity and reliability. To overcome this problem, vibration data from experiments can be used to assess such damage accurately. The FE mode updating process is demonstrated in parameter identification as well as structural damage identification. It is used to minimise the difference between experimental and numerical data. The updated parameters are the modified parameters selected in the FE model with aim of correcting modelling errors and/or damage detection. In this FE model updating procedure, model physical characteristics are changed so that the differences between experimental and numerical dynamic properties are reduced. The FE model updating is carried out using optimisation tools in ANSYS software. Only the first three natural frequencies will be considered in this work. The FE model updating procedure brings the numerical results of the FRP structure in proper correlation to the experimental results, according to an objective function, by changing the FE model parameters. The test results of the structure under intact and damage states are presented. It is suggested that there is damage at the unbounded joint when there is significant change in fixed parameters of the structure beyond acceptable degree. © The Society for Experimental Mechanics, Inc. 2012.
The choice of the materials used for the core and skin of a sandwich structure plays an extremely important role in the skin-core interfacial behaviour. In this paper, three PMI foams are used as core material and the effect of foam type in the skin-core interfacial response is examined.
Slope ambulation is a challenge for trans-femoral amputees due to a relative lack of knee function. The assessment of prosthetic ankles on slopes is required for supporting the design, optimisation, and selection of prostheses. This study assessed two hydraulic ankle-foot devices (one of the hydraulic ankles is controlled by a micro-processor that allows real-time adjustment in ankle resistance and range of motion) used by trans-femoral amputees in ascending and descending a 5-degree slope walking, against a rigid ankle-foot device. Five experienced and active unilateral trans-femoral amputees performed ascending and descending slope tests with their usual prosthetic knee and socket fitted with a rigid ankle-foot, a hydraulic ankle-foot without a micro-processor, and a hydraulic ankle-foot with a micro-processor optimised for ascending and descending slopes. Peak values in hip, knee and ankle joint angles and moments were collected and the normalcy Trend Symmetry Index of the prosthetic ankle moments (as an indication of bio-mimicry) were calculated and assessment. Particular benefits of the hydraulic ankle-foot devices were better bio-mimicry of ankle resistance moment, greater range of motion, and improved passive prosthetic knee stability according to the greater mid-stance external knee extensor moment (especially in descending slope) compared to the rigid design. The micro-processor controlled device demonstrated optimised ankle angle and moment patterns for ascending and descending slope respectively, and was found to potentially further improve the ankle moment bio-minicry and prosthetic knee stability compared to the hydraulic device without a micro-processor. However the difference between the micro-processor controlled device and the one without a micro-processor does not reach a statistically significant level.
A surface-mounted chirped fibre Bragg grating (CFBG) sensor has been used for the first time to monitor delamination growth within a composite material (a transparent, unidirectionally reinforced glass fibre/epoxy resin double-cantilever beam (DCB) specimen). The specimens were tested using a constant displacement rate, with the delamination length being measured using complementary techniques: (i) in situ photography, (ii) surface-mounted strain gauges, and (iii) the surface-mounted CFBG sensors. The unidirectionally reinforced DCB specimens showed characteristics typical of such material which complicate the curvature of the beams, i.e. the development of extensive fibre bridging and pronounced R-curve behaviour. To validate the interpretation of the CFBG reflected spectrum, the experimentally determined strains from the surface-mounted strain gauges have been used, together with in situ photographs of the position of the delamination front. Using the CFBG sensor technique, the delamination length was measured to within about 4 mm over the 60 mm sensor length.
Stem tip pain following revision total knee arthroplasty is a significant cause of patient dissatisfaction, which in the presence of an aseptic well-fixed component has no widely accepted surgical solution. A definitive cause of stem tip pain remains elusive, however it has been suggested that high stress concentrations within the region of the stem tip may play a role. This paper reports a finite element study of a novel clinical technique where a plate is attached to the tibia within the region of the stem tip to reduce stem tip pain. The results demonstrate that the plate reduces stress concentrations in the bone at the stem tip of the implant. The magnitude of stress reduction is dependent upon plate location, material and attachment method.
This paper presents an experimental and numerical study on the structural health monitoring of composite patch repairs using chirped fibre Bragg grating (CFBG) sensors. The repair consisted of bonding a pre-cured patch of the same, but thinner, material to a parent GFRP panel containing a machined hole, with the sensors embedded in the bond-line. The repaired coupons were subjected to four-point flexural loading in fatigue. Bond-line delamination cracks (disbonds) initiated at both ends of the patch repair and grew towards the centre of the repair. Predictions of the strain distributions enabled the reflected spectra obtained during damage growth to be predicted with good agreement between theory and experiment. For practical applications when using CFBG sensors to monitor patch repairs, the results suggest that two sensors should be included within the bond-line so that both vulnerable edges of the repair can be monitored using the low-wavelength end of a sensor.
In this paper it is shown that a chirped fibre Bragg grating sensor embedded within a composite adherend can be used to monitor disbond initiation and propagation in an adhesively bonded single lap-joint. Characteristic changes in the reflected spectra from the sensor indicate both disbond initiation and the current position of the disbond front to within about 2 mm (a distance which depends on adherend material and sensor position in relation to the adhesive bondline). When the sensor extends the full overlap length, disbond initiation from either end of the overlap can be monitored. The results have been modelled using a combination of finite-element analysis and commercial software for predicting FBG spectra; the predicted spectra are in very good agreement with experiment. The CFBG sensor technique could provide the basis for monitoring a wide range of bonded joints and structures where one adherend is a composite material.