MASSIVE: Manufacture of safe and sustainable volatile element functional materials
Start date
31 March 2014End date
31 January 2020Overview
Ensuring availability of next generation ‘safe and sustainable’ thermoelectric, pyroelectric and piezoelectric materials and devices, by addressing the challenges in synthesis, processing and manufacturing scale-up of un-commercialised functional materials.
The world around us is full of modern technology designed to make our lives safer, more comfortable and more efficient. Such technology is made possible by materials and devices that are able to interact with their surrounding environment either by sensing or acting upon it.
Examples of such devices include:
- Motion detectors
- Fuel injectors
- Engine sensors
- Medical diagnostic tools.
These interactive devices contain functional materials that can pose health hazards, are obtained from parts of the world where supply cannot be guaranteed or are relatively scarce.
If access to these functional materials is restricted, many of these advances will no longer be available resulting in a reduction in living standards and decreased UK economic growth. There already exist a number of replacement materials that can provide the same functions without the same levels of concerns around safety, security of supply and sustainability. However, these replacement materials need to be manufactured using different processes compared to existing materials.
Exploration
This project explores new manufacturing technologies that could be used to create interactive devices that contain less harmful and sustainable materials with a secure supply.
This EPSRC-funded project will focus on two types of material - thermoelectric and piezoelectric - where the replacement materials share a set of common challenges:
- They need to be processed at elevated temperatures
- They contain elements that evaporate at high temperatures (making high temperature processing and processing of small elements difficult)
- They are mechanically fragile making it difficult to shape the materials by cutting, grinding or polishing
- They are chemically stable making it difficult to shape them by etching
- Many are air and moisture sensitive.
The proposed research will address these challenges through research streams that engage proactively with industry.
Aims and objectives
Developing scale-up manufacturing capability and know-how for the synthesis, processing and manufacture of un-commercialised thermoelectric, piezoelectric and related materials and devices, which contain volatile and air-sensitive elements and compounds, with engineered nano- and non-equilibrium phases and structures.
This will be delivered through a series of related objectives:
Scaling-up synthesis of particulate materials, including novel composite and nanostructured materials. The manufacture of the feedstock particulate materials in sufficient quantity, composition and purity, is an integral part of the manufacturing chain. Solid state, wet and controlled atmosphere synthesis routes will be scaled-up to determine the requirements for effective large scale production.
Reducing lead time to market through exploration of high throughput manufacturing techniques for films and bulk materials.
Management of high temperature thermal treatments to prevent near-surface degradation (volatilisation) of materials, maintenance of critical nano/microstructures, and co-processing. Manufacturing techniques will be required to balance the conflicting demands of controlling the nano- and micro-structure while at the same time achieving high production outputs. Spark plasma sintering will be explored for bulk materials while atmosphere controlled rapid-sinter processing in combination with printing technologies will be explored for thick film materials.
Understanding the role of manufacturing on the materials behaviour during machining (e.g. during cutting, grinding, polishing). The mechanical integrity of the functional materials will be evaluated as a function of the manufacturing route and conditions. This will identify potential knock-on effects further along the manufacturing chain as a result of substituting materials.
Design of robust interfaces for electrodes, protective coatings, and joints for in-service performance. The interfacial bonding behaviour between dissimilar materials will be characterised to identify and manage the changes required in subsequent processing stages during device manufacture that will arise as a result of substituting materials. This understanding is required where electrodes and protective coatings are required or where two materials must be joined in order to realise the final device.
Incorporation of risk management within the manufacturing design stage to ensure the developed processes are fit-for service. To ensure that new long term problems relating to safety, security of supply and sustainability are not likely to be introduced into the new manufacturing processes, the occupational, consumer, and environmental risk landscape of current and developed manufacturing processes and materials will be compared.
Knowledge transfer through industrial collaboration, dissemination and networking. Increasing the level of technology transfer and training within the community and manufacturing supply chain will be driven by a proactive outreach dissemination programme based on the long-term experiences of the researchers of academic-industrial collaborations.
Funder
Stay connected
Latest tweets
@FNM_Surrey



Team
We welcome collaborations with industry partners in the form of feasibility studies, enabling short-term investigations of novel manufacturing concepts and processes for functional materials and devices, and longer-term industry-led strategic industry development projects to accelerate technology transfer.
Principal investigator

Project liaison officer
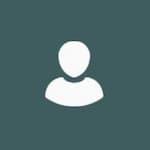
Dr Lynn Boniface
Project Manager
Partner organisation leads
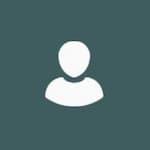
Professor Robert Freer
University of Manchester
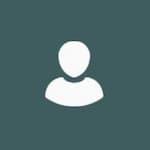
Professor Michael Reece
Queen Mary University of London
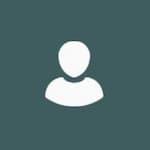
Dr Sophie Rocks
Cranfield University
Partner organisations
- Amphenol Advanced Sensors
- CeramTec UK Ltd
- European Thermodynamics Ltd
- Excelitas Technologies Corp.
- Intrinsiq Materials
- Johnson Matthey
- Kennametal
- M&I materials
- Meggitt plc
- Morgan Advanced Materials
- National Physical Laboratory
- PI ceramic
- Syfer
- Xaar.